Introduction to Aluminum PCBs
Aluminum PCBs, also known as metal core PCBs (MCPCBs), are a type of printed circuit board that utilizes an aluminum substrate instead of the traditional FR-4 material. These PCBs are gaining popularity in various industries due to their excellent thermal management properties, which allow for better heat dissipation and improved performance in high-power applications. In this comprehensive guide, we will delve into the world of aluminum PCBs, exploring their construction, advantages, applications, and much more.
What are Aluminum PCBs?
Aluminum PCBs are printed circuit boards that feature an aluminum substrate as the base material. The aluminum substrate is typically covered with a thin layer of dielectric material, which insulates the copper traces from the metal core. This unique construction allows for efficient heat transfer from the components to the aluminum substrate, making aluminum PCBs ideal for applications that generate significant amounts of heat.
Construction of Aluminum PCBs
The structure of an aluminum PCB consists of several layers:
- Aluminum substrate: The base layer of the PCB, which provides mechanical support and acts as a heat sink.
- Dielectric layer: A thin layer of insulating material that separates the copper traces from the aluminum substrate.
- Copper traces: The conductive pathways that carry electrical signals between components.
- Solder mask: A protective layer that covers the copper traces, leaving only the necessary areas exposed for soldering.
- Silkscreen: A layer of text and symbols that helps identify components and provides assembly instructions.
Layer | Material | Function |
---|---|---|
Aluminum substrate | Aluminum | Provides mechanical support and acts as a heat sink |
Dielectric layer | Insulating material | Separates copper traces from the aluminum substrate |
Copper traces | Copper | Carries electrical signals between components |
Solder mask | Protective material | Covers copper traces, leaving necessary areas exposed for soldering |
Silkscreen | Ink | Identifies components and provides assembly instructions |
Advantages of Aluminum PCBs
Aluminum PCBs offer several advantages over traditional FR-4 PCBs:
Excellent Thermal Management
The primary advantage of aluminum PCBs is their superior thermal management capabilities. The aluminum substrate acts as a built-in heat sink, efficiently transferring heat away from components and distributing it across the entire PCB. This helps to prevent hot spots and ensures that components operate within their specified temperature ranges, leading to improved reliability and longevity.
Lightweight and Durable
Aluminum PCBs are lighter than their FR-4 counterparts, making them suitable for applications where weight is a concern, such as in aerospace and automotive industries. Additionally, aluminum PCBs are more durable and resistant to vibration and mechanical stress, which further enhances their reliability in demanding environments.
Cost-effective for High-power Applications
While aluminum PCBs may have a higher initial cost compared to FR-4 PCBs, they can be more cost-effective in the long run for high-power applications. The improved thermal management properties of aluminum PCBs can help reduce the need for additional heat sinks or cooling solutions, simplifying the overall design and reducing system costs.
