Introduction to LED PCB Base Plates
Light-emitting diode (LED) printed circuit board (PCB) base plates are essential components in the manufacturing of LED lighting products. They provide a stable and efficient platform for mounting LED components and ensuring optimal heat dissipation. With the increasing demand for LED lighting solutions, choosing the right LED PCB base plate is crucial for achieving high-quality and reliable products.
In this comprehensive analysis, we will compare different types of LED PCB base plates, examining their materials, thermal properties, and manufacturing processes. By understanding the advantages and disadvantages of each type, manufacturers can make informed decisions when selecting the most suitable base plate for their LED lighting applications.
Types of LED PCB Base Plates
1. Aluminum PCB Base Plates
Aluminum PCB base plates are widely used in LED lighting applications due to their excellent thermal conductivity and lightweight properties. These base plates consist of an aluminum substrate that is bonded to a thin layer of copper, which serves as the conductive layer for the PCB.
Advantages of Aluminum PCB Base Plates
- High thermal conductivity: Aluminum has a thermal conductivity of approximately 205 W/mK, allowing for efficient heat dissipation from the LED components.
- Lightweight: Aluminum PCBs are lighter compared to other base plate materials, making them suitable for applications where weight is a concern.
- Cost-effective: Aluminum PCBs are relatively inexpensive compared to other high-performance base plate materials.
Disadvantages of Aluminum PCB Base Plates
- Limited electrical insulation: Aluminum is not an inherently insulating material, requiring an additional dielectric layer to provide electrical insulation between the conductive layer and the substrate.
- Potential for corrosion: Aluminum is susceptible to corrosion, especially in harsh environmental conditions, which can affect the long-term reliability of the LED PCB.
2. Copper PCB Base Plates
Copper PCB base plates offer superior thermal conductivity and electrical performance compared to aluminum base plates. These base plates consist of a thick copper substrate that provides both the conductive layer and the heat dissipation medium.
Advantages of Copper PCB Base Plates
- Excellent thermal conductivity: Copper has a thermal conductivity of approximately 400 W/mK, which is nearly twice that of aluminum, enabling highly efficient heat dissipation.
- Superior electrical conductivity: Copper is an excellent electrical conductor, allowing for better current carrying capacity and reduced power losses.
- High reliability: Copper PCBs are more resistant to corrosion and have a longer lifespan compared to aluminum PCBs.
Disadvantages of Copper PCB Base Plates
- Higher cost: Copper PCBs are more expensive than aluminum PCBs due to the higher material cost and more complex manufacturing processes.
- Increased weight: Copper is denser than aluminum, resulting in heavier PCBs, which may not be suitable for weight-sensitive applications.
3. Ceramic PCB Base Plates
Ceramic PCB base plates are gaining popularity in high-power LED applications due to their exceptional thermal performance and electrical insulation properties. These base plates are made from ceramic materials, such as aluminum nitride (AlN) or alumina (Al2O3), which offer a combination of high thermal conductivity and excellent electrical insulation.
Advantages of Ceramic PCB Base Plates
- High thermal conductivity: Ceramic materials like AlN have a thermal conductivity of up to 285 W/mK, providing excellent heat dissipation capabilities.
- Excellent electrical insulation: Ceramic materials are inherently electrically insulating, eliminating the need for additional dielectric layers.
- High temperature stability: Ceramic PCBs can withstand high operating temperatures without deteriorating, making them suitable for high-power LED applications.
Disadvantages of Ceramic PCB Base Plates
- High cost: Ceramic PCBs are significantly more expensive than aluminum or copper PCBs due to the specialized manufacturing processes and materials involved.
- Brittle nature: Ceramic materials are inherently brittle, requiring careful handling during manufacturing and assembly to avoid cracking or breaking.
Comparison of LED PCB Base Plate Materials
To help manufacturers choose the most suitable LED PCB base plate for their applications, we have compiled a comparison table highlighting the key properties of aluminum, copper, and ceramic base plates.
