What is a Flexible PCB?
A flexible printed circuit board (PCB), also known as a flex circuit or flexible electronics, is a type of PCB that consists of a thin, flexible plastic substrate with printed circuitry. Unlike traditional Rigid PCBs, Flexible PCBs can bend, twist, and conform to various shapes, making them ideal for applications where space is limited or where the device needs to move or flex during operation.
Flexible PCBs are composed of a thin, flexible insulating material, such as polyimide or polyester, with conductive traces printed on one or both sides. These traces are typically made of copper and can be coated with a protective layer to prevent oxidation and enhance durability.
Advantages of Flexible PCBs
Flexible PCBs offer several advantages over traditional rigid PCBs:
- Space savings: Flexible PCBs can be bent and folded to fit into tight spaces, reducing the overall size of the device.
- Weight reduction: The thin, lightweight nature of flexible PCBs makes them ideal for applications where weight is a critical factor, such as in aerospace and wearable electronics.
- Improved reliability: Flexible PCBs can withstand vibration, shock, and thermal stress better than rigid PCBs, increasing the overall reliability of the device.
- Enhanced design freedom: The ability to bend and conform to various shapes allows for greater design flexibility and the creation of unique form factors.
- Reduced assembly costs: Flexible PCBs can simplify the assembly process by reducing the number of connectors and wires needed, leading to lower manufacturing costs.
Types of Flexible PCBs
There are three main types of flexible PCBs:
- Single-sided flexible PCBs: These PCBs have conductive traces printed on only one side of the flexible substrate. They are the simplest and most cost-effective type of flexible PCB.
- Double-sided flexible PCBs: These PCBs have conductive traces printed on both sides of the flexible substrate, allowing for more complex circuitry and higher component density.
- Multi-layer flexible PCBs: These PCBs consist of multiple layers of flexible substrates with conductive traces, separated by insulating layers. Multi-layer flexible PCBs offer the highest level of complexity and density, but they are also the most expensive to manufacture.
Type | Layers | Complexity | Cost |
---|---|---|---|
Single-sided | 1 | Low | Low |
Double-sided | 2 | Medium | Medium |
Multi-layer | 3+ | High | High |
Manufacturing Process
The manufacturing process for flexible PCBs is similar to that of rigid PCBs, with a few key differences:
- Substrate selection: The flexible substrate material is chosen based on the specific application requirements, such as temperature range, chemical resistance, and mechanical properties.
- Circuit design: The circuit layout is designed using CAD software, taking into account the unique properties of the flexible substrate and the required bend radii.
- Printing: The conductive traces are printed onto the flexible substrate using screen printing, photolithography, or other methods.
- Etching: The unwanted copper is removed using a chemical etching process, leaving only the desired circuit pattern.
- Protective coating: A protective layer, such as coverlay or solder mask, is applied to the circuit to protect it from damage and environmental factors.
- Lamination: If the design requires multiple layers, the individual layers are laminated together using heat and pressure.
- Cutting and finishing: The completed flexible PCB is cut to the desired shape and size, and any additional features, such as stiffeners or connectors, are added.
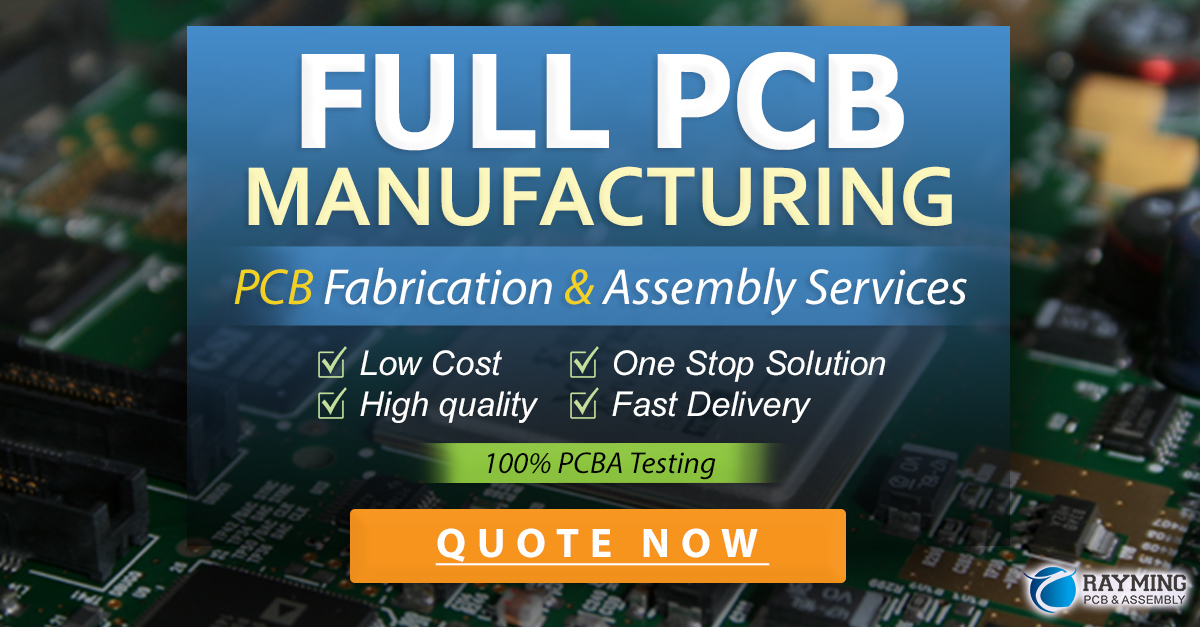
Applications of Flexible PCBs
Flexible PCBs are used in a wide range of industries and applications, including:
- Consumer electronics: Flexible PCBs are commonly used in smartphones, tablets, laptops, and wearable devices, where space is limited and flexibility is required.
