Introduction to Rigid-Flex PCBs
Rigid-Flex PCBs are a revolutionary technology that combines the best features of both rigid and flexible printed circuit boards. These hybrid PCBs consist of rigid and flexible substrates that are laminated together, allowing for a single circuit board to have both rigid and flexible areas. This unique design enables engineers to create more compact, reliable, and complex electronic devices that can withstand harsh environments and frequent flexing.
Rigid-Flex PCBs offer numerous advantages over traditional rigid or Flexible PCBs, including:
- Reduced size and weight
- Increased reliability and durability
- Improved signal integrity
- Enhanced design flexibility
- Simplified assembly process
Applications of Rigid-Flex PCBs
Rigid-Flex PCBs find applications in various industries, such as:
- Aerospace and defense
- Medical devices
- Automotive electronics
- Consumer electronics
- Industrial automation
- Telecommunications
These industries require high-performance, reliable, and compact electronic devices that can operate in challenging conditions. Rigid-Flex PCBs meet these requirements, making them an ideal choice for a wide range of applications.
Rigid-Flex PCB Manufacturing Process
The manufacturing process of Rigid-Flex PCBs is more complex than that of traditional rigid or flexible PCBs. It involves a combination of rigid and flexible PCB manufacturing techniques, as well as specialized materials and equipment. The general steps involved in the Rigid-Flex PCB manufacturing process are:
- Design and layout
- Material selection
- Fabrication of rigid and flexible layers
- Lamination
- Drilling and plating
- Etching and surface finish
- Solder mask and silkscreen
- Electrical testing and inspection
- Cutting and routing
- Final inspection and packaging
Design and Layout Considerations
Designing a Rigid-Flex PCB requires careful consideration of various factors, such as:
- Bend radius and bend cycle requirements
- Material selection for rigid and flexible layers
- Layer stackup and thickness
- Copper weight and trace width
- Via placement and design
- Impedance control
- Signal integrity and EMI/EMC
Designers must also adhere to the manufacturing capabilities and limitations of the chosen Rigid-Flex PCB Manufacturer to ensure a successful and cost-effective production.
Material Selection
The choice of materials for Rigid-Flex PCBs is critical to their performance and reliability. Common materials used in Rigid-Flex PCBs include:
Material Type | Rigid Substrate | Flexible Substrate |
---|---|---|
FR-4 | Yes | No |
Polyimide | No | Yes |
Adhesives | Yes | Yes |
Copper Foil | Yes | Yes |
Coverlay | No | Yes |
The selection of materials depends on the specific application requirements, such as temperature range, flexibility, and electrical properties.
Fabrication and Lamination
The fabrication of Rigid-Flex PCBs involves the creation of both rigid and flexible layers separately, followed by the lamination process to combine them into a single board. The rigid layers are typically made from FR-4 material, while the flexible layers are made from polyimide.
The lamination process is critical to the integrity and reliability of the Rigid-Flex PCB. It involves bonding the rigid and flexible layers together using adhesives and applying heat and pressure in a controlled manner. Proper lamination ensures good adhesion between the layers and prevents delamination during the product’s lifetime.
Advantages of Rigid-Flex PCBs
Space and Weight Reduction
One of the primary advantages of Rigid-Flex PCBs is their ability to reduce the overall size and weight of electronic devices. By combining rigid and flexible sections in a single board, designers can eliminate the need for separate connectors, cables, and wires. This integration leads to more compact and lightweight designs, which is particularly important in applications where space and weight are critical factors, such as aerospace, medical devices, and portable electronics.
Increased Reliability and Durability
Rigid-Flex PCBs offer superior reliability and durability compared to traditional PCB assemblies with separate rigid and flexible boards. The elimination of connectors and cables reduces the number of potential failure points, improving the overall reliability of the device. Additionally, the flexible sections of the Rigid-Flex PCB can withstand repeated flexing and bending without causing damage to the traces or components, making them ideal for applications that require frequent movement or are subject to vibration and shock.
Improved Signal Integrity
Rigid-Flex PCBs provide better signal integrity than traditional PCB assemblies due to the reduced number of interconnects and shorter signal paths. The elimination of connectors and cables minimizes signal reflections, crosstalk, and electromagnetic interference (EMI), resulting in cleaner and more stable signals. This is particularly important in high-speed and high-frequency applications, where signal integrity is critical to the device’s performance.
Enhanced Design Flexibility
Rigid-Flex PCBs offer designers greater flexibility in creating complex and unique form factors. The ability to combine rigid and flexible sections allows for the creation of three-dimensional shapes and the placement of components in unconventional locations. This design flexibility enables the development of more innovative and ergonomic products that can better adapt to the needs of the end-user.
Simplified Assembly Process
The use of Rigid-Flex PCBs can simplify the assembly process by reducing the number of steps and components required. With the elimination of connectors and cables, the assembly time and cost can be significantly reduced. Additionally, the integrated nature of Rigid-Flex PCBs minimizes the risk of assembly errors, such as incorrect connections or damaged components, leading to higher yields and lower rework costs.
