Why Transition from Gerber to IPC-2581 for PCB Data Transfer?
For decades, Gerber files have been the de facto standard for transferring PCB design data from CAD to manufacturing. However, Gerber has limitations:
- Gerber represents layers individually without describing how they relate to each other
- It lacks a standardized way to convey critical PCB data like materials, stack-up, net names, etc.
- Gerber files must be supplemented with additional documentation like fab drawings and drill files
In contrast, IPC-2581 is a newer, intelligent format that packages all the PCB design data into a single XML file. Key advantages of IPC-2581 over Gerber include:
- All layer data and how they relate are fully described in one file
- Material properties, stack-up details, net connectivity, and other critical PCB attributes are included
- IPC-2581 files are self-contained – no need for supplemental drawings and files
- XML format allows for easier data extraction and better integration with CAM and analysis tools
Adopting IPC-2581 streamlines the data handoff from design to manufacturing, reducing errors and cycle time. According to an IPC study, using IPC-2581 instead of Gerber provided the following improvements:
Metric | Gerber | IPC-2581 |
---|---|---|
First-pass success | 73% | 95% |
Rework | 27% | 5% |
Average cycle time | 5-10 days | 1-3 days |
Scrap rate | 5000 ppm | 200 ppm |
Source: IPC-2581 Consortium
The electronics industry is gradually shifting towards intelligent data formats like IPC-2581. Leading CAD tools and manufacturers already support it. Transitioning makes sense to reap significant quality, cost and time-to-market benefits.
How to Transition Your PCB Design Process to IPC-2581
Assess Your Current Workflow
The first step is understanding your existing PCB design and data handoff process:
- What PCB CAD tools do you use?
- How do you currently generate manufacturing data?
- What files get sent to your manufacturer?
- How do you communicate design intent?
- What issues or improvement areas have you noted?
Mapping out your current state will help identify gaps that moving to IPC-2581 can address. It also clarifies the changes needed in your tools and process.
Check IPC-2581 Support in Your PCB CAD Tools
Next, verify that your PCB design software supports exporting to IPC-2581 format. The table below shows the IPC-2581 status for popular PCB CAD tools:
PCB CAD Tool | IPC-2581 Export |
---|---|
Cadence Allegro | Supported |
Siemens PADS | Supported |
Altium Designer | Supported |
Zuken CR-8000 | Supported |
KiCad | Planned |
EAGLE | Not supported |
If your CAD tool lacks IPC-2581 support, consider upgrading to a newer version or switching to compatible software. Open source tools like KiCad are also working on adding IPC-2581 capability.
Coordinate with Your PCB Manufacturer
Moving to a new data format requires close collaboration with your manufacturer. Key steps to take:
- Confirm your manufacturer can accept and process IPC-2581 files
- Understand their specific requirements for IPC-2581 data
- Do test runs exchanging sample IPC-2581 files before going live
- Establish communication channels to resolve any issues quickly
Working closely with your fabricator ensures a smooth rollout of IPC-2581 for real designs. Their insights will be invaluable to optimize your IPC-2581 design data.
Adjust Your Design Workflow
Using IPC-2581 will require some changes to your PCB design workflow and deliverables:
- Design reviews can directly use the IPC-2581 to visualize the complete PCB data
- Generating Gerbers and drawings for handoff is replaced by IPC-2581 export
- Some new data entry may be needed in CAD to populate IPC-2581 parameters
Make a step-by-step plan for the workflow changes. Provide training to your designers on the new aspects. Start with a pilot project to iron out the kinks before deploying IPC-2581 on all new designs.
Monitor and Fine-tune
After you begin using IPC-2581 in production, keep monitoring the results:
- Are you seeing the expected reduction in quality issues and cycle time?
- Any problems in CAD-to-CAM data exchange?
- What feedback are you getting from your manufacturer?
Use these learnings to optimize your IPC-2581 methodology. Participate in user groups to understand best practices and upcoming enhancements to the standard.
FAQ on IPC-2581 Transition
How is IPC-2581 different from ODB++?
Both IPC-2581 and ODB++ are intelligent data formats that aim to replace Gerbers. However, there are some key differences:
- IPC-2581 is an open, neutral standard driven by industry consortia. ODB++ is controlled by a single company, Mentor Graphics.
- IPC-2581 uses standard XML while ODB++ is a proprietary binary format.
- IPC-2581 files are human-readable and easier to parse. ODB++ needs specialized viewers and processors.
In general, IPC-2581 offers similar technical capabilities as ODB++ while providing more openness, interoperability and flexibility.
Will IPC-2581 work for rigid-flex and high-density designs?
