Introduction to PCB Ensure
Printed Circuit Boards (PCBs) are the backbone of modern electronics. They are used in almost every electronic device, from smartphones and laptops to medical equipment and aerospace systems. As such, ensuring the quality and reliability of PCBs is crucial for the proper functioning and longevity of these devices. PCB Ensure is a comprehensive approach to guaranteeing the quality and reliability of PCBs throughout their lifecycle, from design and manufacturing to assembly and testing.
What is PCB Ensure?
PCB Ensure is a set of best practices, standards, and processes aimed at ensuring the quality and reliability of PCBs. It encompasses various aspects of PCB development, including:
- Design for Manufacturability (DFM)
- Component selection and qualification
- Manufacturing process control
- Assembly and soldering techniques
- Testing and inspection methods
- Handling and storage procedures
By adhering to PCB Ensure guidelines, manufacturers can minimize defects, improve yield, and enhance the overall quality of their PCBs.
The Importance of PCB Ensure
Reliability and Longevity
One of the primary goals of PCB Ensure is to improve the reliability and longevity of PCBs. By following best practices in design, manufacturing, and assembly, PCBs are less likely to experience failures or malfunctions during their intended lifespan. This is particularly important for mission-critical applications, such as medical devices or aerospace systems, where PCB failures can have severe consequences.
Cost Reduction
Implementing PCB Ensure practices can also lead to significant cost savings. By catching potential issues early in the design and manufacturing process, manufacturers can avoid costly rework or scrap. Additionally, by improving yield and reducing defects, manufacturers can optimize their production efficiency and lower their overall costs.
Compliance with Industry Standards
PCB Ensure helps manufacturers comply with various industry standards and regulations, such as IPC (Association Connecting Electronics Industries) standards, RoHS (Restriction of Hazardous Substances), and REACH (Registration, Evaluation, Authorization, and Restriction of Chemicals). By adhering to these standards, manufacturers can ensure that their PCBs meet the necessary quality and safety requirements for their intended applications.
Key Elements of PCB Ensure
Design for Manufacturability (DFM)
DFM is a critical aspect of PCB Ensure, as it focuses on designing PCBs that are easy to manufacture and assemble. This involves considering factors such as:
- Board size and thickness
- Layer count and stack-up
- Trace width and spacing
- Via size and placement
- Component placement and orientation
- Soldermask and silkscreen design
By incorporating DFM principles into the PCB design process, manufacturers can minimize potential manufacturing issues and improve the overall quality of their PCBs.
Component Selection and Qualification
Selecting the right components is crucial for ensuring the reliability and performance of PCBs. PCB Ensure recommends establishing a comprehensive component selection and qualification process that includes:
- Defining component requirements and specifications
- Evaluating potential suppliers and their quality control processes
- Conducting incoming inspection and testing of components
- Monitoring component performance and reliability over time
By carefully selecting and qualifying components, manufacturers can minimize the risk of component-related failures and ensure the overall quality of their PCBs.
Manufacturing Process Control
Controlling the manufacturing process is essential for maintaining the quality and consistency of PCBs. PCB Ensure recommends implementing robust process control measures, such as:
- Establishing and monitoring process parameters (e.g., temperature, pressure, time)
- Implementing statistical process control (SPC) techniques
- Conducting regular audits and inspections of the manufacturing process
- Maintaining proper documentation and traceability of materials and processes
By controlling the manufacturing process, manufacturers can minimize process-related defects and ensure the consistent quality of their PCBs.
Assembly and Soldering Techniques
Proper assembly and soldering techniques are critical for ensuring the reliability and performance of PCBs. PCB Ensure recommends following best practices, such as:
- Using appropriate soldering methods (e.g., wave soldering, reflow soldering, hand soldering)
- Selecting the right solder alloy and flux for the application
- Controlling soldering temperature and time
- Implementing proper cleaning and inspection procedures
By using appropriate assembly and soldering techniques, manufacturers can minimize soldering defects and improve the overall quality of their PCBs.
