Introduction
Flexible printed circuit boards (flex PCBs) have become an increasingly popular solution for designers looking to create compact and customizable electronic devices. With their ability to bend and flex, flex PCBs open up new possibilities for innovative product designs and space-saving electronics.
However, as demand for flex PCBs continues to grow, many product developers find themselves wondering – how much does a flex PCB cost? While pricing depends on numerous factors, having a general understanding of flex PCB costs can help you budget for your next project.
In this in-depth guide, we’ll break down the key considerations that impact flex PCB pricing. Whether you’re new to flex circuits or simply want to understand the latest pricing trends, read on to learn what determines flex PCB cost per square inch and overall in 2023.
What Are The Main Factors That Determine Flex PCB Price?
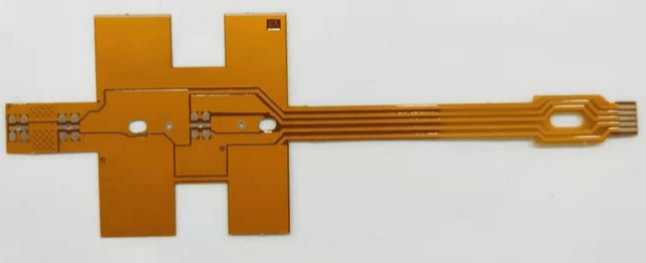
The cost of a flex PCB is influenced by a variety of factors that relate to both the board’s design and manufacturing requirements. Here are some of the key elements that determine the overall price of a flex PCB:
Board Size and Complexity
One of the most basic factors is the physical size and layer count of the board itself. A larger and more layered board will require more raw materials and processing, increasing the cost. Simple single or double-sided flex circuits tend to cost less than complex multilayer boards.
Board Quantity and Production Scale
As with most manufacturing processes, volume and scale impacts per unit pricing. Small prototype orders of just a few boards will be comparatively more expensive than higher volume production runs in the thousands of units.
Materials Used
The base material of the flex board (polyimide, polyester, etc) as well as the type of conductive copper traces impact material costs. More durable or high-frequency materials drive prices upward. The thickness of layers also factors in.
Specialized Coatings and Finishes
Add-on coatings like solder masking, coverlay, or stiffeners add to production processes and expenses. Special finishes like gold plating terminals or edges also increase costs when required.
Component Assembly and Testing
Whether basic SMT component placement or complex chip-on-board assemblies, component assembly and soldering increases labor and quality control costs. Testing and inspection requirements also get factored into the final board pricing.
Lead Times and Rush Orders
Fast turnaround schedules and quick-turn orders will also understandably cost more than standard, longer lead time productions. Last-minute prototype builds often incur rush fees.
How is Flex PCB Pricing Typically Quoted?
Now that we’ve covered the key elements that make up a flex board’s cost, how do PCB manufacturers actually quote and charge for flex circuit orders? Here are two of the most common pricing models:
Price Per Square Inch
The most straightforward method is cost per square inch of board area. In this model, the total board area in square inches is multiplied by a $/in2 rate based on the flex board specs. This accounts for base material costs, processing complexity, and volume.
Example:
- 2″ x 3″ double-sided flex PCB with no special coatings
- 6 square inches total area
- $5/in2 quote for low volume prototype
- Total Price = 6 in2 x $5/in2 = $30
While simple boards can be quoted by area this way, it does not adequately account for assembly costs and other order-specific factors. So a second method is commonly used:
Price Based on Design and Order Requirements
For more complex flex PCB projects, the overall price is custom quoted based on the specific design, components, and order requirements including:
- Board dimensions, layers, and materials
- Special coatings and finishes required
- Component placements, soldering, and assemblies
- Testing specifications and quality checks
- Order volume and schedule
This allows manufacturers more precision in quoting for intricate or high-mix boards by factoring in all cost elements like engineering time, sourcing, production, assembly, inspection, etc. However, the final price is less predictable until you receive the custom quote
How Much Does a 2 Layer Flex PCB Cost on Average?