Yes, IPC-2581 is designed to handle complex PCBs, including:
- Rigid-flex with multiple stack-up zones
- HDI designs with microvias and buildup layers
- Embedded components
- High layer counts
The format scales well to advanced technologies and is future-ready as new PCB constructions evolve.
Is IPC-2581 meant only for PCB fabrication data?
No, IPC-2581 can convey the complete PCB product model and is useful through the entire product lifecycle:
- PCB fabrication
- PCB Assembly
- Test
- Inspection
- Rework/repair
The rich data model of IPC-2581 lends itself well to these different use cases. You can transition to IPC-2581 in phases, starting with fabrication and expanding to other processes.
What is the current industry adoption of IPC-2581?
The adoption of IPC-2581 is growing steadily:
- Major CAD vendors like Cadence, Siemens EDA, Altium and Zuken have added IPC-2581 export
- Several leading manufacturers, including AT&S, Sanmina and Wistron, accept IPC-2581
- Defense, aerospace and automotive OEMs are increasingly using IPC-2581 for better traceability
The recently released IPC-2581 Revision C is expected to accelerate the transition by adding more robust validation and features.
Where can I learn more about IPC-2581?
There are several good resources to dig deeper into IPC-2581:
- IPC-2581 Consortium website
- LinkedIn IPC-2581 Users Group
- IPC APEX Expo conference proceedings
- White papers from Cadence, Siemens EDA, etc.
Reach out to the IPC-2581 Consortium for specific technical queries and support. Many PCB service providers also offer IPC-2581 consulting to help with adoption.
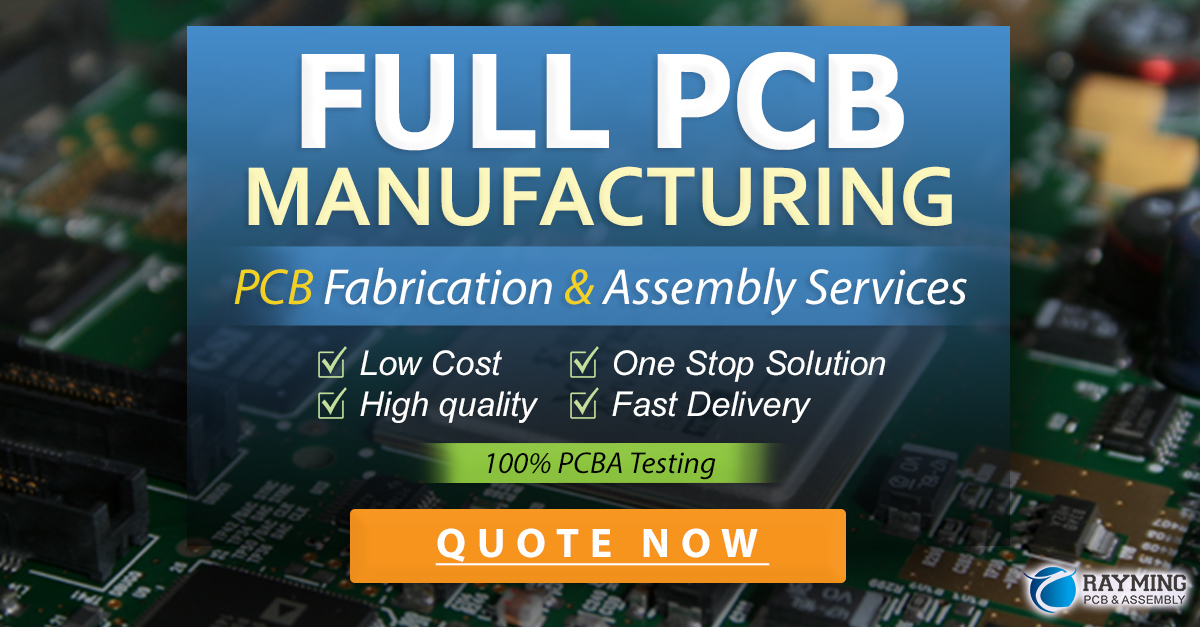
Conclusion
Transitioning from Gerber to IPC-2581 is a significant step forward for the electronics industry. It enables a more intelligent, connected process from PCB design to manufacturing, eliminating data loss and ambiguity.
The IPC-2581 ecosystem is maturing rapidly, with growing support from major design and supply chain players. Designers can confidently make the switch and reap the benefits of faster time-to-market and reduced post-release issues.
The key is to plan the transition systematically and collaborate closely with stakeholders. By assessing tooling, fine-tuning design data and monitoring results, the shift to IPC-2581 will be smooth and deliver compelling ROI.
Leave a Reply