What is an 8 Layer PCB?
An 8 layer PCB is a printed circuit board that consists of eight conductive copper layers laminated together with insulating material. These layers are interconnected through via holes, allowing for complex routing and signal integrity. The increased number of layers enables designers to create more compact and feature-rich electronic devices.
Advantages of 8 Layer PCBs
- High Density: 8 layer PCBs can accommodate a large number of components and complex circuitry in a compact space.
- Improved Signal Integrity: The additional layers help reduce electromagnetic interference (EMI) and crosstalk, ensuring cleaner and more stable signals.
- Enhanced Thermal Management: Multiple layers allow for better heat dissipation, preventing overheating and improving the overall reliability of the device.
- Increased Functionality: With more layers, designers can incorporate advanced features and functionalities into the PCB design.
Choosing the Right 8 Layer PCB Manufacturer
Selecting a reliable and experienced 8 layer PCB manufacturer is crucial to ensure the quality and performance of your final product. Consider the following factors when choosing a manufacturer:
Experience and Expertise
Look for a manufacturer with a proven track record in producing 8 layer PCBs. They should have the necessary expertise and knowledge to handle complex designs and meet your specific requirements.
Quality Control and Certifications
Ensure that the manufacturer adheres to strict quality control standards and holds relevant certifications, such as ISO 9001 and UL. These certifications demonstrate their commitment to delivering high-quality products.
Technology and Equipment
A reputable 8 layer PCB manufacturer should invest in state-of-the-art technology and equipment. This includes advanced manufacturing processes, such as automated optical inspection (AOI) and X-ray inspection, to ensure the accuracy and reliability of the PCBs.
Lead Time and Cost
Consider the manufacturer’s lead time and cost structure. While cost is an important factor, it should not compromise the quality of the PCBs. Strike a balance between affordability and reliability to ensure the best value for your project.
The 8 Layer PCB Manufacturing Process
The manufacturing process for 8 layer PCBs involves several critical steps. Understanding these steps can help you appreciate the complexity and precision involved in producing high-quality PCBs.
Step 1: Design and Preparation
The process begins with the PCB design, which is created using specialized software such as Altium Designer or Eagle. The design is then thoroughly reviewed and optimized for manufacturability.
Step 2: Layer Stack-up
The layer stack-up is determined based on the design requirements. This involves arranging the eight conductive layers and insulating materials in the appropriate order to ensure optimal signal integrity and manufacturability.
Step 3: Lamination
The conductive layers and insulating materials are laminated together under high pressure and temperature to form a solid, multi-layer structure.
Step 4: Drilling
Via holes are drilled through the laminated board to create interconnections between the layers. The size and position of these holes are critical for ensuring proper connectivity.
Step 5: Plating
The drilled holes are plated with copper to establish electrical connections between the layers. This process involves electroless copper deposition followed by electrolytic copper plating.
Step 6: Etching
The unwanted copper areas on each layer are etched away using a chemical process, leaving only the desired conductive traces and pads.
Step 7: Solder Mask and Silkscreen
A solder mask is applied to the PCB surface to protect the copper traces and prevent short circuits. Silkscreen printing is then used to add component labels and other identifying marks.
Step 8: Surface Finish
A surface finish, such as ENIG (Electroless Nickel Immersion Gold) or HASL (Hot Air Solder Leveling), is applied to the exposed copper areas to enhance solderability and protect against oxidation.
Step 9: Electrical Testing
The manufactured PCBs undergo rigorous electrical testing to ensure they meet the specified requirements and are free from defects.
Step 10: Packaging and Shipping
The completed 8 layer PCBs are packaged and shipped to the customer, ready for component assembly and integration into the final electronic device.
