Common PCB Substrate Materials
There are several common substrate materials used in PCB manufacturing, each with its own set of properties and advantages. The following table summarizes the most widely used PCB substrate materials:
Material | Description | Key Properties |
---|---|---|
FR-4 | Glass-reinforced epoxy laminate | Good electrical insulation, moderate thermal stability, cost-effective |
High Tg FR-4 | FR-4 with higher glass transition temperature | Improved thermal stability and reliability compared to standard FR-4 |
Polyimide | High-performance thermoplastic polymer | Excellent thermal stability, high dimensional stability, low dielectric constant |
PTFE (Teflon) | Fluoropolymer | Low dielectric constant, low dissipation factor, high thermal stability |
Ceramic | Inorganic, non-metallic material | High thermal conductivity, low thermal expansion, excellent electrical insulation |
Metal Core | Metal base with dielectric layer | High thermal conductivity, efficient heat dissipation, improved mechanical strength |
Flexible (Polyimide, PET) | Thin, flexible polymer films | Flexibility, lightweight, conformability to various shapes |
FR-4 (Flame Retardant 4)
FR-4 is the most commonly used PCB substrate material, consisting of a glass-reinforced epoxy laminate. It offers a balance of good electrical insulation, mechanical strength, and cost-effectiveness. FR-4 is suitable for a wide range of applications, including consumer electronics, industrial control systems, and telecommunications equipment.
Advantages of FR-4:
– Good electrical insulation properties
– Moderate thermal stability
– Cost-effective and widely available
– Suitable for most general-purpose applications
Disadvantages of FR-4:
– Limited high-frequency performance due to higher dielectric constant and dissipation factor
– Moderate thermal conductivity, which may be insufficient for high-power applications
High Tg FR-4
High Tg FR-4 is an enhanced version of the standard FR-4 substrate, featuring a higher glass transition temperature (Tg). The increased Tg value improves the thermal stability and reliability of the PCB, making it more suitable for applications that require higher operating temperatures or increased durability.
Advantages of High Tg FR-4:
– Improved thermal stability compared to standard FR-4
– Enhanced reliability and durability
– Suitable for applications with higher operating temperatures
Disadvantages of High Tg FR-4:
– Slightly higher cost than standard FR-4
– Still limited in terms of high-frequency performance
Polyimide
Polyimide is a high-performance thermoplastic polymer that offers excellent thermal stability, high dimensional stability, and a low dielectric constant. It is commonly used in applications that demand high reliability and performance, such as aerospace, military, and high-speed digital circuits.
Advantages of Polyimide:
– Excellent thermal stability, with a high glass transition temperature
– High dimensional stability, minimizing warpage and distortion
– Low dielectric constant, suitable for high-frequency applications
– Resistant to chemicals and solvents
Disadvantages of Polyimide:
– Higher cost compared to FR-4 and other standard materials
– More challenging to process and manufacture
PTFE (Polytetrafluoroethylene, Teflon)
PTFE, also known as Teflon, is a fluoropolymer with exceptional electrical properties, including a low dielectric constant and low dissipation factor. It is ideal for high-frequency applications, such as RF and microwave circuits, where signal integrity is critical.
Advantages of PTFE:
– Low dielectric constant and dissipation factor, minimizing signal loss
– High thermal stability and chemical resistance
– Excellent performance in high-frequency applications
Disadvantages of PTFE:
– Higher cost compared to other substrate materials
– Challenging to process and manufacture due to its unique properties
– Limited mechanical strength and durability
Ceramic
Ceramic substrates are made from inorganic, non-metallic materials and offer excellent thermal conductivity, low thermal expansion, and high electrical insulation. They are commonly used in high-power applications, such as power electronics and LED lighting, where efficient heat dissipation is critical.
Advantages of Ceramic:
– High thermal conductivity, enabling efficient heat dissipation
– Low thermal expansion, minimizing stress and warpage
– Excellent electrical insulation properties
– High mechanical strength and durability
Disadvantages of Ceramic:
– Higher cost compared to organic substrate materials
– Brittle and prone to cracking if not handled properly
– Limited flexibility in terms of design and manufacturing
Metal Core
Metal core substrates consist of a metal base, typically aluminum, with a thin dielectric layer laminated on top. The metal core provides excellent thermal conductivity, allowing for efficient heat dissipation from power-generating components. Metal core PCBs are commonly used in high-power applications, such as power supplies, motor drives, and LED lighting.
Advantages of Metal Core:
– High thermal conductivity, enabling efficient heat dissipation
– Improved mechanical strength and rigidity
– Suitable for high-power applications
Disadvantages of Metal Core:
– Higher cost compared to standard FR-4 substrates
– Limited electrical insulation properties due to the metal core
– Requires specialized manufacturing processes
Flexible Substrates (Polyimide, PET)
Flexible substrates, such as polyimide and polyethylene terephthalate (PET), are thin, flexible polymer films that allow for the creation of flexible and conformable PCBs. These substrates are ideal for applications that require flexibility, such as wearable electronics, medical devices, and aerospace systems.