Property | Aluminum PCB | Copper PCB | Ceramic PCB |
---|---|---|---|
Thermal Conductivity | 205 W/mK | 400 W/mK | Up to 285 W/mK |
Electrical Conductivity | Good | Excellent | Poor (insulating) |
Weight | Lightweight | Heavy | Moderate |
Cost | Low | High | Very High |
Corrosion Resistance | Moderate | High | High |
Temperature Stability | Good | Good | Excellent |
Electrical Insulation | Requires additional layer | Requires additional layer | Inherent |
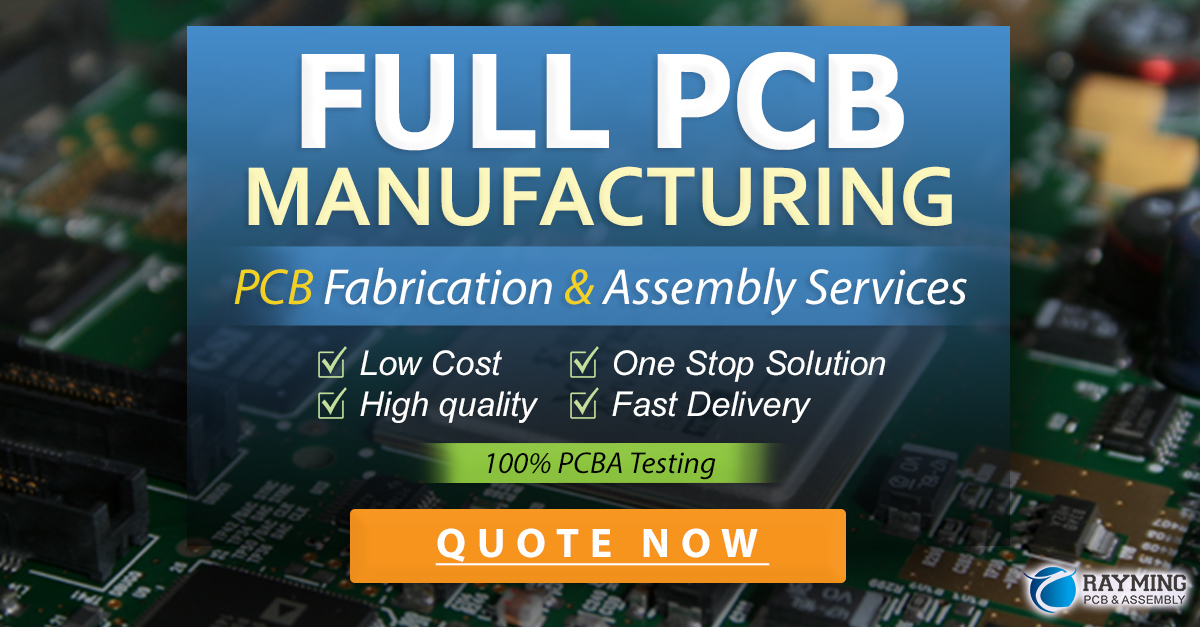
Factors to Consider When Choosing LED PCB Base Plates
When selecting an LED PCB base plate, manufacturers should consider several key factors to ensure optimal performance and reliability of their LED lighting products.
1. Thermal Management Requirements
The primary function of an LED PCB base plate is to dissipate heat generated by the LED components. Manufacturers should consider the thermal power density of their LED application and choose a base plate material with sufficient thermal conductivity to maintain acceptable operating temperatures.
2. Electrical Performance
The electrical conductivity of the base plate material can impact the overall efficiency and power loss of the LED PCB. Copper base plates offer the best electrical performance, while aluminum and ceramic base plates may require additional measures to minimize electrical losses.
3. Weight and Size Constraints
In applications where weight and size are critical factors, such as in automotive or aerospace lighting, manufacturers should opt for lightweight base plate materials like aluminum or ceramic. However, the trade-off between weight and thermal performance should be carefully evaluated.
4. Environmental Conditions
The operating environment of the LED lighting product should be considered when selecting a base plate material. In harsh conditions, such as high humidity or corrosive environments, copper or ceramic base plates may be preferable due to their higher corrosion resistance compared to aluminum.
5. Cost and Manufacturing Considerations
The cost of the base plate material and the associated manufacturing processes can significantly impact the overall cost of the LED lighting product. Aluminum PCBs offer the most cost-effective solution, while copper and ceramic PCBs come with higher costs due to their superior performance and specialized manufacturing requirements.
Frequently Asked Questions (FAQ)
-
Q: What is the main purpose of an LED PCB base plate?
A: The main purpose of an LED PCB base plate is to provide a stable and efficient platform for mounting LED components and to ensure optimal heat dissipation, which is critical for maintaining the performance and longevity of LED lighting products. -
Q: Which base plate material offers the highest thermal conductivity?
A: Copper PCB base plates offer the highest thermal conductivity among the commonly used materials, with a thermal conductivity of approximately 400 W/mK, nearly twice that of aluminum. -
Q: Are ceramic PCB base plates suitable for high-power LED applications?
A: Yes, ceramic PCB base plates are particularly well-suited for high-power LED applications due to their exceptional thermal performance, excellent electrical insulation properties, and high temperature stability. -
Q: Why are aluminum PCB base plates widely used in LED lighting applications?
A: Aluminum PCB base plates are widely used in LED lighting applications because they offer a good balance of thermal conductivity, lightweight properties, and cost-effectiveness, making them suitable for a wide range of LED lighting products. -
Q: How does the operating environment influence the choice of LED PCB base plate material?
A: The operating environment should be considered when selecting an LED PCB base plate material, as harsh conditions, such as high humidity or corrosive environments, may require the use of materials with higher corrosion resistance, such as copper or ceramic base plates.
Conclusion
Choosing the right LED PCB base plate is crucial for ensuring the optimal performance, reliability, and cost-effectiveness of LED lighting products. By understanding the advantages and disadvantages of aluminum, copper, and ceramic base plates, manufacturers can make informed decisions based on their specific application requirements.
Factors such as thermal management, electrical performance, weight and size constraints, environmental conditions, and cost should be carefully considered when selecting an LED PCB base plate material. By weighing these factors and consulting with experienced PCB manufacturers, LED lighting product designers can develop high-quality and efficient solutions that meet the growing demands of the market.
As LED technology continues to advance, it is essential for manufacturers to stay up-to-date with the latest developments in PCB base plate materials and manufacturing processes. By doing so, they can capitalize on the opportunities presented by the rapidly growing LED lighting industry and deliver innovative, high-performance products to their customers.
Leave a Reply