Introduction to PCB Finishes
Printed Circuit Boards (PCBs) are essential components in modern electronic devices. They provide a platform for mounting and interconnecting electronic components, ensuring reliable and efficient functionality. One crucial aspect of PCB manufacturing is the choice of surface finish. The surface finish protects the exposed copper traces on the PCB from oxidation and enhances the solderability of the board. Two popular PCB finishes are Organic Solderability Preservative (OSP) and Electroless Nickel Immersion Gold (ENIG). In this article, we will delve into the details of OSP and ENIG, exploring their characteristics, advantages, and applications.
What is OSP?
Overview of OSP
Organic Solderability Preservative (OSP) is a chemical coating applied to the exposed copper traces on a PCB. It is a thin, transparent layer that protects the copper from oxidation and maintains its solderability. OSP is an organic compound, typically consisting of benzimidazole or benzotriazole derivatives.
How OSP Works
The OSP coating process involves the following steps:
- Cleaning: The PCB is thoroughly cleaned to remove any contaminants or residues.
- Micro-etching: The copper surface is slightly etched to improve adhesion of the OSP coating.
- OSP Application: The PCB is immersed in an OSP solution, allowing the organic compounds to form a protective layer on the copper surface.
- Drying: The PCB is dried to remove any excess solution and ensure a uniform coating.
The OSP coating chemically bonds with the copper surface, creating a barrier against oxidation. It also enhances the wettability of the copper, enabling better solder joint formation during the assembly process.
Advantages of OSP
OSP offers several advantages as a PCB surface finish:
- Cost-effective: OSP is one of the most economical surface finish options available.
- Flat surface: OSP provides a flat surface, making it suitable for fine-pitch components and high-density designs.
- Good solderability: OSP maintains the solderability of the copper surface, ensuring reliable solder joints.
- Quick processing: The OSP coating process is relatively fast, reducing manufacturing time.
- Environmentally friendly: OSP is an environmentally friendly option as it does not contain lead or other harmful substances.
Disadvantages of OSP
Despite its advantages, OSP also has some limitations:
- Limited shelf life: OSP-coated PCBs have a shorter shelf life compared to other surface finishes. The coating can degrade over time, affecting solderability.
- Sensitivity to handling: OSP-coated PCBs are susceptible to contamination from handling, requiring careful storage and packaging.
- Not suitable for multiple reflow cycles: OSP may not withstand multiple reflow cycles, making it less suitable for certain assembly processes.
What is ENIG?
Overview of ENIG
Electroless Nickel Immersion Gold (ENIG) is a two-layer metallic surface finish applied to PCBs. It consists of a layer of nickel, followed by a thin layer of gold. The nickel layer provides a barrier against copper diffusion, while the gold layer protects the nickel from oxidation and enhances solderability.
How ENIG Works
The ENIG coating process involves the following steps:
- Cleaning: The PCB is cleaned to remove any contaminants or residues.
- Micro-etching: The copper surface is slightly etched to improve adhesion of the nickel layer.
- Electroless Nickel Plating: The PCB is immersed in an electroless nickel plating solution, allowing a layer of nickel to be deposited on the copper surface.
- Immersion Gold Plating: The nickel-plated PCB is then immersed in an immersion gold solution, resulting in a thin layer of gold deposited on top of the nickel.
- Rinsing and Drying: The PCB is rinsed and dried to remove any excess solution and ensure a uniform coating.
The nickel layer in ENIG serves as a barrier, preventing the diffusion of copper into the solder joint. The gold layer provides excellent solderability and protects the nickel from oxidation.
Advantages of ENIG
ENIG offers several advantages as a PCB surface finish:
- Excellent solderability: The gold layer in ENIG provides excellent solderability, resulting in reliable solder joints.
- Long shelf life: ENIG-coated PCBs have a longer shelf life compared to OSP, as the gold layer protects the nickel from oxidation.
- Suitable for multiple reflow cycles: ENIG can withstand multiple reflow cycles, making it suitable for various assembly processes.
- Good corrosion resistance: The nickel layer in ENIG provides good corrosion resistance, protecting the copper traces.
- Compatibility with various components: ENIG is compatible with a wide range of components, including fine-pitch and BGA packages.
Disadvantages of ENIG
ENIG also has some drawbacks to consider:
- Higher cost: ENIG is more expensive compared to OSP due to the use of gold and the additional processing steps involved.
- Potential for black pad: ENIG can sometimes lead to a phenomenon called “black pad,” where the nickel layer becomes brittle and separates from the copper surface, causing solderability issues.
- Thicker surface: ENIG results in a slightly thicker surface compared to OSP, which may impact certain fine-pitch applications.
