Introduction to PCB Manufacturing
Printed Circuit Boards (PCBs) are the backbone of modern electronics. They provide a platform for mounting and connecting electronic components, enabling the creation of complex circuits and systems. Choosing the right PCB Manufacturer is crucial for ensuring the quality, reliability, and cost-effectiveness of your electronic products. In this comprehensive guide, we will explore the key factors to consider when selecting a PCB manufacturer and provide insights into the PCB manufacturing process.
Understanding the PCB Manufacturing Process
Before diving into the criteria for choosing a PCB manufacturer, it’s essential to understand the basic steps involved in the PCB manufacturing process. This knowledge will help you better evaluate the capabilities and expertise of potential manufacturers.
PCB Design and Layout
The PCB manufacturing process begins with the design and layout of the circuit board. This step involves creating a schematic diagram that represents the electrical connections between components and translating it into a physical layout. The layout determines the placement of components, routing of traces, and the overall dimensions of the PCB.
PCB Fabrication
Once the design is finalized, the PCB fabrication process begins. This involves the following steps:
-
Substrate Preparation: The base material, typically a laminate such as FR-4, is cut to the required size and thickness.
-
Copper Cladding: A thin layer of copper is bonded to one or both sides of the substrate.
-
Drilling: Holes are drilled through the substrate to accommodate through-hole components and vias.
-
Patterning: The desired circuit pattern is transferred onto the copper layer using photolithography or silkscreen printing.
-
Etching: The unwanted copper is removed using a chemical etching process, leaving behind the desired circuit traces.
-
Lamination: Multiple layers of the PCB are aligned and bonded together using heat and pressure.
-
Surface Finishing: A protective coating, such as solder mask or silkscreen, is applied to the PCB surface to prevent oxidation and improve solderability.
PCB Assembly
After the fabrication process, the PCB is ready for component assembly. This involves the following steps:
-
Solder Paste Application: Solder paste is applied to the pads where components will be placed.
-
Component Placement: Surface mount components are placed onto the solder paste using pick-and-place machines or manual methods.
-
Reflow Soldering: The PCB is heated in a reflow oven, causing the solder paste to melt and form a permanent connection between the components and the PCB.
-
Through-Hole Soldering: Through-hole components are inserted into the drilled holes and soldered manually or using wave soldering machines.
-
Inspection and Testing: The assembled PCB undergoes visual inspection and electrical testing to ensure proper functionality and adherence to specifications.
Key Factors to Consider When Choosing a PCB Manufacturer
Now that you have a basic understanding of the PCB manufacturing process, let’s explore the key factors to consider when selecting a PCB manufacturer.
1. Manufacturing Capabilities
One of the primary considerations when choosing a PCB manufacturer is their manufacturing capabilities. This includes the types of PCBs they can produce, the materials they work with, and the level of complexity they can handle.
PCB Types
PCBs can be classified into several categories based on their construction and functionality. Some common types include:
- Single-sided PCBs: These have components and traces on only one side of the substrate.
- Double-sided PCBs: These have components and traces on both sides of the substrate, with through-hole connections between the layers.
- Multi-layer PCBs: These consist of multiple layers of substrate and copper, allowing for more complex circuits and higher component density.
- Flexible PCBs: These use flexible substrates, enabling the PCB to bend and conform to various shapes.
- Rigid-Flex PCBs: These combine rigid and flexible sections, providing both stability and flexibility in a single board.
Ensure that the manufacturer you choose has experience and expertise in producing the specific type of PCB you require.
Materials and Substrates
PCBs can be manufactured using various materials and substrates, each with its own properties and advantages. Common substrate materials include:
- FR-4: A glass-reinforced epoxy laminate, widely used for its good electrical insulation and mechanical strength.
- High-Tg FR-4: A variant of FR-4 with improved thermal stability, suitable for high-temperature applications.
- Polyimide: A flexible substrate material known for its high heat resistance and dimensional stability.
- Aluminum: Used for metal-core PCBs, providing excellent thermal dissipation for high-power applications.
Consider the specific requirements of your application, such as temperature range, dielectric properties, and mechanical stability, when selecting a manufacturer that works with the appropriate materials.