Testing and Inspection Methods
Testing and inspection are essential for identifying and correcting potential issues before PCBs are shipped to customers. PCB Ensure recommends implementing a comprehensive testing and inspection plan that includes:
- Visual inspection
- Automated Optical Inspection (AOI)
- X-ray inspection
- Electrical testing (e.g., continuity, insulation resistance, high-potential)
- Functional testing
- Environmental testing (e.g., thermal cycling, humidity, vibration)
By conducting thorough testing and inspection, manufacturers can identify and correct potential issues, ensuring the quality and reliability of their PCBs.
Handling and Storage Procedures
Proper handling and storage of PCBs are essential for maintaining their quality and reliability. PCB Ensure recommends following best practices, such as:
- Using appropriate packaging materials (e.g., ESD-safe bags, moisture barrier bags)
- Controlling the storage environment (e.g., temperature, humidity)
- Implementing proper handling procedures (e.g., ESD protection, avoid mechanical damage)
- Establishing shelf-life management and first-in-first-out (FIFO) practices
By following proper handling and storage procedures, manufacturers can minimize the risk of damage or degradation to their PCBs.
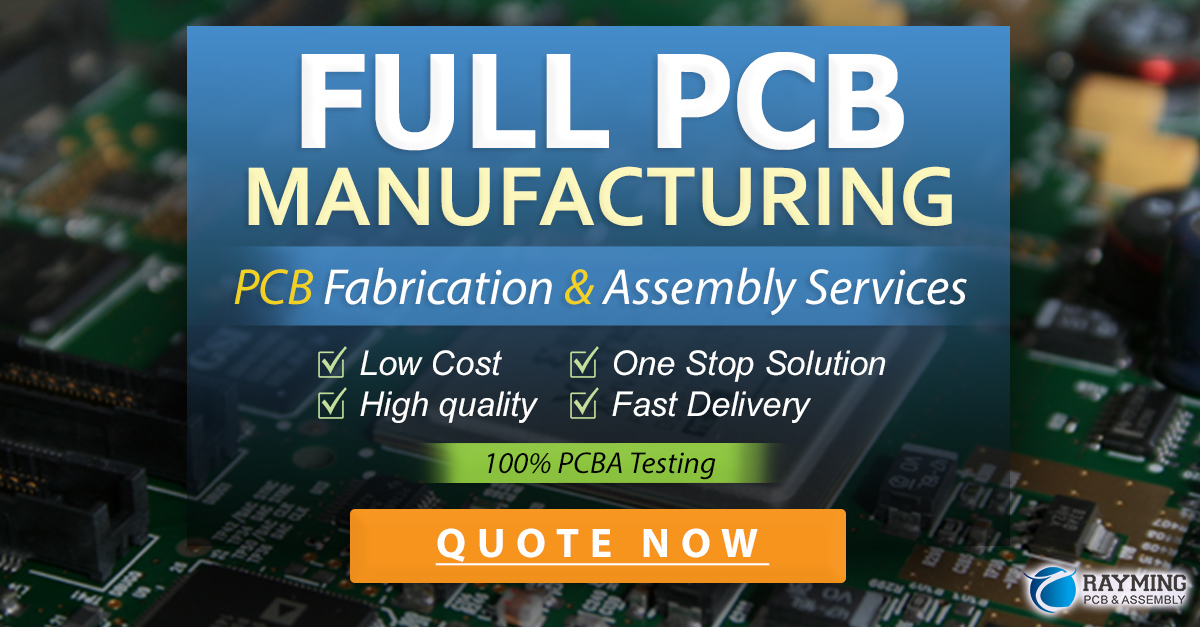
Implementing PCB Ensure
Developing a PCB Ensure Plan
To effectively implement PCB Ensure, manufacturers should develop a comprehensive plan that outlines their specific goals, strategies, and processes. This plan should include:
- Identifying key stakeholders and their roles
- Defining quality and reliability targets
- Establishing design, manufacturing, assembly, and testing procedures
- Implementing training and education programs for employees
- Developing metrics and key performance indicators (KPIs) to measure progress
By developing a PCB Ensure plan, manufacturers can ensure a systematic and organized approach to improving the quality and reliability of their PCBs.