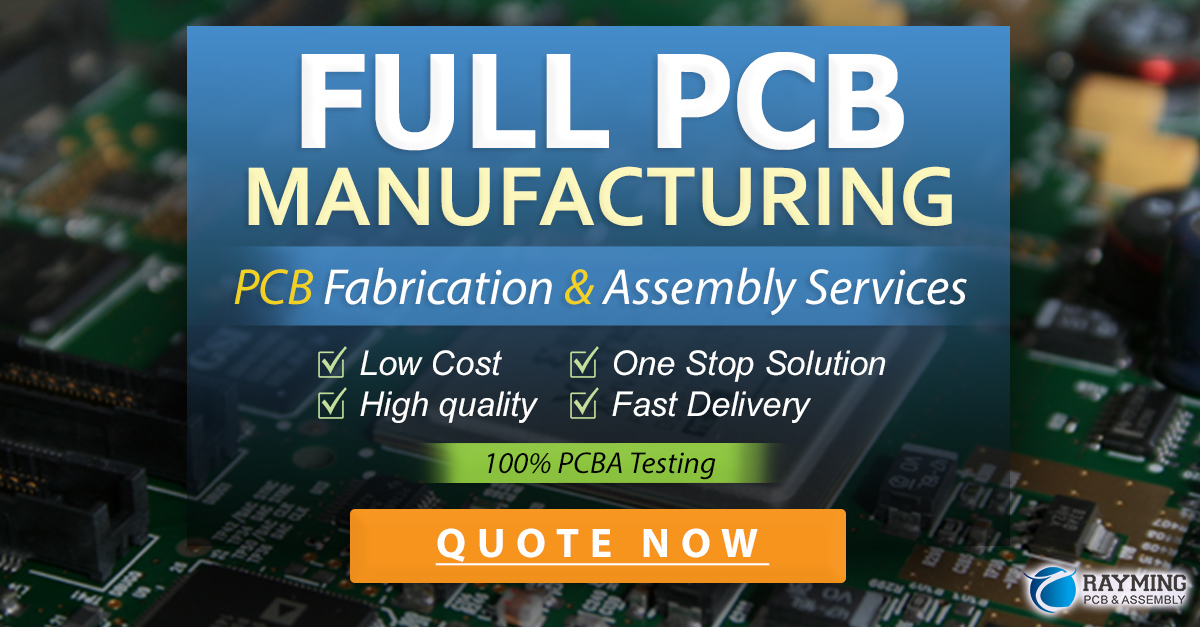
Choosing a Rigid-Flex PCB Manufacturer
When selecting a Rigid-Flex PCB manufacturer, it is essential to consider several factors to ensure a successful Partnership and high-quality products. Some key considerations include:
- Experience and expertise in Rigid-Flex PCB manufacturing
- Range of layer counts and materials supported
- Manufacturing capabilities and capacity
- Quality control and testing procedures
- Certifications and compliance with industry standards
- Technical support and customer service
- Lead times and pricing
It is also important to work closely with the chosen manufacturer throughout the design and development process to ensure that the Rigid-Flex PCB meets all the application requirements and is optimized for manufacturability and cost-effectiveness.
FAQs
1. What is the maximum number of layers that can be achieved in a Rigid-Flex PCB?
Rigid-Flex PCBs can be manufactured with up to 30 layers, combining both rigid and flexible layers. However, the actual number of layers depends on the specific application requirements and the manufacturing capabilities of the chosen Rigid-Flex PCB manufacturer.
2. Can Rigid-Flex PCBs be used in high-temperature applications?
Yes, Rigid-Flex PCBs can be designed to withstand high temperatures by using appropriate materials and manufacturing techniques. For example, using polyimide as the flexible substrate and high-temperature FR-4 for the rigid layers can enable the Rigid-Flex PCB to operate in temperature ranges up to 150°C or higher.
3. How does the bend radius affect the design of a Rigid-Flex PCB?
The bend radius is a critical factor in the design of a Rigid-Flex PCB, as it determines the minimum allowable radius of curvature for the flexible sections without causing damage or degrading performance. The bend radius depends on the thickness and material of the flexible layers, as well as the copper weight and trace width. Designers must consider the bend radius requirements when laying out the components and routing the traces to ensure the reliability and durability of the Rigid-Flex PCB.
4. What are the common challenges faced in Rigid-Flex PCB manufacturing?
Some common challenges in Rigid-Flex PCB manufacturing include:
- Ensuring proper lamination and adhesion between the rigid and flexible layers
- Maintaining the desired bend radius and flexibility of the flexible sections
- Achieving accurate registration between the rigid and flexible layers
- Controlling the impedance and signal integrity in the flexible sections
- Handling and processing thin and delicate flexible materials
Experienced Rigid-Flex PCB manufacturers employ specialized equipment, processes, and expertise to overcome these challenges and produce high-quality products.
5. How do I choose the right Rigid-Flex PCB manufacturer for my project?
When choosing a Rigid-Flex PCB manufacturer, consider factors such as their experience and expertise in Rigid-Flex PCB manufacturing, range of layer counts and materials supported, manufacturing capabilities and capacity, quality control and testing procedures, certifications and compliance with industry standards, technical support and customer service, and lead times and pricing. It is also essential to work closely with the manufacturer throughout the design and development process to ensure the Rigid-Flex PCB meets all the application requirements and is optimized for manufacturability and cost-effectiveness.
Conclusion
Rigid-Flex PCBs are a game-changing technology that combines the benefits of rigid and flexible PCBs, enabling the creation of more compact, reliable, and complex electronic devices. With their ability to reduce size and weight, increase reliability and durability, improve signal integrity, and enhance design flexibility, Rigid-Flex PCBs find applications in various industries, from aerospace and medical devices to automotive and consumer electronics.
The manufacturing process of Rigid-Flex PCBs is more complex than that of traditional PCBs, involving specialized materials, equipment, and techniques. Designers must carefully consider various factors, such as bend radius, material selection, and layer stackup, to ensure the optimal performance and reliability of the Rigid-Flex PCB.
When choosing a Rigid-Flex PCB manufacturer, it is essential to consider their experience, capabilities, and commitment to quality and customer support. By partnering with the right manufacturer and working closely with them throughout the design and development process, companies can leverage the benefits of Rigid-Flex PCBs to create innovative and high-performance electronic products that meet the demands of today’s challenging applications.
Leave a Reply