Manufacturing Complexity
PCBs can vary greatly in complexity, from simple single-sided boards to multi-layer boards with fine-pitch components and high-density interconnects. Evaluate the manufacturer’s capabilities in handling the level of complexity required for your project. This includes their ability to produce boards with:
- High layer counts: The number of layers in a multi-layer PCB.
- Fine-pitch components: Components with small lead spacing, requiring precise placement and soldering.
- Blind and buried vias: Vias that connect inner layers without being visible on the surface.
- Controlled impedance: Precise control of trace widths and spacing to maintain consistent impedance for high-speed signals.
Choose a manufacturer that has a proven track record of successfully producing PCBs with similar complexity to your requirements.
2. Quality and Certifications
Quality is a critical factor when selecting a PCB manufacturer. A reliable manufacturer should have robust quality control processes in place to ensure consistent and defect-free production. Look for manufacturers with the following certifications and quality assurance practices:
ISO 9001 Certification
ISO 9001 is an internationally recognized standard for quality management systems. It demonstrates that the manufacturer has established and follows a documented quality management system, ensuring consistent processes and continuous improvement.
IPC Standards Compliance
IPC (Association Connecting Electronics Industries) is a global trade association that develops standards for the electronics industry. Ensure that the manufacturer adheres to relevant IPC standards, such as:
- IPC-A-600: Acceptability of Printed Boards
- IPC-A-610: Acceptability of Electronic Assemblies
- IPC-6012: Qualification and Performance Specification for Rigid Printed Boards
Compliance with these standards ensures that the manufacturer follows industry-accepted practices for PCB fabrication and assembly.
UL Certification
Underwriters Laboratories (UL) is a global safety certification company that tests and certifies products for safety and performance. If your application requires UL certification, choose a manufacturer that can produce UL-certified PCBs.
In-House Quality Control
Inquire about the manufacturer’s in-house quality control processes. They should have a dedicated quality control department that conducts regular inspections and tests throughout the manufacturing process. This may include:
- Visual inspections
- Automated optical inspection (AOI)
- X-ray inspection
- Electrical testing
- Functional testing
A robust quality control process helps identify and address issues early, reducing the risk of receiving defective or substandard PCBs.
3. Lead Time and Turnaround
Lead time and turnaround are important considerations when choosing a PCB manufacturer, especially if you have tight deadlines or require quick prototyping. Lead time refers to the time between placing an order and receiving the finished product, while turnaround refers to the time it takes for the manufacturer to complete the production process.
Standard Lead Times
Most manufacturers offer standard lead times for different types of PCBs and quantities. These can range from a few days to several weeks, depending on the complexity of the board and the manufacturer’s capacity. Make sure to discuss your specific lead time requirements with potential manufacturers to ensure they can meet your needs.
Expedited Services
Some manufacturers offer expedited services for urgent projects or quick-turn prototypes. These services may include:
- Rush production: Prioritizing your order and allocating additional resources to complete it faster.
- Quick-turn prototyping: Offering accelerated production for small quantities of prototype boards.
- Dedicated project management: Assigning a dedicated project manager to oversee your order and ensure timely delivery.
Keep in mind that expedited services often come at a premium cost, so consider the trade-off between lead time and budget when making your decision.
On-Time Delivery
Consistently meeting promised lead times is crucial for maintaining your own production schedules and customer commitments. Inquire about the manufacturer’s on-time delivery rate and their processes for ensuring timely completion of orders. A reliable manufacturer should have a track record of delivering PCBs on or before the agreed-upon date.
4. Cost and Pricing
Cost is always a significant factor when selecting a PCB manufacturer. However, it’s important to consider the total cost of ownership rather than just the upfront price per unit. The lowest price may not always provide the best value in terms of quality, reliability, and long-term cost savings.
Pricing Factors
Several factors can influence the pricing of PCBs, including:
- Board size and complexity: Larger and more complex boards generally cost more to manufacture.
- Material selection: The choice of substrate material and surface finish can impact the overall cost.
- Quantity: Higher quantities often result in lower per-unit costs due to economies of scale.
- Layer count: Multi-layer boards are more expensive than single or double-sided boards.
- Turnaround time: Expedited services or quick-turn prototyping may incur additional costs.
Request quotes from multiple manufacturers and compare not only the prices but also the included services, quality commitments, and lead times.
