Overview of the PCBA Manufacturing Process
The PCBA manufacturing process can be broken down into the following main steps:
- PCB Design and Fabrication
- SMT (Surface Mount Technology) Assembly
- THT (Through-Hole Technology) Assembly
- Inspection and Testing
- Conformal Coating and Potting
- Final Assembly and Packaging
Each of these steps plays a crucial role in ensuring the quality, reliability, and functionality of the final product. Let’s explore each step in more detail.
PCB Design and Fabrication
The PCBA manufacturing process begins with the design and fabrication of the PCB (Printed Circuit Board). This step involves several sub-steps:
PCB Design
The PCB design process starts with creating a schematic diagram of the electronic circuit. This diagram shows the various components and their interconnections. Next, a layout designer uses specialized software to create a physical layout of the PCB, determining the placement of components and routing of traces.
PCB Fabrication
Once the PCB design is finalized, the fabrication process begins. This involves the following sub-steps:
-
Substrate Preparation: The PCB substrate, typically made of FR-4 (a glass-reinforced epoxy laminate), is cleaned and prepared for the subsequent steps.
-
Copper Cladding: A thin layer of copper is laminated onto the substrate using heat and pressure.
-
Drilling: Holes are drilled into the PCB to accommodate through-hole components and vias (vertical interconnect access).
-
Patterning: The desired circuit pattern is transferred onto the copper layer using photolithography. This involves applying a photoresist coating, exposing it to UV light through a photomask, and developing the resist to remove the unexposed areas.
-
Etching: The exposed copper is etched away using a chemical solution, leaving behind the desired circuit pattern.
-
Plating: The holes and exposed copper traces are plated with a thin layer of copper, followed by a layer of tin-lead (SnPb) or lead-free (ENIG, OSP) surface finish to protect the copper and enhance solderability.
-
Solder Mask Application: A green or other colored solder mask is applied to the PCB, covering the areas where soldering is not required. This helps to prevent short circuits and improves the PCB’s appearance.
-
Silkscreen Printing: White silkscreen ink is used to print component identifiers, logos, and other markings on the PCB.
-
Surface Finish: The exposed copper pads are coated with a surface finish, such as HASL (Hot Air Solder Leveling), ENIG (Electroless Nickel Immersion Gold), or OSP (Organic Solderability Preservative), to protect the copper from oxidation and enhance solderability.
PCB Fabrication Process
Step | Description |
---|---|
1 | Substrate Preparation |
2 | Copper Cladding |
3 | Drilling |
4 | Patterning |
5 | Etching |
6 | Plating |
7 | Solder Mask Application |
8 | Silkscreen Printing |
9 | Surface Finish |
SMT (Surface Mount Technology) Assembly
SMT assembly is the process of mounting surface mount devices (SMDs) onto the PCB. This process involves several steps:
Solder Paste Printing
Solder paste, a mixture of tiny solder spheres and flux, is applied onto the PCB pads using a stencil printer. The stencil has openings that correspond to the PCB pads, allowing the solder paste to be deposited precisely.
Component Placement
SMDs are placed onto the solder paste-coated pads using an automated Pick-and-Place machine. These machines use vacuum nozzles to pick up components from reels or trays and place them accurately on the PCB.
Reflow Soldering
The PCB with the placed components is passed through a reflow oven. The oven heats the PCB in a controlled manner, causing the solder paste to melt and form a permanent bond between the components and the PCB pads. The temperature profile of the reflow process is carefully controlled to ensure proper solder joint formation and to prevent damage to the components.
Inspection
After reflow soldering, the PCB undergoes visual inspection to check for any defects, such as missing components, misaligned components, or solder bridges. Automated optical inspection (AOI) systems are often used to perform this task quickly and accurately.
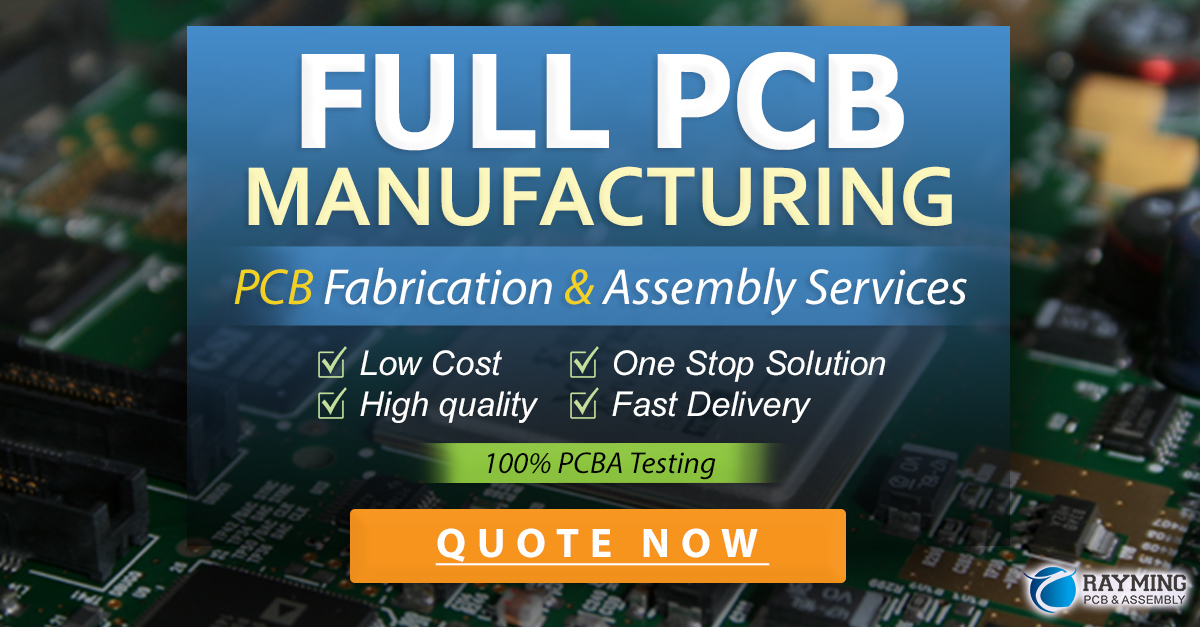
THT (Through-Hole Technology) Assembly
THT assembly involves inserting leads of through-hole components into the drilled holes of the PCB and soldering them in place. This process is typically performed after SMT assembly and involves the following steps:
Component Insertion
Through-hole components are manually inserted into the corresponding holes on the PCB. This process can also be automated using specialized insertion machines for high-volume production.
