What are PCB Vias?
Printed Circuit Board (PCB) vias are small holes drilled through the board to create electrical connections between different layers of a multi-layer PCB. Vias allow signals to pass from one layer to another, enabling more complex circuit designs and more efficient use of board space. They are essential components in modern PCB design, as they facilitate the creation of high-density, multi-layer boards.
Types of PCB Vias
There are several types of vias used in PCB design, each with its own characteristics and applications:
- Through-hole vias
- Blind vias
- Buried vias
- Microvias
- Solid vias
- Hollow vias
Through-hole Vias
Through-hole vias are the most common type of via. They are drilled through the entire thickness of the PCB, connecting all layers from top to bottom. These vias are typically plated with a conductive material, such as copper, to ensure reliable electrical connections.
Advantages | Disadvantages |
---|---|
Easy to manufacture | Occupy more board space |
Cost-effective | Limit component placement |
Provide strong mechanical connections | Increase board thickness |
Blind Vias
Blind vias are drilled from one side of the PCB and terminate at a specific inner layer, rather than passing through the entire board. They are used to connect an outer layer to one or more inner layers, but not to the opposite outer layer.
Advantages | Disadvantages |
---|---|
Save board space | More expensive to manufacture |
Allow for higher component density | Require precise drilling |
Reduce signal interference | Limited to connecting outer layers to inner layers |
Buried Vias
Buried vias are located entirely within the inner layers of a PCB, connecting two or more inner layers without reaching either outer layer. They are used to create connections between inner layers without affecting the outer layers or components.
Advantages | Disadvantages |
---|---|
Save board space | More expensive to manufacture |
Allow for higher component density | Require precise alignment of inner layers |
Reduce signal interference | Limited to connecting inner layers |
Microvias
Microvias are small-diameter vias, typically less than 0.15mm (6 mils) in diameter. They are used in high-density PCB designs to create connections between closely spaced components or to connect fine-pitch BGA packages.
Advantages | Disadvantages |
---|---|
Allow for high-density designs | More expensive to manufacture |
Reduce signal interference | Require specialized equipment |
Enable the use of fine-pitch components | Limited to connecting outer layers to inner layers |
Solid Vias
Solid vias are filled with a conductive material, such as copper or a conductive paste, to create a solid connection between layers. They are used in high-power applications or when a strong mechanical connection is required.
Advantages | Disadvantages |
---|---|
Provide strong mechanical connections | More expensive to manufacture |
Improve thermal dissipation | Require additional processing steps |
Reduce signal interference | May cause thermal stress during soldering |
Hollow Vias
Hollow vias, also known as air-core vias, are not filled with a conductive material. They are used in high-frequency applications to reduce capacitance and improve signal integrity.
Advantages | Disadvantages |
---|---|
Reduce capacitance | Weaker mechanical connections |
Improve signal integrity | May require additional support structures |
Cost-effective | Not suitable for high-power applications |
PCB Via Design Considerations
When designing vias for a PCB, several factors must be considered to ensure optimal performance and manufacturability:
- Via size and drill diameter
- Via placement and spacing
- Via-in-pad design
- Thermal relief vias
- Vias for high-speed signals
Via Size and Drill Diameter
The size and drill diameter of a via are critical factors in PCB design. Smaller vias allow for higher component density and more efficient use of board space, but they are more challenging to manufacture and may increase production costs. Larger vias are easier to manufacture and provide stronger mechanical connections, but they occupy more board space and may limit component placement.
When selecting via sizes, designers must consider the following:
- The current-carrying capacity of the via
- The mechanical strength required for the connection
- The available board space and component density
- The manufacturing capabilities of the PCB fabricator
Typical via drill diameters range from 0.2mm to 1.0mm, with 0.3mm to 0.6mm being the most common.
Via Placement and Spacing
Via placement and spacing are essential for ensuring proper electrical connections and preventing signal interference. Vias should be placed as close to their associated components as possible to minimize signal path length and reduce inductance. However, vias must also be spaced far enough apart to prevent crosstalk and maintain signal integrity.
The following guidelines can help optimize via placement and spacing:
- Place vias as close to their associated components as possible
- Maintain a minimum spacing between vias to prevent crosstalk
- Avoid placing vias in sensitive areas, such as under components or in high-speed signal paths
- Use via fences or shielding to isolate sensitive signals from interference
Via-in-Pad Design
Via-in-pad (VIP) design involves placing a via directly in the solder pad of a component. This technique is used to save board space and improve signal integrity by reducing the signal path length. However, VIP design requires careful consideration of the solder joint and the via’s impact on the component’s mechanical and thermal properties.