Cost Optimization
While cost is important, it should be balanced against other factors such as quality and reliability. However, there are ways to optimize costs without compromising on these aspects:
- Design for Manufacturability (DFM): Collaborate with the manufacturer during the design phase to ensure your PCB layout is optimized for their production processes. This can help reduce manufacturing costs and improve yields.
- Standardization: Using standard sizes, materials, and components can help reduce costs compared to custom or specialized options.
- Volume discounts: If you have high-volume requirements, negotiate volume discounts with the manufacturer to achieve better pricing.
- Long-term partnerships: Building a long-term relationship with a manufacturer can lead to cost savings through improved efficiency, trust, and understanding of your specific needs.
Remember that the cheapest option may not always be the most cost-effective in the long run, especially if it results in quality issues, delays, or additional rework.
5. Technical Support and Communication
Effective communication and technical support are vital for a successful partnership with a PCB manufacturer. Look for a manufacturer that is responsive, knowledgeable, and willing to collaborate with you throughout the production process.
Technical Expertise
The manufacturer should have a team of experienced engineers and technicians who can provide valuable insights and recommendations for your PCB design and manufacturing. They should be knowledgeable about the latest industry trends, technologies, and best practices.
Design Support
Many manufacturers offer design support services to help optimize your PCB layout for manufacturability and performance. This can include:
- Design rule checks (DRC): Verifying that your design meets the manufacturer’s production capabilities and constraints.
- Design for Manufacturing (DFM) analysis: Identifying potential issues or improvements in your design to enhance manufacturability and reduce costs.
- Gerber file generation: Assisting with the creation of production-ready Gerber files that meet the manufacturer’s requirements.
Take advantage of these services to streamline the production process and avoid potential issues down the line.
Communication Channels
Clear and efficient communication is essential for a smooth production process. The manufacturer should provide multiple communication channels, such as:
- Phone and email support: Readily available contact points for inquiries, updates, and issue resolution.
- Online portals: Secure platforms for placing orders, tracking progress, and accessing documentation.
- Regular progress updates: Proactive communication about the status of your order, including milestones and any potential delays.
Choose a manufacturer that is responsive to your inquiries and provides timely and transparent communication throughout the production process.
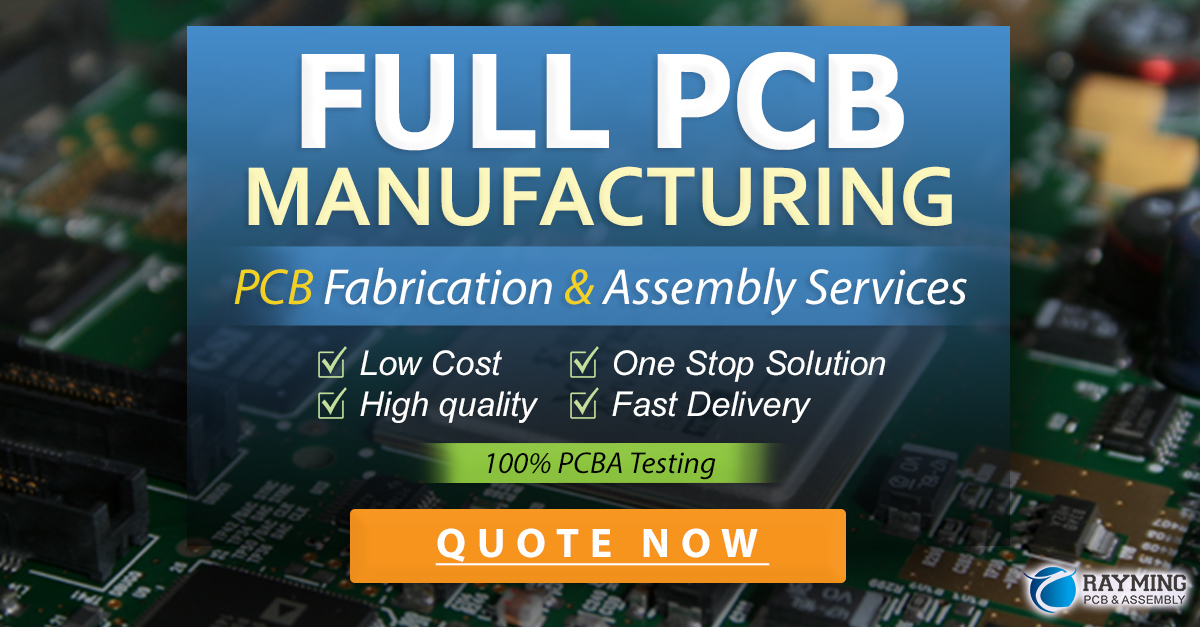
Frequently Asked Questions (FAQ)
