What is a Metal Core PCB (MCPCB)?
A Metal Core Printed Circuit Board (MCPCB) is a specialized type of PCB that incorporates a metal substrate as its base material instead of the traditional FR-4 or other dielectric materials. The metal substrate, typically aluminum or copper, provides excellent thermal conductivity, allowing for efficient heat dissipation from high-power electronic components. MCPCBs are widely used in applications that require effective thermal management, such as LED lighting, power electronics, and automotive systems.
Key Features of MCPCBs
- Thermal Conductivity: The metal core acts as a heat spreader, rapidly transferring heat away from components and distributing it evenly across the board.
- Electrical Insulation: A thin dielectric layer is applied on top of the metal core to provide electrical insulation between the metal and the copper traces.
- Mechanical Strength: The metal core provides enhanced mechanical strength and rigidity compared to traditional PCBs.
- Lightweight: Despite the metal core, MCPCBs are relatively lightweight due to the thin metal substrate and the absence of heavy heat sinks.
Advantages of Using MCPCBs
Enhanced Thermal Management
The primary advantage of using MCPCBs is their superior thermal management capabilities. The metal core acts as an integrated heat sink, efficiently conducting heat away from power-hungry components such as LEDs, power transistors, and voltage regulators. This improved thermal dissipation helps to maintain optimal operating temperatures, prevent thermal runaway, and extend the lifespan of the components.
Increased Power Density
With the ability to dissipate heat more effectively, MCPCBs allow for higher power densities compared to traditional PCBs. This means that more power can be delivered to the components without the risk of overheating, enabling the design of compact and high-performance electronic systems.
Improved Reliability
The enhanced thermal management provided by MCPCBs contributes to improved overall system reliability. By keeping the components within their safe operating temperature range, the risk of thermal-related failures is significantly reduced. This is particularly important in applications where reliability is critical, such as automotive electronics, industrial controls, and medical devices.
Cost and Space Savings
MCPCBs eliminate the need for separate heat sinks or other external cooling solutions, leading to cost and space savings in the overall system design. The integrated metal core serves as a built-in heat sink, reducing the number of components required and simplifying the assembly process.
MCPCB Manufacturing Process
The manufacturing process of MCPCBs involves several key steps to ensure proper thermal and electrical performance:
- Metal Core Preparation: The metal substrate, typically aluminum or copper, is cleaned and treated to remove any impurities and improve adhesion.
- Dielectric Layer Application: A thin layer of dielectric material, such as polyimide or epoxy, is applied onto the metal core. This layer provides electrical insulation between the metal and the copper traces.
- Copper Foil Lamination: A copper foil is laminated onto the dielectric layer using heat and pressure. The copper foil will form the conductive traces and pads on the MCPCB.
- Circuit Patterning: The desired circuit pattern is transferred onto the copper foil using photolithography or other imaging techniques. This involves applying a photoresist, exposing it to light through a patterned mask, and developing the resist to reveal the circuit pattern.
- Etching: The unwanted copper areas are etched away using a chemical etching process, leaving behind the desired copper traces and pads.
- Solder Mask Application: A solder mask layer is applied over the copper traces to protect them from oxidation and provide insulation. Openings are left in the solder mask for component pads and exposed copper areas.
- Surface Finish: A surface finish, such as HASL (Hot Air Solder Leveling), ENIG (Electroless Nickel Immersion Gold), or OSP (Organic Solderability Preservative), is applied to the exposed copper areas to improve solderability and protect against corrosion.
- Fabrication: The MCPCB panel is drilled, routed, and fabricated to the desired shape and size.
- Quality Control: The finished MCPCBs undergo thorough quality control checks to ensure they meet the required specifications and performance standards.