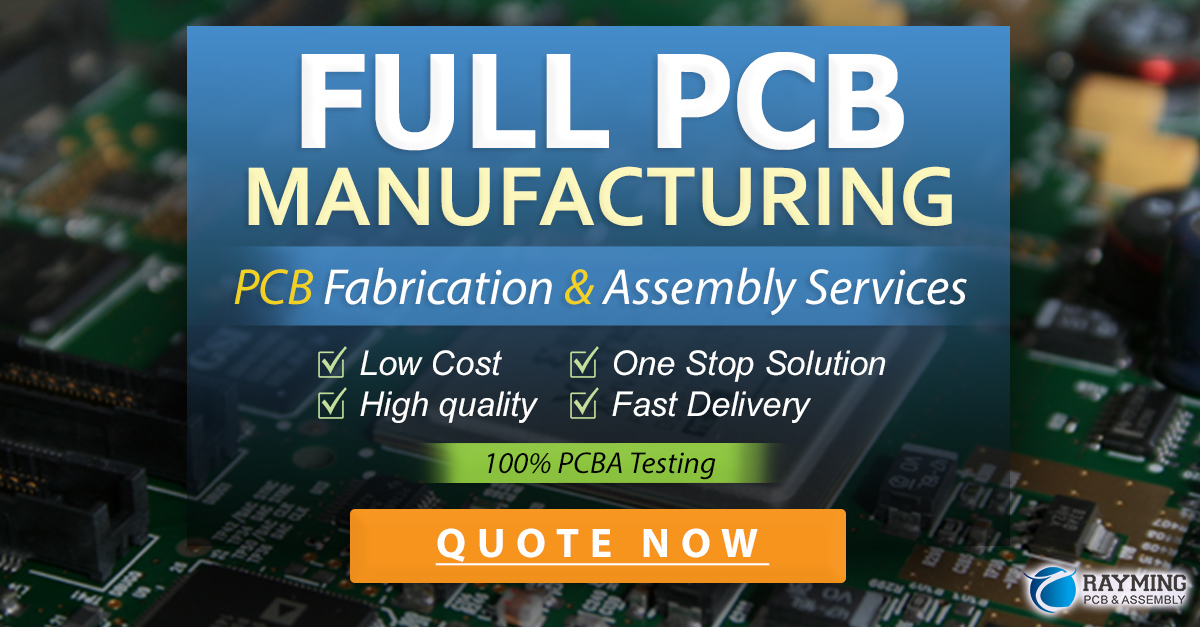
Applications of Aluminum PCBs
Aluminum PCBs find applications in various industries where thermal management and high-power handling are crucial:
-
LED lighting: Aluminum PCBs are widely used in LED lighting applications, as they help dissipate the heat generated by high-power LEDs, ensuring optimal performance and longevity.
-
Automotive electronics: In the automotive industry, aluminum PCBs are used in power inverters, motor controllers, and other high-power electronic systems where reliable thermal management is essential.
-
Power electronics: Aluminum PCBs are ideal for power electronic applications, such as switch-mode power supplies (SMPS), rectifiers, and motor drives, where efficient heat dissipation is critical for reliable operation.
-
Aerospace and defense: In aerospace and defense applications, aluminum PCBs are used in radar systems, avionics, and other high-performance electronic systems that require excellent thermal management and reliability in harsh environments.
-
Industrial automation: Aluminum PCBs are employed in industrial automation systems, such as motor controllers, power supplies, and sensors, where they help ensure reliable operation in demanding industrial environments.
Designing with Aluminum PCBs
When designing with aluminum PCBs, there are several factors to consider:
Thermal Management
To maximize the thermal management benefits of aluminum PCBs, designers should carefully consider component placement and routing. High-power components should be placed close to the aluminum substrate to facilitate efficient heat transfer, while low-power components can be placed farther away. Thermal vias can be used to further enhance heat dissipation by providing a direct thermal path from the components to the aluminum substrate.
Dielectric Material Selection
The choice of dielectric material is crucial in aluminum PCB design. The dielectric layer must provide adequate insulation between the copper traces and the aluminum substrate while also allowing for efficient heat transfer. Common dielectric materials used in aluminum PCBs include:
- Aluminum oxide (Al2O3)
- Boron nitride (BN)
- Aluminum nitride (AlN)
- Epoxy-based dielectrics
Each dielectric material has its own thermal conductivity, dielectric constant, and breakdown voltage, which should be considered when selecting the appropriate material for a specific application.
Coefficient of Thermal Expansion (CTE) Matching
Another important consideration in aluminum PCB design is the matching of the coefficient of thermal expansion (CTE) between the aluminum substrate, dielectric layer, and copper traces. Mismatches in CTE can lead to mechanical stress and potential reliability issues during thermal cycling. To mitigate this, designers can use specialized dielectric materials with CTEs closer to that of aluminum, or they can employ techniques such as oversized via holes and anchoring copper traces to the aluminum substrate.
Manufacturing Process of Aluminum PCBs
The manufacturing process of aluminum PCBs differs slightly from that of traditional FR-4 PCBs:
-
Substrate preparation: The aluminum substrate is cleaned and treated to ensure proper adhesion of the dielectric layer.
-
Dielectric layer application: The chosen dielectric material is applied to the aluminum substrate using techniques such as screen printing, roller coating, or lamination.
