What are Aluminum PCBs?
Aluminum PCBs, also known as metal Core PCBs (MCPCBs), are printed circuit boards that use aluminum as the base material instead of the traditional FR-4 substrate. The aluminum base provides excellent thermal conductivity, allowing for efficient heat dissipation from electronic components. This makes aluminum PCBs ideal for applications that generate significant amounts of heat, such as high-power LED lighting, automotive electronics, and power electronics.
Key Features of Aluminum PCBs
- Excellent thermal conductivity
- Improved heat dissipation
- Enhanced mechanical stability
- Longer lifespan of electronic components
- Lightweight and durable
Advantages of Using Aluminum PCBs
Superior Heat Dissipation
One of the primary advantages of using aluminum PCBs is their superior heat dissipation capabilities. The aluminum base acts as a heat sink, quickly transferring heat away from electronic components and distributing it evenly across the board. This helps to maintain optimal operating temperatures, preventing overheating and ensuring the longevity of the components.
Improved Thermal Management
Aluminum PCBs offer improved thermal management compared to traditional FR-4 PCBs. The high thermal conductivity of aluminum allows for more efficient cooling of electronic components, reducing the need for additional heatsinks or cooling solutions. This can lead to more compact and streamlined designs, as well as cost savings on additional cooling components.
Enhanced Mechanical Stability
The aluminum base of MCPCBs provides enhanced mechanical stability compared to FR-4 PCBs. Aluminum is a strong and durable material that can withstand vibrations, shocks, and other mechanical stresses. This makes aluminum PCBs suitable for applications that require robust and reliable performance, such as automotive electronics and industrial equipment.
Longer Lifespan of Electronic Components
By efficiently dissipating heat and maintaining optimal operating temperatures, aluminum PCBs can significantly extend the lifespan of electronic components. Overheating is a common cause of component failure, and by mitigating this issue, aluminum PCBs can improve the reliability and durability of electronic devices.
Lightweight and Durable
Aluminum PCBs are lightweight compared to other metal core PCBs, such as copper. This makes them suitable for applications where weight is a critical factor, such as in aerospace and portable electronics. Despite their lightweight nature, aluminum PCBs are still highly durable and can withstand harsh environmental conditions.
Applications of Aluminum PCBs
High-Power LED Lighting
Aluminum PCBs are widely used in high-power LED lighting applications due to their excellent thermal management capabilities. LEDs generate a significant amount of heat, and efficient heat dissipation is crucial for maintaining their performance and longevity. Aluminum PCBs can effectively transfer heat away from the LEDs, ensuring stable operation and preventing premature failure.
Automotive Electronics
The automotive industry relies on aluminum PCBs for various electronic applications, such as engine control units, power inverters, and LED lighting systems. The enhanced mechanical stability and thermal management provided by aluminum PCBs make them suitable for the demanding conditions encountered in automotive environments, including vibrations, temperature fluctuations, and exposure to moisture and chemicals.
Power Electronics
Aluminum PCBs are commonly used in power electronic applications, such as switch-mode power supplies, motor drives, and solar inverters. These applications involve high power densities and generate substantial amounts of heat. The excellent thermal conductivity of aluminum PCBs helps to dissipate heat efficiently, ensuring reliable operation and preventing thermal runaway.
Industrial Equipment
Industrial equipment often requires robust and reliable electronic components that can withstand harsh environmental conditions. Aluminum PCBs are well-suited for industrial applications due to their enhanced mechanical stability, thermal management, and durability. They can be found in various industrial devices, such as sensors, controllers, and communication systems.
Aerospace and Defense
Aluminum PCBs are used in aerospace and defense applications where weight reduction and thermal management are critical. The lightweight nature of aluminum PCBs helps to reduce the overall weight of electronic systems, which is essential for aircraft and satellites. Additionally, the enhanced thermal management capabilities of aluminum PCBs ensure reliable operation in the extreme temperature conditions encountered in aerospace environments.
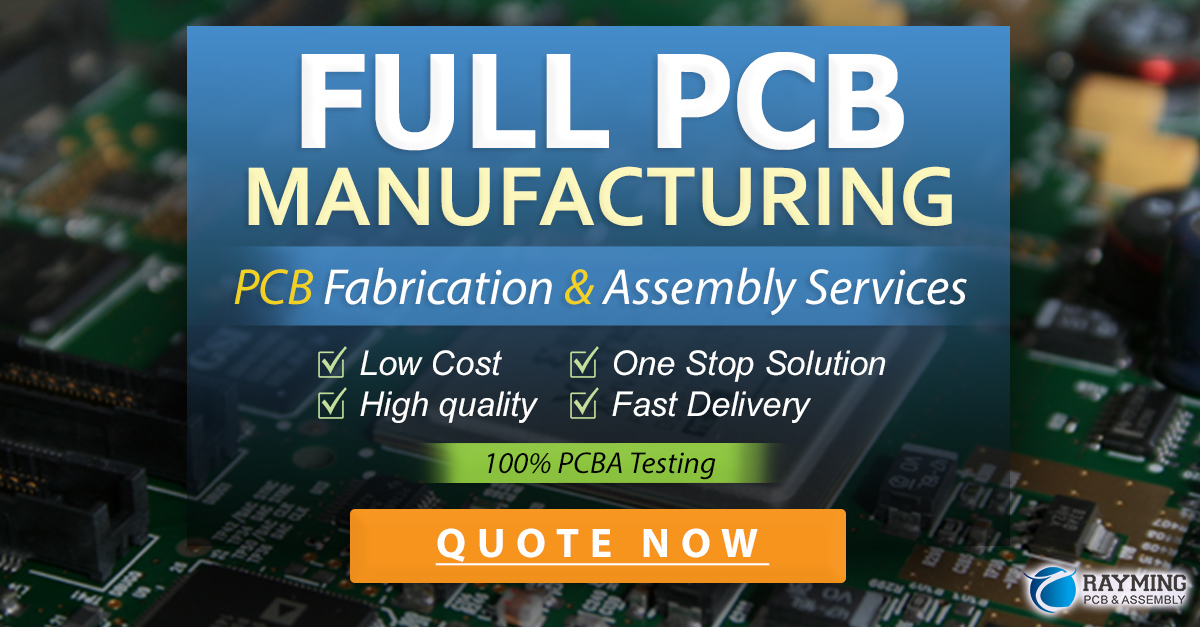
RAYPCB’s Aluminum PCB Manufacturing Capabilities
RAYPCB is a leading manufacturer of high-quality aluminum PCBs, offering a wide range of customization options to meet the specific needs of our clients. Our state-of-the-art manufacturing facilities and experienced team of engineers ensure that every aluminum PCB we produce meets the highest standards of quality and reliability.