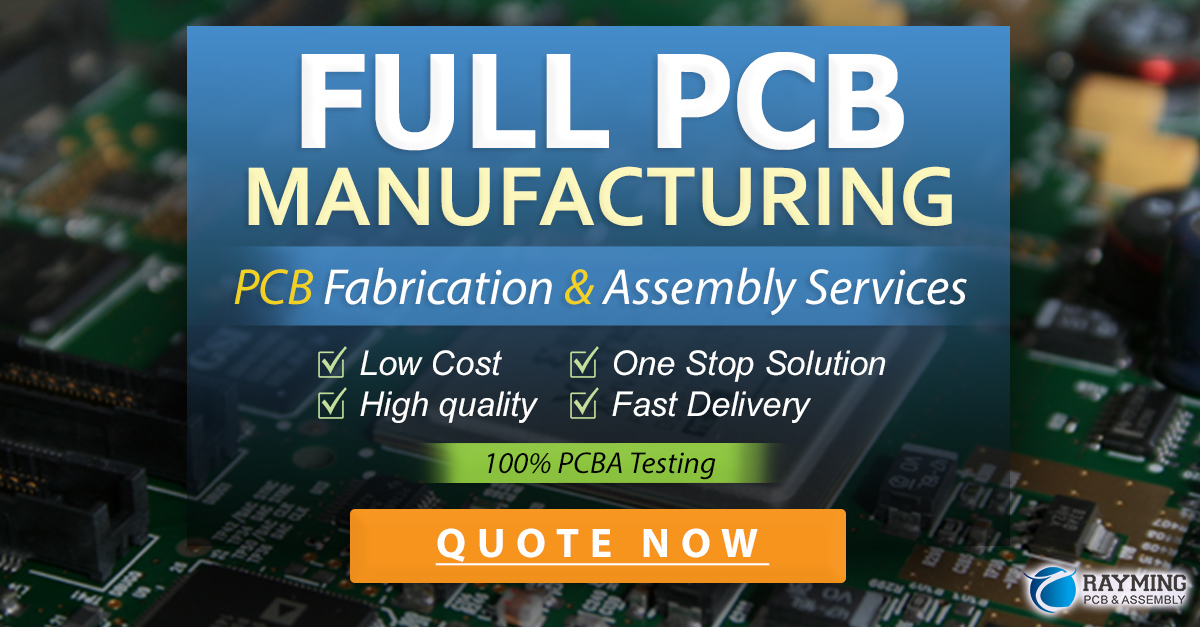
MCPCB Materials
The choice of materials used in MCPCBs is crucial for achieving optimal thermal and electrical performance. Here are the common materials used in MCPCB construction:
Metal Core Materials
- Aluminum: Aluminum is the most widely used metal core material due to its excellent thermal conductivity, lightweight nature, and cost-effectiveness. It is suitable for most MCPCB applications.
- Copper: Copper has higher thermal conductivity than aluminum but is more expensive and heavier. It is used in high-performance applications that require maximum heat dissipation.
Dielectric Materials
- Polyimide: Polyimide is a high-temperature resistant polymer with good electrical insulation properties. It is commonly used as the dielectric layer in MCPCBs.
- Epoxy: Epoxy-based dielectric materials offer good adhesion and thermal stability. They are often used in combination with ceramic fillers to enhance thermal conductivity.
- Ceramic-Filled: Ceramic-filled dielectric materials, such as aluminum oxide or boron nitride, provide excellent thermal conductivity and electrical insulation. They are used in high-power applications.
Copper Foil
The copper foil used in MCPCBs is typically high-purity, low-profile copper with a thickness ranging from 0.5 oz to 4 oz. The choice of copper thickness depends on the current-carrying requirements and the desired thermal performance.
MCPCB Design Considerations
When designing MCPCBs, several key factors need to be considered to ensure optimal thermal and electrical performance:
Thermal Management
- Thermal Vias: Thermal vias are used to transfer heat from the top layer to the metal core. They are placed strategically near high-power components to provide a low-resistance thermal path.
- Copper Thickness: Thicker copper traces and pads can enhance thermal conductivity and improve heat spreading. However, thicker copper also increases the overall board thickness and cost.
- Dielectric Thickness: The thickness of the dielectric layer affects the thermal resistance between the copper traces and the metal core. A thinner dielectric layer improves thermal performance but requires careful control during manufacturing.
Electrical Design
- Impedance Control: Proper impedance control is essential for high-speed and high-frequency signals. The dielectric constant of the MCPCB materials should be considered when designing controlled impedance traces.
- Signal Integrity: The metal core can act as a ground plane, providing a low-impedance return path for signals. However, the proximity of the metal core to the signal traces can also introduce capacitive coupling and affect signal integrity. Careful layout and spacing are necessary to minimize these effects.
Mechanical Considerations
- Board Thickness: MCPCBs are typically thicker than traditional PCBs due to the presence of the metal core. This should be considered when designing enclosures and mounting arrangements.