-
Copper foil lamination: A thin layer of copper foil is laminated onto the dielectric layer using heat and pressure.
-
Circuit patterning: The desired circuit pattern is created on the copper foil using photolithography and etching processes.
-
Drilling and plating: Holes are drilled through the PCB, and the walls of the holes are plated with copper to create electrical connections between layers.
-
Solder mask application: A solder mask is applied to the PCB to protect the copper traces and prevent short circuits.
-
Surface finish application: A surface finish, such as HASL, ENIG, or OSP, is applied to the exposed copper areas to prevent oxidation and enhance solderability.
-
Silkscreen printing: The silkscreen layer is printed onto the PCB to provide component identification and assembly instructions.
-
Singulation: The individual PCBs are cut from the panel using routing or scoring techniques.
Choosing the Right Aluminum PCB Manufacturer
When selecting an aluminum PCB manufacturer, consider the following factors:
-
Experience and expertise: Choose a manufacturer with extensive experience in fabricating aluminum PCBs and a proven track record of delivering high-quality products.
-
Quality control: Ensure that the manufacturer adheres to strict quality control standards and employs rigorous testing and inspection procedures throughout the manufacturing process.
-
Technical support: Look for a manufacturer that offers comprehensive technical support and can provide guidance on design, material selection, and manufacturing processes.
-
Certifications: Select a manufacturer that holds relevant certifications, such as ISO 9001, UL, and RoHS, to ensure that their products meet industry standards and regulatory requirements.
-
Lead time and pricing: Consider the manufacturer’s lead times and pricing structure to ensure that they align with your project requirements and budget.
Frequently Asked Questions (FAQ)
-
Q: What is the main difference between aluminum PCBs and traditional FR-4 PCBs?
A: The main difference is the substrate material. Aluminum PCBs use an aluminum substrate, which provides excellent thermal conductivity, while FR-4 PCBs use a glass-reinforced epoxy substrate, which has lower thermal conductivity. -
Q: Can aluminum PCBs be used for all types of electronic applications?
A: While aluminum PCBs offer superior thermal management, they may not be suitable for all applications. They are best suited for high-power applications that generate significant amounts of heat, such as LED lighting, power electronics, and automotive electronics. -
Q: Are aluminum PCBs more expensive than FR-4 PCBs?
A: Aluminum PCBs typically have a higher initial cost compared to FR-4 PCBs due to the specialized materials and manufacturing processes involved. However, they can be more cost-effective in the long run for high-power applications, as they can reduce the need for additional cooling solutions. -
Q: What are the key considerations when designing with aluminum PCBs?
A: When designing with aluminum PCBs, key considerations include thermal management, dielectric material selection, and coefficient of thermal expansion (CTE) matching. Proper component placement, routing, and the use of thermal vias can help optimize thermal performance. -
Q: How do I choose the right aluminum PCB manufacturer for my project?
A: When selecting an aluminum PCB manufacturer, consider factors such as experience and expertise, quality control, technical support, certifications, lead time, and pricing. Look for a manufacturer with a proven track record of delivering high-quality aluminum PCBs and comprehensive support throughout the design and manufacturing process.
Conclusion
Aluminum PCBs offer a compelling solution for high-power electronic applications that require efficient thermal management and reliable performance. By leveraging the excellent thermal conductivity of the aluminum substrate, these PCBs can help dissipate heat more effectively, reducing the need for additional cooling solutions and improving overall system reliability.
When designing with aluminum PCBs, it is essential to consider factors such as thermal management, dielectric material selection, and CTE matching to ensure optimal performance and reliability. Choosing the right aluminum PCB manufacturer is also crucial, as it can significantly impact the quality, lead time, and overall success of your project.
As the demand for high-performance electronic systems continues to grow across various industries, aluminum PCBs are poised to play an increasingly important role in enabling the development of reliable, efficient, and cost-effective solutions. By understanding the advantages, applications, and design considerations associated with aluminum PCBs, engineers and designers can make informed decisions when selecting the most appropriate PCB technology for their projects.
Leave a Reply