What is Solder Mask and Why is it Important?
Solder mask, also known as solder resist or solder stop mask, is a thin layer of polymer applied to the copper traces of a printed circuit board (PCB). Its primary purpose is to protect the copper traces from oxidation, prevent Solder Bridges from forming between closely spaced pads, and provide electrical insulation. Solder mask also helps to improve the aesthetics of the PCB by providing a uniform color, typically green, but other colors like blue, red, yellow, black, and white are also available.
The application of solder mask is a crucial step in the PCB manufacturing process, as it ensures the reliability and longevity of the final product. Without solder mask, the exposed copper traces would be vulnerable to damage from handling and environmental factors, leading to reduced performance or complete failure of the electronic device.
Benefits of Solder Mask:
- Protection against oxidation and corrosion
- Electrical insulation between conductive traces
- Prevention of solder bridges during assembly
- Improved aesthetics and readability of the PCB
- Enhanced durability and reliability of the final product
Solder Mask Application Methods
There are several methods for applying solder mask to a PCB, each with its advantages and disadvantages. The choice of method depends on factors such as the desired finish quality, production volume, and cost. The most common solder mask application methods are:
1. Silk Screen Printing
Silk screen printing is a traditional method for applying solder mask to PCBs. It involves using a fine mesh screen with a stencil of the desired solder mask pattern. The solder mask ink is then forced through the screen onto the PCB surface using a squeegee. This method is suitable for low to medium volume production and can achieve a relatively thick solder mask layer (typically 0.001″ to 0.003″).
Advantages:
- Low setup costs
- Suitable for small to medium production volumes
- Thicker solder mask layer provides better insulation and protection
Disadvantages:
- Lower resolution compared to other methods
- Slower production speed
- Difficulty in achieving consistent thickness across the PCB
2. Liquid Photo Imageable (LPI) Solder Mask
LPI solder mask is a photosensitive polymer that is applied to the PCB surface as a liquid. The liquid solder mask is then exposed to UV light through a photomask, which hardens the exposed areas. The unexposed areas are then removed using a developer solution, leaving behind the desired solder mask pattern. LPI solder mask offers higher resolution and finer features compared to silk screen printing.
Advantages:
- High resolution and fine feature definition
- Consistent thickness across the PCB
- Faster production speed compared to silk screen printing
- Suitable for high-volume production
Disadvantages:
- Higher setup costs due to the need for a photomask
- Requires specialized equipment for exposure and development
- Thinner solder mask layer compared to silk screen printing
3. Dry Film Solder Mask
Dry film solder mask is a solid photosensitive film that is laminated onto the PCB surface using heat and pressure. The film is then exposed to UV light through a photomask, which crosslinks the exposed areas. The unexposed areas are removed using a developer solution, similar to the LPI process. Dry film solder mask offers excellent resolution and fine feature definition.
Advantages:
- High resolution and fine feature definition
- Consistent thickness across the PCB
- Suitable for high-volume production
- Excellent adhesion to the PCB surface
Disadvantages:
- Higher material costs compared to liquid solder mask
- Requires specialized lamination equipment
- Limited flexibility in terms of solder mask color options
Solder Mask Application Process
Regardless of the chosen application method, the solder mask application process generally follows these steps:
- PCB Surface Preparation
- Clean the PCB surface to remove any contaminants or debris
- Ensure the copper traces are free from oxidation
-
Apply a surface treatment (e.g., plasma or chemical cleaning) to improve solder mask adhesion
-
Solder Mask Application
- Apply the solder mask material to the PCB surface using the chosen method (silk screen printing, LPI, or dry film)
-
Ensure uniform coverage and thickness across the PCB
-
Exposure (for LPI and dry film methods)
- Align the photomask with the PCB and expose the solder mask to UV light
-
The exposure time and intensity depend on the solder mask material and desired thickness
-
Development
- Remove the unexposed solder mask areas using a developer solution
-
Rinse the PCB with water to stop the development process
-
Curing
- Place the PCB in an oven to cure the solder mask
-
Curing temperature and time depend on the solder mask material and desired properties
