1. Types of Motor Controllers
There are several types of motor controllers, each designed to cater to specific motor types and application requirements. Some of the most common types include:
1.1 DC Motor Controllers
DC motor controllers are used to control the speed and direction of DC motors. They work by varying the voltage or current supplied to the motor, which in turn affects its speed and torque. DC motor controllers can be further classified into:
- PWM (Pulse Width Modulation) controllers
- Linear controllers
- Brushless DC motor controllers
1.2 AC Motor Controllers
AC motor controllers are designed to control the speed and torque of AC motors, such as induction motors and synchronous motors. They work by adjusting the frequency and voltage of the AC power supplied to the motor. Some common types of AC motor controllers include:
- Variable Frequency Drives (VFDs)
- Soft starters
- AC servo controllers
1.3 Stepper Motor Controllers
Stepper motor controllers are used to control the precise position and speed of stepper motors. They work by sending a sequence of pulses to the motor, which causes it to rotate in discrete steps. Stepper motor controllers are commonly used in applications that require precise positioning, such as 3D printers and CNC machines.
Motor Controller Type | Motor Type | Key Features |
---|---|---|
DC Motor Controllers | DC Motors | Speed and direction control, PWM, linear, or brushless |
AC Motor Controllers | AC Motors (Induction, Synchronous) | Speed and torque control, VFDs, soft starters, servo controllers |
Stepper Motor Controllers | Stepper Motors | Precise position and speed control, pulse sequence control |
2. Motor Controller Architectures
Motor controllers can be designed using various architectures, each with its own advantages and limitations. The two main architectures are:
2.1 Open-Loop Architecture
In an open-loop architecture, the motor controller does not receive any feedback from the motor regarding its actual speed, position, or torque. Instead, it relies on predefined control parameters to regulate the motor’s operation. Open-loop controllers are simpler and less expensive than closed-loop controllers, but they are less accurate and may suffer from performance variations due to load changes or environmental factors.
2.2 Closed-Loop Architecture
In a closed-loop architecture, the motor controller receives feedback from the motor via sensors, such as encoders or resolvers. This feedback is used to continuously adjust the control parameters to ensure that the motor maintains the desired speed, position, or torque. Closed-loop controllers offer higher accuracy and better performance than open-loop controllers, but they are more complex and expensive.
Architecture | Feedback | Advantages | Disadvantages |
---|---|---|---|
Open-Loop | No | Simpler, less expensive | Less accurate, sensitive to load and environmental changes |
Closed-Loop | Yes (sensors) | Higher accuracy, better performance | More complex, expensive |
3. Motor Control Techniques
There are several motor control techniques used in motor controllers to achieve the desired performance and efficiency. Some of the most common techniques include:
3.1 Scalar Control
Scalar control, also known as V/f control, is a simple and widely used technique for controlling AC induction motors. It works by maintaining a constant ratio between the voltage and frequency supplied to the motor, which in turn maintains a constant magnetic flux in the motor. Scalar control is easy to implement and provides good speed regulation, but it may not offer optimal torque control, especially at low speeds.
3.2 Vector Control
Vector control, also known as field-oriented control (FOC), is a more advanced technique for controlling AC motors. It works by decomposing the motor current into two orthogonal components: the flux-producing current and the torque-producing current. By controlling these components independently, vector control can achieve high-performance speed and torque regulation, even at low speeds. However, vector control is more complex to implement and requires accurate knowledge of the motor parameters.
3.3 Direct Torque Control (DTC)
Direct torque control is another advanced technique for controlling AC motors, particularly induction motors. It works by directly controlling the motor’s torque and stator flux, using a lookup table to select the appropriate voltage vectors. DTC offers fast torque response and good efficiency, but it may produce higher torque ripple compared to vector control.
