Introduction to Metal-Core PCB and Its Advantages in LED Applications
Metal-Core PCB (MCPCB) is a specialized type of printed circuit board that has gained significant popularity in LED-based products due to its superior thermal management properties. Unlike standard PCBs, which are made entirely of FR-4 or other dielectric materials, MCPCBs feature a metal core that acts as a heat sink, efficiently dissipating heat generated by the LED components. This article will explore the reasons why MCPCBs are preferred over standard PCBs in LED applications, and how they contribute to enhanced performance, reliability, and longevity of LED-based products.
What is a Metal-Core PCB?
A Metal-Core PCB is a printed circuit board that consists of a metal core, typically aluminum, sandwiched between a thin layer of dielectric material and a copper circuit layer. The metal core serves as a heat spreader, quickly conducting heat away from the LED components mounted on the board. This unique construction allows MCPCBs to offer several advantages over standard PCBs in terms of thermal management, power handling, and mechanical stability.
Advantages of Metal-Core PCBs in LED Applications
- Superior Thermal Management
- Increased Power Handling Capability
- Enhanced Mechanical Stability
- Improved Reliability and Longevity
- Cost-Effectiveness in High-Power Applications
How Metal-Core PCBs Enhance Thermal Management in LED Products
Understanding the Importance of Thermal Management in LEDs
LEDs are highly sensitive to temperature fluctuations, and their performance, efficiency, and lifespan are significantly affected by the heat generated during operation. As LEDs become more powerful and compact, effective thermal management becomes increasingly critical to ensure optimal performance and prevent premature failure. Standard PCBs, which rely solely on the copper layers and dielectric material for heat dissipation, often struggle to provide adequate thermal management in high-power LED applications.
The Role of Metal Core in Heat Dissipation
The metal core in MCPCBs acts as a highly efficient heat spreader, quickly conducting heat away from the LED components and distributing it evenly across the board. Aluminum, the most commonly used metal core material, has a thermal conductivity of approximately 200 W/mK, which is significantly higher than the thermal conductivity of FR-4 (0.3 W/mK), the primary material used in standard PCBs. This superior thermal conductivity allows MCPCBs to dissipate heat more effectively, reducing the operating temperature of the LEDs and preventing thermal damage.
Comparing Thermal Performance of MCPCBs and Standard PCBs
To illustrate the difference in thermal performance between MCPCBs and standard PCBs, consider the following table:
PCB Type | Thermal Conductivity (W/mK) | Thermal Resistance (°C/W) | Maximum Power Density (W/cm²) |
---|---|---|---|
Standard PCB (FR-4) | 0.3 | 10-20 | 1-2 |
Metal-Core PCB (Aluminum) | 150-200 | 0.5-1.5 | 5-10 |
As shown in the table, MCPCBs offer significantly lower thermal resistance and higher power density compared to standard PCBs. This translates to better heat dissipation, lower LED junction temperatures, and the ability to handle higher power levels without compromising performance or reliability.
Power Handling and Mechanical Stability Advantages of Metal-Core PCBs
Increased Power Handling Capability
The superior thermal management properties of MCPCBs allow them to handle higher power levels compared to standard PCBs. As LEDs become more powerful, the ability to dissipate heat effectively becomes crucial in maintaining optimal performance and preventing thermal runaway. With their metal core acting as a heat sink, MCPCBs can support higher power densities without experiencing thermal stress or degradation.
Enhanced Mechanical Stability
The metal core in MCPCBs not only improves thermal performance but also provides enhanced mechanical stability to the board. The rigid metal core reduces board warpage and thermal expansion, which can cause mechanical stress on the LED components and lead to premature failure. This increased stability is particularly important in applications where the LED board is subjected to vibration, shock, or extreme temperature variations.