Continuous Improvement
PCB Ensure is not a one-time event but an ongoing process of continuous improvement. Manufacturers should regularly review and update their PCB Ensure practices based on:
- Feedback from customers and stakeholders
- Analysis of quality and reliability data
- Advancements in technology and industry standards
- Changes in market demands and requirements
By continuously improving their PCB Ensure practices, manufacturers can stay ahead of the curve and maintain a competitive edge in the market.
FAQ
-
What is the difference between PCB Ensure and other quality control methods?
PCB Ensure is a comprehensive approach that encompasses all aspects of PCB development, from design to testing. It focuses on preventing issues rather than just detecting them, and it emphasizes continuous improvement based on data analysis and stakeholder feedback. -
How can PCB Ensure help reduce costs?
By catching potential issues early in the design and manufacturing process, PCB Ensure can help avoid costly rework or scrap. Additionally, by improving yield and reducing defects, manufacturers can optimize their production efficiency and lower their overall costs. -
Is PCB Ensure applicable to all types of PCBs?
Yes, PCB Ensure principles can be applied to all types of PCBs, regardless of their complexity or application. However, the specific procedures and requirements may vary depending on the PCB’s intended use and the relevant industry standards. -
How long does it take to implement PCB Ensure?
The time required to implement PCB Ensure varies depending on the size and complexity of the organization, as well as the current state of their quality control processes. However, most manufacturers can expect to see significant improvements within a few months to a year of starting their PCB Ensure journey. -
What are the key benefits of PCB Ensure?
The key benefits of PCB Ensure include improved reliability and longevity of PCBs, reduced costs through defect prevention and yield improvement, and compliance with industry standards and regulations. Additionally, PCB Ensure can help manufacturers differentiate themselves in the market and build stronger relationships with their customers.
Conclusion
PCB Ensure is a critical approach for manufacturers looking to improve the quality, reliability, and cost-effectiveness of their PCBs. By following best practices in design, manufacturing, assembly, and testing, manufacturers can minimize defects, optimize production efficiency, and enhance the overall performance of their products. Implementing PCB Ensure requires a comprehensive plan and a commitment to continuous improvement, but the benefits – including improved customer satisfaction, reduced costs, and compliance with industry standards – make it a worthwhile investment for any PCB manufacturer.
PCB Ensure Element | Key Considerations |
---|---|
Design for Manufacturability (DFM) | – Board size and thickness – Layer count and stack-up – Trace width and spacing – Via size and placement – Component placement and orientation – Soldermask and silkscreen design |
Component Selection and Qualification | – Defining component requirements and specifications – Evaluating potential suppliers and their quality control processes – Conducting incoming inspection and testing of components – Monitoring component performance and reliability over time |
Manufacturing Process Control | – Establishing and monitoring process parameters – Implementing statistical process control (SPC) techniques – Conducting regular audits and inspections of the manufacturing process – Maintaining proper documentation and traceability of materials and processes |
Assembly and Soldering Techniques | – Using appropriate soldering methods – Selecting the right solder alloy and flux for the application – Controlling soldering temperature and time – Implementing proper cleaning and inspection procedures |
Testing and Inspection Methods | – Visual inspection – Automated Optical Inspection (AOI) – X-ray inspection – Electrical testing – Functional testing – Environmental testing |
Handling and Storage Procedures | – Using appropriate packaging materials – Controlling the storage environment – Implementing proper handling procedures – Establishing shelf-life management and first-in-first-out (FIFO) practices |
By addressing each of these key elements, manufacturers can ensure a comprehensive and effective approach to PCB Quality and reliability. With PCB Ensure, manufacturers can deliver high-quality products that meet the evolving needs of their customers and the industry as a whole.
Leave a Reply