Introduction to PCB Surface Finishes
Printed Circuit Boards (PCBs) are the backbone of modern electronics, connecting and supporting various components to create functional devices. One crucial aspect of PCB Manufacturing is the surface finish, which protects the exposed copper traces and pads from oxidation and enhances the board’s solderability. With several surface finish options available, each with its own advantages and disadvantages, it’s essential to understand their properties to make an informed decision for your specific application. In this comprehensive guide, we will explore the pros and cons of seven popular PCB surface finish types.
1. HASL (Hot Air Solder Leveling)
1.1 Overview
HASL is a widely used and cost-effective PCB surface finish that involves dipping the board in molten solder and then using hot air to remove excess solder, creating a flat surface.
1.2 Pros
- Inexpensive and widely available
- Excellent solderability
- Good shelf life
- Suitable for both through-hole and SMD components
1.3 Cons
- Uneven surface due to solder dipping process
- Not suitable for fine-pitch components
- High-temperature process may cause thermal shock to the PCB
- Contains lead (Pb), which is not RoHS compliant
2. ENIG (Electroless Nickel Immersion Gold)
2.1 Overview
ENIG is a popular lead-free surface finish that consists of an electroless nickel layer followed by a thin immersion gold layer, providing excellent solderability and durability.
2.2 Pros
- Flat and uniform surface
- Excellent solderability
- Suitable for fine-pitch components
- Good shelf life
- RoHS compliant
2.3 Cons
- More expensive than HASL
- Prone to “black pad” issue due to improper plating processes
- Gold layer may dissolve into the solder joint during reflow
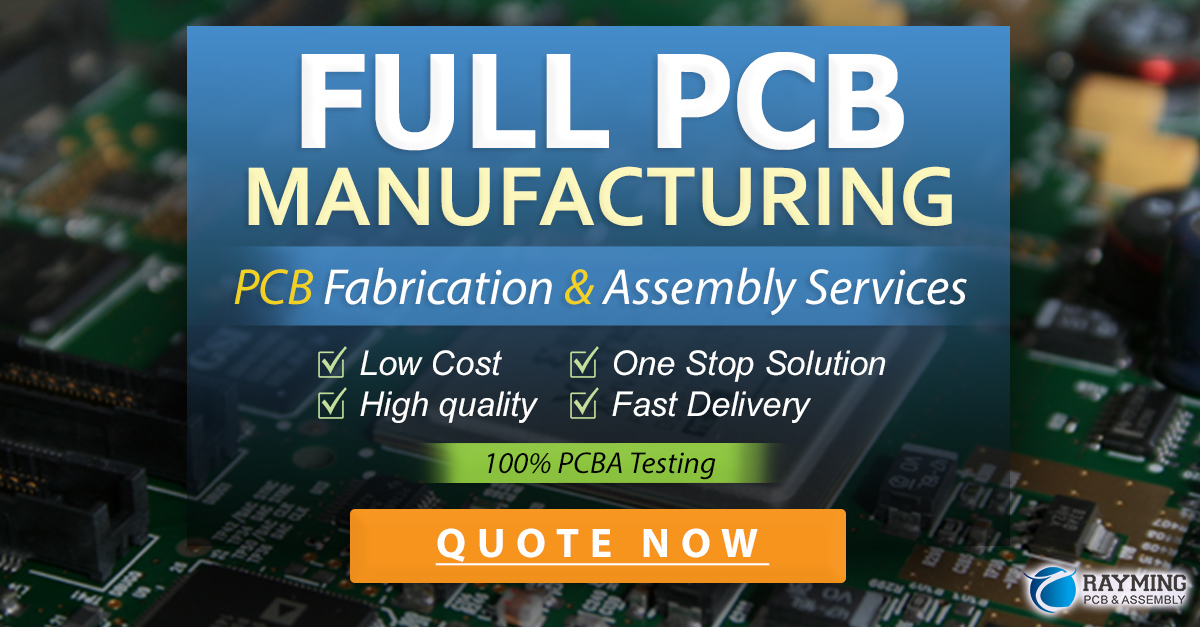
3. OSP (Organic Solderability Preservative)
3.1 Overview
OSP is a lead-free, organic coating that protects the copper surface from oxidation and provides good solderability.
