Introduction to PCB Cores
At the heart of every printed circuit board (PCB) lies its core, a fundamental component that provides the foundation for the board’s structural integrity and electrical performance. The core of a PCB is a critical element that plays a significant role in determining the overall quality, reliability, and functionality of the circuit board. In this comprehensive article, we will delve into the intricacies of PCB cores, exploring their composition, types, and the crucial role they play in the manufacturing process.
What is a PCB Core?
A PCB core, also known as the substrate or base material, is the central layer of a printed circuit board. It is typically made of a non-conductive material, such as fiberglass or epoxy resin, which provides a stable and insulating platform for the copper traces and components that make up the circuit. The core acts as the backbone of the PCB, offering mechanical support and electrical insulation between the conductive layers.
The Importance of PCB Cores
The core of a PCB is essential for several reasons:
-
Structural Integrity: The core provides the necessary rigidity and strength to the PCB, ensuring that it can withstand the stresses and strains of the manufacturing process and the demands of its intended application.
-
Electrical Insulation: The non-conductive nature of the core material prevents short circuits and unwanted electrical interactions between the conductive layers of the PCB.
-
Thermal Stability: The core helps to dissipate heat generated by the components and circuitry, preventing overheating and ensuring the long-term reliability of the PCB.
-
Dimensional Stability: The core maintains the PCB’s shape and size, even under varying environmental conditions, such as temperature fluctuations and humidity changes.
Types of PCB Cores
PCB cores can be classified into several categories based on their composition and properties. Each type of core material has its own unique characteristics, advantages, and limitations, making it suitable for specific applications and requirements.
FR-4 Core
FR-4 (Flame Retardant 4) is the most commonly used core material in the PCB industry. It is a composite material made of woven fiberglass cloth impregnated with epoxy resin. FR-4 offers excellent mechanical and electrical properties, making it an ideal choice for a wide range of applications.
Advantages of FR-4 Core:
– High mechanical strength and durability
– Good electrical insulation properties
– Excellent thermal stability
– Flame retardant
– Cost-effective
CEM-3 Core
CEM-3 (Composite Epoxy Material 3) is another popular core material used in PCB manufacturing. It is a composite of woven fiberglass cloth and epoxy resin, similar to FR-4, but with a lower glass-to-resin ratio. CEM-3 is often used as a more economical alternative to FR-4 in less demanding applications.
Advantages of CEM-3 Core:
– Lower cost compared to FR-4
– Good mechanical strength
– Adequate electrical insulation properties
– Suitable for general-purpose applications
Polyimide Core
Polyimide is a high-performance polymer material known for its exceptional thermal and chemical resistance. Polyimide cores are used in applications that require the PCB to withstand extreme temperatures and harsh environments.
Advantages of Polyimide Core:
– Excellent thermal stability (up to 260°C)
– High chemical resistance
– Good mechanical strength
– Low dielectric constant and loss
Aluminum Core
Aluminum Core PCBs, also known as Metal Core PCBs (MCPCBs), feature a thin layer of aluminum as the core material. The aluminum core offers superior thermal conductivity, allowing for efficient heat dissipation from high-power components.
Advantages of Aluminum Core:
– Excellent thermal conductivity
– Improved heat dissipation
– Reduced thermal stress on components
– Suitable for high-power applications, such as LED lighting and power electronics
PCB Core Thickness
The thickness of a PCB core is another critical factor that influences the board’s performance and manufacturability. The core thickness is typically measured in mils (thousandths of an inch) or millimeters.
Common PCB Core Thicknesses:
– 0.8 mm (31 mil)
– 1.0 mm (39 mil)
– 1.2 mm (47 mil)
– 1.6 mm (63 mil)
– 2.0 mm (79 mil)
The choice of core thickness depends on several factors, including:
-
Application Requirements: The intended use of the PCB dictates the necessary structural strength and rigidity, which in turn influences the core thickness.
-
Layer Count: The number of conductive layers in the PCB affects the overall thickness of the board. Multi-layer PCBs often require thicker cores to accommodate the additional layers and maintain structural integrity.
-
Component Placement: The size and weight of the components mounted on the PCB can impact the required core thickness to ensure proper support and prevent warping or deformation.
-
Manufacturing Constraints: The PCB manufacturing process and the capabilities of the fabrication facility may limit the available core thicknesses.
