What is PCB Quality and Why Does it Matter?
PCB quality refers to how well a printed circuit board is designed and manufactured to meet its intended performance, reliability, and durability requirements. The quality of a PCB directly impacts the functionality, stability, and lifespan of the electronic device it powers.
Poor PCB quality can lead to a range of issues, including:
– Malfunctions and failures of the end product
– Increased manufacturing costs and delays
– Damage to a company’s reputation
– Potential safety hazards for end-users
On the other hand, high-quality PCBs provide numerous benefits:
– Reliable performance of the electronic device
– Longer product lifespan
– Reduced manufacturing costs and time-to-market
– Enhanced company reputation and customer satisfaction
– Compliance with industry standards and regulations
Therefore, prioritizing PCB quality is crucial for any company developing electronic products. It ensures the end product functions as intended, meets customer expectations, and complies with relevant standards.
Factors That Impact PCB Quality
Several key factors influence the quality of a printed circuit board throughout the design and manufacturing process:
1. PCB Design
The PCB design lays the foundation for board quality. A well-designed PCB takes into account:
– Schematic capture and layout
– Component selection and placement
– Signal integrity and electromagnetic compatibility (EMC)
– Thermal management
– Manufacturing considerations (e.g., design for manufacturability)
2. Material Selection
The materials used in PCB fabrication significantly impact quality. Key considerations include:
– Laminate material properties (e.g., FR-4, high-frequency materials)
– Copper foil thickness and quality
– Solder mask and silkscreen ink quality
– Surface finishes (e.g., HASL, ENIG, OSP)
3. Manufacturing Processes
The quality of the manufacturing processes directly affects PCB quality. Critical processes include:
– Etching and plating
– Drilling and routing
– Solder mask application
– Silkscreen printing
– Surface finishing
– Electrical testing and inspection
4. Quality Control and Testing
Rigorous quality control and testing procedures are essential to ensure PCB quality. These include:
– Incoming material inspections
– In-process quality checks
– Automated optical inspection (AOI)
– Flying probe testing
– Functional testing
– Burn-in testing
– Compliance with industry standards (e.g., IPC, MIL-SPEC)
5. Supplier and Manufacturer Selection
Choosing reputable suppliers and manufacturers with a proven track record of producing high-quality PCBs is crucial. Factors to consider:
– Certifications and qualifications (e.g., ISO 9001, UL, IPC)
– Experience and expertise in specific PCB technologies
– Quality management systems and procedures
– Customer support and communication
– Lead times and pricing
Ensuring PCB Quality Through Design Best Practices
Designing a high-quality PCB involves adhering to industry best practices and standards. Some key design considerations include:
1. Schematic Capture and Review
- Create a clear and accurate schematic
- Perform thorough schematic reviews to catch errors early
- Use consistent naming conventions and symbols
- Verify component footprints and pinouts
2. PCB Layout and Routing
- Follow manufacturer’s design rules and guidelines
- Optimize component placement for manufacturability and signal integrity
- Route traces with appropriate width, spacing, and length
- Minimize crosstalk and electromagnetic interference (EMI)
- Implement proper grounding and power distribution
3. Signal Integrity and EMC
- Perform signal integrity simulations to analyze critical signals
- Implement impedance control for high-speed signals
- Use appropriate termination and matching techniques
- Incorporate EMI suppression methods (e.g., shielding, filtering)
- Comply with relevant EMC regulations and standards
4. Thermal Management
- Conduct thermal analysis to identify hot spots
- Provide adequate copper pour for heat dissipation
- Use thermal vias and heat sinks when necessary
- Consider component power ratings and temperature specifications
5. Design for Manufacturability (DFM)
- Adhere to manufacturer’s DFM guidelines
- Use standard component sizes and packages when possible
- Provide adequate spacing and clearances for manufacturing processes
- Incorporate fiducial marks and tooling holes
- Specify appropriate solder mask and silkscreen requirements
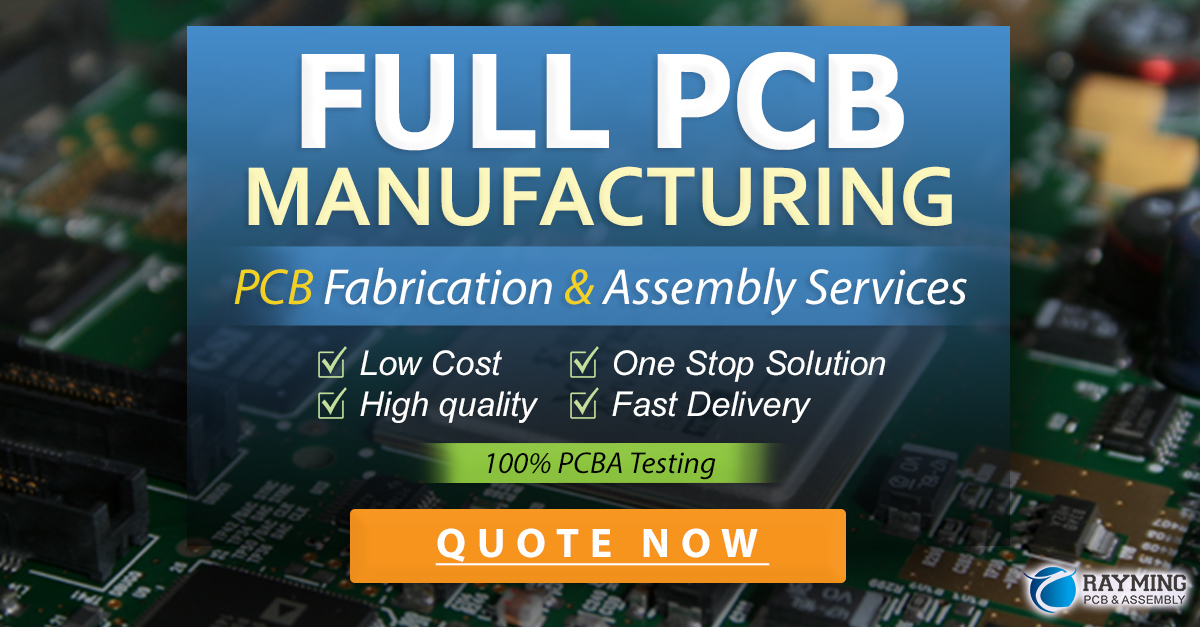
Manufacturing Process Control and Quality Assurance
Maintaining high PCB quality during manufacturing requires strict process control and quality assurance measures.