When implementing VIP design, designers should:
- Ensure the via size is compatible with the solder pad and component lead
- Use filled or capped vias to prevent solder wicking and improve joint strength
- Consider the thermal expansion differences between the via and the component
- Verify the manufacturability of the VIP design with the PCB fabricator
Thermal Relief Vias
Thermal relief vias are used to improve the solderability of large copper areas, such as ground planes or power planes. These vias are placed around the perimeter of the copper area to provide a thermal path for heat dissipation during soldering, preventing the formation of cold solder joints.
Thermal relief vias should be designed with the following considerations:
- Use a sufficient number of vias to provide adequate thermal relief
- Space the vias evenly around the perimeter of the copper area
- Ensure the via size is compatible with the solder paste and soldering process
- Verify the thermal relief design with the PCB fabricator
Vias for High-Speed Signals
High-speed signals require special consideration when designing vias to maintain signal integrity and prevent interference. The following techniques can be used to optimize vias for high-speed signals:
- Use microvias to minimize signal path length and reduce inductance
- Employ differential pair vias for balanced signal transmission
- Implement ground vias adjacent to signal vias to provide shielding and reduce crosstalk
- Use back-drilling to remove the unused portion of through-hole vias, reducing stub resonance
Designers should also consider the impedance matching and return path of high-speed signals when placing vias to ensure optimal signal quality.
PCB Via covering
Via covering, also known as via capping or Via Filling, is the process of sealing the top or bottom of a via with a conductive material. This technique is used to improve the mechanical strength of the via, prevent solder wicking, and enhance the electrical and thermal properties of the connection.
Techniques for Via Covering
There are several techniques for covering vias, each with its own advantages and disadvantages:
- Via filling with conductive epoxy
- Via capping with copper foil
- Via plugging with a conductive paste
- Via Plating with electroless copper
Via Filling with Conductive Epoxy
Via filling with conductive epoxy involves injecting a conductive epoxy material into the Via hole and curing it to create a solid, conductive connection. This technique provides a strong mechanical connection and good electrical conductivity, but it may be more expensive and time-consuming than other methods.
Advantages | Disadvantages |
---|---|
Strong mechanical connection | More expensive process |
Good electrical conductivity | Longer processing time |
Suitable for high-power applications | May cause thermal stress during curing |
Via Capping with Copper Foil
Via capping with copper foil involves placing a small piece of copper foil over the top or bottom of the via and soldering it in place. This technique is simple and cost-effective, but it may not provide as strong a mechanical connection as other methods.
Advantages | Disadvantages |
---|---|
Simple and cost-effective | Weaker mechanical connection |
Fast processing time | May not be suitable for high-power applications |
Minimal impact on board thickness | Requires precise placement of copper foil |
Via Plugging with a Conductive Paste
Via plugging with a conductive paste involves filling the via hole with a conductive paste material, such as silver-filled epoxy, and curing it to create a solid connection. This technique provides good electrical conductivity and can be used for high-density designs, but it may be more expensive than other methods.
Advantages | Disadvantages |
---|---|
Good electrical conductivity | More expensive process |
Suitable for high-density designs | May cause thermal stress during curing |
Can be used for small-diameter vias | Requires precise dispensing of paste |
Via Plating with Electroless Copper
Via plating with electroless copper involves depositing a layer of copper on the walls of the via hole using an electroless plating process. This technique provides a uniform, conductive coating that enhances the electrical and thermal properties of the via, but it may be more expensive and time-consuming than other methods.
Advantages | Disadvantages |
---|---|
Uniform, conductive coating | More expensive process |
Enhances electrical and thermal properties | Longer processing time |
Suitable for high-reliability applications | Requires specialized equipment and chemicals |
Choosing the Right Via Covering Technique
When selecting a via covering technique, designers should consider the following factors:
- The electrical and mechanical requirements of the application
- The available board space and component density
- The manufacturing capabilities of the PCB fabricator
- The cost and time constraints of the project
Designers should also consult with their PCB fabricator to determine the most suitable via covering technique for their specific application and manufacturing process.