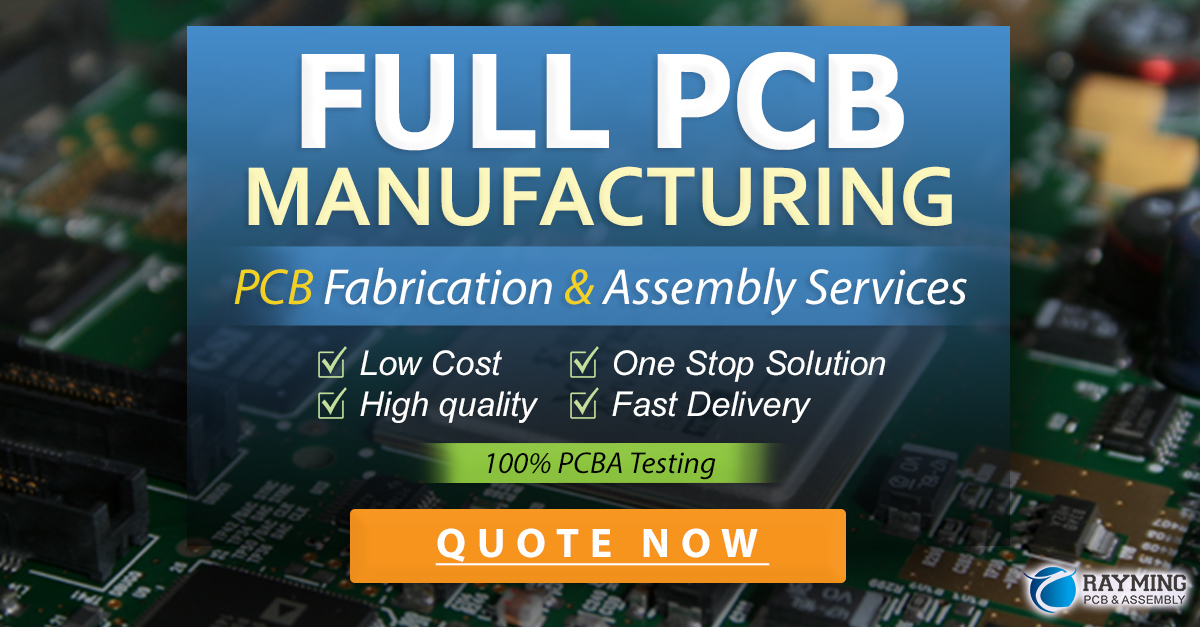
The Role of PCB Cores in Manufacturing
The core of a PCB plays a crucial role throughout the manufacturing process, from design to fabrication and assembly.
PCB Design Considerations
When designing a PCB, engineers must consider the properties and limitations of the chosen core material. The core’s dielectric constant, thermal conductivity, and mechanical strength influence the design decisions, such as trace width, spacing, and via size.
Fabrication Process
The PCB fabrication process begins with the preparation of the core material. The core is cut to the desired size and shape, and the conductive layers are laminated onto its surface. The lamination process involves applying heat and pressure to bond the copper foil to the core material.
After lamination, the PCB undergoes a series of processes, including drilling, plating, and etching, to create the desired circuit pattern on the conductive layers. The core’s stability and uniformity are essential for ensuring the accuracy and reliability of these processes.
Assembly and Reliability
The core’s mechanical and thermal properties play a significant role in the assembly and long-term reliability of the PCB. The core must provide adequate support for the components and withstand the stresses of the soldering process. Additionally, the core’s thermal conductivity helps to dissipate heat generated by the components, preventing overheating and ensuring the PCB’s longevity.
FAQs
-
What is the most common PCB core material?
The most common PCB core material is FR-4, a composite of woven fiberglass cloth and epoxy resin. FR-4 is widely used due to its excellent mechanical, electrical, and thermal properties, as well as its cost-effectiveness. -
Can I use different core materials in the same PCB?
Yes, it is possible to use different core materials in the same PCB, creating a hybrid or multi-material board. This approach is often used when specific areas of the PCB require different properties, such as high thermal conductivity or improved mechanical strength. -
How does the core thickness affect the PCB’s performance?
The core thickness influences the PCB’s structural integrity, rigidity, and ability to support the mounted components. Thicker cores provide better mechanical stability and can accommodate more conductive layers, while thinner cores are suitable for applications that require flexibility or reduced overall board thickness. -
What are the advantages of using an aluminum core PCB?
Aluminum core PCBs offer superior thermal conductivity, allowing for efficient heat dissipation from high-power components. This makes them ideal for applications that generate significant amounts of heat, such as LED lighting, power electronics, and automotive systems. -
How do I choose the right core material for my PCB?
Choosing the right core material depends on several factors, including the intended application, environmental conditions, required electrical and mechanical properties, and budget constraints. Consult with a PCB manufacturer or design expert to determine the most suitable core material for your specific needs.
Conclusion
The core of a PCB is a critical component that forms the foundation of the entire circuit board. It provides the necessary structural support, electrical insulation, and thermal stability required for the proper functioning and reliability of the PCB. Understanding the different types of core materials, their properties, and their impact on the manufacturing process is essential for designing and producing high-quality PCBs.
By selecting the appropriate core material and thickness, engineers can ensure that their PCBs meet the specific requirements of their intended application, whether it be in terms of mechanical strength, thermal management, or electrical performance. As technology advances and new materials emerge, the role of PCB cores will continue to evolve, enabling the development of more advanced and reliable electronic devices.
Leave a Reply