What is PCB Panelization?
PCB panelization is the process of combining multiple printed circuit board (PCB) designs onto a single panel for manufacturing. This technique is commonly used to increase production efficiency and reduce costs. By grouping several smaller PCBs together, manufacturers can optimize the use of materials, minimize handling, and streamline the assembly process.
Benefits of PCB Panelization
- Cost reduction: Panelizing PCBs allows for a more efficient use of materials, reducing waste and lowering overall production costs.
- Increased throughput: Handling multiple PCBs as a single panel speeds up the manufacturing process, resulting in higher output and shorter lead times.
- Improved consistency: Panelization ensures that all PCBs within a panel undergo the same manufacturing conditions, leading to more consistent quality across the boards.
- Simplified assembly: Grouping PCBs together makes it easier to automate the assembly process, reducing the need for manual intervention and minimizing the risk of errors.
PCB Panelization Techniques
There are several techniques used for PCB panelization, each with its own advantages and considerations. The choice of technique depends on factors such as the PCB design, material, and the intended application. Some common panelization methods include:
Tab Routing
Tab routing involves connecting individual PCBs with thin strips of material called tabs. These tabs hold the boards together during manufacturing and are later removed during the depaneling process. Tab routing offers several benefits:
- Easy to implement and cost-effective
- Suitable for a wide range of PCB designs and materials
- Allows for efficient use of panel space
However, tab routing also has some limitations:
- Requires additional panel space for the tabs
- May leave behind small protrusions on the board edges after depaneling
- Not suitable for designs with intricate or delicate edges
V-Scoring
V-scoring is a technique that uses a V-shaped groove to create a weak point between individual PCBs. This groove is cut partially through the panel, allowing the boards to be easily separated after manufacturing. V-scoring offers several advantages:
- Provides clean, smooth edges after depaneling
- Minimizes the risk of damage to the PCBs during separation
- Suitable for designs with tight tolerances or delicate components near the edges
However, V-scoring also has some drawbacks:
- Requires specialized equipment for creating the V-grooves
- May weaken the overall strength of the panel
- Not suitable for thick or rigid PCB materials
Perforated Breakaway
Perforated breakaway panelization involves creating a series of small, closely spaced holes along the edges of individual PCBs. These perforations weaken the material, allowing the boards to be easily separated by breaking along the perforated lines. This method offers several benefits:
- Easy to implement and cost-effective
- Provides clean, smooth edges after depaneling
- Suitable for a wide range of PCB designs and materials
However, perforated breakaway also has some limitations:
- Requires additional panel space for the perforations
- May leave behind small protrusions on the board edges after depaneling
- Not suitable for designs with components near the edges
Considerations for PCB Panelization
When designing PCBs for panelization, there are several factors to consider to ensure a successful manufacturing process. Some key considerations include:
Panel Size and Layout
The size and layout of the panel should be optimized to maximize the number of PCBs that can fit while leaving enough space for panelization features such as tabs, grooves, or perforations. It’s essential to work closely with the manufacturer to determine the optimal panel size and layout for your specific PCB design.
Material Selection
The choice of PCB material can impact the panelization process. Some materials, such as rigid PCBs, may require different panelization techniques compared to flexible or Rigid-flex PCBs. It’s important to select a material that is compatible with the intended panelization method and can withstand the stresses of the manufacturing process.
Component Placement
When designing PCBs for panelization, it’s crucial to consider the placement of components near the board edges. Components that are too close to the edges may be damaged during the depaneling process or may interfere with panelization features such as tabs or perforations. It’s recommended to keep a sufficient clearance between components and the board edges to ensure a smooth panelization and depaneling process.
Depaneling Method
The choice of depaneling method should be based on the specific requirements of the PCB design and the intended application. Some common depaneling methods include:
- Manual breakaway: Suitable for low-volume production or prototyping
- Mechanical routing: Offers clean, precise cuts but may be more time-consuming
- Laser cutting: Provides high precision and minimal stress on the PCBs but requires specialized equipment
It’s essential to discuss the depaneling options with the manufacturer to determine the most suitable method for your PCB panelization project.
