Understanding High Current PCB Applications
High current PCBs find applications in various industries, including:
- Power electronics
- Automotive systems
- Industrial automation
- Telecommunications
- Aerospace and defense
These applications often involve high power consumption, requiring the PCB to handle substantial currents without compromising performance or reliability. Some examples of high current PCB applications include:
- Motor drives
- Power inverters
- Battery management systems
- Switching mode power supplies
- High-power LED lighting
Key Considerations for High Current PCB Design
Conductor Sizing and Thickness
One of the most critical aspects of high current PCB design is determining the appropriate conductor width and thickness. The cross-sectional area of the conductor directly affects its current-carrying capacity and resistance. Inadequate conductor sizing can lead to excessive heat generation, voltage drop, and potential failure.
To calculate the required conductor width, designers can use the following formula:
W = (I × ρ × L) / (ΔT × t × k)
Where:
– W = Conductor width (mils)
– I = Current (A)
– ρ = Resistivity of the conductor material (Ω·mil)
– L = Length of the conductor (mils)
– ΔT = Temperature rise above ambient (°C)
– t = Conductor thickness (mils)
– k = Thermal conductivity of the PCB material (W/m·K)
The following table provides a quick reference for the current-carrying capacity of copper conductors based on their width and thickness:
Copper Thickness (oz) | Trace Width (mils) | Current Capacity (A) |
---|---|---|
1 | 10 | 1.5 |
1 | 20 | 3.0 |
1 | 50 | 7.5 |
2 | 10 | 3.0 |
2 | 20 | 6.0 |
2 | 50 | 15.0 |
Thermal Management
Effective thermal management is crucial in high current PCB design to prevent overheating and ensure reliable operation. Heat generated by components and conductors must be efficiently dissipated to maintain acceptable operating temperatures. Some thermal management techniques include:
- Using wide, thick conductors to minimize resistance and heat generation.
- Implementing thermal relief pads for components to improve heat dissipation.
- Incorporating thermal vias to transfer heat from inner layers to outer layers and heatsinks.
- Using high thermal conductivity PCB materials, such as Metal Core PCBs or insulated metal substrates (IMS).
- Designing adequate spacing between components and conductors to facilitate air flow and heat dissipation.
Layer Stack-up and Insulation
The layer stack-up of a high current PCB plays a vital role in its performance and reliability. Proper layer arrangement and insulation help minimize electromagnetic interference (EMI), reduce crosstalk, and improve signal integrity. Some best practices for layer stack-up design include:
- Using dedicated power and ground planes to provide low-impedance power distribution and minimize voltage drop.
- Separating sensitive signals from high current traces to reduce electromagnetic interference.
- Implementing appropriate insulation between layers to prevent electrical shorts and maintain signal integrity.
- Using higher dielectric constant materials for improved insulation and reduced layer count.
Component Selection
Selecting the right components is essential for high current PCB design. Components must be rated for the expected current levels and have appropriate package sizes and thermal characteristics. Some factors to consider when selecting components include:
- Current rating: Ensure components can handle the required current without overheating or failing.
- Package size: Choose components with packages that provide adequate heat dissipation and current handling capabilities.
- Thermal resistance: Opt for components with low thermal resistance to minimize heat generation and improve overall thermal performance.
- Voltage rating: Select components with voltage ratings suitable for the application to prevent breakdown or failure.
Layout Techniques
Proper layout techniques are critical for optimizing the performance and reliability of high current PCBs. Some essential layout considerations include:
- Minimizing conductor lengths to reduce resistance and voltage drop.
- Avoiding sharp corners and abrupt changes in conductor width to prevent current crowding and heat concentration.
- Providing adequate clearance between components and conductors to facilitate heat dissipation and prevent electrical shorts.
- Using Kelvin Connections for accurate current sensing and measurement.
- Implementing proper grounding techniques to minimize ground loops and reduce electromagnetic interference.
Simulations and Analysis
Before fabricating a high current PCB, it is essential to perform simulations and analyses to validate the design and identify potential issues. Some common simulation and analysis techniques include:
- DC Voltage drop analysis: Ensures that the voltage drop across conductors is within acceptable limits.
- Thermal analysis: Predicts the temperature distribution across the PCB and identifies hot spots that may require additional cooling.
- Current density analysis: Verifies that the current density in conductors is within safe limits to prevent excessive heating and potential failure.
- Signal integrity analysis: Evaluates the quality of signal transmission and identifies potential issues such as crosstalk, reflections, and EMI.
By performing these simulations and analyses, designers can optimize the PCB layout, component placement, and conductor sizing to ensure optimal performance and reliability.
