What Are LED PCBs?
LED PCBs are specialized printed circuit boards designed to support and interconnect LEDs. They provide a stable platform for mounting LEDs and ensure proper electrical connections, heat dissipation, and mechanical stability. LED PCBs are typically made from materials such as FR-4, aluminum, or ceramics, depending on the specific requirements of the application.
Components of LED PCBs
LED PCBs consist of several key components that work together to ensure optimal LED performance:
- Substrate: The base material of the PCB, which provides mechanical support and electrical insulation.
- Copper Layers: Conductive paths that carry electrical signals and power to the LEDs.
- Solder Mask: A protective layer that prevents short circuits and enhances the PCB’s durability.
- Silkscreen: A printed layer that provides labels, logos, and other identifying information.
- LED Pads: Designated areas on the PCB where LEDs are mounted and soldered.
LED PCB Manufacturing Process
The manufacturing process of LED PCBs involves several stages, each critical to ensuring the quality and reliability of the final product.
PCB Design and Layout
The first step in LED PCB manufacturing is designing the circuit schematic and creating the PCB layout. This involves determining the optimal placement of LEDs, routing the electrical connections, and incorporating any necessary components such as resistors, capacitors, or drivers. Specialized PCB Design Software is used to create the layout, which is then sent for fabrication.
PCB fabrication
The PCB fabrication process begins with the creation of a copper-clad laminate, which serves as the substrate for the LED PCB. The copper layer is then patterned using a photolithography process, where the desired circuit pattern is transferred onto the copper using a photomask and light-sensitive resist. The unwanted copper is etched away, leaving behind the conductive traces.
Solder Mask Application
After the copper patterning, a solder mask is applied to the PCB. The solder mask is a protective layer that covers the copper traces, leaving only the LED pads and other components exposed. This layer prevents short circuits, provides insulation, and improves the PCB’s durability.
Silkscreen Printing
The silkscreen layer is then printed onto the PCB, providing labels, logos, and other identifying information. This layer helps in the assembly process and makes it easier to identify components and their orientations.
Component Assembly
Once the PCB fabrication is complete, the LED components are assembled onto the board. This process typically involves automated Pick-and-place machines that precisely position the LEDs and other components onto their designated pads. The components are then soldered onto the PCB using reflow soldering or Wave Soldering techniques.
Testing and Quality Control
After assembly, the LED PCBs undergo rigorous testing and quality control procedures to ensure their functionality, reliability, and adherence to specifications. This may include visual inspections, electrical tests, and burn-in tests to identify any defects or performance issues.
LED PCB Design Considerations
Designing an LED PCB requires careful consideration of various factors to ensure optimal performance, reliability, and longevity. Some key design considerations include:
Thermal Management
LEDs generate heat during operation, which can impact their performance and lifespan. Effective thermal management is crucial in LED PCB design. This can be achieved through the use of heat sinks, thermal vias, or Metal-Core PCBs (MCPCBs) that efficiently dissipate heat away from the LEDs.
Current and Voltage Requirements
LEDs have specific current and voltage requirements that must be met for proper operation. The LED PCB design must incorporate appropriate current limiting resistors and ensure that the power supply can deliver the required current and voltage to each LED.
LED Placement and Spacing
The placement and spacing of LEDs on the PCB can affect the overall light output, uniformity, and visual appearance. Proper spacing between LEDs helps prevent thermal crosstalk and ensures even light distribution. The design should also consider the viewing angle and intensity requirements of the application.
Color Consistency
In applications where color consistency is critical, such as in display backlighting or architectural lighting, the LED PCB design must account for variations in LED binning and color temperature. Careful selection and grouping of LEDs with similar characteristics can help achieve a uniform color output.
Electrical Isolation and Protection
LED PCBs often require electrical isolation and protection features to ensure safe and reliable operation. This may include the use of optocouplers, surge protection devices, or conformal coatings to protect against electrical interference, static discharge, or environmental factors.
