Introduction to Ceramic PCB
Ceramic printed circuit boards (PCBs) are a type of specialized PCB that uses a ceramic substrate material instead of the more common FR-4 fiberglass. Ceramic PCBs offer several advantages over traditional PCBs, including superior thermal conductivity, lower dielectric loss, and higher reliability in harsh environments. These properties make ceramic PCBs ideal for high-frequency, high-power, and high-temperature applications in industries such as aerospace, defense, and telecommunications.
In this comprehensive article, we will delve into the world of ceramic PCBs, exploring their construction, benefits, applications, and manufacturing process. We will also compare ceramic PCBs with other types of PCBs and discuss the factors to consider when choosing a ceramic PCB for your project.
What is a Ceramic PCB?
A ceramic PCB is a printed circuit board that uses a ceramic material, such as alumina (Al2O3) or aluminum nitride (AlN), as the substrate instead of the more common FR-4 fiberglass. The ceramic substrate is an inorganic, non-metallic material that exhibits excellent electrical insulation properties, high thermal conductivity, and low dielectric loss.
Ceramic PCBs are typically composed of multiple layers of ceramic substrates bonded together with conductive traces, vias, and pads made of metals such as copper, gold, or silver. The number of layers in a ceramic PCB can vary depending on the complexity of the circuit design and the application requirements.
Advantages of Ceramic PCBs
Ceramic PCBs offer several advantages over traditional FR-4 PCBs:
-
Superior thermal conductivity: Ceramic materials have higher thermal conductivity than FR-4, allowing for better heat dissipation and improved thermal management in high-power applications.
-
Lower dielectric loss: Ceramic substrates have lower dielectric loss than FR-4, making them suitable for high-frequency applications where signal integrity is critical.
-
Higher reliability: Ceramic PCBs are more resistant to moisture, chemicals, and extreme temperatures, making them more reliable in harsh environments.
-
Dimensional stability: Ceramic materials have a lower coefficient of thermal expansion (CTE) than FR-4, resulting in better dimensional stability over a wide temperature range.
-
Improved mechanical strength: Ceramic substrates are harder and more rigid than FR-4, providing better mechanical stability and durability.
Disadvantages of Ceramic PCBs
Despite their numerous benefits, ceramic PCBs also have some disadvantages:
-
Higher cost: Ceramic PCBs are generally more expensive than FR-4 PCBs due to the higher cost of ceramic materials and the specialized manufacturing processes required.
-
Limited flexibility: Ceramic substrates are brittle and have limited flexibility compared to FR-4, making them less suitable for applications that require bendable or flexible PCBs.
-
Longer lead times: The manufacturing process for ceramic PCBs is more complex and time-consuming than that of FR-4 PCBs, resulting in longer lead times.
-
Limited availability: Not all PCB manufacturers offer ceramic PCB Fabrication services, which can limit the availability and sourcing options for designers and engineers.
Construction of Ceramic PCBs
Ceramic PCBs are constructed using a multi-layer process that involves bonding ceramic substrates together with conductive traces, vias, and pads. The most common ceramic materials used in PCB fabrication are alumina (Al2O3) and aluminum nitride (AlN).
Alumina (Al2O3)
Alumina is the most widely used ceramic material in PCB fabrication due to its excellent electrical insulation properties, high thermal conductivity, and good mechanical strength. Alumina has a dielectric constant of approximately 9.8 and a thermal conductivity of 20-30 W/mK, making it suitable for a wide range of high-frequency and high-power applications.
Aluminum Nitride (AlN)
Aluminum nitride is another popular ceramic material used in PCB fabrication, particularly for applications that require even higher thermal conductivity than alumina. AlN has a thermal conductivity of 170-200 W/mK, which is several times higher than that of alumina. However, AlN is more expensive than alumina and has a slightly lower dielectric constant of 8.8.
Conductive Materials
The conductive traces, vias, and pads in ceramic PCBs are typically made of metals such as copper, gold, or silver. Copper is the most common choice due to its excellent electrical conductivity, low cost, and ease of processing. Gold and silver are used in applications that require higher conductivity, better corrosion resistance, or improved wire bonding capabilities.
Layer Stackup
Ceramic PCBs can have multiple layers of ceramic substrates bonded together to form a complex circuit design. The number of layers in a ceramic PCB can vary depending on the application requirements, but typically ranges from 2 to 20 layers. The layer stackup of a ceramic PCB consists of alternating layers of ceramic substrates and conductive traces, with vias connecting the different layers.
