Introduction to Metal-Core PCBs
Metal-Core Printed Circuit Boards (MCPCBs), also known as thermal management boards or insulated metal substrates, are a specialized type of PCB that utilizes a metal core as the base material instead of the traditional FR-4 substrate. The metal core, typically made of aluminum, provides superior thermal conductivity compared to standard PCBs, making them ideal for applications that generate significant heat.
Key Features of Metal-Core PCBs
- Metal core (usually aluminum) as the base material
- Dielectric layer for electrical insulation
- Copper circuit layer for electrical connections
- Enhanced thermal conductivity and heat dissipation
Advantages of Metal-Core PCBs
1. Superior Thermal Management
One of the primary advantages of Metal-Core PCBs is their excellent thermal management capabilities. The metal core, usually made of aluminum, offers significantly higher thermal conductivity than traditional FR-4 substrates. This allows for efficient heat dissipation from the electronic components mounted on the PCB, preventing overheating and ensuring optimal performance.
Thermal Conductivity Comparison
Material | Thermal Conductivity (W/mK) |
---|---|
Aluminum | 205 – 250 |
Copper | 385 – 400 |
FR-4 | 0.3 – 0.4 |
As evident from the table above, aluminum and copper, the materials commonly used in Metal-Core PCBs, have significantly higher thermal conductivity compared to FR-4, the standard material for traditional PCBs.
2. Improved Reliability and Longevity
The efficient heat dissipation provided by Metal-Core PCBs contributes to improved reliability and longevity of the electronic components. By preventing overheating, MCPCBs reduce the risk of component failure and extend the overall lifespan of the electronic device. This is particularly important in applications where reliability is critical, such as automotive electronics, power electronics, and LED lighting systems.
3. Reduced Size and Weight
Metal-Core PCBs allow for the design of more compact and lightweight electronic devices. The metal core provides a rigid and stable base, eliminating the need for additional heat sinks or cooling solutions. This enables designers to create smaller form factors and reduces the overall weight of the device, which is especially beneficial in space-constrained applications or where weight reduction is crucial, such as in aerospace and portable electronics.
4. Enhanced Electrical Performance
In addition to thermal management, Metal-Core PCBs offer enhanced electrical performance. The metal core acts as a ground plane, providing a low-impedance path for electrical currents. This reduces electromagnetic interference (EMI) and improves signal integrity, resulting in better overall electrical performance of the device.
5. Cost-Effective Solution
While the initial cost of Metal-Core PCBs may be higher compared to traditional PCBs, they offer a cost-effective solution in the long run. The improved thermal management and reliability of MCPCBs reduce the need for additional cooling components and minimize the risk of device failure, leading to lower maintenance and replacement costs over the product’s lifecycle.
Applications of Metal-Core PCBs
Metal-Core PCBs find applications in various industries where thermal management and reliability are critical. Some common applications include:
- Power Electronics
- Switching power supplies
- Motor drives
-
Inverters
-
Automotive Electronics
- Engine control units (ECUs)
- Lighting systems
-
Battery management systems
-
LED Lighting
- High-power LED arrays
- LED driver circuits
-
Solid-state lighting fixtures
-
Aerospace and Defense
- Radar systems
- Avionics
-
Satellite communication devices
-
Industrial Automation
- Motor Controllers
- Sensors and actuators
- Programmable logic controllers (PLCs)
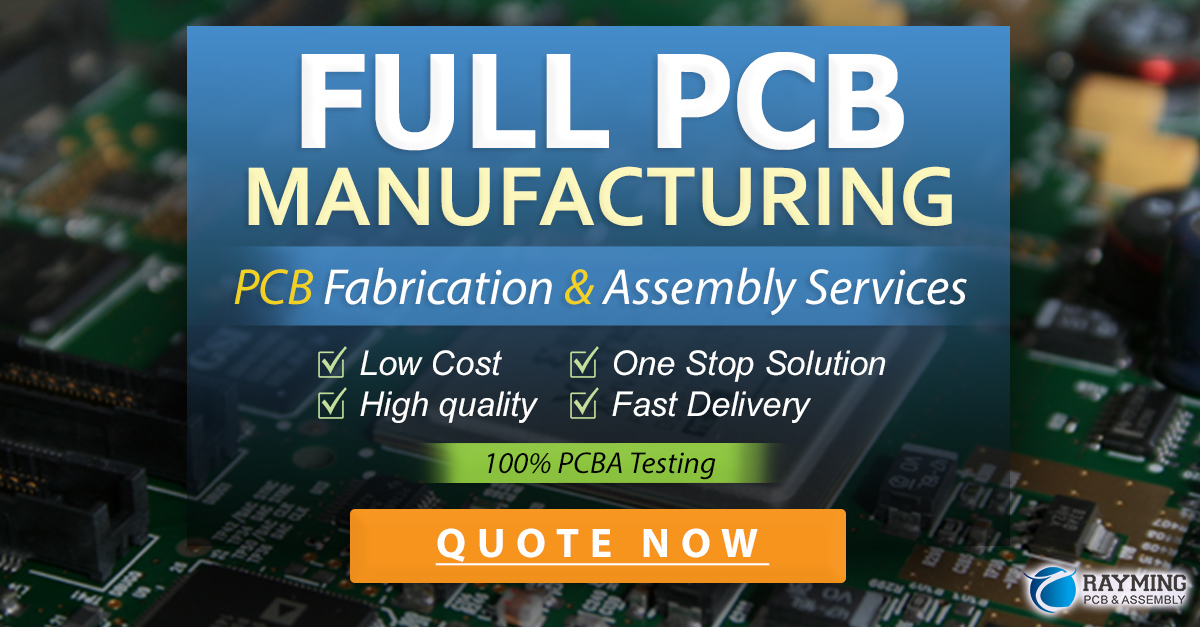
Design Considerations for Metal-Core PCBs
When designing Metal-Core PCBs, several key factors must be considered to ensure optimal performance and reliability:
1. Dielectric Layer Selection
The dielectric layer in Metal-Core PCBs serves as an electrical insulator between the metal core and the copper circuit layer. The choice of dielectric material is crucial as it affects the thermal conductivity, electrical insulation, and mechanical properties of the PCB. Common dielectric materials include:
- Epoxy-based dielectrics
- Polyimide-based dielectrics
- Ceramic-filled dielectrics
The selection of the dielectric material depends on the specific application requirements, such as operating temperature range, dielectric strength, and thermal conductivity.