Aluminum PCB stackup Options
We offer various aluminum PCB stackup options to cater to different application requirements:
Stackup Type | Description | Typical Applications |
---|---|---|
Single-layer | One layer of copper on an aluminum base | LED lighting, simple power electronics |
Double-layer | Two layers of copper on an aluminum base | Automotive electronics, industrial control systems |
Multi-layer | Multiple layers of copper on an aluminum base | Complex power electronics, aerospace applications |
Dielectric Materials
RAYPCB offers a range of dielectric materials for aluminum PCBs, each with its own unique properties and benefits:
Dielectric Material | Thermal Conductivity (W/mK) | Dielectric Constant | Typical Applications |
---|---|---|---|
Epoxy resin | 0.3 – 0.5 | 3.5 – 4.5 | General-purpose electronics |
Polyimide | 0.2 – 0.3 | 3.2 – 3.6 | High-temperature applications |
Ceramic | 2.0 – 3.0 | 6.0 – 10.0 | High-frequency applications |
Advanced Manufacturing Techniques
RAYPCB employs advanced manufacturing techniques to ensure the highest quality and reliability of our aluminum PCBs:
- Precision drilling and routing for accurate hole placement and board outline
- Selective plating for enhanced thermal management and signal integrity
- Automated optical inspection (AOI) for defect detection and quality control
- Thermal cycling and stress testing to ensure reliability under extreme conditions
Designing with Aluminum PCBs
When designing with aluminum PCBs, there are several key considerations to keep in mind:
Thermal Management
- Ensure proper thermal interface material (TIM) selection and application between the aluminum base and electronic components
- Consider the placement of high-power components to optimize heat dissipation
- Use thermal vias to transfer heat from the components to the aluminum base
Mechanical Considerations
- Account for the different thermal expansion coefficients of aluminum and other materials used in the PCB
- Use appropriate fastening methods and mounting techniques to ensure mechanical stability
- Consider the weight and size constraints of the application
Electrical Considerations
- Ensure proper grounding and shielding to minimize electromagnetic interference (EMI)
- Consider the impact of the aluminum base on signal integrity and impedance matching
- Use appropriate surface finishes and coatings to prevent corrosion and enhance solderability
Frequently Asked Questions (FAQ)
1. What is the difference between aluminum PCBs and traditional FR-4 PCBs?
Aluminum PCBs use an aluminum base as the substrate material, while FR-4 PCBs use a glass-reinforced epoxy laminate. Aluminum PCBs offer superior thermal conductivity and heat dissipation compared to FR-4 PCBs, making them ideal for applications that generate significant amounts of heat.
2. Can aluminum PCBs be used for high-frequency applications?
Yes, aluminum PCBs can be used for high-frequency applications. However, the choice of dielectric material is crucial in these cases. Ceramic dielectrics, which have a higher dielectric constant and lower loss tangent, are often used in combination with aluminum PCBs for high-frequency applications.
3. How do I select the appropriate aluminum PCB stackup for my application?
The selection of the appropriate aluminum PCB stackup depends on several factors, including the complexity of the circuit, the power requirements, and the thermal management needs. Single-layer and double-layer stackups are suitable for simple and low-power applications, while multi-layer stackups are used for more complex and high-power applications.
4. What are the common challenges when designing with aluminum PCBs?
Some common challenges when designing with aluminum PCBs include accounting for the different thermal expansion coefficients of materials, ensuring proper thermal interface material selection and application, and considering the impact of the aluminum base on signal integrity and impedance matching.
5. How does RAYPCB Ensure the quality and reliability of its aluminum PCBs?
RAYPCB employs advanced manufacturing techniques, such as precision drilling and routing, selective plating, automated optical inspection, and thermal cycling and stress testing, to ensure the highest quality and reliability of our aluminum PCBs. Our experienced team of engineers works closely with clients to provide customized solutions that meet their specific requirements.
Conclusion
Aluminum PCBs offer numerous advantages over traditional FR-4 PCBs, including superior thermal management, enhanced mechanical stability, and longer lifespan of electronic components. These benefits make aluminum PCBs an ideal choice for a wide range of applications, such as high-power LED lighting, automotive electronics, power electronics, industrial equipment, and aerospace and defense.
RAYPCB is a leading manufacturer of high-quality aluminum PCBs, offering a wide range of customization options and advanced manufacturing techniques to meet the specific needs of our clients. By understanding the key considerations when designing with aluminum PCBs and leveraging RAYPCB’s expertise, you can unlock the full potential of this innovative technology and create reliable, high-performance electronic products.
For more information about aluminum PCBs and how RAYPCB can help you with your next project, please visit our website or contact our sales team today.
Leave a Reply