Why is Via Filling Important?
Via filling plays a vital role in the functionality and reliability of modern PCBs. Here are some key reasons why via filling is essential:
-
Improved Electrical Conductivity: By filling the vias with a conductive material, the electrical connection between layers is enhanced, reducing resistance and improving signal integrity.
-
Increased Mechanical Strength: Filled vias provide additional mechanical support to the PCB, making it more resilient to stress and vibration.
-
Better Heat Dissipation: Filled vias act as thermal conduits, allowing heat to dissipate more efficiently from one layer to another, thus improving the thermal management of the PCB.
-
Reduced Electromagnetic Interference (EMI): Filled vias help minimize EMI by providing a low-impedance path for high-frequency signals, thereby reducing unwanted noise and cross-talk between layers.
-
Enhanced Manufacturing Process: Via filling enables the use of advanced manufacturing techniques, such as blind and buried vias, which allow for higher density PCB designs and improved overall performance.
Via Filling Techniques
There are several techniques used for via filling, each with its own advantages and limitations. The choice of technique depends on factors such as the size of the vias, the desired filling material, and the specific requirements of the PCB design. Here are some common via filling techniques:
1. Electroplating
Electroplating is a popular method for via filling, especially for small-diameter vias. In this process, the PCB is immersed in an electrolytic solution containing the desired filling material, typically copper. An electric current is applied, causing the copper ions to deposit onto the walls and bottom of the vias, gradually filling them up.
Advantages:
– Uniform filling of vias
– Suitable for high-volume production
– Compatible with a wide range of via sizes
Limitations:
– Requires specialized equipment and skilled operators
– Can be time-consuming for thick PCBs or large via diameters
– May require additional processing steps, such as planarization
2. Screen Printing
Screen printing involves using a stencil to apply a conductive paste, such as copper or silver-filled epoxy, onto the surface of the PCB and into the vias. The paste is then cured using heat, forming a solid conductive fill within the vias.
Advantages:
– Cost-effective for low-volume production
– Suitable for larger via diameters
– Faster than electroplating for some applications
Limitations:
– Limited to relatively shallow vias
– May require multiple printing cycles for complete filling
– Potential for voids or inconsistencies in the fill material
3. Conductive Ink Filling
Conductive ink filling is a newer technique that uses a specialized inkjet printer to deposit a conductive ink directly into the vias. The ink is then cured using heat or ultraviolet (UV) light, forming a solid conductive fill.
Advantages:
– High precision and control over the filling process
– Suitable for small via diameters and high-density PCB designs
– Minimal waste and clean-up requirements
Limitations:
– Relatively slow process compared to other techniques
– Limited to specific ink formulations and curing methods
– May require specialized equipment and software
Via Filling Materials
The choice of via filling material depends on the specific requirements of the PCB, such as electrical conductivity, thermal performance, and cost. Here are some common materials used for via filling:
-
Copper: Copper is the most widely used material for via filling due to its excellent electrical conductivity and compatibility with the copper traces on the PCB. Copper-filled vias provide a seamless electrical connection between layers and enhance the overall performance of the PCB.
-
Conductive Epoxy: Conductive epoxies are polymer-based materials filled with conductive particles, such as silver or copper. These materials offer good electrical conductivity and can be applied using screen printing or dispensing techniques. Conductive epoxies are often used for larger via diameters or when a more flexible fill material is required.
-
Solder Paste: Solder paste, a mixture of tiny solder particles and flux, can be used to fill vias in some applications. The paste is applied using screen printing or dispensing, and then reflowed using heat to form a solid conductive fill. Solder-filled vias are commonly used in Multilayer PCBs with through-hole components.
-
Conductive Inks: Conductive inks are specialized formulations designed for inkjet printing or dispensing directly into vias. These inks typically contain conductive particles, such as silver or copper, suspended in a liquid carrier. After printing, the ink is cured using heat or UV light to form a solid conductive fill. Conductive inks offer high precision and control over the filling process, making them suitable for high-density PCB designs.