1. Process Control
- Establish and document standard operating procedures (SOPs)
- Monitor and control critical process parameters (e.g., temperature, pressure, time)
- Perform regular equipment maintenance and calibration
- Implement statistical process control (SPC) techniques
2. Automated Optical Inspection (AOI)
- Use AOI systems to detect surface defects and anomalies
- Develop comprehensive AOI programs and libraries
- Set appropriate defect detection thresholds
- Regularly review and update AOI programs
3. Electrical Testing
- Perform flying probe or bed-of-nails testing for electrical continuity and shorts
- Conduct functional testing to verify PCB performance
- Perform boundary scan testing for complex digital boards
- Implement in-circuit testing (ICT) for analog and mixed-signal boards
4. Quality Assurance and Inspection
- Visually inspect PCBs for defects and workmanship issues
- Perform cross-sectional analysis to verify internal layer integrity
- Conduct solderability testing on surface finishes
- Perform mechanical stress tests (e.g., thermal cycling, vibration)
5. Traceability and Documentation
- Implement a robust traceability system for materials and processes
- Maintain detailed manufacturing and inspection records
- Use unique identifiers (e.g., barcodes, serial numbers) for each PCB
- Provide certificates of conformance (CoCs) and test reports
Industry Standards and Certifications
Adhering to industry standards and obtaining relevant certifications demonstrates a commitment to PCB quality and helps ensure consistency across the supply chain.
1. IPC Standards
- IPC-A-600: Acceptability of Printed Boards
- IPC-6012: Qualification and Performance Specification for Rigid Printed Boards
- IPC-A-610: Acceptability of Electronic Assemblies
- IPC J-STD-001: Requirements for Soldered Electrical and Electronic Assemblies
- IPC-7711/7721: Rework of Electronic Assemblies
2. ISO Standards
- ISO 9001: Quality Management Systems
- ISO 14001: Environmental Management Systems
- ISO 45001: Occupational Health and Safety Management Systems
3. Military and Aerospace Standards
- MIL-PRF-31032: Performance Specification for Printed Circuit Board Assemblies
- MIL-PRF-55110: Printed Wiring Board, Rigid, General Specification For
- AS9100: Quality Management Systems – Requirements for Aviation, Space and Defense Organizations
4. Industry Certifications
- UL (Underwriters Laboratories)
- CSA (Canadian Standards Association)
- TÜV (Technischer Überwachungsverein)
- CQC (China Quality Certification)
Troubleshooting and Failure Analysis
Despite best efforts, PCB quality issues may still arise. Effective troubleshooting and failure analysis techniques help identify root causes and implement corrective actions.
1. Visual and Optical Inspection
- Use microscopes, magnifiers, and digital imaging for detailed visual inspection
- Identify surface defects, such as cracks, delamination, and contamination
- Check for proper component placement and orientation
- Verify solder joint quality and appearance
2. Electrical Testing and Measurement
- Use multimeters, oscilloscopes, and logic analyzers to measure electrical parameters
- Perform continuity and resistance tests to detect open or short circuits
- Measure voltage levels and waveforms to identify signal integrity issues
- Conduct current measurements to detect overcurrent conditions or short circuits
3. Non-Destructive Testing (NDT)
- Utilize X-ray inspection to examine internal structures and solder joints
- Perform acoustic microscopy to detect delamination and voids
- Use thermography to identify hot spots and thermal dissipation issues
- Employ 3D computed tomography (CT) scanning for detailed internal analysis
4. Destructive Physical Analysis (DPA)
- Perform cross-sectional analysis to examine internal layers and plated through-holes
- Use chemical etching or grinding to expose internal structures
- Conduct scanning electron microscopy (SEM) for high-magnification imaging
- Perform energy-dispersive X-ray spectroscopy (EDS) for elemental analysis
5. Root Cause Analysis and Corrective Action
- Gather and analyze data from inspection and testing results
- Use problem-solving techniques (e.g., 5 Whys, Ishikawa diagrams) to identify root causes
- Develop and implement corrective action plans to address quality issues
- Monitor the effectiveness of corrective actions through continued inspection and testing
Continuous Improvement and Supplier Management
Continuously improving PCB quality and managing supplier relationships are essential for long-term success.