- Medical devices: Flexible PCBs are used in medical implants, diagnostic equipment, and patient monitoring systems, where reliability and biocompatibility are critical.
- Automotive: Flexible PCBs are used in vehicle dashboard displays, sensor systems, and lighting applications, where they must withstand harsh environmental conditions.
- Aerospace: Flexible PCBs are used in satellites, aircraft, and spacecraft, where weight reduction and reliability are paramount.
- Industrial: Flexible PCBs are used in robotics, automation systems, and control panels, where they must withstand vibration, shock, and extreme temperatures.
Design Considerations for Flexible PCBs
When designing a flexible PCB, several key factors must be considered:
- Bend radius: The minimum bend radius of the flexible PCB must be determined based on the thickness of the substrate and the number of layers. Exceeding the minimum bend radius can cause damage to the circuit.
- Strain relief: Proper strain relief must be incorporated into the design to prevent damage to the circuit during flexing and bending.
- Material selection: The flexible substrate material must be chosen based on the specific application requirements, such as temperature range, chemical resistance, and mechanical properties.
- Trace width and spacing: The width and spacing of the conductive traces must be carefully designed to ensure proper electrical performance and to minimize the risk of short circuits during bending.
- Stiffeners: Stiffeners can be added to specific areas of the flexible PCB to provide additional support and prevent excessive bending.
FAQ
-
Q: Can flexible PCBs be used in high-temperature applications?
A: Yes, certain flexible substrate materials, such as polyimide, can withstand high temperatures up to 260°C, making them suitable for high-temperature applications. -
Q: Are flexible PCBs more expensive than rigid PCBs?
A: In general, flexible PCBs are more expensive to manufacture than rigid PCBs due to the specialized materials and processes required. However, the overall system cost may be lower when using flexible PCBs due to reduced assembly time and the elimination of connectors and wires. -
Q: Can flexible PCBs be repaired if damaged?
A: Repairing a flexible PCB can be challenging due to the delicate nature of the thin substrate and the difficulty in accessing the damaged area. In many cases, it is more cost-effective to replace the entire flexible PCB rather than attempting a repair. -
Q: How do I choose the right flexible substrate material for my application?
A: When selecting a flexible substrate material, consider factors such as the required temperature range, chemical resistance, mechanical properties, and cost. Consult with a flexible PCB Manufacturer or materials supplier to determine the best material for your specific application. -
Q: Can flexible PCBs be used in medical implants?
A: Yes, flexible PCBs can be designed using biocompatible materials and manufacturing processes to ensure they are safe for use in medical implants. However, strict regulatory requirements must be met, and extensive testing is required to validate the safety and reliability of the implant.
Conclusion
Flexible PCBs offer a versatile and reliable solution for applications requiring flexibility, space savings, and durability. By understanding the different types of flexible PCBs, their manufacturing processes, and key design considerations, engineers and product designers can leverage the benefits of flexible electronics to create innovative and efficient devices across a wide range of industries.
As technology continues to advance, the demand for flexible PCBs is expected to grow, driven by the increasing popularity of wearable devices, the miniaturization of electronics, and the need for more reliable and adaptable solutions in harsh environments. By staying informed about the latest developments in flexible PCB Technology and working closely with experienced manufacturers, companies can stay ahead of the curve and bring cutting-edge products to market faster than ever before.
Leave a Reply