-
Inspection and Quality Control
- Visually inspect the PCB for any defects or irregularities in the solder mask
- Perform electrical tests to ensure proper insulation and connectivity
- Conduct adhesion tests to verify the solder mask’s bond strength to the PCB surface
Step | Silk Screen Printing | Liquid Photo Imageable (LPI) | Dry Film |
---|---|---|---|
PCB Surface Preparation | Required | Required | Required |
Solder Mask Application | Ink forced through screen | Liquid applied to PCB surface | Film laminated onto PCB |
Exposure | Not applicable | UV light through photomask | UV light through photomask |
Development | Not applicable | Developer solution | Developer solution |
Curing | Required | Required | Required |
Inspection and Quality Control | Required | Required | Required |
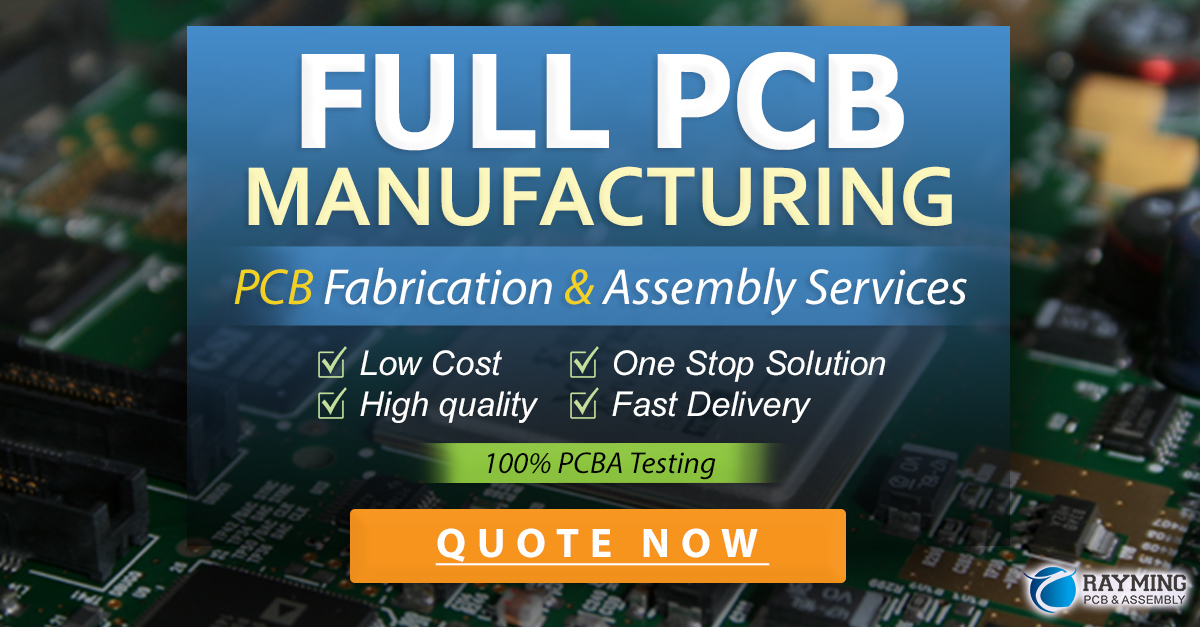
Solder Mask Design Considerations
When designing a PCB with solder mask, several factors should be considered to ensure optimal performance and manufacturability:
- Solder Mask Clearance
- Provide adequate clearance between the solder mask opening and the copper pad to allow for proper solder wetting
- Insufficient clearance can lead to poor solderability and weak solder joints
-
Excessive clearance can result in exposed copper and reduced insulation
-
Solder Mask Thickness
- Choose the appropriate solder mask thickness based on the application and manufacturing method
- Thicker solder mask provides better insulation and protection but may impact fine feature resolution
-
Thinner solder mask allows for higher resolution but may compromise insulation properties
-
Solder Mask Color
- Select a solder mask color that provides good contrast with the PCB Legend and components
- Green is the most common color, but other options are available for specific applications or aesthetics
-
Consider the impact of solder mask color on the PCB’s thermal properties and light reflection
-
Solder Mask Surface Finish
- Choose a surface finish that is compatible with the solder mask material and the assembly process
- Matte finish provides better adhesion for component labels and reduces light reflection
-
Glossy finish offers a smoother surface and improved aesthetics but may impact label adhesion
-
Solder Mask Alignment
- Ensure proper alignment between the solder mask and the copper traces to prevent any shorts or exposed copper
- Use fiducial marks to aid in the alignment process during solder mask application
Frequently Asked Questions (FAQ)
- What is the difference between solder mask and solder paste?
-
Solder mask is a protective polymer layer applied to the PCB surface to insulate and protect the copper traces. Solder paste, on the other hand, is a mixture of solder alloy and flux used to create electrical and mechanical connections between components and the PCB during the assembly process.
-
Can solder mask be removed from a PCB?
-
Yes, solder mask can be removed from a PCB using chemical or mechanical methods. However, removing the solder mask can expose the copper traces to oxidation and damage, compromising the PCB’s integrity and reliability. Solder mask removal should only be done when necessary, such as for rework or repair purposes.
-
What is the typical thickness of a solder mask layer?
-
The typical thickness of a solder mask layer varies depending on the application method and the desired properties. Silk screen printed solder mask can range from 0.001″ to 0.003″ (25 to 75 μm), while LPI and dry film solder mask layers are typically thinner, ranging from 0.0005″ to 0.002″ (12 to 50 μm).
-
Can solder mask be applied to Flexible PCBs?
-
Yes, solder mask can be applied to flexible PCBs, but the choice of solder mask material and application method should be carefully considered. Flexible solder mask materials, such as polyimide or acrylic-based formulations, are designed to withstand the bending and flexing of the PCB without cracking or delaminating.
-
How does solder mask affect the PCB’s electrical properties?
- Solder mask is an insulating material that helps to prevent short circuits and improve the PCB’s electrical performance. The solder mask’s dielectric constant and thickness can impact the PCB’s impedance, capacitance, and signal integrity. When designing high-frequency or high-speed circuits, it is essential to consider the solder mask’s electrical properties and their impact on the overall system performance.
In conclusion, solder mask application is a critical step in the PCB manufacturing process, providing protection, insulation, and improved aesthetics to the final product. By understanding the different application methods, design considerations, and frequently asked questions, PCB Designers and manufacturers can ensure the production of high-quality, reliable printed circuit boards.
Leave a Reply