Introduction to PCB Surface Mount Technology
PCB Surface Mount Technology (SMT) has revolutionized the electronics manufacturing industry since its introduction in the 1960s. SMT allows for the placement of electronic components directly onto the surface of a printed circuit board (PCB), rather than through holes in the board. This technology has enabled the production of smaller, lighter, and more densely packed electronic devices.
The PCB Surface Mount Plant (PCB-SMP) is a specialized facility designed to efficiently assemble PCBs using SMT. These plants are equipped with state-of-the-art machinery and skilled personnel to handle the complex process of placing and soldering tiny components onto PCBs.
Key Advantages of PCB Surface Mount Technology
- Miniaturization: SMT allows for smaller component sizes and denser PCB layouts.
- Improved Performance: Shorter lead lengths in SMT Components reduce parasitic capacitance and inductance, enhancing circuit performance.
- Cost-Effective: Automated assembly processes in PCB-SMPs reduce labor costs and increase production efficiency.
- Flexibility: SMT accommodates a wide range of component packages and sizes, enabling design flexibility.
PCB-SMP Assembly Process Overview
The PCB-SMP assembly process consists of several critical steps that ensure the accurate placement and soldering of components onto the PCB. Here’s an overview of the main stages:
1. Solder Paste Application
Solder paste, a mixture of tiny solder particles suspended in a flux medium, is applied to the PCB’s surface using a stencil or screen printing process. The stencil ensures that the solder paste is deposited precisely on the component pads.
2. Component Placement
Surface mount components are placed onto the solder paste-coated pads using high-speed, automated pick-and-place machines. These machines use vacuum nozzles or grippers to pick up components from reels or trays and place them accurately on the PCB.
3. Reflow Soldering
After component placement, the PCB undergoes a reflow soldering process. The board is passed through a reflow oven, which applies a controlled temperature profile to melt the solder particles in the paste, forming a permanent electrical and mechanical connection between the components and the PCB.
4. Inspection and Testing
Following the reflow soldering process, the assembLED PCBs are inspected for any defects or misalignments using automated optical inspection (AOI) systems or manual visual inspection. Electrical testing may also be performed to ensure the functionality of the assembled board.
Advanced Capabilities of PCB-SMPs
Modern PCB-SMPs are equipped with advanced technologies and capabilities that enable them to handle a wide range of PCB Assembly requirements. Some of these key capabilities include:
High-Speed, High-Precision Component Placement
State-of-the-art pick-and-place machines in PCB-SMPs can place components at speeds of up to 100,000 components per hour (CPH) with an accuracy of ±50 microns. This enables the efficient assembly of complex, high-density PCBs.
Multi-Layer PCB Assembly
PCB-SMPs can handle the assembly of multi-layer PCBs, which consist of multiple conductive layers separated by insulating layers. These complex PCBs are essential for advanced electronic devices that require high interconnect density and signal integrity.
Diverse Component Compatibility
SMT allows for the use of a wide range of component packages, including small outline integrated circuits (SOICs), quad flat packages (QFPs), ball grid arrays (BGAs), and chip scale packages (CSPs). PCB-SMPs are capable of handling these various component types and sizes.
Automated Optical Inspection (AOI)
AOI systems in PCB-SMPs use high-resolution cameras and advanced image processing algorithms to detect assembly defects such as component misalignment, solder bridging, or missing components. This automated inspection process ensures the quality and reliability of the assembLED PCBs.
Traceability and Data Management
Modern PCB-SMPs incorporate traceability systems that track components and PCBs throughout the assembly process. This data management capability enables better quality control, inventory management, and facilitates root cause analysis in case of any issues.