2. Thermal Management Design
Effective thermal management is the primary goal of Metal-Core PCBs. To optimize heat dissipation, designers must consider factors such as:
- Thermal vias: Placing thermal vias strategically to enhance heat transfer from the components to the metal core.
- Copper thickness: Increasing the copper thickness of the circuit layer can improve thermal conductivity and heat spreading.
- Component placement: Arranging components in a way that maximizes heat dissipation and minimizes hotspots.
Thermal simulation tools can be used to analyze the thermal performance of the PCB design and make necessary optimizations.
3. Manufacturing Process
The manufacturing process for Metal-Core PCBs differs from that of traditional PCBs. The key steps involved in MCPCB manufacturing include:
- Metal core preparation: Cleaning and surface treatment of the metal core.
- Dielectric layer application: Laminating or screen printing the dielectric layer onto the metal core.
- Copper foil lamination: Bonding the copper foil to the dielectric layer.
- Circuit patterning: Etching the copper foil to create the desired circuit pattern.
- Finishing: Applying surface finishes, solder mask, and silkscreen as required.
It is essential to work with a PCB manufacturer experienced in Metal-Core PCB fabrication to ensure high-quality and reliable boards.
Frequently Asked Questions (FAQ)
1. What is the typical thickness of a Metal-Core PCB?
The thickness of a Metal-Core PCB can vary depending on the application and design requirements. Common thicknesses range from 0.5mm to 3.0mm, with 1.6mm being a typical value. The metal core itself is usually between 0.5mm and 2.0mm thick, while the dielectric layer and copper circuit layer add to the overall thickness.
2. Can Metal-Core PCBs be used in high-voltage applications?
Yes, Metal-Core PCBs can be used in high-voltage applications, provided that the appropriate dielectric material and thickness are selected. The dielectric layer must have sufficient dielectric strength to withstand the high voltages present in the application. Polyimide-based dielectrics and ceramic-filled dielectrics are commonly used in high-voltage Metal-Core PCBs due to their excellent electrical insulation properties.
3. How does the cost of Metal-Core PCBs compare to traditional PCBs?
Metal-Core PCBs are generally more expensive than traditional PCBs due to the additional materials and manufacturing processes involved. The cost of the metal core, dielectric layer, and specialized fabrication steps contribute to the higher initial cost. However, the improved thermal management and reliability offered by Metal-Core PCBs can lead to cost savings in the long run through reduced cooling requirements and lower maintenance and replacement costs.
4. Are Metal-Core PCBs suitable for high-frequency applications?
Metal-Core PCBs can be used in high-frequency applications, but special considerations must be taken during the design process. The metal core can affect the impedance and signal integrity of high-frequency circuits. To mitigate these effects, designers can use techniques such as controlled impedance routing, ground planes, and shielding. It is essential to work with experienced PCB designers and manufacturers to ensure the Metal-Core PCB is optimized for high-frequency performance.
5. Can Metal-Core PCBs be used in flexible electronics applications?
While Metal-Core PCBs are traditionally rigid, recent advancements in materials and manufacturing processes have enabled the development of flexible Metal-Core PCBs. These flexible MCPCBs use thin, flexible dielectric materials and thin metal cores to achieve a certain degree of flexibility. However, the flexibility is limited compared to traditional flexible PCBs, and the application scope is narrower. Flexible Metal-Core PCBs are mainly used in applications where moderate flexibility and enhanced thermal management are required simultaneously.
Conclusion
Metal-Core PCBs offer significant advantages over traditional PCBs in terms of thermal management, reliability, size reduction, and electrical performance. By utilizing a metal core as the base material, MCPCBs provide efficient heat dissipation, improved component lifespan, and compact design possibilities. These benefits make Metal-Core PCBs an attractive solution for a wide range of applications, including power electronics, automotive electronics, LED lighting, aerospace, and industrial automation.
When designing Metal-Core PCBs, careful consideration must be given to dielectric layer selection, thermal management design, and manufacturing processes. Working with experienced PCB designers and manufacturers is crucial to ensure the optimal performance and reliability of the final product.
As technology advances and the demand for efficient thermal management and high-performance electronics continues to grow, Metal-Core PCBs are poised to play an increasingly important role in shaping the future of electronic devices. By understanding the advantages and design considerations of MCPCBs, engineers and designers can harness their potential to create innovative, reliable, and thermally optimized electronic solutions.
Leave a Reply