3.2 Pros
- Cost-effective
- Flat and uniform surface
- Suitable for fine-pitch components
- RoHS compliant
- Easier to inspect compared to other finishes
3.3 Cons
- Limited shelf life (around 6-12 months)
- Sensitive to handling and moisture
- May require additional cleaning steps before soldering
4. Immersion Silver
4.1 Overview
Immersion silver is a lead-free surface finish that deposits a thin layer of silver onto the copper surface, providing good solderability and conductivity.
4.2 Pros
- Flat and uniform surface
- Excellent solderability
- Suitable for fine-pitch components
- Good electrical conductivity
- RoHS compliant
4.3 Cons
- More expensive than OSP
- Prone to tarnishing over time
- Limited shelf life compared to ENIG
5. Immersion Tin
5.1 Overview
Immersion tin is a lead-free surface finish that deposits a thin layer of tin onto the copper surface, offering good solderability and compatibility with lead-free solders.
5.2 Pros
- Flat and uniform surface
- Good solderability
- Suitable for fine-pitch components
- Compatible with lead-free solders
- RoHS compliant
5.3 Cons
- Prone to tin whiskers, which can cause short circuits
- Limited shelf life compared to ENIG
- May require additional handling precautions
6. ENEPIG (Electroless Nickel Electroless Palladium Immersion Gold)
6.1 Overview
ENEPIG is a high-performance surface finish that consists of an electroless nickel layer, an electroless palladium layer, and a thin immersion gold layer, providing excellent solderability, durability, and wire bonding capabilities.
6.2 Pros
- Flat and uniform surface
- Excellent solderability
- Suitable for fine-pitch components
- Good shelf life
- Compatible with wire bonding
- RoHS compliant
6.3 Cons
- Most expensive surface finish option
- Complex and time-consuming plating process
- Requires strict process control to avoid defects
7. DIG (Direct Immersion Gold)
7.1 Overview
DIG is a surface finish that deposits a thin layer of gold directly onto the copper surface, eliminating the need for a nickel layer.
7.2 Pros
- Flat and uniform surface
- Good solderability
- Suitable for fine-pitch components
- Faster plating process compared to ENIG
- RoHS compliant
7.3 Cons
- More expensive than ENIG
- Limited shelf life compared to ENIG
- Gold layer may dissolve into the solder joint during reflow
- Not suitable for wire bonding
Comparison Table
Surface Finish | Cost | Shelf Life | Solderability | Fine-Pitch Compatibility | RoHS Compliant |
---|---|---|---|---|---|
HASL | Low | Good | Excellent | Not Suitable | No |
ENIG | High | Excellent | Excellent | Suitable | Yes |
OSP | Low | Limited | Good | Suitable | Yes |
Immersion Silver | Moderate | Limited | Excellent | Suitable | Yes |
Immersion Tin | Moderate | Limited | Good | Suitable | Yes |
ENEPIG | Very High | Excellent | Excellent | Suitable | Yes |
DIG | High | Limited | Good | Suitable | Yes |
Frequently Asked Questions (FAQ)
1. Which surface finish is the most cost-effective?
HASL and OSP are the most cost-effective surface finishes, making them suitable for budget-constrained projects. However, they may not be the best choice for high-density designs or applications that require longer shelf life.
2. Which surface finish is the most durable?
ENIG and ENEPIG are the most durable surface finishes, offering excellent shelf life and protection against oxidation. They are ideal for applications that require long-term storage or exposure to harsh environments.
3. Which surface finish is best for fine-pitch components?
ENIG, ENEPIG, Immersion Silver, and DIG are all suitable for fine-pitch components due to their flat and uniform surfaces. OSP and Immersion Tin can also be used for fine-pitch components but may require additional care during handling and assembly.
4. Are all surface finishes RoHS compliant?
All surface finishes discussed in this guide, except for HASL, are RoHS compliant. HASL contains lead (Pb), which is restricted under the RoHS directive.
5. Which surface finish is best for wire bonding?
ENEPIG is the best surface finish for wire bonding applications, as it provides a suitable surface for both soldering and wire bonding. ENIG can also be used for wire bonding, but it may require additional process control to ensure optimal results.
Conclusion
Selecting the appropriate PCB surface finish depends on various factors, including cost, shelf life, solderability, component compatibility, and environmental regulations. By understanding the pros and cons of each surface finish type, you can make an informed decision that best suits your project’s requirements. Consider the information provided in this guide, consult with your PCB Manufacturer, and conduct thorough testing to ensure the chosen surface finish meets your performance and reliability goals.
Leave a Reply