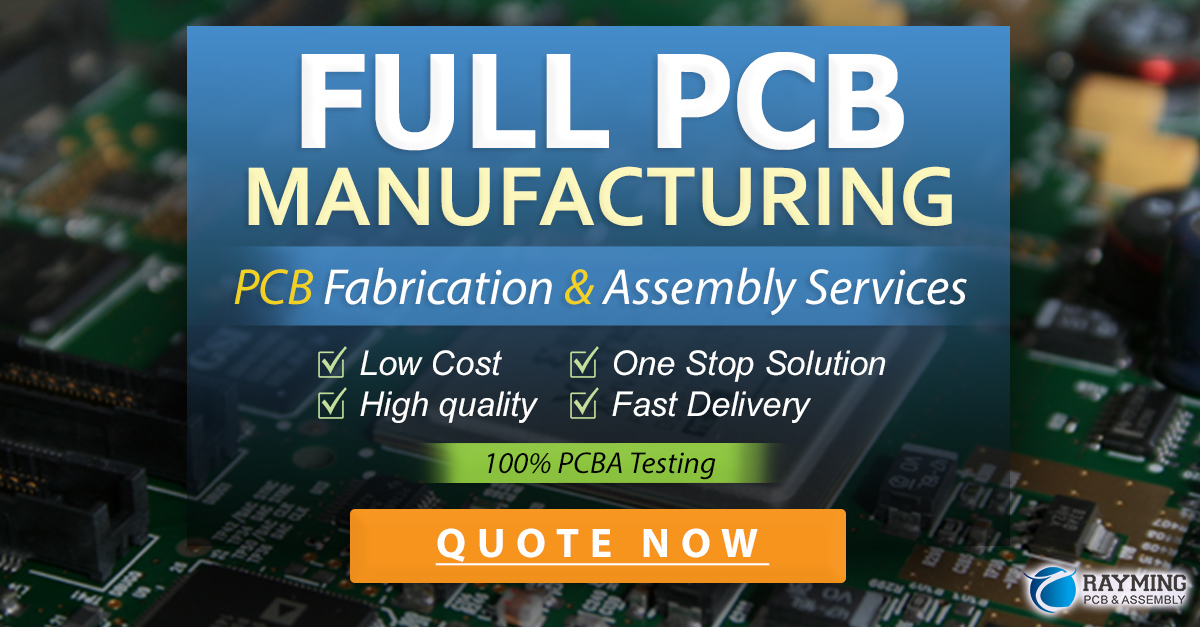
Reliability, Longevity, and Cost-Effectiveness of Metal-Core PCBs in LED Products
Improved Reliability and Longevity
The use of MCPCBs in LED-based products contributes to improved reliability and longevity of the LEDs. By effectively managing the heat generated by the LEDs, MCPCBs help maintain lower junction temperatures, which is a critical factor in determining the lifespan of an LED. Higher temperatures can cause accelerated degradation of the LED package, leading to reduced light output and eventual failure. By keeping the LED temperature within the optimal range, MCPCBs help extend the service life of LED-based products.
Cost-Effectiveness in High-Power Applications
While MCPCBs may have a higher initial cost compared to standard PCBs, they offer significant cost advantages in high-power LED applications. The improved thermal management and power handling capabilities of MCPCBs allow for the use of fewer LEDs to achieve the desired light output, reducing the overall component count and assembly costs. Additionally, the extended lifespan of LEDs mounted on MCPCBs results in lower maintenance and replacement costs over the product’s lifetime.
Frequently Asked Questions (FAQ)
-
Q: Can Metal-Core PCBs be used with any type of LED?
A: MCPCBs are compatible with most types of LEDs, including high-power, COB, and SMD LEDs. However, it is essential to consider the specific requirements of the LED, such as voltage, current, and thermal characteristics, when designing the MCPCB Layout. -
Q: What are the common metal core materials used in MCPCBs?
A: Aluminum is the most widely used metal core material in MCPCBs due to its excellent thermal conductivity, lightweight nature, and cost-effectiveness. Other materials, such as copper and copper-molybdenum alloys, are also used in specialized applications that require even higher thermal performance. -
Q: How does the dielectric layer in MCPCBs affect thermal performance?
A: The dielectric layer in MCPCBs serves as an electrical insulator between the metal core and the copper circuit layer. While the dielectric layer is essential for the proper functioning of the board, it also acts as a thermal barrier. To minimize the impact on thermal performance, the dielectric layer in MCPCBs is typically made as thin as possible while still maintaining the required electrical insulation properties. -
Q: Can Metal-Core PCBs be manufactured with the same design rules as standard PCBs?
A: MCPCBs generally follow similar design rules as standard PCBs, but there are some specific considerations to keep in mind. These include the choice of dielectric material, the thickness of the dielectric layer, and the thermal management requirements of the LED components. It is essential to work with a PCB manufacturer experienced in MCPCB Fabrication to ensure optimal design and manufacturing. -
Q: Are Metal-Core PCBs suitable for all LED-based products?
A: While MCPCBs offer significant advantages in terms of thermal management and power handling, they may not be necessary for all LED-based products. In applications where the LED power density is low, and the ambient temperature is well-controlled, standard PCBs may provide sufficient thermal management. However, for high-power LED applications or products operating in challenging environmental conditions, MCPCBs are often the preferred choice for ensuring optimal performance and reliability.
Conclusion
Metal-Core PCBs have emerged as the go-to solution for LED-based products that demand superior thermal management, increased power handling, and enhanced reliability. By incorporating a metal core as a heat spreader, MCPCBs effectively dissipate heat generated by the LEDs, maintaining lower junction temperatures and preventing thermal damage. This, in turn, leads to improved performance, extended lifespan, and cost-effectiveness in high-power LED applications.
As the LED industry continues to evolve, with ever-increasing power densities and more demanding applications, the importance of effective thermal management will only grow. Metal-Core PCBs, with their unique construction and superior thermal properties, are well-positioned to meet these challenges and enable the development of next-generation LED-based products that push the boundaries of performance, efficiency, and reliability.
Leave a Reply