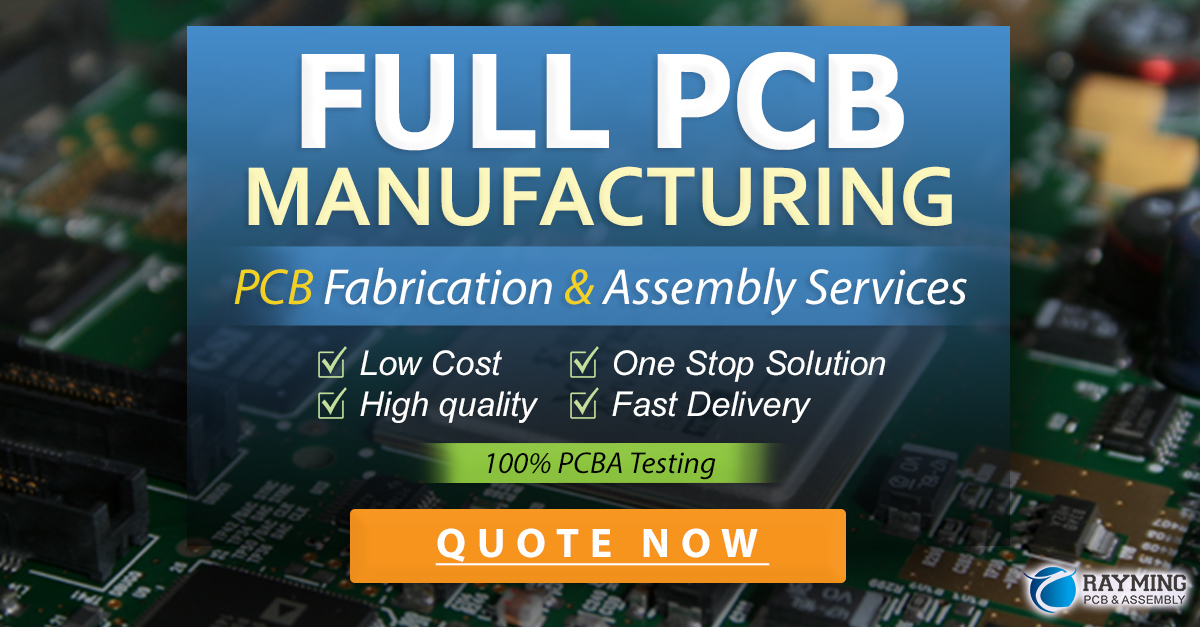
Frequently Asked Questions (FAQ)
- What is the difference between a through-hole via and a blind via?
-
A through-hole via passes through the entire thickness of the PCB, connecting all layers from top to bottom. A blind via, on the other hand, is drilled from one side of the PCB and terminates at a specific inner layer, connecting an outer layer to one or more inner layers but not to the opposite outer layer.
-
What are microvias, and when are they used?
-
Microvias are small-diameter vias, typically less than 0.15mm (6 mils) in diameter. They are used in high-density PCB designs to create connections between closely spaced components or to connect fine-pitch BGA packages. Microvias allow for higher component density and reduced signal interference.
-
What is via-in-pad (VIP) design, and what are its advantages?
-
Via-in-pad (VIP) design involves placing a via directly in the solder pad of a component. This technique saves board space and improves signal integrity by reducing the signal path length. However, VIP design requires careful consideration of the solder joint and the via’s impact on the component’s mechanical and thermal properties.
-
What are thermal relief vias, and why are they used?
-
Thermal relief vias are used to improve the solderability of large copper areas, such as ground planes or power planes. These vias are placed around the perimeter of the copper area to provide a thermal path for heat dissipation during soldering, preventing the formation of cold solder joints.
-
What factors should be considered when choosing a via covering technique?
- When selecting a via covering technique, designers should consider the electrical and mechanical requirements of the application, the available board space and component density, the manufacturing capabilities of the PCB fabricator, and the cost and time constraints of the project. Consultation with the PCB fabricator is also essential to determine the most suitable technique for the specific application and manufacturing process.
In conclusion, PCB vias are essential components in modern PCB design, enabling the creation of high-density, multi-layer boards with complex circuit designs. By understanding the different types of vias, their design considerations, and the various via covering techniques, designers can create reliable, high-performance PCBs that meet the demands of today’s electronic devices. Careful planning, collaboration with PCB fabricators, and adherence to best practices in via design and implementation are key to ensuring the success of any PCB project.
Leave a Reply