Control Technique | Motor Type | Key Features |
---|---|---|
Scalar Control (V/f) | AC Induction Motors | Simple, good speed regulation, less optimal at low speeds |
Vector Control (FOC) | AC Motors | High-performance speed and torque regulation, complex implementation |
Direct Torque Control (DTC) | AC Induction Motors | Fast torque response, good efficiency, higher torque ripple |
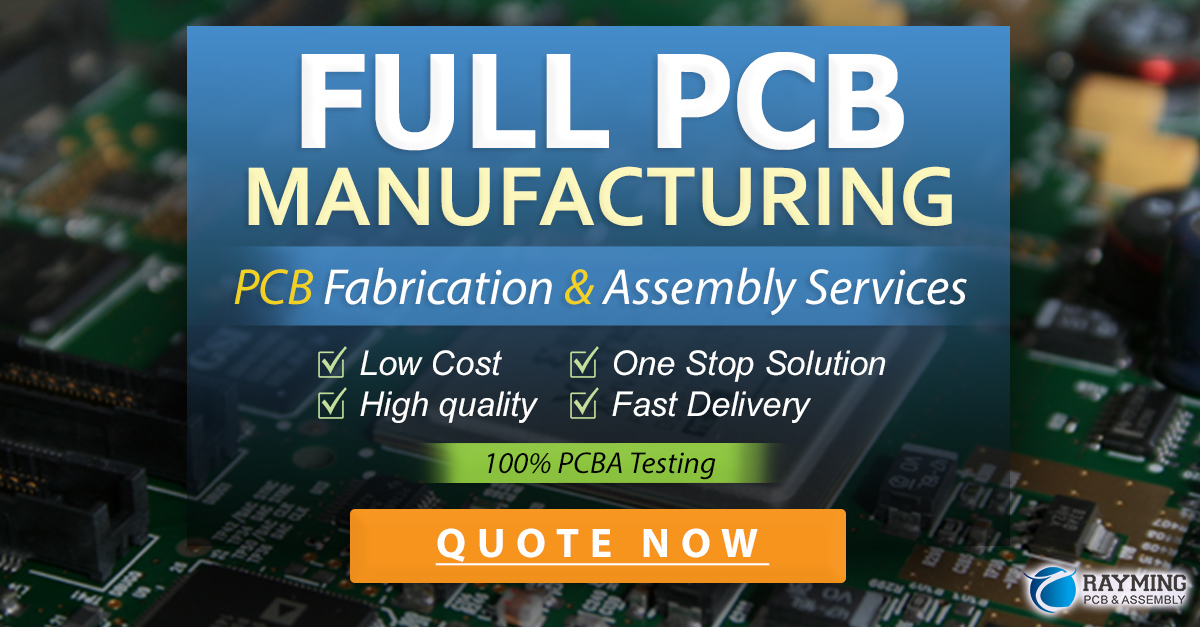
4. Motor Controller Applications
Motor controllers find applications in a wide range of industries and systems, including:
4.1 Industrial Automation
In industrial automation, motor controllers are used to control the motors that drive conveyor belts, robotic arms, packaging machines, and other equipment. They enable precise control of speed, position, and torque, ensuring efficient and reliable operation of the automated systems.
4.2 Electric Vehicles
Motor controllers are a critical component in electric vehicles (EVs) and hybrid electric vehicles (HEVs). They control the electric motors that propel the vehicle, managing the power flow between the battery, motor, and regenerative braking system. Advanced motor controllers in EVs and HEVs help optimize energy efficiency, extend driving range, and improve overall performance.
4.3 HVAC Systems
In heating, ventilation, and air conditioning (HVAC) systems, motor controllers are used to control the motors that drive fans, compressors, and pumps. They enable efficient and precise control of airflow, temperature, and humidity, ensuring optimal comfort and energy efficiency in buildings.
