What is HDI PCB?
HDI PCB is a type of printed circuit board that features higher wiring density per unit area compared to conventional PCBs. This increased density is achieved through the use of smaller vias, finer trace widths and spaces, and multiple layers of interconnections. The result is a compact, high-performance board that can accommodate a greater number of components and complex circuitry in a smaller footprint.
The IPC (Association Connecting Electronics Industries) defines HDI PCBs as having one or more of the following features:
- Via hole diameter less than 0.15mm (6 mil)
- Line width/space less than 0.09mm (3.5 mil)
- Capture pad diameter less than 0.25mm (10 mil)
Benefits of HDI PCB
HDI PCB technology offers numerous advantages over traditional PCB designs:
-
Miniaturization: HDI PCBs enable the creation of smaller, more compact electronic devices without sacrificing functionality or performance.
-
Increased functionality: With higher wiring density, HDI PCBs can accommodate more components and complex circuitry, allowing for enhanced device capabilities.
-
Improved signal integrity: Shorter signal paths and reduced layer count in HDI PCBs minimize signal loss and distortion, resulting in better signal integrity and overall performance.
-
Reduced power consumption: HDI PCBs’ compact design leads to shorter trace lengths, which in turn reduces power consumption and improves energy efficiency.
-
Cost-effectiveness: Although the initial cost of HDI PCBs may be higher, their ability to integrate more functionality into a smaller space often results in lower overall system costs.
Applications of HDI PCB
HDI PCB technology finds applications across various industries and products, including:
-
Consumer electronics: Smartphones, tablets, wearables, and other portable devices heavily rely on HDI PCBs to achieve their compact size and advanced features.
-
Automotive electronics: As vehicles become more technologically advanced, HDI PCBs are used in infotainment systems, driver assistance features, and electronic control units.
-
Medical devices: HDI PCBs are essential in the development of miniaturized, high-performance medical devices such as implantable devices, diagnostic equipment, and wearable health monitors.
-
Aerospace and defense: The aerospace and defense industries utilize HDI PCBs in avionics, satellite systems, and military communication equipment, where reliability and performance are critical.
-
Industrial automation: HDI PCBs are used in robotics, machine vision systems, and other industrial automation applications that require high-speed data processing and compact design.
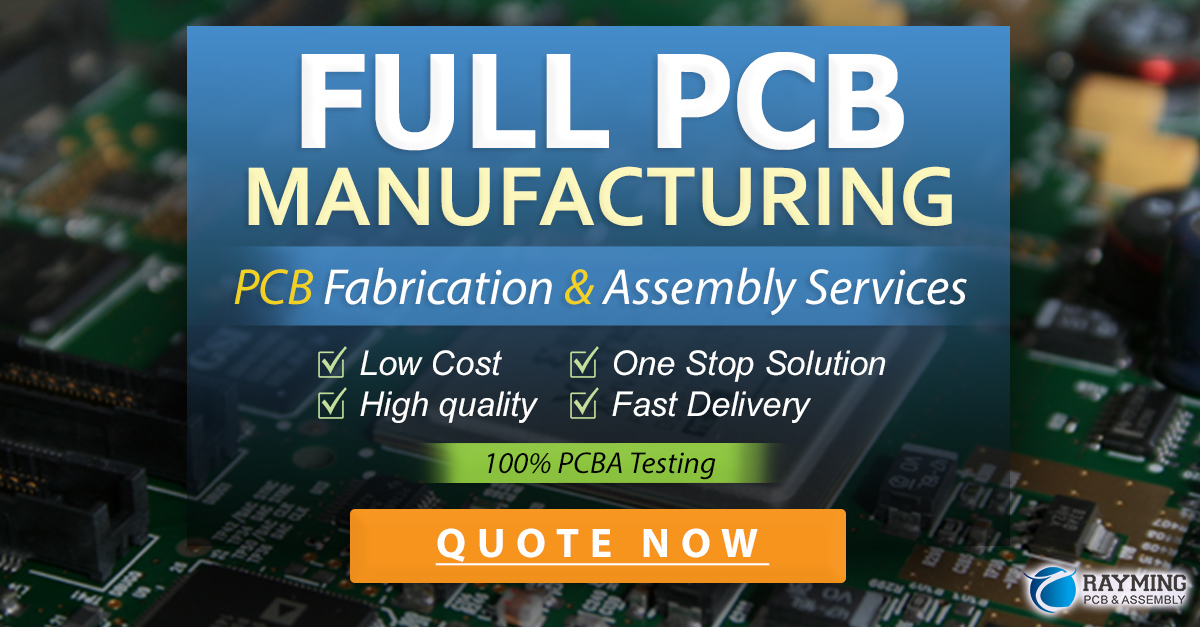
HDI PCB Manufacturing Process
The manufacturing process for HDI PCBs is more complex and precise than that of traditional PCBs. The key steps involved in HDI PCB Fabrication are:
-
Material selection: High-quality, high-performance materials such as polyimide or liquid crystal polymer (LCP) are often used for HDI PCBs to ensure reliability and durability.
-
Drilling: Mechanical or laser drilling is used to create the small, precise vias required for HDI PCBs. Laser drilling is preferred for its ability to create smaller, more accurate holes.
-
Plating: The drilled holes are plated with copper to create the interconnections between layers. Various plating techniques, such as electroless and electrolytic plating, are employed.