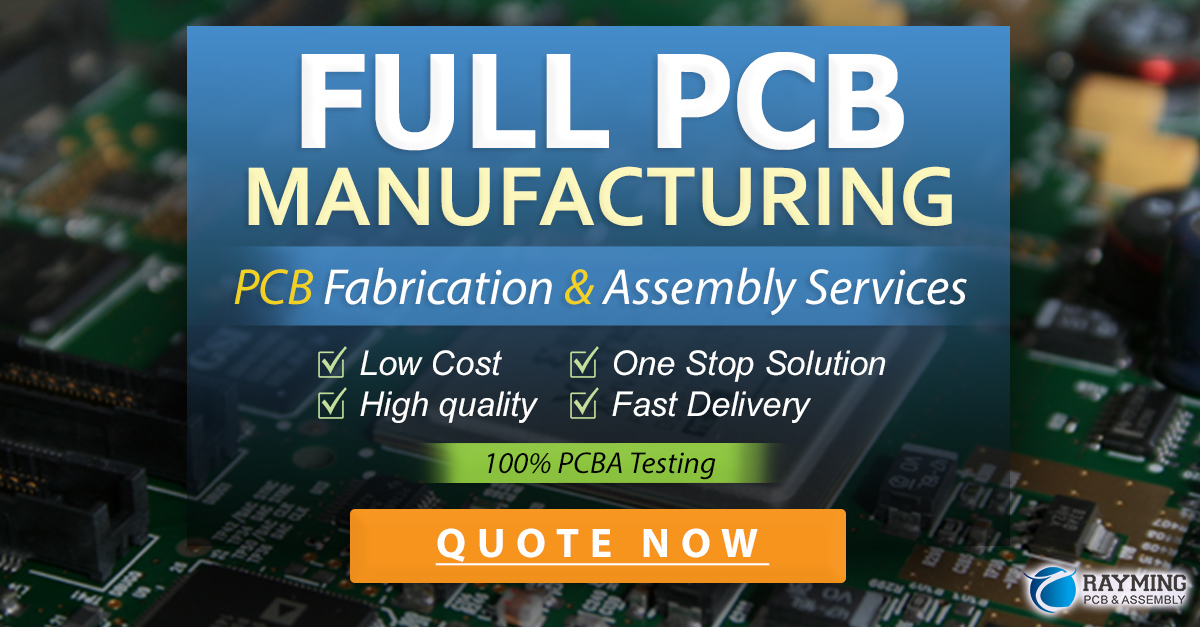
Designing for 8 Layer PCBs
Designing an 8 layer PCB requires careful consideration of various factors to ensure optimal performance and manufacturability. Here are some key design guidelines:
Signal Integrity
Pay close attention to signal integrity by minimizing crosstalk and EMI. Use proper routing techniques, such as proper trace spacing and ground planes, to maintain clean and stable signals.
Layer Stack-up
Optimize the layer stack-up to achieve the desired electrical characteristics and minimize signal integrity issues. Consider factors such as dielectric constant, thickness, and copper weight when selecting materials.
Via Placement
Strategically place vias to minimize signal distortion and improve manufacturability. Avoid placing vias in high-density areas or close to critical components.
Thermal Management
Incorporate thermal management techniques, such as using thermal vias and copper pour, to dissipate heat effectively and prevent overheating.
Design Rule Check (DRC)
Perform thorough Design Rule Checks (DRC) to ensure your design adheres to the manufacturer’s specifications and industry standards. This helps avoid potential manufacturing issues and delays.
FAQ
-
Q: What is the typical turnaround time for 8 layer PCBs?
A: The turnaround time for 8 layer PCBs varies depending on the manufacturer and the complexity of the design. Generally, it ranges from 7 to 14 days, but expedited options may be available for urgent projects. -
Q: How much does an 8 layer PCB cost?
A: The cost of an 8 layer PCB depends on factors such as the size, quantity, and complexity of the design. On average, 8 layer PCBs are more expensive than 4 or 6 layer PCBs due to the increased material and manufacturing costs. It’s best to request a quote from multiple manufacturers to compare pricing. -
Q: Can 8 layer PCBs be manufactured with impedance control?
A: Yes, 8 layer PCBs can be manufactured with impedance control. Impedance control is essential for high-speed designs to ensure proper signal integrity. Discuss your specific impedance requirements with the manufacturer to ensure they can meet your needs. -
Q: What are the common applications of 8 layer PCBs?
A: 8 layer PCBs are commonly used in complex electronic devices that require high-density component placement and advanced functionalities. Some examples include: - Telecommunications equipment
- Medical devices
- Aerospace and defense systems
- High-performance computing devices
-
Automotive electronics
-
Q: How can I ensure the quality of my 8 layer PCBs?
A: To ensure the quality of your 8 layer PCBs, consider the following: - Choose a reputable and experienced manufacturer with strict quality control processes.
- Provide clear and detailed design specifications to minimize misinterpretation.
- Request a prototype or sample before mass production to verify the quality and functionality.
- Perform thorough testing and inspection upon receiving the manufactured PCBs.
- Establish open communication with your manufacturer to address any issues promptly.
Conclusion
8 layer PCBs offer a powerful solution for creating complex and compact electronic devices. By understanding the manufacturing process, design considerations, and the importance of choosing the right manufacturer, you can ensure the success of your 8 layer PCB project. Remember to prioritize quality, reliability, and open communication throughout the manufacturing process to achieve the best results.
When selecting an 8 layer PCB manufacturer, consider their experience, expertise, quality control measures, and technological capabilities. By partnering with a trusted manufacturer and following best design practices, you can unlock the full potential of 8 layer PCBs and bring your innovative electronic products to life.
Layer | Description |
---|---|
1 | Top Layer (Signal) |
2 | Ground Plane |
3 | Signal Layer |
4 | Power Plane |
5 | Signal Layer |
6 | Ground Plane |
7 | Signal Layer |
8 | Bottom Layer (Signal) |
Table 1: Typical 8 Layer PCB Stack-up
In conclusion, 8 layer PCBs are a testament to the advancements in PCB manufacturing technology. By leveraging the benefits of increased layer count, designers can create more compact, feature-rich, and reliable electronic devices. With the right manufacturer by your side and a solid understanding of the manufacturing process and design considerations, you can confidently embark on your 8 layer PCB journey and bring your innovative ideas to fruition.
Leave a Reply