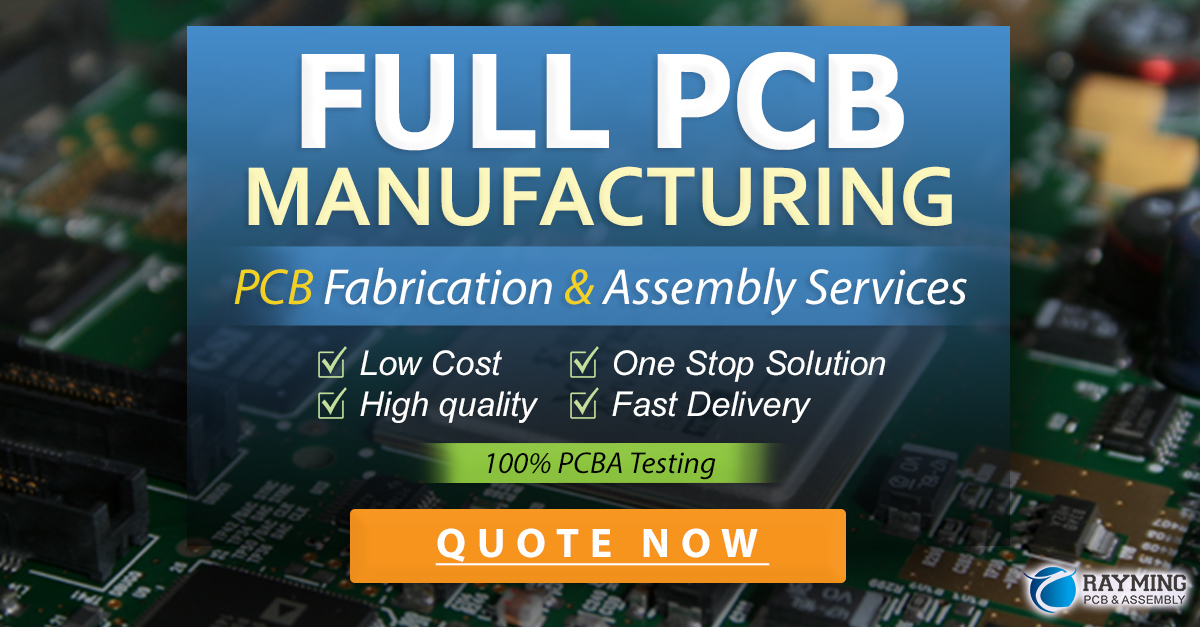
Challenges in Via Filling
While via filling offers numerous benefits, there are also some challenges associated with the process. Here are some common issues that can arise during via filling:
-
Void Formation: Voids, or air pockets, can form within the filled vias due to insufficient filling, trapped air, or outgassing during the curing process. Voids can compromise the electrical and thermal performance of the vias and may lead to reliability issues over time.
-
Incomplete Filling: Incomplete filling occurs when the filling material fails to completely fill the via, leaving gaps or spaces. This can happen due to inadequate material flow, improper curing, or compatibility issues between the filling material and the via surface.
-
Thermal Stress: During the via filling process, especially when using high-temperature curing methods, thermal stress can develop within the PCB. This stress can cause delamination, warping, or other mechanical issues, particularly in thick or high-density PCBs.
-
Compatibility Issues: The choice of filling material must be compatible with the PCB substrate, surface finishes, and other components. Incompatible materials can lead to poor adhesion, delamination, or chemical reactions that compromise the integrity of the filled vias.
-
Cost and Time: Via filling can add significant cost and time to the PCB manufacturing process, particularly for high-density designs or large production volumes. Balancing the benefits of via filling with the associated costs and lead times is an important consideration for PCB designers and manufacturers.
