What is Immersion Silver PCB Finish?
Immersion silver (IAg) is a popular surface finish for printed circuit boards (PCBs) that provides excellent solderability, conductivity, and shelf life. It is a lead-free, RoHS-compliant finish that deposits a thin layer of pure silver onto the copper pads and through-holes of a PCB. Immersion silver has gained widespread adoption in the electronics industry as an alternative to other finishes like HASL, ENIG, and OSP.
Advantages of Immersion Silver Finish
Immersion silver offers several key benefits compared to other PCB Finishes:
- Excellent solderability: The pure silver coating provides superior wetting and spreading of solder, resulting in reliable solder joints.
- High conductivity: Silver is the most conductive metal, ensuring optimal electrical performance.
- Flat surface: IAg produces a planar surface, ideal for fine-pitch components and Wire Bonding.
- RoHS Compliance: Immersion silver is lead-free and meets RoHS environmental regulations.
- Cost-effective: Compared to gold-based finishes like ENIG, immersion silver is more economical.
- Good shelf life: When stored properly, IAg-finished boards can maintain solderability for 12+ months.
Immersion Silver vs. Other Finishes
Here’s a comparison table of immersion silver against other common PCB finishes:
Finish | Solderability | Durability | Cost | Shelf Life | RoHS |
---|---|---|---|---|---|
Immersion Ag | Excellent | Good | Medium | 12+ months | Yes |
ENIG | Excellent | Excellent | High | 12+ months | Yes |
HASL (SnPb) | Good | Excellent | Low | 6+ months | No |
HASL (Pb-free) | Fair | Excellent | Low | 6+ months | Yes |
OSP | Good | Poor | Low | 3-6 months | Yes |
The Immersion Silver Process
The immersion silver plating process involves several steps to deposit a thin, uniform layer of silver onto the exposed copper surfaces of a PCB.
Step 1: Surface Preparation
Before plating, the PCB undergoes a thorough cleaning process to remove contaminants and oxides from the copper surface. This typically includes:
- Degreasing to remove oils and organics
- Microetching to remove surface oxides and roughen the copper for better adhesion
- Acid activation to ensure a clean, oxide-free surface
Step 2: Silver Immersion
The cleaned PCB is immersed in the immersion silver plating bath, which contains a silver salt solution (usually silver nitrate) and proprietary additives. The silver ions in the solution displace the copper atoms on the surface, resulting in a self-limiting reaction that deposits a thin silver layer. The thickness of the silver layer is typically between 0.05 and 0.2 µm.
The immersion silver reaction can be represented as:
2 Ag+(aq) + Cu(s) → 2 Ag(s) + Cu2+(aq)
Step 3: Rinsing and Drying
After plating, the PCB is rinsed with deionized water to remove any residual plating solution and then dried using hot air or nitrogen. The rinsing step is critical to prevent staining or discoloration of the silver surface.
Step 4: Inspection and Packaging
The finished PCBs are visually inspected for any defects, discoloration, or inconsistencies in the silver coating. Boards that pass inspection are packaged in vacuum-sealed bags with desiccants to maintain the finish quality during storage and transport.
Immersion Silver Shelf Life and Storage
One of the concerns with immersion silver is its susceptibility to tarnishing and oxidation over time, which can degrade solderability. However, proper storage and handling can significantly extend the shelf life of IAg-finished boards.
Factors Affecting Immersion Silver Shelf Life
Several factors can influence the shelf life of immersion silver PCBs:
- Environmental conditions: High humidity, temperature, and exposure to sulfur-containing atmospheres can accelerate tarnishing.
- Surface contamination: Fingerprints, oils, and other contaminants can degrade the silver surface.
- Plating quality: Inconsistencies in the plating process, such as uneven thickness or poor adhesion, can reduce shelf life.
- Storage materials: Acidic or sulfur-containing paper, cardboard, or foam can cause tarnishing.
Best Practices for Storing Immersion Silver PCBs
To maximize the shelf life of immersion silver boards, follow these storage guidelines:
- Store boards in a cool, dry environment with relative humidity below 70% and temperature below 30°C.
- Use sulfur-free, pH-neutral packaging materials, such as vacuum-sealed bags with desiccants.
- Avoid touching the silver surface with bare hands to prevent contamination.
- Bake boards at 100-125°C for 2-4 hours before assembly to remove any absorbed moisture.
By following these practices, immersion silver PCBs can maintain solderability for 12 months or more.