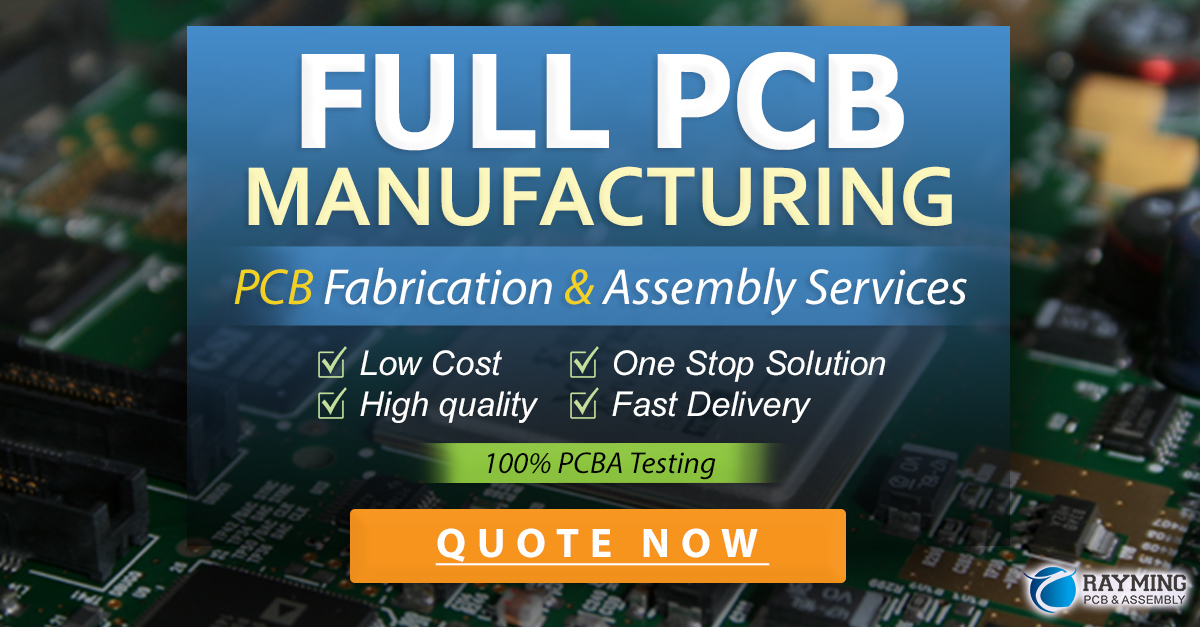
PCB Panelization at Screaming Circuits
At Screaming Circuits, we offer professional PCB panelization services to help our customers optimize their PCB designs for manufacturing. Our experienced team works closely with clients to determine the best panelization approach based on their specific requirements, taking into account factors such as PCB design, material, and intended application.
Our Panelization Process
- Design review: Our team reviews the customer’s PCB design to identify any potential issues or challenges related to panelization.
- Panelization strategy: We work with the customer to develop an optimal panelization strategy, considering factors such as panel size, layout, and depaneling method.
- Panel creation: Our skilled technicians create the panelized PCB design, ensuring that all panelization features are properly implemented and the design is optimized for manufacturing.
- Manufacturing: We manufacture the panelized PCBs using state-of-the-art equipment and strict quality control measures to ensure consistent, high-quality results.
- Depaneling: After manufacturing, we depanel the PCBs using the chosen method, such as manual breakaway, mechanical routing, or laser cutting, depending on the customer’s requirements.
Benefits of PCB Panelization with Screaming Circuits
- Expert guidance: Our experienced team provides expert advice and support throughout the panelization process, helping customers optimize their PCB designs for manufacturing.
- Customized solutions: We offer tailored panelization solutions based on each customer’s unique requirements, ensuring the best possible results for their specific PCB design and application.
- High-quality manufacturing: Our state-of-the-art equipment and strict quality control measures ensure consistent, high-quality PCBs, even in high-volume production runs.
- Fast turnaround: We understand the importance of timely delivery and work efficiently to provide fast turnaround times without compromising on quality.
Conclusion
PCB panelization is a critical process in the manufacturing of printed circuit boards, offering numerous benefits such as cost reduction, increased throughput, and improved consistency. By understanding the various panelization techniques and considerations, designers and manufacturers can optimize their PCB designs for efficient and cost-effective production.
At Screaming Circuits, we are committed to providing our customers with expert PCB panelization services, helping them achieve the best possible results for their PCB projects. With our experienced team, customized solutions, and high-quality manufacturing, we are the ideal partner for all your PCB panelization needs.
Frequently Asked Questions (FAQ)
- What is the minimum clearance required between components and board edges for PCB panelization?
-
The minimum clearance between components and board edges varies depending on the panelization method and the specific PCB design. However, a general rule of thumb is to maintain a clearance of at least 1.5mm to ensure a smooth panelization and depaneling process.
-
Can PCB panelization be used for flexible or rigid-flex PCBs?
-
Yes, PCB panelization can be used for flexible and rigid-flex PCBs, but the panelization techniques and considerations may differ from those used for rigid PCBs. It’s essential to work closely with the manufacturer to determine the best panelization approach for your specific flexible or rigid-flex PCB design.
-
How does PCB panelization affect the overall cost of PCB manufacturing?
-
PCB panelization can significantly reduce the overall cost of PCB manufacturing by optimizing the use of materials, minimizing handling, and streamlining the assembly process. By grouping multiple PCBs together on a single panel, manufacturers can reduce waste, increase throughput, and ultimately lower production costs.
-
What is the difference between tab routing and v-scoring in PCB panelization?
-
Tab routing involves connecting individual PCBs with thin strips of material called tabs, which are later removed during the depaneling process. V-scoring, on the other hand, uses a V-shaped groove to create a weak point between individual PCBs, allowing for easy separation after manufacturing. Tab routing is more suitable for a wide range of PCB designs and materials, while v-scoring provides clean, smooth edges and is better suited for designs with tight tolerances or delicate components near the edges.
-
How do I choose the best depaneling method for my PCB panelization project?
- The choice of depaneling method depends on several factors, such as the PCB design, material, and intended application. Manual breakaway is suitable for low-volume production or prototyping, mechanical routing offers clean, precise cuts but may be more time-consuming, and laser cutting provides high precision and minimal stress on the PCBs but requires specialized equipment. It’s essential to discuss the depaneling options with the manufacturer to determine the most suitable method for your specific PCB panelization project.
Leave a Reply