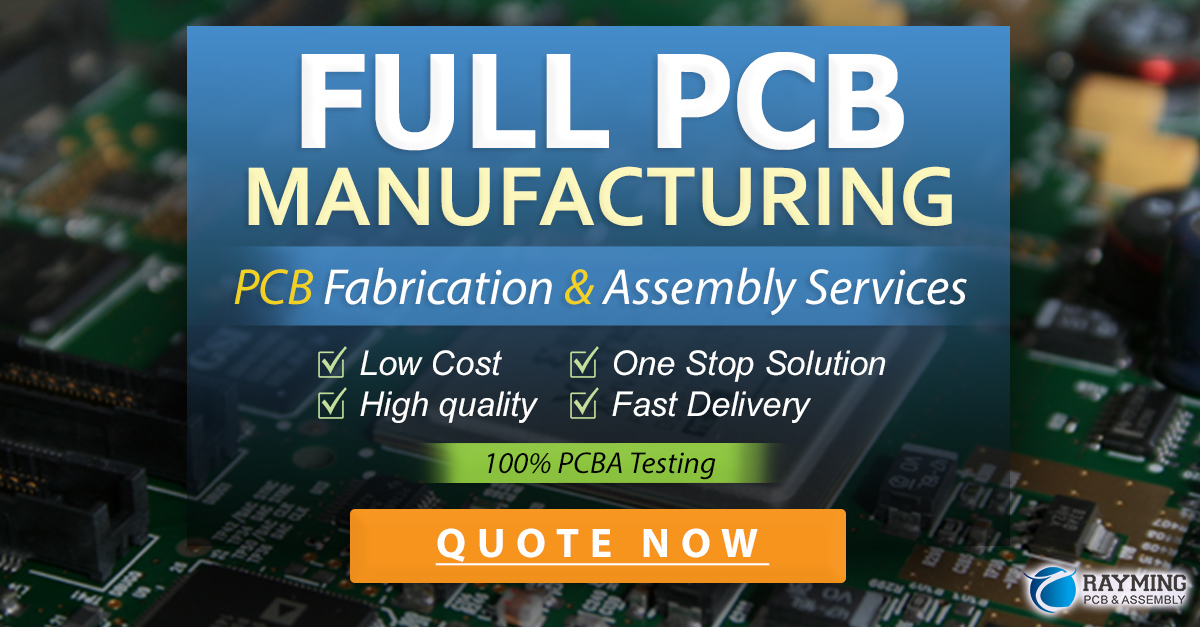
Applications of Ceramic PCBs
Ceramic PCBs are used in a wide range of industries and applications that require high performance, reliability, and durability. Some of the most common applications of ceramic PCBs include:
Aerospace and Defense
Ceramic PCBs are widely used in aerospace and defense applications due to their ability to withstand extreme temperatures, vibrations, and shock. They are used in radar systems, satellite communications, avionics, and missile guidance systems.
High-Frequency and RF Applications
Ceramic PCBs are ideal for high-frequency and RF applications due to their low dielectric loss and excellent signal integrity properties. They are used in telecommunications equipment, wireless base stations, and microwave devices.
Power Electronics
Ceramic PCBs are used in power electronics applications that require high thermal conductivity and efficient heat dissipation. They are used in motor drives, power converters, and high-power LED lighting systems.
Automotive Electronics
Ceramic PCBs are used in automotive electronics applications that require high reliability and durability in harsh environments. They are used in engine control units, transmission control modules, and hybrid electric vehicle power systems.
Medical Devices
Ceramic PCBs are used in medical devices that require high reliability and biocompatibility. They are used in implantable devices, medical imaging equipment, and surgical instruments.
Manufacturing Process of Ceramic PCBs
The manufacturing process of ceramic PCBs is more complex and specialized than that of traditional FR-4 PCBs. The process involves several steps, including:
-
Substrate Preparation: The ceramic substrates are cut to the desired size and shape, and any necessary holes or cavities are drilled or punched.
-
Metallization: The conductive traces, vias, and pads are deposited onto the ceramic substrates using thin-film or thick-film metallization techniques, such as screen printing, sputtering, or plating.
-
Layup and Lamination: The metallized ceramic substrates are stacked and aligned according to the circuit design, and then laminated together under high pressure and temperature to form a solid board.
-
Drilling and Cutting: Any necessary through-holes or cutouts are drilled or machined into the laminated board.
-
Surface Finishing: The exposed metal surfaces are finished with a protective coating, such as nickel/gold plating or solder mask, to improve solderability and prevent oxidation.
-
Inspection and Testing: The finished ceramic PCBs are inspected for defects and tested for electrical and mechanical performance to ensure they meet the required specifications.