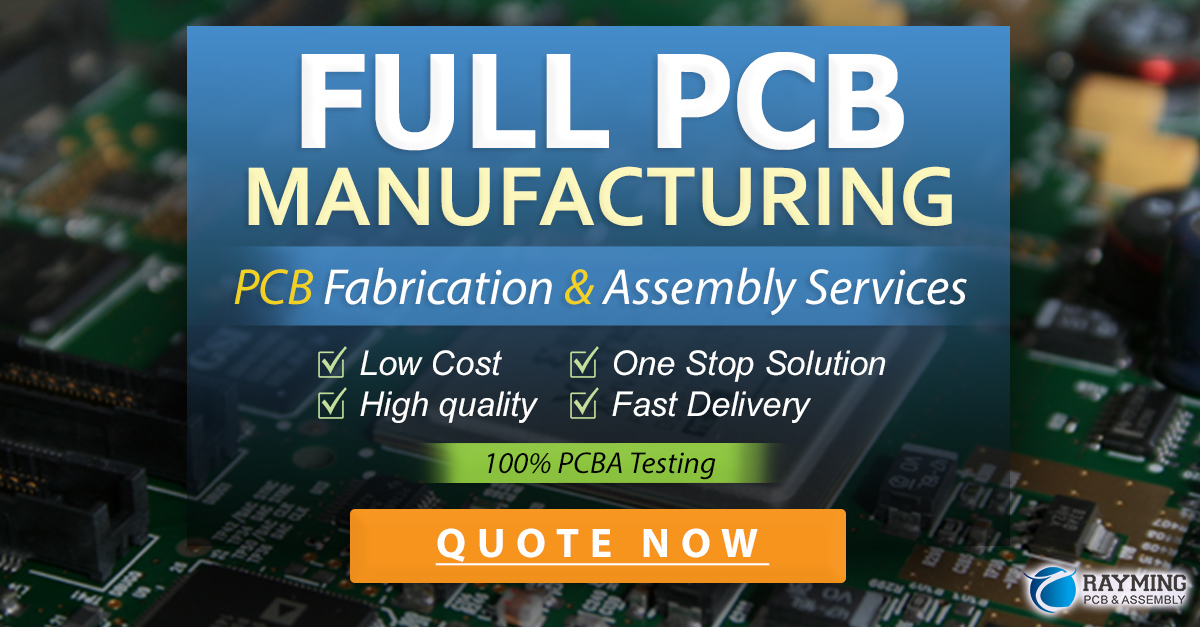
Manufacturing Considerations
When manufacturing high current PCBs, it is crucial to work with experienced and reputable PCB fabricators who have the necessary capabilities and expertise. Some manufacturing considerations include:
- Copper thickness: Ensure that the PCB fabricator can provide the required copper thickness for high current conductors.
- Plating: Specify appropriate plating options, such as heavy copper or silver plating, to improve conductivity and heat dissipation.
- Solder mask: Choose a solder mask with good thermal and electrical properties to protect the PCB and prevent short circuits.
- Inspection and testing: Request rigorous inspection and testing procedures to ensure the PCB meets the required specifications and quality standards.
Frequently Asked Questions (FAQ)
-
What is the difference between high current and high voltage PCBs?
High current PCBs are designed to handle large amounts of current, typically in the range of several amperes to hundreds of amperes. In contrast, high voltage PCBs are designed to withstand high voltages, often exceeding several kilovolts. While some applications may require both high current and high voltage handling, the design considerations for each type of PCB are different. -
How do I determine the appropriate conductor width for my high current PCB?
To determine the appropriate conductor width, you need to consider factors such as the required current, conductor length, temperature rise, and PCB material properties. You can use the formula provided in the “Conductor Sizing and Thickness” section of this article to calculate the minimum conductor width based on these parameters. Additionally, referring to the current-carrying capacity table can provide a quick reference for common conductor sizes. -
What are some effective thermal management techniques for high current PCBs?
Effective thermal management techniques for high current PCBs include using wide and thick conductors, implementing thermal relief pads for components, incorporating thermal vias, using high thermal conductivity PCB materials, and designing adequate spacing between components and conductors. These techniques help dissipate heat generated by components and conductors, preventing overheating and ensuring reliable operation. -
Why is layer stack-up important in high current PCB design?
Layer stack-up is important in high current PCB design because it affects the PCB’s performance and reliability. Proper layer arrangement and insulation help minimize electromagnetic interference (EMI), reduce crosstalk, and improve signal integrity. Using dedicated power and ground planes, separating sensitive signals from high current traces, and implementing appropriate insulation between layers are some best practices for layer stack-up design. -
What simulations and analyses should I perform before fabricating a high current PCB?
Before fabricating a high current PCB, it is recommended to perform simulations and analyses such as DC voltage drop analysis, thermal analysis, current density analysis, and signal integrity analysis. These simulations help validate the design, identify potential issues, and optimize the PCB layout, component placement, and conductor sizing for optimal performance and reliability.
Conclusion
Designing high current PCBs requires careful consideration of various factors, including conductor sizing, thermal management, layer stack-up, component selection, and layout techniques. By understanding the key principles and best practices outlined in this article, designers can create robust and reliable PCBs that can handle high currents without compromising performance or safety.
Effective thermal management, proper layer stack-up, and appropriate component selection are crucial for ensuring the long-term reliability of high current PCBs. Conducting simulations and analyses before fabrication helps validate the design and identify potential issues, saving time and resources in the long run.
When manufacturing high current PCBs, it is essential to work with experienced and reputable PCB fabricators who have the necessary capabilities and expertise to meet the specific requirements of the application. Proper communication and collaboration between the design team and the fabricator can help ensure a successful outcome.
As the demand for high current PCBs continues to grow across various industries, staying up-to-date with the latest design techniques, materials, and manufacturing processes is crucial for designers and engineers. By continuously improving and refining high current PCB design practices, we can push the boundaries of power electronics and enable new and innovative applications in the future.
Leave a Reply