What are Aluminum PCBs?
Aluminum PCBs, also known as metal core PCBs (MCPCBs), are printed circuit boards that use aluminum as the base material instead of the traditional FR-4 substrate. The aluminum base provides excellent thermal conductivity, allowing for efficient heat dissipation from electronic components. This makes aluminum PCBs ideal for applications that generate significant amounts of heat, such as high-power LEDs, power electronics, and automotive systems.
Key Features of Aluminum PCBs
- High thermal conductivity
- Improved heat dissipation
- Increased durability and strength
- Lightweight compared to other metal core PCBs
- Cost-effective solution for thermal management
Advantages of Using Aluminum PCBs
Enhanced Thermal Management
One of the primary advantages of using aluminum PCBs is their superior thermal management capabilities. The aluminum base acts as a heat sink, efficiently conducting heat away from electronic components. This helps to prevent overheating, which can lead to component failure and reduced system reliability.
The thermal conductivity of aluminum is significantly higher than that of traditional FR-4 substrates, as shown in the table below:
Material | Thermal Conductivity (W/mK) |
---|---|
Aluminum | 205 – 250 |
FR-4 | 0.3 – 0.4 |
This high thermal conductivity allows aluminum PCBs to dissipate heat more effectively, ensuring stable operation even in high-temperature environments.
Improved Durability and Strength
Aluminum PCBs offer improved durability and strength compared to traditional PCBs. The aluminum base provides a robust foundation that can withstand physical stresses and vibrations. This makes aluminum PCBs suitable for applications that require high reliability, such as automotive electronics and industrial control systems.
Moreover, aluminum PCBs have a higher flexural strength than FR-4 PCBs, making them more resistant to bending and warping. This is particularly important for applications where the PCB may be subjected to mechanical stresses during installation or operation.
Lightweight and Cost-Effective
Compared to other metal core PCBs, such as those based on copper or steel, aluminum PCBs are lightweight. This makes them an attractive option for applications where weight reduction is crucial, such as in aerospace and portable electronics.
In addition to being lightweight, aluminum PCBs are also cost-effective. Aluminum is less expensive than other metals used in metal core PCBs, making it a more affordable solution for thermal management. This cost advantage is particularly significant in high-volume production runs.
Applications of Aluminum PCBs
High-Power LED Lighting
Aluminum PCBs are widely used in high-power LED lighting applications. LEDs generate a significant amount of heat, which must be effectively dissipated to ensure optimal performance and longevity. By using aluminum PCBs, LED manufacturers can efficiently conduct heat away from the LEDs, preventing thermal degradation and premature failure.
Power Electronics
Power electronics, such as motor drives, inverters, and power supplies, often require efficient thermal management to operate reliably. Aluminum PCBs provide an effective solution for dissipating heat generated by power components, such as MOSFETs and IGBTs. By maintaining a stable operating temperature, aluminum PCBs can help extend the lifespan of power electronics and improve system performance.
Automotive Electronics
Automotive electronics are subjected to harsh environmental conditions, including high temperatures, vibrations, and mechanical stresses. Aluminum PCBs offer a rugged and reliable solution for automotive applications, such as engine control units, power steering systems, and LED lighting. The aluminum base provides excellent thermal management and mechanical stability, ensuring reliable operation in demanding automotive environments.
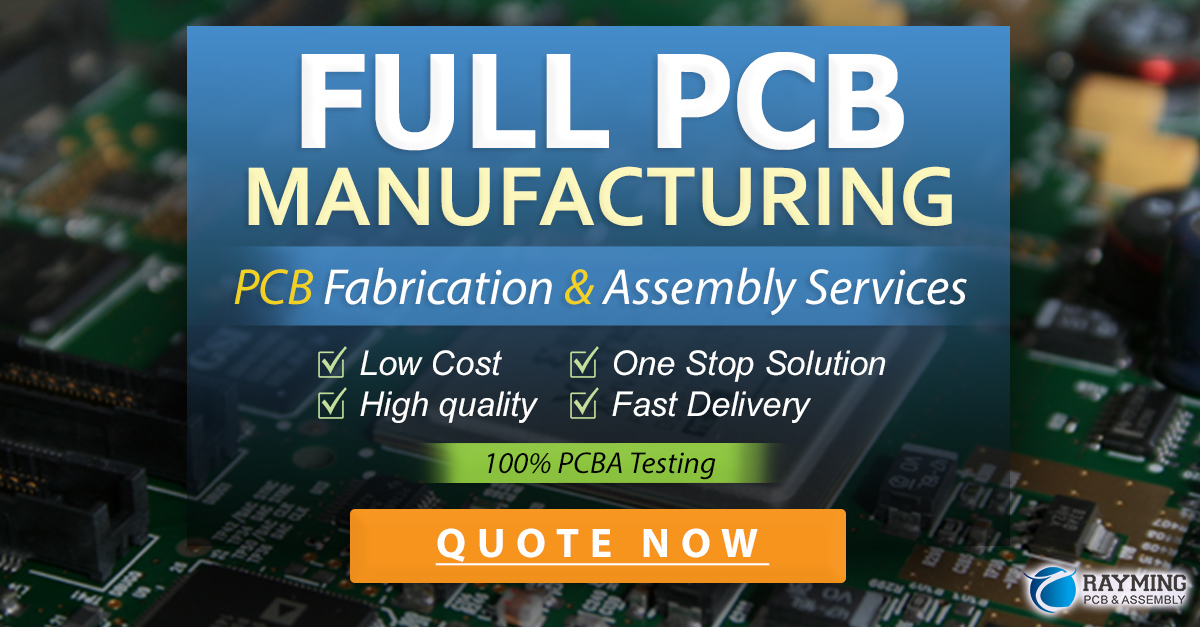
Designing with Aluminum PCBs
Thermal Considerations
When designing with aluminum PCBs, it is essential to consider the thermal characteristics of the system. The thermal conductivity of the aluminum base should be taken into account when calculating the thermal resistance and heat dissipation requirements.