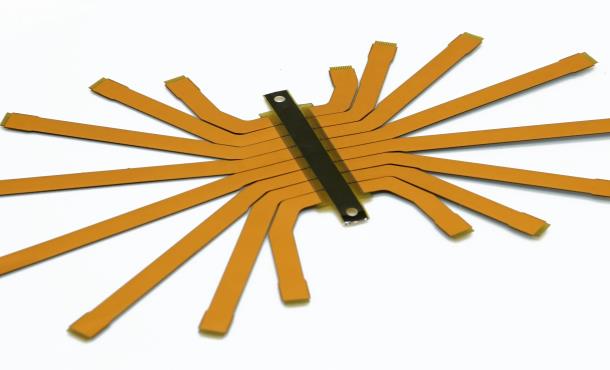
To give an idea of typical base pricing in today’s market, here are approximate costs for a common 2-layer flex board configuration:
Board Size | Prototype Price | Low Volume Price | Mid Volume Price | High Volume Price |
---|---|---|---|---|
1 in2 | $10 | $4 | $2 | $1 |
10 in2 | $30 | $12 | $8 | $5 |
50 in2 | $120 | $50 | $30 | $20 |
100 in2 | $200 | $80 | $60 | $40 |
As you can see, increasing volume drives down the per unit pricing significantly. This table simply reflects baseline 2-layer board fabrication – any assemblies, coatings, or specialty materials will increase costs further.
We’ll now take a look at how pricing progresses for boards with additional layers:
Flex PCB Cost Per Layer
Here’s an overview of how base price per square inch typically increases with each additional conductive layer:
Layer Count | Prototype | Low Volume | Mid Volume | High Volume |
---|---|---|---|---|
2 Layers | $10/in2 | $3/in2 | $2/in2 | $1/in2 |
4 Layers | $15/in2 | $6/in2 | $4/in2 | $2/in2 |
6 Layers | $25/in2 | $10/in2 | $5/in2 | $3/in2 |
8 Layers | $40/in2 | $15/in2 | $8/in2 | $5/in2 |
As you can see, costs per in2 climb rapidly as layer counts exceed 6. This is due to higher material demands, more complex processing, and increased likelihood of defects.
Beyond just the number of layers, actual layer composition can also affect pricing:
- Copper thickness – Thicker copper increases material costs
- Adhesive films – Specialty adhesive films are more expensive than standard acrylic bonding
Additional Flex PCB Cost Considerations
Beyond the base board itself, here are some additional flex PCB design factors that increase manufacturing costs:
Coatings and Coverlays: Solder mask, coverlay layers, aqueous coating, stiffeners, and shielding all add labor and material costs. Coverlay for multilayer flex can add around $3/in2.
Special Terminations: Gold plating exposed traces or connection points adds $0.50-1 per square inch. Other platings like tin-lead or nickel-gold also add cost.
Flex-Rigid Boards: Combining stiff and flexible substrates on one PCB adds complexity and expense for advanced processing.
Component Assembly: SMT component placement, soldering, inspection, cleaning adds $0.25-2.00/in2 depending on complexity. Chip-on-board or chip-on-flex assemblies add even more.
Design Support: Complex designs requiring engineering collaboration or design for manufacturing support can incur added NRE (non-recurring engineering) fees.
Testing and Certification: Extensive electrical testing, fixture development, and process certifications (like IPC or ISO) will increase cost as well.
Quick-Turn Schedule: Reduced lead times for rapid prototyping or ramp-up demand rush and expedite fees.
Economies of Scale in Flex PCB Manufacturing
An important trend to note is how flexible PCB per unit pricing drops dramatically as order volumes increase into mass production. Here’s an example price progression for a sample 2-layer board from prototype through high volume:
Stage | Volume | Price |
---|---|---|
Prototype | 10 boards | $50 each |
Pre-Production | 100 boards | $20 each |
Early Production | 1,000 boards | $10 each |
Full Production | 10,000+ boards | $5 each |
As you can see, scaling production volume from 10 to 10,000 units reduces per board cost by 90%! This economy of scale allows manufacturers to spread fixed costs over more boards.
In summary, project developers should budget higher costs for low volume pilot runs, but can realize substantial savings when scaling up orders into mass production volumes.
How to Get The Best Flex PCB Prices?