1. What is the minimum order quantity (MOQ) for PCBs?
The minimum order quantity varies among manufacturers and depends on factors such as board complexity, materials, and production processes. Some manufacturers specialize in low-volume production and offer MOQs as low as one piece for prototype runs. Others may have higher MOQs for standard production, typically ranging from 50 to 100 pieces. It’s important to discuss your specific quantity requirements with potential manufacturers to ensure they can accommodate your needs.
2. How long does it typically take to manufacture PCBs?
The lead time for PCB manufacturing depends on several factors, including the complexity of the board, the selected materials, and the manufacturer’s production capacity. Standard lead times can range from a few days to several weeks. For simple, single-sided boards, lead times may be as short as 24-48 hours, while complex, multi-layer boards may require 2-3 weeks or more. Many manufacturers offer expedited services for faster turnaround times, but these often come at a premium cost. Always discuss your specific lead time requirements with the manufacturer to ensure they can meet your deadlines.
3. What is the typical cost range for PCBs?
The cost of PCBs varies widely depending on factors such as board size, complexity, material selection, quantity, and turnaround time. Simple, single-sided boards in low quantities may cost a few dollars per piece, while complex, multi-layer boards in high volumes can cost several hundred dollars or more per piece. To get an accurate cost estimate, it’s best to request quotes from multiple manufacturers based on your specific requirements. Keep in mind that the lowest price may not always provide the best value in terms of quality and reliability.
4. What should I look for in a PCB manufacturer’s quality control process?
A reliable PCB manufacturer should have a robust quality control process in place to ensure consistent and defect-free production. Key elements to look for include:
- ISO 9001 certification: Demonstrates that the manufacturer follows a documented quality management system.
- IPC standards compliance: Ensures that the manufacturer adheres to industry-accepted practices for PCB fabrication and assembly.
- In-house quality control: Dedicated quality control department conducting regular inspections and tests, such as visual inspections, automated optical inspection (AOI), X-ray inspection, and electrical testing.
- Traceability: Ability to trace materials, processes, and operators involved in the production of each PCB for quality assurance and issue resolution.
Don’t hesitate to ask potential manufacturers about their specific quality control processes and certifications to ensure they meet your quality expectations.
5. How do I ensure my intellectual property (IP) is protected when working with a PCB manufacturer?
Protecting your intellectual property is a valid concern when outsourcing PCB manufacturing. To mitigate risks and ensure your IP is safeguarded, consider the following measures:
- Non-disclosure agreements (NDAs): Have the manufacturer sign a comprehensive NDA that prohibits them from disclosing or using your proprietary information without authorization.
- Secure data transfer: Use secure file transfer protocols and encryption when sharing sensitive design files and documentation with the manufacturer.
- Limited access: Request that the manufacturer limit access to your project files and information to only the essential personnel directly involved in the production process.
- IP protection policies: Inquire about the manufacturer’s internal policies and practices for protecting customer IP, such as employee training, data security measures, and physical access controls.
- Jurisdiction: Consider working with manufacturers in countries with strong IP protection laws and enforcement mechanisms.
Ultimately, building a trust-based relationship with your chosen PCB manufacturer is key to ensuring the protection of your intellectual property.
Conclusion
Choosing the right PCB manufacturer is a critical decision that can greatly impact the success of your electronic products. By considering factors such as manufacturing capabilities, quality and certifications, lead time and turnaround, cost and pricing, and technical support and communication, you can make an informed choice that aligns with your specific requirements and expectations.
Remember to prioritize quality, reliability, and long-term value over short-term cost savings. Building a strong, collaborative relationship with your PCB manufacturer can lead to improved efficiency, innovation, and success in the competitive electronics industry.
As you embark on your search for the ideal PCB manufacturer, use this guide as a reference to evaluate potential partners and make a well-informed decision. With the right PCB manufacturer by your side, you can bring your electronic designs to life with confidence and achieve your business goals.
Leave a Reply