Comparison of Ceramic PCBs with Other Types of PCBs
Ceramic PCBs offer unique benefits compared to other types of PCBs, such as FR-4, polyimide, and Metal-Core PCBs. The following table compares the key properties of these different PCB Types:
Property | Ceramic PCB | FR-4 PCB | Polyimide PCB | Metal-Core PCB |
---|---|---|---|---|
Thermal Conductivity | High | Low | Low | High |
Dielectric Loss | Low | Moderate | Low | N/A |
Temperature Resistance | High | Moderate | High | High |
Mechanical Strength | High | Moderate | High | High |
Flexibility | Low | Moderate | High | Low |
Cost | High | Low | Moderate | Moderate |
As shown in the table, ceramic PCBs excel in thermal conductivity, dielectric loss, temperature resistance, and mechanical strength, but are more expensive and less flexible than other PCB types. FR-4 PCBs are the most common and economical choice for general-purpose applications, while polyimide PCBs offer high flexibility and temperature resistance for specialized applications. Metal-Core PCBs provide high thermal conductivity for power electronics applications but do not have dielectric properties.
Factors to Consider When Choosing a Ceramic PCB
When choosing a ceramic PCB for your application, there are several factors to consider:
-
Electrical Requirements: Consider the frequency, power, and signal integrity requirements of your application and choose a ceramic material with the appropriate dielectric constant and loss tangent.
-
Thermal Requirements: Consider the heat generation and dissipation requirements of your application and choose a ceramic material with the appropriate thermal conductivity.
-
Mechanical Requirements: Consider the mechanical stress, vibration, and shock requirements of your application and choose a ceramic material with the appropriate mechanical strength and stiffness.
-
Environmental Requirements: Consider the temperature, humidity, and chemical exposure requirements of your application and choose a ceramic material with the appropriate environmental resistance.
-
Cost and Lead Time: Consider the budget and schedule constraints of your project and choose a ceramic PCB supplier that can meet your cost and lead time requirements.
-
Manufacturing Capabilities: Consider the complexity and precision requirements of your circuit design and choose a ceramic PCB manufacturer with the appropriate fabrication capabilities and quality control processes.
Frequently Asked Questions (FAQ)
-
What is the difference between a ceramic PCB and a traditional FR-4 PCB?
A: Ceramic PCBs use a ceramic substrate material, such as alumina or aluminum nitride, instead of the FR-4 fiberglass used in traditional PCBs. Ceramic PCBs offer superior thermal conductivity, lower dielectric loss, and higher reliability in harsh environments compared to FR-4 PCBs. -
What are the most common ceramic materials used in PCB fabrication?
A: The most common ceramic materials used in PCB fabrication are alumina (Al2O3) and aluminum nitride (AlN). Alumina is widely used for its excellent electrical insulation properties, high thermal conductivity, and good mechanical strength, while aluminum nitride is used for applications that require even higher thermal conductivity. -
What are the typical applications of ceramic PCBs?
A: Ceramic PCBs are commonly used in high-frequency, high-power, and high-temperature applications in industries such as aerospace, defense, telecommunications, power electronics, automotive electronics, and medical devices. -
How does the manufacturing process of ceramic PCBs differ from that of traditional PCBs?
A: The manufacturing process of ceramic PCBs is more complex and specialized than that of traditional PCBs, involving steps such as substrate preparation, metallization, layup and lamination, drilling and cutting, surface finishing, and inspection and testing. -
What factors should be considered when choosing a ceramic PCB for a specific application?
A: When choosing a ceramic PCB, factors to consider include electrical requirements (frequency, power, signal integrity), thermal requirements (heat generation and dissipation), mechanical requirements (stress, vibration, shock), environmental requirements (temperature, humidity, chemical exposure), cost and lead time constraints, and manufacturing capabilities of the supplier.
Conclusion
Ceramic PCBs are a specialized type of printed circuit board that offer superior performance and reliability compared to traditional FR-4 PCBs in high-frequency, high-power, and harsh environment applications. By using ceramic substrate materials such as alumina or aluminum nitride, ceramic PCBs provide excellent thermal conductivity, low dielectric loss, and high mechanical strength.
When choosing a ceramic PCB for your application, it is important to consider the electrical, thermal, mechanical, and environmental requirements of your design, as well as the cost, lead time, and manufacturing capabilities of your supplier. By carefully evaluating these factors and working with an experienced ceramic PCB manufacturer, you can ensure that your project achieves the desired performance, reliability, and cost-effectiveness.
As technology continues to advance and demand for high-performance electronics grows, ceramic PCBs will play an increasingly important role in enabling the next generation of innovative products and systems across a wide range of industries.
Leave a Reply