-
Patterning: The desired circuit pattern is transferred onto the PCB Layers using photolithography. This process involves applying a photoresist, exposing it to UV light through a patterned mask, and developing the resist to reveal the circuit pattern.
-
Lamination: The individual PCB layers are aligned and bonded together under heat and pressure to form the multi-layer HDI PCB stack.
-
Surface finishing: The exposed copper surfaces are coated with a protective finish, such as ENIG (Electroless Nickel Immersion Gold) or ENEPIG (Electroless Nickel Electroless Palladium Immersion Gold), to prevent oxidation and improve solderability.
-
Electrical testing: The completed HDI PCB undergoes rigorous electrical testing to ensure functionality, reliability, and adherence to specifications.
HDI PCB Design Considerations
Designing an HDI PCB requires careful consideration of various factors to ensure optimal performance and manufacturability:
-
Layer stack-up: Determining the appropriate number of layers and their arrangement is crucial for HDI PCB design. The stack-up must consider signal integrity, power distribution, and manufacturing constraints.
-
Via types and placement: HDI PCBs employ various types of vias, such as blind, buried, and micro vias, to achieve high-density interconnections. Via placement must be optimized to minimize signal degradation and manufacturing challenges.
-
Trace width and spacing: Narrower trace widths and smaller spacing between traces enable higher wiring density but also pose challenges for manufacturing and signal integrity. Designers must strike a balance between density and manufacturability.
-
Component placement: Careful component placement is essential to minimize signal path lengths, reduce crosstalk, and facilitate efficient routing. High-density component placement requires consideration of manufacturing capabilities and assembly processes.
-
Signal integrity analysis: Conducting thorough signal integrity analysis is critical in HDI PCB design to ensure reliable high-speed performance. This includes evaluating impedance matching, crosstalk, and signal reflections.
-
Thermal management: With higher component density and increased power consumption, thermal management becomes a key concern in HDI PCB design. Appropriate thermal management strategies, such as the use of thermal vias and heat spreaders, must be incorporated.
Future Trends in HDI PCB Technology
As electronic devices continue to evolve, HDI PCB technology must keep pace with the growing demands for miniaturization, performance, and functionality. Some of the future trends in HDI PCB technology include:
-
Advanced materials: The development of new, high-performance materials, such as low-loss dielectrics and thermally conductive substrates, will enable the creation of even more advanced HDI PCBs.
-
Embedded components: The integration of passive components, such as resistors and capacitors, directly into the PCB Substrate will further increase component density and minimize board size.
-
3D printing: Additive manufacturing techniques, such as 3D printing, may be used to create complex HDI PCB structures and enable new design possibilities.
-
5G and beyond: As the demand for high-speed, low-latency communication grows with the adoption of 5G and future wireless technologies, HDI PCBs will play a crucial role in enabling the necessary hardware.
-
Artificial intelligence: The integration of AI capabilities into edge devices will require advanced HDI PCB solutions to accommodate the necessary processing power and memory in compact form factors.
FAQs
-
What is the difference between HDI PCB and traditional PCB?
HDI PCBs have higher wiring density per unit area compared to traditional PCBs. They feature smaller vias, finer trace widths and spaces, and multiple layers of interconnections, enabling more compact and complex designs. -
What are the benefits of using HDI PCBs in electronic devices?
HDI PCBs offer several benefits, including miniaturization, increased functionality, improved signal integrity, reduced power consumption, and cost-effectiveness. These advantages make HDI PCBs an attractive choice for a wide range of electronic applications. -
What industries commonly use HDI PCBs?
HDI PCBs are used in various industries, such as consumer electronics, automotive electronics, medical devices, aerospace and defense, and industrial automation. They are particularly valuable in applications that require high performance, compact size, and complex functionality. -
What are the key design considerations for HDI PCBs?
When designing HDI PCBs, engineers must consider factors such as layer stack-up, via types and placement, trace width and spacing, component placement, signal integrity, and thermal management. Careful attention to these aspects ensures optimal performance and manufacturability. -
How do HDI PCBs contribute to the development of future electronic devices?
HDI PCBs play a crucial role in enabling the development of advanced electronic devices. As trends such as 5G, artificial intelligence, and the Internet of Things continue to evolve, HDI PCBs will be essential in providing the necessary high-density interconnections, signal integrity, and compact form factors required by these technologies.
Conclusion
HDI PCB technology has revolutionized the world of electronics manufacturing, enabling the creation of smaller, more powerful, and more sophisticated devices. With its ability to accommodate higher wiring density, improved signal integrity, and reduced power consumption, HDI PCBs have become an indispensable tool for industries ranging from consumer electronics to aerospace and defense.
As electronic devices continue to evolve and new technologies emerge, HDI PCBs will remain at the forefront of innovation, pushing the boundaries of what is possible in terms of performance, functionality, and miniaturization. By understanding the intricacies of HDI PCB technology, designers and engineers can harness its potential to create the next generation of cutting-edge electronic devices.
Feature | HDI PCB | Traditional PCB |
---|---|---|
Via hole diameter | Less than 0.15mm (6 mil) | Greater than 0.15mm |
Line width/space | Less than 0.09mm (3.5 mil) | Greater than 0.09mm |
Capture pad diameter | Less than 0.25mm (10 mil) | Greater than 0.25mm |
Wiring density | High | Low |
Layers | Multiple | Fewer |
Size | Compact | Larger |
Signal integrity | Improved | Lesser |
Power consumption | Reduced | Higher |
Cost | Higher initial cost | Lower initial cost |
Leave a Reply