Thermal vias, which are conductive paths that transfer heat from the components to the aluminum base, play a crucial role in the thermal management of aluminum PCBs. The size, number, and placement of thermal vias should be carefully considered to ensure efficient heat transfer.
Dielectric Layer Selection
The dielectric layer, which insulates the copper traces from the aluminum base, is another important consideration when designing with aluminum PCBs. The dielectric material should have good thermal conductivity to facilitate heat transfer while providing adequate electrical insulation.
Some common dielectric materials used in aluminum PCBs include:
- Alumina (Al2O3)
- Boron Nitride (BN)
- Aluminum Nitride (AlN)
The choice of dielectric material depends on the specific requirements of the application, such as the required thermal conductivity, dielectric strength, and cost.
Manufacturing Process
The manufacturing process for aluminum PCBs differs from that of traditional PCBs due to the presence of the aluminum base. The key steps in the manufacturing process include:
- Bonding the dielectric layer to the aluminum base
- Applying the copper foil to the dielectric layer
- Patterning the copper traces using standard PCB fabrication techniques
- Applying a protective coating to the exposed aluminum surfaces
It is important to work with a PCB manufacturer that has experience in fabricating aluminum PCBs to ensure the highest quality and reliability.
Choosing the Right Aluminum PCB Manufacturer
When selecting an aluminum PCB manufacturer, several factors should be considered to ensure the best quality and service. These factors include:
- Experience in manufacturing aluminum PCBs
- Quality control processes and certifications
- Technical support and design assistance
- Lead times and delivery reliability
- Cost and minimum order quantities
RAYPCB, a leading PCB manufacturer, offers high-quality aluminum PCBs for a wide range of applications. With state-of-the-art manufacturing facilities and a team of experienced engineers, RAYPCB provides reliable and cost-effective aluminum PCB solutions to meet the unique needs of their customers.
Frequently Asked Questions (FAQ)
-
Q: What is the difference between aluminum PCBs and traditional FR-4 PCBs?
A: Aluminum PCBs use an aluminum base instead of the FR-4 substrate used in traditional PCBs. The aluminum base provides superior thermal conductivity, allowing for better heat dissipation from electronic components. -
Q: Can aluminum PCBs be used for all types of electronic applications?
A: While aluminum PCBs offer excellent thermal management and mechanical stability, they are particularly suitable for applications that generate significant amounts of heat, such as high-power LEDs, power electronics, and automotive systems. -
Q: Are aluminum PCBs more expensive than traditional PCBs?
A: Aluminum PCBs may have a higher initial cost compared to traditional FR-4 PCBs due to the additional materials and manufacturing processes involved. However, they can be cost-effective in the long run, especially for applications that require efficient thermal management and high reliability. -
Q: What are the key design considerations when working with aluminum PCBs?
A: When designing with aluminum PCBs, it is important to consider factors such as thermal management, dielectric layer selection, and the placement of thermal vias. Working with an experienced PCB manufacturer can help ensure optimal design and performance. -
Q: How do I choose the right aluminum PCB manufacturer?
A: When selecting an aluminum PCB manufacturer, look for a company with experience in fabricating aluminum PCBs, strong quality control processes, and reliable technical support. RAYPCB is a trusted manufacturer that offers high-quality aluminum PCB solutions for a wide range of applications.
Conclusion
Aluminum PCBs offer a robust and reliable solution for applications that require efficient thermal management and high durability. By leveraging the superior thermal conductivity and mechanical strength of aluminum, these PCBs can help ensure stable operation and extended lifespan for electronic components.
When designing with aluminum PCBs, it is crucial to consider factors such as thermal management, dielectric layer selection, and manufacturing processes. Working with an experienced PCB manufacturer like RAYPCB can help ensure optimal design and performance for your specific application requirements.
As the demand for high-performance electronics continues to grow, aluminum PCBs are poised to play an increasingly important role in enabling reliable and efficient thermal management solutions across a wide range of industries.
Leave a Reply