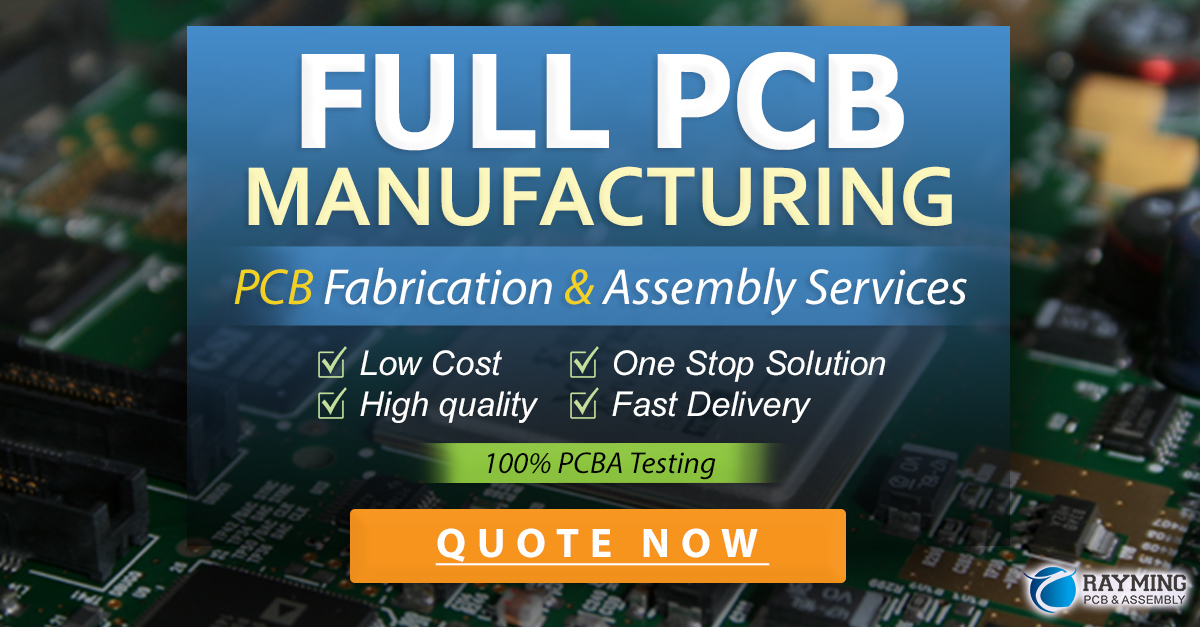
OSP vs ENIG: A Comparison
Characteristic | OSP | ENIG |
---|---|---|
Composition | Organic compound (benzimidazole or benzotriazole) | Nickel layer + thin gold layer |
Thickness | Thin, transparent layer | Thicker than OSP |
Solderability | Good | Excellent |
Shelf Life | Limited (degrades over time) | Longer (gold protects nickel from oxidation) |
Reflow Cycles | Not suitable for multiple reflow cycles | Suitable for multiple reflow cycles |
Cost | Cost-effective | More expensive than OSP |
Corrosion Resistance | Limited | Good (nickel layer provides protection) |
Compatibility | Suitable for fine-pitch components | Compatible with various components, including fine-pitch |
Potential Issues | Contamination from handling, degradation over time | Black pad (nickel layer becomes brittle) |
Applications of OSP and ENIG
OSP Applications
OSP is commonly used in the following applications:
- Consumer electronics: OSP is often used in cost-sensitive consumer electronic products where solderability and cost are primary concerns.
- Short-term storage: OSP is suitable for PCBs that will be assembled relatively quickly after manufacturing, as it has a limited shelf life.
- Fine-pitch components: OSP provides a flat surface, making it suitable for mounting fine-pitch components.
ENIG Applications
ENIG is preferred in applications that require:
- Long-term storage: ENIG-coated PCBs have a longer shelf life, making them suitable for products that may be stored for extended periods before assembly.
- Multiple reflow cycles: ENIG can withstand multiple reflow cycles, making it suitable for assembly processes that involve multiple heating stages.
- Corrosion resistance: The nickel layer in ENIG provides good corrosion resistance, making it suitable for applications exposed to harsh environments.
- High-reliability products: ENIG is often used in high-reliability products, such as aerospace, medical, and military applications, where solderability and reliability are critical.
Conclusion
Choosing between OSP and ENIG as a PCB surface finish depends on various factors, including cost, solderability requirements, shelf life, and the specific application. OSP is a cost-effective option that provides good solderability and is suitable for fine-pitch components. However, it has a limited shelf life and may not withstand multiple reflow cycles. On the other hand, ENIG offers excellent solderability, longer shelf life, and compatibility with multiple reflow cycles. It also provides good corrosion resistance but comes at a higher cost and has the potential for black pad issues.
When selecting a PCB surface finish, it is essential to consider the specific requirements of the application, the assembly process, and the long-term reliability expectations. Consulting with PCB manufacturers and assembly experts can help in making an informed decision based on the project’s needs.
As technology advances, new surface finish options may emerge, offering improved performance and addressing the limitations of existing finishes. Staying updated with industry trends and advancements can help in selecting the most suitable surface finish for future PCB designs.
Frequently Asked Questions (FAQ)
1. What is the main difference between OSP and ENIG?
OSP is an organic compound coating that protects the copper traces on a PCB, while ENIG is a two-layer metallic coating consisting of a nickel layer and a thin gold layer.
2. Which surface finish is more cost-effective, OSP or ENIG?
OSP is generally more cost-effective compared to ENIG due to its simpler processing and the absence of expensive materials like gold.
3. Can OSP withstand multiple reflow cycles?
OSP is not suitable for multiple reflow cycles as the coating may degrade during repeated heating stages. ENIG, on the other hand, can withstand multiple reflow cycles.
4. What is the shelf life of OSP and ENIG-coated PCBs?
OSP-coated PCBs have a limited shelf life as the coating can degrade over time, affecting solderability. ENIG-coated PCBs have a longer shelf life due to the protection provided by the gold layer.
5. Which surface finish is more suitable for fine-pitch components?
Both OSP and ENIG are suitable for fine-pitch components. OSP provides a flat surface, while ENIG’s thin gold layer allows for good solderability and compatibility with fine-pitch components.
Leave a Reply