Wave Soldering
The PCB is passed over a molten solder wave, which selectively solders the component leads to the PCB pads. The solder wave is created by pumping molten solder through a nozzle, forming a standing wave. As the PCB moves over the wave, the solder wets the component leads and the PCB pads, creating a strong mechanical and electrical bond.
Inspection
After wave soldering, the PCB undergoes visual inspection to check for any defects, such as poor solder joints, bridging, or missing components.
Inspection and Testing
Throughout the PCBA manufacturing process, various inspection and testing methods are employed to ensure the quality and functionality of the assembLED PCB. Some of these methods include:
Automated Optical Inspection (AOI)
AOI systems use high-resolution cameras and advanced image processing algorithms to detect surface-level defects, such as missing components, misaligned components, or solder bridges.
X-Ray Inspection
X-ray inspection is used to detect hidden defects, such as voids in solder joints, which cannot be detected by visual inspection methods.
In-Circuit Testing (ICT)
ICT involves using a bed-of-nails fixture to make electrical contact with specific points on the PCB. This allows for testing the PCB’s functionality, component values, and circuit continuity.
Functional Testing
Functional testing involves powering up the assembled PCB and testing its functionality under real-world operating conditions. This helps to ensure that the PCB performs as intended and meets the specified requirements.
Conformal Coating and Potting
In some cases, the assembled PCB may require additional protection against environmental factors, such as moisture, dust, or chemical exposure. This is achieved through conformal coating or potting.
Conformal Coating
Conformal coating involves applying a thin layer of protective material, such as acrylic, silicone, or urethane, over the assembled PCB. This coating helps to protect the PCB from moisture, dust, and other contaminants, while also providing electrical insulation.
Potting
Potting involves encapsulating the assembled PCB in a protective compound, such as epoxy or silicone. This provides a higher level of protection than conformal coating and is often used in harsh environmental conditions or for high-reliability applications.
Final Assembly and Packaging
Once the PCBA is complete, it undergoes final assembly and packaging. This may involve:
- Mounting the PCBA into an enclosure or housing
- Connecting the PCBA to other sub-assemblies or components
- Attaching connectors, cables, or other interfaces
- Applying labels, barcodes, or other identifying marks
- Packaging the final product for shipment or storage
Frequently Asked Questions (FAQ)
- What is the difference between PCB and PCBA?
-
A PCB (Printed Circuit Board) is the bare board without any components mounted on it. A PCBA (Printed Circuit Board Assembly) is a PCB with electronic components soldered onto it, making it a functional electronic assembly.
-
What are the advantages of SMT over THT?
-
SMT (Surface Mount Technology) offers several advantages over THT (Through-Hole Technology), including smaller component sizes, higher component density, better performance at high frequencies, and faster assembly speeds. SMT also allows for automated assembly processes, reducing manual labor and improving consistency.
-
What is the purpose of solder paste in SMT assembly?
-
Solder paste, a mixture of tiny solder spheres and flux, is used in SMT assembly to temporarily hold the components in place on the PCB pads before reflow soldering. During the reflow process, the solder paste melts and forms a permanent electrical and mechanical bond between the components and the PCB.
-
What is the role of a reflow oven in SMT assembly?
-
A reflow oven is used in SMT assembly to melt the solder paste and form a permanent bond between the surface mount components and the PCB pads. The oven heats the PCB in a controlled manner, following a specific temperature profile to ensure proper solder joint formation without damaging the components.
-
What are some common inspection methods used in PCBA manufacturing?
- Some common inspection methods used in PCBA manufacturing include Automated Optical Inspection (AOI), X-Ray Inspection, In-Circuit Testing (ICT), and Functional Testing. These methods help to detect defects, ensure the functionality of the assembled PCB, and maintain the overall quality of the final product.
Conclusion
The PCBA manufacturing process is a complex and multi-step process that requires precision, attention to detail, and adherence to strict quality standards. From PCB design and fabrication to SMT and THT assembly, inspection and testing, and final assembly and packaging, each step plays a crucial role in creating a functional and reliable electronic product.
By understanding the various steps and techniques involved in PCBA manufacturing, engineers, designers, and manufacturers can make informed decisions, optimize their processes, and ensure the production of high-quality electronic assemblies.
Leave a Reply