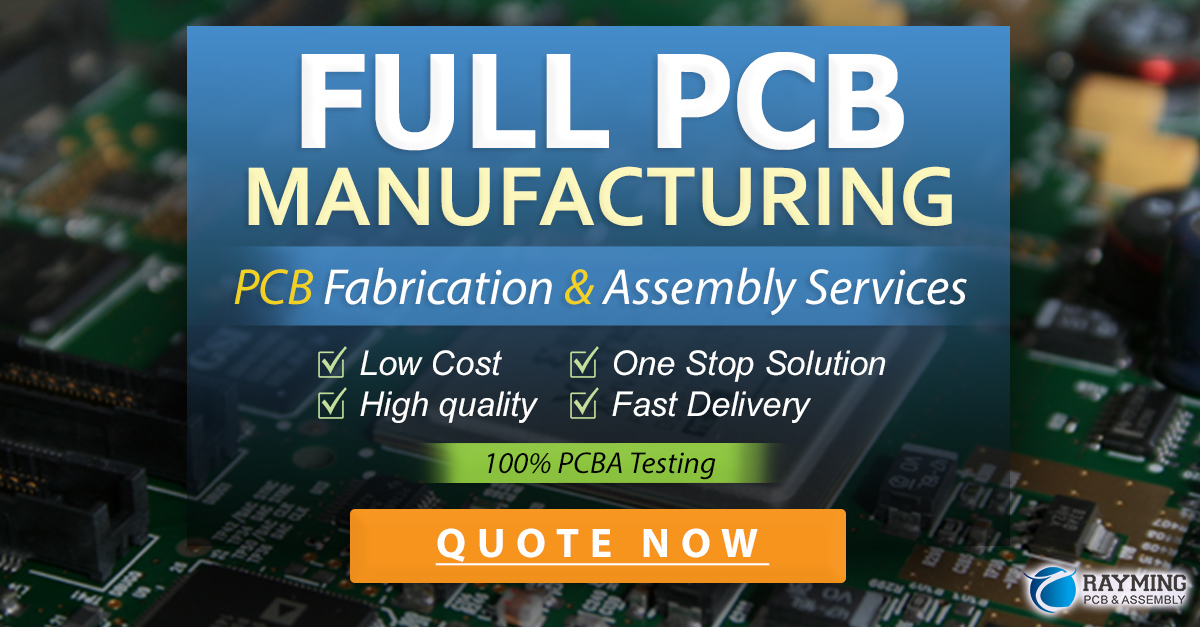
Soldering with Immersion Silver
Immersion silver is known for its excellent solderability, but there are a few considerations to keep in mind when soldering IAg-finished boards.
Solder Paste Selection
When selecting a solder paste for immersion silver, consider the following:
- Alloy composition: Choose a lead-free solder alloy that is compatible with silver, such as SAC305 (96.5% Sn, 3% Ag, 0.5% Cu) or Sn96.5Ag3.5.
- Flux type: Use a no-clean, halide-free flux to minimize the risk of corrosion and residue.
- Powder size: Select a powder size appropriate for the component pitch and stencil thickness, typically Type 3 or Type 4.
Reflow Profile Considerations
Immersion silver is compatible with standard lead-free reflow profiles, but some adjustments may be necessary:
- Peak temperature: Aim for a peak temperature of 235-245°C to ensure proper solder wetting and minimize thermal stress.
- Time above liquidus (TAL): Maintain a TAL of 60-90 seconds to allow for adequate solder joint formation.
- Cooling rate: Control the cooling rate to prevent excessive intermetallic compound (IMC) growth, which can cause brittle solder joints.
Hand Soldering
When hand soldering immersion silver boards, use a lead-free solder wire with a no-clean, halide-free flux core. Set the soldering iron temperature to 350-400°C and minimize the contact time to prevent overheating the silver surface.
Immersion Silver and RoHS Compliance
Immersion silver is a fully RoHS-compliant PCB finish, as it contains no lead or other restricted substances. The RoHS (Restriction of Hazardous Substances) Directive, first introduced in the European Union in 2006, restricts the use of six hazardous materials in electrical and electronic products:
- Lead (Pb)
- Mercury (Hg)
- Cadmium (Cd)
- Hexavalent chromium (Cr6+)
- Polybrominated biphenyls (PBB)
- Polybrominated diphenyl ethers (PBDE)
By using immersion silver as a PCB finish, manufacturers can ensure compliance with RoHS regulations and other environmental standards. This is particularly important for products marketed in the EU, but many other countries have adopted similar restrictions.
Frequently Asked Questions (FAQ)
1. What is the typical thickness of an immersion silver finish?
The typical thickness of an immersion silver finish ranges from 0.05 to 0.2 µm (2-8 µin). This thin layer provides sufficient protection and solderability without adding significant cost or affecting the PCB’s dimensional tolerances.
2. Can immersion silver be used for wire bonding?
Yes, immersion silver is suitable for wire bonding due to its flat, planar surface. It is compatible with both gold and aluminum wire bonding processes, making it a versatile choice for advanced packaging applications.
3. How does immersion silver compare to ENIG in terms of cost?
Immersion silver is generally more cost-effective than ENIG (Electroless Nickel Immersion Gold) due to the lower cost of silver compared to gold. The simpler plating process also contributes to the lower overall cost of IAg.
4. Is immersion silver suitable for High-Frequency PCBs?
Yes, immersion silver is an excellent choice for high-frequency PCBs due to its high conductivity and low surface roughness. The thin, uniform silver layer minimizes signal loss and maintains the PCB’s controlled impedance characteristics.
5. Can immersion silver be used in combination with other finishes?
Immersion silver can be used in combination with other finishes, such as ENIG or OSP, in a mixed-finish PCB design. This allows designers to select the most appropriate finish for each area of the board based on requirements such as solderability, wire bonding, or cost.
Conclusion
Immersion silver is a high-performance, RoHS-compliant PCB finish that offers excellent solderability, conductivity, and shelf life. Its advantages, such as flat surface, cost-effectiveness, and compatibility with various soldering processes, make it a popular choice for a wide range of electronics applications. By understanding the immersion silver plating process, storage requirements, and soldering considerations, PCB manufacturers and assemblers can ensure the highest quality and reliability of their immersion silver-finished boards.
Leave a Reply