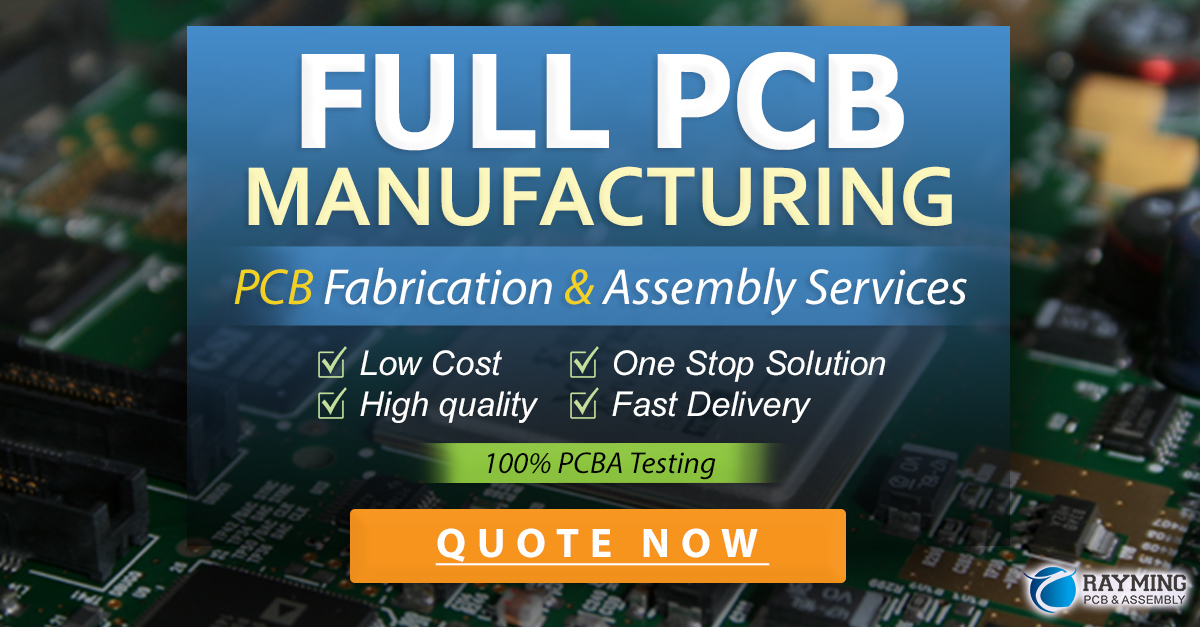
Applications of LED PCBs
LED PCBs find applications in a wide range of industries and products, leveraging the benefits of LEDs such as energy efficiency, long lifespan, and design flexibility. Some common applications include:
Lighting
LED PCBs are extensively used in various lighting applications, including:
- General illumination: Residential, commercial, and industrial lighting fixtures.
- Automotive lighting: Headlights, taillights, and interior lighting.
- Street lighting: Roadway, parking lot, and public space lighting.
- Backlighting: Display backlighting for televisions, monitors, and mobile devices.
Signage and Displays
LED PCBs are commonly used in signage and display applications, such as:
- Digital signage: Advertising displays, information boards, and menu boards.
- LED video walls: Large-scale displays for events, stadiums, and public spaces.
- Channel letters: Illuminated lettering for storefronts and building signage.
Medical Devices
LED PCBs are utilized in various medical devices and applications, including:
- Endoscopy: Illumination for minimally invasive surgical procedures.
- Phototherapy: Treatment of skin conditions such as jaundice and psoriasis.
- Dental curing: Light-curing of dental composites and adhesives.
Horticulture
LED PCBs are increasingly used in horticultural lighting applications, such as:
- Grow lights: Illumination for indoor plant growth and greenhouse cultivation.
- Vertical farming: Efficient lighting solutions for urban and indoor farming.
Automotive and Transportation
LED PCBs find applications in the automotive and transportation industries, including:
- Interior lighting: Ambient lighting, reading lights, and instrument panel illumination.
- Exterior lighting: Headlights, taillights, and turn signals.
- Transportation lighting: Lighting for buses, trains, and aircraft.
Frequently Asked Questions (FAQ)
-
What are the advantages of using LED PCBs over traditional lighting methods?
LED PCBs offer several advantages over traditional lighting methods, including higher energy efficiency, longer lifespan, compact size, design flexibility, and improved color rendering. They also generate less heat and require lower maintenance compared to incandescent or fluorescent lighting. -
Can LED PCBs be customized for specific applications?
Yes, LED PCBs can be customized to meet the specific requirements of different applications. This includes the choice of substrate material, LED type and arrangement, thermal management features, and electrical characteristics. Customization allows for optimal performance and integration into the desired application. -
What is the typical lifespan of an LED PCB?
The lifespan of an LED PCB depends on various factors such as the quality of components, operating conditions, and thermal management. However, LED PCBs generally have a long lifespan compared to traditional lighting solutions. High-quality LED PCBs can last for tens of thousands of hours, often exceeding 50,000 hours of continuous operation. -
How do I choose the right LED PCB for my application?
Choosing the right LED PCB for your application involves considering several factors, such as the desired light output, color temperature, power requirements, thermal management needs, and environmental conditions. It’s important to consult with LED PCB manufacturers or suppliers who can provide guidance based on your specific requirements and help you select the most suitable solution. -
What are the challenges in LED PCB manufacturing, and how are they addressed?
LED PCB manufacturing faces challenges such as ensuring proper thermal management, achieving consistent color output, and maintaining high reliability. These challenges are addressed through careful design considerations, material selection, and manufacturing processes. Techniques such as using thermally conductive substrates, implementing effective cooling mechanisms, and employing strict quality control measures help overcome these challenges and ensure the production of high-quality LED PCBs.
Conclusion
LED PCBs have revolutionized the lighting industry by providing an efficient, versatile, and reliable solution for incorporating LEDs into various applications. Understanding the fundamentals of LED PCBs, their manufacturing process, design considerations, and applications is crucial for anyone involved in the development or integration of LED-based products.
By leveraging the advantages of LED PCBs, designers and manufacturers can create innovative lighting solutions that meet the growing demands for energy efficiency, performance, and design flexibility. As LED technology continues to advance, the potential applications and benefits of LED PCBs will only expand, driving further innovations in the lighting industry and beyond.
Leave a Reply