Advantages of Flexible Substrates:
– Flexibility and conformability to various shapes and configurations
– Lightweight and thin, enabling compact and portable designs
– Suitable for applications that require bending, folding, or stretching
Disadvantages of Flexible Substrates:
– Limited thermal conductivity compared to rigid substrates
– Reduced mechanical strength and durability
– Higher cost compared to standard rigid substrates
Selecting the Right PCB Substrate Material
When choosing the appropriate PCB substrate material for your project, consider the following factors:
- Electrical Requirements:
- Dielectric constant and dissipation factor for high-frequency applications
-
Electrical insulation properties for high-voltage applications
-
Thermal Requirements:
- Thermal conductivity for efficient heat dissipation
-
Thermal stability and glass transition temperature for high-temperature applications
-
Mechanical Requirements:
- Mechanical strength and rigidity for demanding environments
-
Flexibility and conformability for applications that require bending or folding
-
Cost and Availability:
- Material cost and its impact on the overall project budget
-
Availability and lead times for the selected substrate material
-
Manufacturing Considerations:
- Compatibility with standard PCB manufacturing processes
- Specialized manufacturing requirements for certain substrate materials
By carefully evaluating these factors and consulting with PCB design and manufacturing experts, you can select the most suitable substrate material for your specific project requirements.
Frequently Asked Questions (FAQ)
- What is the most commonly used PCB substrate material?
-
FR-4 (Flame Retardant 4) is the most widely used PCB substrate material due to its good balance of electrical insulation, mechanical strength, and cost-effectiveness.
-
Which substrate material is best for high-frequency applications?
-
PTFE (Teflon) and low-loss materials like Rogers laminates are preferred for high-frequency applications due to their low dielectric constant and low dissipation factor, which minimize signal loss and ensure signal integrity.
-
What are the advantages of using a metal core substrate?
-
Metal core substrates offer high thermal conductivity, enabling efficient heat dissipation from power-generating components. They also provide improved mechanical strength and rigidity compared to standard FR-4 substrates.
-
Are flexible substrates suitable for all applications?
-
Flexible substrates, such as polyimide and PET, are suitable for applications that require flexibility, conformability, and lightweight design. However, they may have limitations in terms of thermal conductivity, mechanical strength, and durability compared to rigid substrates.
-
How do I select the right PCB substrate material for my project?
- When selecting the appropriate PCB substrate material, consider factors such as electrical requirements (dielectric constant, insulation properties), thermal requirements (conductivity, stability), mechanical requirements (strength, flexibility), cost and availability, and manufacturing considerations. Consult with PCB design and manufacturing experts to make an informed decision based on your specific project needs.
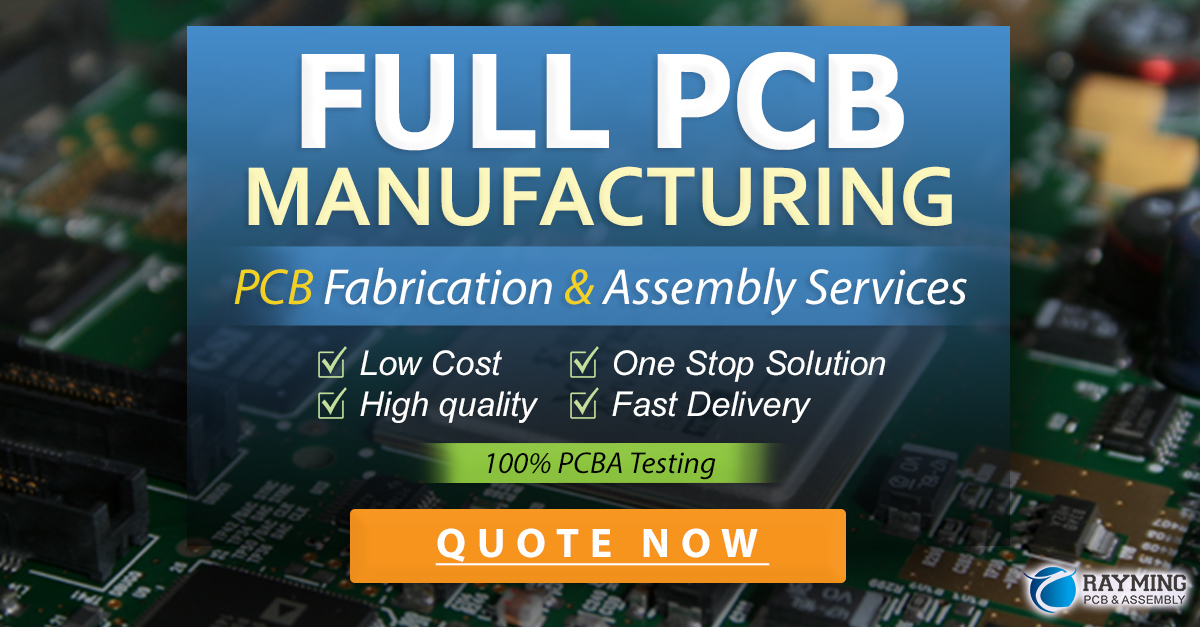
Conclusion
Choosing the right PCB substrate material is a critical aspect of designing and manufacturing reliable and high-performance printed circuit boards. By understanding the characteristics and advantages of various substrate materials, such as FR-4, high Tg FR-4, polyimide, PTFE, ceramic, metal core, and flexible substrates, you can make an informed decision that aligns with your project’s specific requirements.
Consider factors such as electrical properties, thermal performance, mechanical stability, cost, and manufacturing compatibility when selecting the appropriate substrate material. By doing so, you can ensure that your PCB meets the desired performance, reliability, and cost targets, ultimately contributing to the success of your project.
Leave a Reply