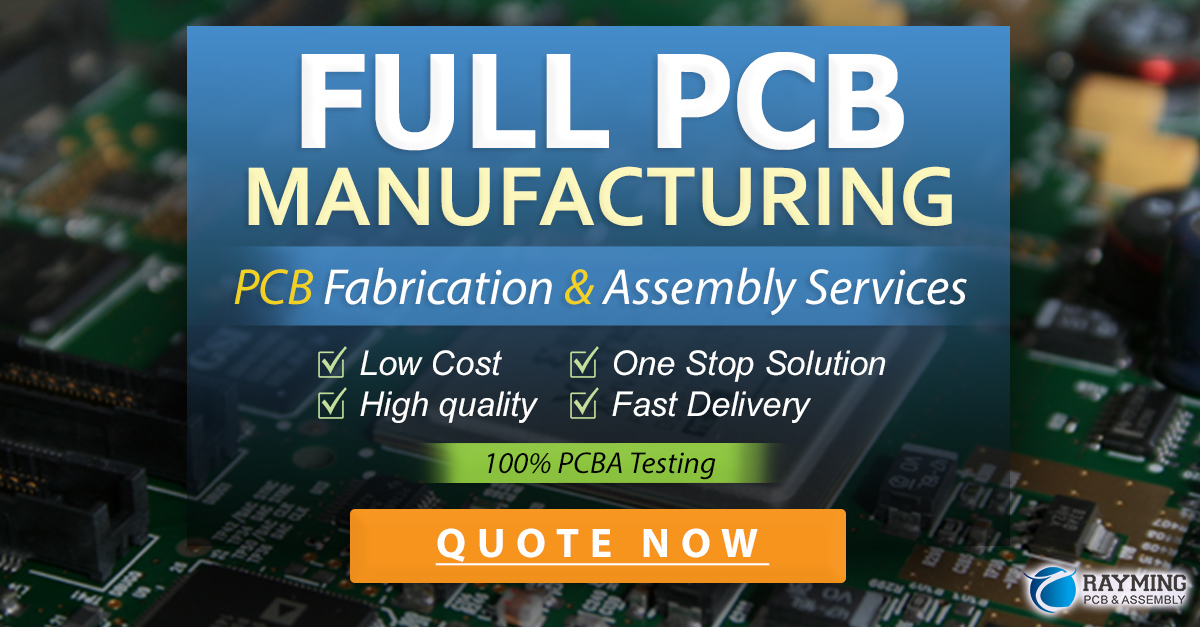
PCB-SMP Performance Metrics
To assess the capability and performance of a PCB-SMP, several key metrics are used:
Metric | Description |
---|---|
First Pass Yield (FPY) | The percentage of PCBs that pass all inspections and tests without requiring rework or repair. Higher FPY indicates better process control and quality. |
Defects Per Million Opportunities (DPMO) | The number of defects found per million components placed. Lower DPMO values signify higher quality and reliability. |
Throughput | The number of PCBs assembled per unit time, often measured in boards per hour (BPH). Higher throughput indicates greater production efficiency. |
Overall Equipment Effectiveness (OEE) | A measure of the overall performance of the PCB-SMP, taking into account factors such as availability, performance, and quality. Higher OEE percentages indicate better overall plant performance. |
Environmental and Sustainability Considerations
As the electronics industry grows, PCB-SMPs are increasingly focusing on environmental sustainability and responsible manufacturing practices. Some key initiatives include:
Lead-Free Soldering
The use of lead-free solder alloys, such as tin-silver-copper (SAC), has become the norm in PCB-SMPs to comply with RoHS (Restriction of Hazardous Substances) regulations and reduce the environmental impact of electronic waste.
Energy Efficiency
PCB-SMPs are implementing energy-efficient equipment and processes to reduce their carbon footprint. This includes the use of low-energy lighting, optimized reflow oven profiles, and energy management systems.
Waste Reduction and Recycling
Efforts are being made to minimize waste generation in PCB-SMPs through the optimization of material usage, the implementation of recycling programs for scrap materials, and the proper disposal of hazardous waste.