Best Practices for Via Filling
To ensure successful via filling and optimal PCB performance, here are some best practices to follow:
-
Choose the Right Technique: Select the via filling technique that best suits your PCB design, production volume, and budget. Consider factors such as via size, aspect ratio, and desired filling material when making your choice.
-
Optimize Via Design: Design vias with appropriate diameters, spacing, and aspect ratios to facilitate effective filling. Consult with your PCB manufacturer to ensure your via design is compatible with their filling processes and capabilities.
-
Control Material Properties: Ensure the filling material has the desired electrical, thermal, and mechanical properties for your application. Work with your material supplier to select the best formulation and curing method for your specific needs.
-
Monitor Process Parameters: Closely monitor and control the process parameters during via filling, such as temperature, pressure, and curing time. Consistent and well-controlled processes help minimize voids, incomplete filling, and other defects.
-
Perform Quality Inspections: Regularly inspect filled vias using cross-sectioning, X-ray imaging, or other methods to assess the quality of the fill. Identify and address any issues promptly to maintain high yields and reliability.
-
Collaborate with Experts: Partner with experienced PCB manufacturers, material suppliers, and equipment providers who have expertise in via filling. Their knowledge and support can help optimize your via filling process and ensure the best possible results for your PCB design.
Frequently Asked Questions (FAQ)
- What is the difference between blind, buried, and through vias?
- Blind vias connect an outer layer to an inner layer, but do not go through the entire PCB.
- Buried vias connect two or more inner layers, but do not reach the outer layers.
-
Through vias connect all layers of the PCB, from top to bottom.
-
Can all PCB designs benefit from via filling?
-
While via filling offers many advantages, not all PCB designs require it. The decision to use via filling depends on factors such as the PCB’s intended application, performance requirements, and manufacturing constraints. In general, high-density, high-speed, or thermally demanding PCBs are more likely to benefit from via filling.
-
How does via filling affect the cost and lead time of PCB production?
-
Via filling typically adds cost and time to the PCB manufacturing process. The exact impact depends on factors such as the chosen filling technique, the number and size of vias, and the production volume. In general, via filling can increase the cost and lead time by 20-50% compared to a non-filled PCB. However, the benefits of via filling, such as improved performance and reliability, often outweigh the additional costs for critical applications.
-
Can filled vias be reworked or repaired?
-
Reworking or repairing filled vias can be challenging, as the filling material must be removed without damaging the surrounding PCB structure. The feasibility of rework depends on the specific filling material and technique used. In general, it is best to avoid the need for rework by ensuring proper via design, material selection, and process control during the initial manufacturing stage.
-
How can I ensure the reliability of filled vias in my PCB design?
- To ensure the reliability of filled vias, follow best practices such as optimizing via design, selecting compatible materials, controlling process parameters, and performing regular quality inspections. Collaborate with experienced PCB manufacturers and material suppliers who can provide guidance and support throughout the via filling process. Additionally, consider incorporating filled via reliability testing, such as thermal cycling or cross-sectioning, into your PCB qualification and monitoring plans.
Conclusion
Via filling is a critical process in the manufacturing of high-performance PCBs. By filling the vias with conductive materials, designers can improve electrical conductivity, mechanical strength, thermal management, and EMI performance. The choice of via filling technique and material depends on factors such as via size, PCB design, and specific application requirements.
While via filling presents some challenges, such as void formation, incomplete filling, and thermal stress, these can be mitigated through proper design, material selection, process control, and quality inspections. By following best practices and collaborating with experienced partners, PCB designers and manufacturers can successfully incorporate via filling into their projects and achieve optimal results.
As PCB technologies continue to advance, via filling will play an increasingly important role in enabling the next generation of high-density, high-speed, and high-reliability electronic devices. By understanding the principles, techniques, and benefits of via filling, PCB professionals can stay at the forefront of this critical technology and deliver innovative solutions to meet the ever-evolving demands of the electronics industry.
Leave a Reply