- Coefficient of Thermal Expansion (CTE): The CTE mismatch between the metal core, dielectric layer, and copper traces can lead to thermal stresses during temperature cycling. Proper material selection and layout techniques can help mitigate these stresses.
Applications of MCPCBs
MCPCBs find applications in various industries where thermal management and high power density are critical. Some common applications include:
LED Lighting
MCPCBs are extensively used in LED lighting applications, such as high-power LED fixtures, streetlights, and automotive lighting. The metal core efficiently dissipates the heat generated by the LEDs, ensuring stable light output and prolonging the lifespan of the LEDs.
Power Electronics
Power electronic devices, such as motor drives, power supplies, and inverters, generate significant heat during operation. MCPCBs provide a compact and efficient solution for thermal management in these applications, eliminating the need for bulky heat sinks.
Automotive Electronics
MCPCBs are used in various automotive electronic systems, including engine control units, power steering modules, and LED headlights. The enhanced thermal performance of MCPCBs ensures reliable operation in the harsh automotive environment.
Industrial Controls
Industrial control systems often involve high-power components and operate in demanding environments. MCPCBs provide a rugged and thermally efficient solution for these applications, ensuring reliable operation and extended system life.
Renewable Energy
MCPCBs are used in solar inverters, wind turbine controls, and other renewable energy applications. The efficient thermal management provided by MCPCBs helps to maintain optimal operating temperatures and improves system efficiency.
Frequently Asked Questions (FAQs)
-
What is the difference between MCPCBs and traditional PCBs?
MCPCBs have a metal substrate, typically aluminum or copper, as the base material, while traditional PCBs use FR-4 or other dielectric materials. The metal core in MCPCBs provides excellent thermal conductivity, allowing for efficient heat dissipation from high-power components. -
Can MCPCBs be used for all types of electronic circuits?
While MCPCBs offer superior thermal management, they may not be suitable for all types of electronic circuits. MCPCBs are primarily used in applications that generate significant heat or require high power density, such as LED lighting, power electronics, and automotive systems. -
How does the dielectric layer in MCPCBs provide electrical insulation?
The dielectric layer in MCPCBs is a thin layer of insulating material, such as polyimide or epoxy, that is applied between the metal core and the copper traces. This layer prevents electrical short-circuits and provides the necessary insulation between the conductive layers. -
Are MCPCBs more expensive than traditional PCBs?
Yes, MCPCBs are generally more expensive than traditional PCBs due to the additional materials and manufacturing steps involved. However, the cost difference is often justified by the enhanced thermal performance and the elimination of separate heat sinks or cooling solutions. -
Can MCPCBs be manufactured with multiple copper layers?
Yes, MCPCBs can be manufactured with multiple copper layers, just like traditional PCBs. The number of layers depends on the specific design requirements and the capabilities of the MCPCB manufacturer. Multi-layer MCPCBs offer increased flexibility in circuit design and signal routing.
Conclusion
Metal Core PCBs (MCPCBs) offer a compelling solution for applications that demand efficient thermal management and high power density. By incorporating a metal substrate as the base material, MCPCBs provide excellent thermal conductivity, allowing for effective heat dissipation from high-power components. The enhanced thermal performance of MCPCBs enables the design of compact, reliable, and high-performance electronic systems.
The manufacturing process of MCPCBs involves several key steps, including metal core preparation, dielectric layer application, copper foil lamination, circuit patterning, and surface finishing. The choice of materials, such as the metal core, dielectric layer, and copper foil, plays a crucial role in achieving the desired thermal and electrical properties.
When designing MCPCBs, careful consideration must be given to thermal management, electrical design, and mechanical aspects. Techniques such as the use of thermal vias, appropriate copper thickness, and proper impedance control contribute to optimal performance.
MCPCBs find widespread applications in industries such as LED lighting, power electronics, automotive electronics, industrial controls, and renewable energy. The superior thermal management capabilities of MCPCBs make them an ideal choice for applications that generate significant heat or require high power density.
As electronic systems continue to push the boundaries of performance and power density, MCPCBs will play an increasingly important role in enabling efficient thermal management and reliable operation. With ongoing advancements in materials and manufacturing technologies, MCPCBs are poised to meet the evolving needs of the electronics industry.
Leave a Reply