Application | Motor Controller Role |
---|---|
Industrial Automation | Control motors for conveyor belts, robotic arms, packaging machines, etc. |
Electric Vehicles | Control electric motors for propulsion, manage power flow and energy efficiency |
HVAC Systems | Control motors for fans, compressors, and pumps, optimize comfort and energy efficiency |
5. Motor Controller Selection Considerations
When selecting a motor controller for a specific application, several factors should be considered, including:
5.1 Motor Type and Ratings
The motor controller must be compatible with the type of motor being used (DC, AC, or stepper) and must be rated to handle the motor’s power, voltage, and current requirements. Selecting a controller with insufficient ratings can lead to poor performance or damage to the controller and motor.
5.2 Control Requirements
The control requirements of the application, such as speed range, torque accuracy, and dynamic response, should be carefully evaluated when selecting a motor controller. Different control techniques (scalar, vector, or DTC) may be better suited for specific applications based on their performance characteristics.
5.3 Environment and Safety
The operating environment and safety requirements should also be considered when selecting a motor controller. Factors such as temperature range, humidity, vibration, and electromagnetic interference (EMI) can affect the controller’s performance and reliability. Safety features, such as over-current protection, over-temperature protection, and safe torque off (STO), may be required in certain applications to ensure operator safety and prevent equipment damage.
6. Future Trends in Motor Controllers
As technology advances, motor controllers are expected to evolve to meet the changing demands of various applications. Some of the future trends in motor controllers include:
6.1 Intelligent and Connected Controllers
The integration of advanced sensors, communication interfaces, and data analytics capabilities will enable the development of intelligent and connected motor controllers. These controllers will be able to monitor the motor’s health, detect potential faults, and optimize performance based on real-time data, leading to predictive maintenance and improved overall system efficiency.
6.2 Miniaturization and Integration
With the increasing demand for compact and efficient systems, motor controllers are expected to become smaller and more integrated. Advances in power electronics and packaging technologies will enable the development of highly integrated motor controller modules, combining control, power, and communication functions in a single compact unit.
6.3 Advanced Control Algorithms
Research in motor control theory and algorithms will continue to drive the development of more advanced and efficient motor controllers. Techniques such as model predictive control (MPC), adaptive control, and artificial intelligence-based control may be increasingly adopted to improve the performance and adaptability of motor controllers in complex and dynamic applications.
Frequently Asked Questions (FAQ)
- Q: What is the difference between open-loop and closed-loop motor controllers?
A: Open-loop motor controllers do not receive feedback from the motor and rely on predefined control parameters, while closed-loop controllers use sensors to obtain feedback from the motor and continuously adjust the control parameters for better accuracy and performance.
- Q: Can a DC motor controller be used with an AC motor?
A: No, DC motor controllers are designed specifically for DC motors and cannot be used with AC motors. AC motors require dedicated AC motor controllers, such as variable frequency drives or soft starters.
- Q: What is the advantage of vector control over scalar control in AC motor applications?
A: Vector control offers high-performance speed and torque regulation, even at low speeds, by independently controlling the flux-producing and torque-producing components of the motor current. Scalar control, while simpler to implement, may not provide optimal torque control at low speeds.
- Q: How do motor controllers contribute to energy efficiency in electric vehicles?
A: Advanced motor controllers in electric vehicles optimize energy efficiency by precisely controlling the power flow between the battery, motor, and regenerative braking system. They can also implement efficient control strategies, such as maximum torque per ampere (MTPA) or maximum efficiency, to minimize losses and extend the driving range.
- Q: What safety features should be considered when selecting a motor controller for industrial applications?
A: Safety features such as over-current protection, over-temperature protection, and safe torque off (STO) are important considerations when selecting a motor controller for industrial applications. These features help prevent equipment damage and ensure operator safety in case of faults or emergency situations.
In conclusion, understanding motor controller theory and applications is essential for designing and implementing efficient and reliable motor-driven systems. By considering factors such as motor type, control requirements, and operating environment, engineers can select the most suitable motor controller for their specific application. As technology continues to advance, motor controllers are expected to become more intelligent, integrated, and efficient, enabling new possibilities in various industries.
Leave a Reply