Future Trends in PCB-SMP Technology
As the demand for more advanced and miniaturized electronic devices continues to grow, PCB-SMPs are evolving to keep pace with these trends. Some of the future developments in PCB-SMP technology include:
Advanced Packaging Technologies
The adoption of advanced packaging technologies, such as system-in-package (SiP) and package-on-package (PoP), is expected to increase in PCB-SMPs. These technologies enable the integration of multiple die or packages into a single module, further enhancing the miniaturization and functionality of electronic devices.
Flexible and Stretchable Electronics
The development of flexible and stretchable PCBs is gaining momentum, driven by the growing demand for wearable electronics and the Internet of Things (IoT) applications. PCB-SMPs will need to adapt their processes and equipment to handle the assembly of these novel PCB materials.
Industry 4.0 and Smart Manufacturing
The integration of Industry 4.0 technologies, such as the Industrial Internet of Things (IIoT), big data analytics, and machine learning, is expected to transform PCB-SMPs. These technologies will enable real-time process monitoring, predictive maintenance, and adaptive process control, leading to improved efficiency, quality, and agility.
Frequently Asked Questions (FAQ)
-
Q: What is the difference between through-hole and surface mount technology?
A: Through-hole technology involves the insertion of component leads through holes in the PCB, which are then soldered on the opposite side. Surface mount technology, on the other hand, involves the placement of components directly onto the surface of the PCB, with solder connections made on the same side. SMT allows for smaller components and denser PCB layouts compared to through-hole technology. -
Q: Can PCB-SMPs handle both single-sided and double-sided PCB assembly?
A: Yes, modern PCB-SMPs are capable of assembling both single-sided and double-sided PCBs. Double-sided PCB assembly involves the placement and soldering of components on both sides of the board, which requires additional process steps and equipment compared to single-sided assembly. -
Q: What is the role of solder paste in the PCB-SMP assembly process?
A: Solder paste is a critical material in the PCB-SMP assembly process. It consists of tiny solder particles suspended in a flux medium and is applied to the PCB’s surface prior to component placement. The solder paste holds the components in place during the reflow soldering process and forms the electrical and mechanical connection between the components and the PCB. -
Q: How do PCB-SMPs ensure the quality and reliability of assembled PCBs?
A: PCB-SMPs employ various quality control measures to ensure the quality and reliability of assembled PCBs. These include automated optical inspection (AOI) systems that detect assembly defects, electrical testing to verify the functionality of the board, and traceability systems that track components and PCBs throughout the assembly process. Additionally, PCB-SMPs adhere to strict process control and quality management standards to minimize defects and ensure consistent performance. -
Q: What challenges do PCB-SMPs face when assembling miniaturized electronic devices?
A: As electronic devices become smaller and more complex, PCB-SMPs face several challenges in their assembly. These include the handling and placement of extremely small components, the need for higher precision in component placement, and the management of increased heat density during the reflow soldering process. To overcome these challenges, PCB-SMPs invest in advanced equipment, process optimization, and the development of specialized techniques for miniaturized component assembly.
Conclusion
The PCB Surface Mount Plant (PCB-SMP) plays a crucial role in the production of modern electronic devices. Equipped with advanced technologies and capabilities, PCB-SMPs enable the efficient assembly of complex, high-density PCBs using surface mount technology (SMT). From high-speed component placement to automated inspection and traceability, PCB-SMPs ensure the quality, reliability, and performance of assembled PCBs.
As the electronics industry continues to evolve, PCB-SMPs are embracing environmental sustainability, adopting lead-free soldering, energy-efficient processes, and waste reduction initiatives. Looking to the future, PCB-SMPs are poised to integrate advanced packaging technologies, flexible and stretchable electronics, and Industry 4.0 principles to meet the ever-growing demands of the electronics market.
By understanding the capabilities, processes, and performance metrics of PCB-SMPs, electronics manufacturers can make informed decisions when selecting a PCB assembly partner and ensure the successful production of their products.
Leave a Reply