1. Quality Management Systems (QMS)
- Implement a robust QMS based on industry standards (e.g., ISO 9001)
- Establish quality objectives, policies, and procedures
- Conduct regular internal audits and management reviews
- Encourage employee training and engagement in quality improvement initiatives
2. Statistical Process Control (SPC)
- Collect and analyze process data to monitor performance and identify trends
- Use control charts to detect process variations and anomalies
- Implement corrective and preventive actions based on SPC data
- Continuously update and refine process parameters and control limits
3. Supplier Qualification and Evaluation
- Establish clear supplier selection criteria based on quality, delivery, and cost
- Conduct on-site audits and assessments of supplier facilities and processes
- Review supplier certifications, test reports, and quality records
- Implement a supplier scorecard system to track performance and identify improvement areas
4. Communication and Collaboration
- Foster open and transparent communication with suppliers
- Share quality requirements, expectations, and feedback regularly
- Collaborate on problem-solving and continuous improvement initiatives
- Conduct joint quality planning and review meetings
5. Supplier Development and Partnerships
- Provide technical support and training to help suppliers improve their processes
- Share best practices and lessons learned across the supply chain
- Develop long-term partnerships with key suppliers
- Engage suppliers in early product development and design for manufacturability efforts
FAQ
-
What is the difference between a high-quality and low-quality PCB?
A high-quality PCB is designed and manufactured to meet or exceed industry standards and customer requirements. It exhibits excellent performance, reliability, and durability. In contrast, a low-quality PCB may have design flaws, manufacturing defects, or substandard materials, leading to poor performance, malfunctions, or premature failure. -
How can I ensure the quality of the PCBs I purchase?
To ensure PCB quality, work with reputable suppliers and manufacturers that have a proven track record of producing high-quality boards. Request certifications, test reports, and quality documentation. Specify your quality requirements clearly and conduct incoming inspections to verify the quality of received PCBs. -
What are the most common PCB quality issues?
Common PCB quality issues include: - Manufacturing defects (e.g., shorts, opens, misalignments)
- Solder joint quality issues (e.g., cold joints, bridging, insufficient solder)
- Laminate defects (e.g., delamination, cracks, voids)
- Plating issues (e.g., insufficient plating, voids, nodules)
- Component placement and orientation errors
-
Signal integrity and EMI problems
-
How can I troubleshoot PCB quality issues?
To troubleshoot PCB quality issues: - Perform visual and optical inspections to identify surface defects and anomalies.
- Conduct electrical tests to detect continuity, shorts, and signal integrity problems.
- Use non-destructive testing methods (e.g., X-ray, acoustic microscopy, thermography) for internal analysis.
- Perform destructive physical analysis (e.g., cross-sectioning, SEM) for detailed examination.
-
Analyze the data and use problem-solving techniques to identify root causes and develop corrective actions.
-
What industry standards should I follow for PCB quality?
Key industry standards for PCB quality include: - IPC-A-600: Acceptability of Printed Boards
- IPC-6012: Qualification and Performance Specification for Rigid Printed Boards
- IPC-A-610: Acceptability of Electronic Assemblies
- IPC J-STD-001: Requirements for Soldered Electrical and Electronic Assemblies
- IPC-7711/7721: Rework of Electronic Assemblies
- MIL-PRF-31032: Performance Specification for Printed Circuit Board Assemblies
- AS9100: Quality Management Systems – Requirements for Aviation, Space and Defense Organizations
Factor | Impact on PCB Quality |
---|---|
PCB Design | A well-designed PCB considers schematic capture, layout, component selection, signal integrity, thermal management, and manufacturability. |
Material Selection | The choice of laminate materials, copper foil, solder mask, and surface finishes directly affects PCB performance and reliability. |
Manufacturing Processes | The quality of etching, plating, drilling, routing, and other manufacturing processes determines the physical integrity and functionality of the PCB. |
Quality Control and Testing | Rigorous quality control measures, such as AOI, electrical testing, and inspections, help identify and eliminate defects and ensure compliance with industry standards. |
Supplier and Manufacturer | Selecting reputable suppliers and manufacturers with proven quality management systems and certifications is crucial for obtaining high-quality PCBs consistently. |
This comprehensive guide covers the essential aspects of PCB quality, from design and manufacturing to testing, troubleshooting, and continuous improvement. By understanding and implementing these best practices, companies can ensure the production of high-quality PCBs that meet performance, reliability, and regulatory requirements, ultimately contributing to the success of their electronic products.
Leave a Reply