What are Flex PCB Stiffeners?
Flex PCB stiffeners, also known as Rigid-Flex PCB stiffeners or reinforcement members, are rigid materials that are bonded to specific areas of a Flexible PCB to provide mechanical support and enhance the overall stability of the circuit. These stiffeners are strategically placed in regions where the flex PCB requires additional strength, such as connector areas, mounting points, or areas subjected to repeated bending or stress.
The primary purpose of flex PCB stiffeners is to prevent excessive bending, twisting, or stretching of the flexible circuit, which could lead to damage, delamination, or failure of the electrical connections. By adding rigidity to specific areas, stiffeners help maintain the integrity of the flex PCB and ensure reliable performance in demanding applications.
Types of Flex PCB Stiffeners
There are several types of flex PCB stiffeners available, each with its own characteristics and applications. The most common types include:
1. FR4 Stiffeners
FR4 (Flame Retardant 4) is a widely used material for flex PCB stiffeners. It is a glass-reinforced epoxy laminate that offers excellent mechanical strength, dimensional stability, and electrical insulation properties. FR4 stiffeners are commonly used in applications that require high rigidity and durability.
2. Polyimide Stiffeners
Polyimide stiffeners are made from high-performance polymers known for their exceptional thermal stability, chemical resistance, and mechanical strength. They are lightweight and offer good flexibility, making them suitable for applications that require a balance between rigidity and flexibility.
3. Aluminum Stiffeners
Aluminum stiffeners are used in applications that demand high thermal conductivity and heat dissipation. They are lightweight, strong, and offer excellent thermal management properties. Aluminum stiffeners are often used in high-power electronic devices or applications where heat dissipation is critical.
4. Stainless Steel Stiffeners
Stainless steel stiffeners provide exceptional mechanical strength and durability. They are suitable for applications that require high levels of rigidity and resistance to harsh environments. Stainless steel stiffeners are commonly used in industrial, automotive, and aerospace applications.
Materials Used for Flex PCB Stiffeners
The choice of material for flex PCB stiffeners depends on various factors, including the specific application requirements, environmental conditions, mechanical properties, and cost considerations. Some of the commonly used materials for flex PCB stiffeners include:
Material | Properties | Applications |
---|---|---|
FR4 | High mechanical strength, dimensional stability, electrical insulation | General-purpose, high-rigidity applications |
Polyimide | Lightweight, flexible, thermal stability, chemical resistance | Applications requiring balance between rigidity and flexibility |
Aluminum | Lightweight, high thermal conductivity, heat dissipation | High-power electronics, thermal management |
Stainless Steel | Exceptional mechanical strength, durability, resistance to harsh environments | Industrial, automotive, aerospace applications |
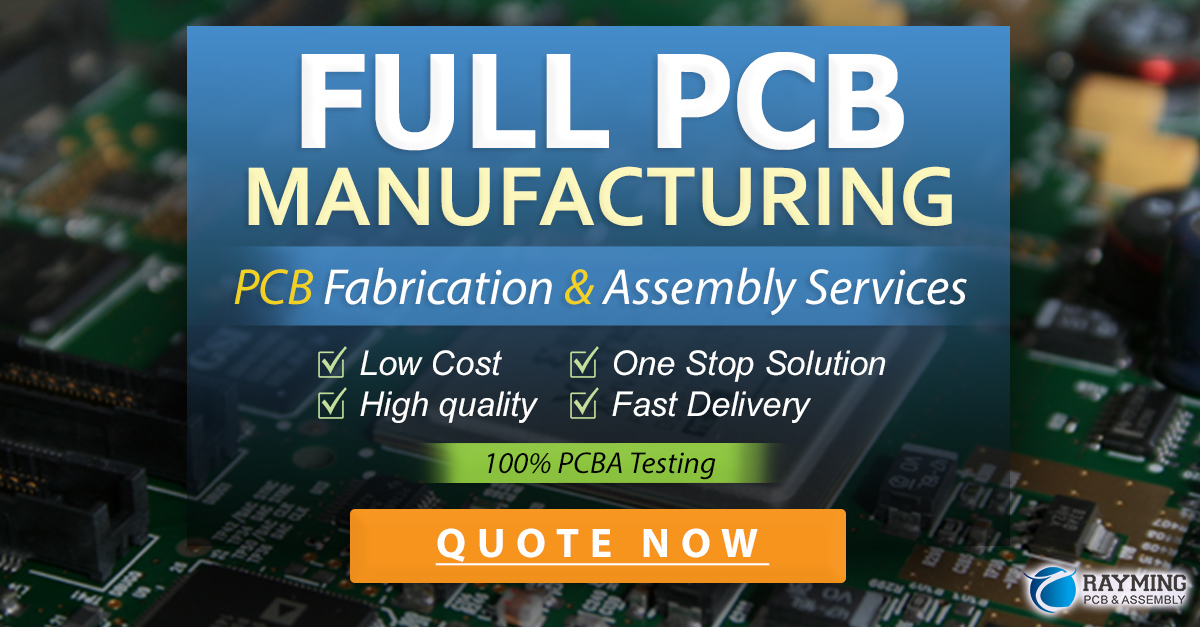
Manufacturing Process of Flex PCB Stiffeners
The manufacturing process of flex PCB stiffeners involves several steps to ensure proper bonding and integration with the flexible circuit. The general process includes:
- Material Selection: The appropriate stiffener material is selected based on the application requirements and desired properties.