Below are some tips designers can follow to get the most cost-effective flex PCB manufacturing quote:
- Optimize board size – Minimize dimensions and consolidate space to reduce square inches.
- Design for easier processing – Allow adequate spacing, avoid irregular shapes, minimize layer counts.
- Select cost-effective materials – Standard polyimide and adhesive films instead of exotic films. Standard 1/1oz copper instead of 2/2oz copper.
- Only specify essential coatings/finishes – Don’t over-specify solder mask or plating unless required.
- Consolidate orders – Manufacture boards for multiple projects simultaneously to maximize panel utilization.
- Request competitive quotes – Get pricing from multiple manufacturers, but share the same detailed design files for apples-to-apples comparison.
- Leverage supplier relationships – Develop trusted partnerships with suppliers to receive pricing incentives and preferred customer support.
- Plan realistically – Discuss manufacturing schedules openly to avoid last minute change orders and rush charges.
Flex PCB Cost per Square Inch – 2023 Price Examples
To give a snapshot of current market pricing, here are some real-world flex PCB price samples from domestic and overseas manufacturers:
2-layer US Prototype:
- Flex board with FR-4 stiffener, no coatings or special finishes
- $10/in2 quote for low-mix prototype order
4-layer China Production:
- Medium complexity flex-rigid PCB for medical device
- Solder mask, silkscreen, gold fingers
- $6/in2 quote for 1,000 boards
6-layer India Prototype:
- Multilayer flex with rigid section for foldable display
- Special polyimide film, coverlay, stiffener
- $28/in2 quoted for 20 boards
8-layer Mexico Mid-Volume:
- High complexity rigid-flex board for aerospace system
- Tight impedance control requirements
- $18/in2 quote for 500 boards
10-layer Japan Prototype
- Advanced flex PCB with chip-on-board assembly
- Low loss dielectric material required
- $90/in2 quote for 5 board prototype
As you can see, prices vary widely depending on application demands. When requesting quotes, be sure to share all mechanical and electrical requirements to get accurate pricing.
Flex PCB Cost Calculator
Rather than static price tables, many flex PCB suppliers provide online cost calculators to estimate pricing based on your specific design parameters.
By inputting details like:
- Board dimensions
- Layer count
- Material types
- Production volume
- Lead time
You can get an interactive instant quote tailored to your unique specifications and order requirements.
Cost calculators are a useful way to perform quick what-if analyses to optimize your design and budget or compare process options. Just be sure to validate any preliminary quotes with the PCB manufacturer before finalizing orders.
Conclusion
Determining the exact cost for a flex PCB depends on a variety of factors spanning from the board geometry and materials to production scale and assembly complexity.
While flex circuits were once a niche solution, advancing manufacturing techniques have made flexible boards a very cost-competitive option – especially for higher volume productions.
By understanding the key pricing factors and design considerations outlined in this guide, you’ll be equipped to better estimate and control costs for your next flex PCB project.
Flex PCB Cost FAQs
Here are answers to some frequently asked questions about flex PCB pricing:
What are the main factors affecting flex PCB cost?
The primary drivers of flex PCB pricing are: board size/complexity, order volume, base material type, layer count, special coatings/finishes, component assembly, and production schedule.
Does flex PCB cost increase with more bend cycles?
Yes, designing a flex board for more bend cycles requires more durable materials and processing, which increases cost. Light duty flex are lowest cost, while dynamic flex are highest.
Is flex PCB cheaper than rigid PCB?
Generally no – flex PCBs require specialized materials and processes, so they are typically more expensive than equivalent rigid boards for low-moderate volumes. In mass volumes, they can approach rigid PCB cost levels.
Can flex PCB be manufactured at home?
Home PCB fabrication is very limited and produces low reliability boards. Flex PCBs in particular require advanced materials, metal sputtering vacuums, and lamination presses well beyond DIY capabilities. Professional manufacturing is recommended.
How much does flex PCB prototyping cost?
Prototyping costs typically range from $10-50/in2 for 2-6 layer boards, and $50-100+/in2 for complex multi-layer flex. Exact pricing depends on size, layer count, and other specifications.
Leave a Reply