- Cutting and Shaping: The stiffener material is cut and shaped to the desired dimensions and contours using precision cutting methods such as laser cutting, die cutting, or CNC Machining.
- Surface Preparation: The surfaces of the stiffener and the flex PCB are cleaned and prepared for bonding. This may involve roughening the surfaces to improve adhesion.
- Adhesive Application: A suitable adhesive, such as epoxy or acrylic-based adhesives, is applied to the bonding surfaces of the stiffener and the flex PCB.
- Alignment and Lamination: The stiffener is aligned with the designated area on the flex PCB, and the two components are laminated together under controlled pressure and temperature conditions.
- Curing: The laminated assembly is subjected to a curing process to allow the adhesive to fully bond and achieve its maximum strength.
- Inspection and Testing: The final assembly is inspected for proper alignment, adhesion, and any defects. Electrical and mechanical testing may be performed to ensure the functionality and reliability of the flex PCB with the integrated stiffener.
Advantages of Using Flex PCB Stiffeners
Flex PCB stiffeners offer several advantages that make them essential in the design and manufacturing of flexible circuits:
- Enhanced Mechanical Stability: Stiffeners provide additional rigidity to specific areas of the flex PCB, preventing excessive bending, twisting, or deformation. This enhances the overall mechanical stability and durability of the circuit.
- Improved Reliability: By minimizing the risk of damage or failure due to mechanical stress, stiffeners contribute to the improved reliability and longevity of the flex PCB Assembly.
- Localized Reinforcement: Stiffeners allow for targeted reinforcement of specific areas on the flex PCB, such as connector regions or mounting points, without adding unnecessary rigidity to the entire circuit.
- Dimensional Control: Stiffeners help maintain the desired shape and dimensions of the flex PCB, especially in applications where precise positioning or alignment is critical.
- Heat Dissipation: Certain stiffener materials, such as aluminum, offer excellent thermal conductivity, aiding in heat dissipation and thermal management of the flex PCB assembly.
- Design Flexibility: Flex PCB stiffeners can be customized in terms of shape, size, and material to meet specific application requirements, allowing for greater design flexibility and optimization.
Applications of Flex PCB Stiffeners
Flex PCB stiffeners find applications in various industries and products where flexibility, reliability, and mechanical stability are crucial. Some common applications include:
- Consumer Electronics: Smartphones, wearables, smart home devices, and other portable electronics often utilize flex PCBs with stiffeners for compact and reliable designs.
- Automotive Electronics: Flex PCBs with stiffeners are used in automotive applications such as infotainment systems, sensors, and electronic control units, where vibration and harsh environments are common.
- Medical Devices: Medical equipment, such as patient monitors, imaging devices, and wearable sensors, leverage flex PCBs with stiffeners for reliable performance and user comfort.
- Aerospace and Defense: Flex PCBs with stiffeners are used in aerospace and defense applications, including avionics, satellite systems, and military equipment, where high reliability and durability are essential.
- Industrial Equipment: Industrial control systems, robotics, and automation equipment often incorporate flex PCBs with stiffeners for reliable operation in demanding environments.
Frequently Asked Questions (FAQ)
- Q: What materials are commonly used for flex PCB stiffeners?
A: Common materials used for flex PCB stiffeners include FR4, polyimide, aluminum, and stainless steel. The choice of material depends on the specific application requirements, such as mechanical strength, thermal conductivity, and environmental factors. - Q: How are flex PCB stiffeners attached to the flexible circuit?
A: Flex PCB stiffeners are typically bonded to the flexible circuit using adhesives, such as epoxy or acrylic-based adhesives. The bonding process involves surface preparation, adhesive application, alignment, lamination, and curing to ensure a strong and reliable bond between the stiffener and the flex PCB. - Q: Can flex PCB stiffeners be customized to specific shapes and sizes?
A: Yes, flex PCB stiffeners can be customized to meet specific design requirements. They can be cut and shaped using precision cutting methods like laser cutting, die cutting, or CNC machining to achieve the desired contours and dimensions. - Q: How do flex PCB stiffeners enhance the reliability of flexible circuits?
A: Flex PCB stiffeners enhance the reliability of flexible circuits by providing localized reinforcement and preventing excessive bending, twisting, or deformation. This minimizes the risk of damage or failure due to mechanical stress, ensuring reliable performance and longevity of the flex PCB assembly. - Q: Are flex PCB stiffeners suitable for applications with high thermal requirements?
A: Yes, certain flex PCB stiffener materials, such as aluminum, offer excellent thermal conductivity and heat dissipation properties. These stiffeners can aid in thermal management by efficiently transferring heat away from critical components, making them suitable for applications with high thermal requirements.
Conclusion
Flex PCB stiffeners play a vital role in the design and manufacturing of flexible printed circuit boards, providing mechanical support, stability, and protection to the flexible circuits. By understanding the types, materials, manufacturing processes, and advantages of flex PCB stiffeners, designers and manufacturers can make informed decisions to optimize the performance and reliability of their flexible PCB assemblies.
As the demand for compact, lightweight, and reliable electronics continues to grow across various industries, the importance of flex PCB stiffeners cannot be overstated. Their ability to provide localized reinforcement, enhance mechanical stability, and improve overall reliability makes them an essential component in the development of advanced electronic devices and systems.
By leveraging the benefits of flex PCB stiffeners and selecting the appropriate materials and design approaches, manufacturers can create robust and high-performance flexible circuits that meet the evolving needs of modern electronics applications.
Leave a Reply