Introduction
A flexible printed circuit board (FPCB) is a type of printed circuit board that is made with flexible insulating substrate material. FPCBs are widely used in electronics when reduced thickness and weight, improved reliability, and flexible form factors are required. They are commonly found in consumer electronics, medical devices, automotive electronics, aerospace applications, and more.
As FPCBs become more prevalent across industries, choosing the right flexible PCB manufacturer is crucial to get high-quality and reliable circuit boards tailored to your specific application requirements. In this comprehensive guide, we have compiled a list of the top flexible PCB manufacturers operating globally in 2023.
What is a Flexible Printed Circuit Board?
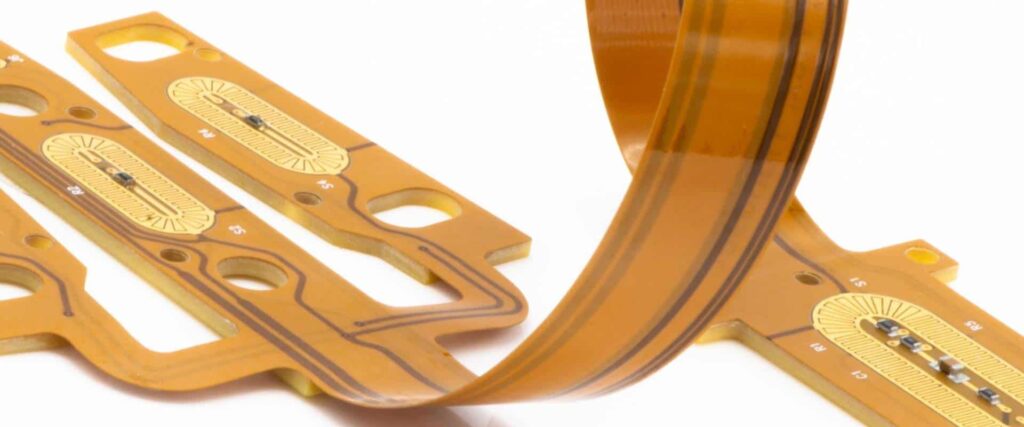
A flexible printed circuit board is composed of thin and flexible dielectric substrate materials such as polyimide or transparent conductive polyester film. The circuit traces are printed or bonded onto this flexible base material using copper foils and specialized adhesives.
FPCBs offer several advantages over traditional rigid PCBs:
- Extremely thin and lightweight – can be bent and folded into 3D configurations
- Improved reliability with flex-to-install connector designs
- Can conform to challenging shapes and small spaces
- Withstand vibration and flexing stresses
- Simplified product assembly and part reductions
Typical applications of FPCBs include:
- Consumer electronics – laptops, mobile phones, wearables
- Automotive electronics
- Medical devices
- Industrial electronics
- Aerospace and military products
Flex Circuit Materials
The flexible materials used in FPCBs include:
- Polyimide – Most common type of flexible PCB material offering high heat resistance. Examples are Kapton® from Dupont and Apical® from Kaneka.
- Polyester – More economical alternative to polyimide. Lower maximum operating temperature.
- Liquid Crystal Polymer (LCP) – Used for highly miniaturized flex circuits requiring excellent electrical performance.
- Fluoropolymers – Specialty flex circuit substrates with resistance to harsh chemicals and extreme temperatures.
Flexible PCB Configurations
Flex circuits can be manufactured in different configurations depending on the application requirements:
- Single-sided – Circuitry on one side of the substrate only
- Double-sided – Circuitry on both sides
- Multilayer – Multiple conductive layers separated by insulating dielectric layers
- Rigid-flex – Combination of rigid and flexible PCB sections
Top 10 Flexible PCB Manufacturers
Here are the top 10 global manufacturers of high-quality flexible printed circuit boards:
1. Flexium Interconnect
- One of the largest flexible PCB manufacturers worldwide
- Founded in 2000, headquartered in Taiwan
- 8 manufacturing plants and over 1000 employees
- Specializes in consumer electronics and automotive applications
- Rigid-flex, high-density interconnects (HDI), and flexible metal core PCBs
- Flexium Flexible Printed Circuits Group, Compeq Manufacturing, and Zhen Ding Tech are subsidiaries
2. Career Technology
- Leading Chinese maker of FPCBs and flexible packaging substrates
- Founded in 1999, based in Taiwan with factories in China
- Products include single, double, and multilayer flex circuits
- Specialized technology for rigid-flex PCBs
- Major customers are consumer electronics, telecommunications, and automotive companies
3. Flex (Flextronics)
- Global EMS company providing design, engineering, manufacturing, and logistics
- Headquartered in Singapore, facilities worldwide
- Makes a wide range of flexible PCBs, rigid-flex, HDI, FPC assemblies
- Expertise in medical, automotive, industrial, aerospace, defense applications
4. Nitto Denko
- Japanese company manufacturing various FPCB types
- Formed in 1918, headquarters in Osaka, plants across Japan, China and Vietnam
- Products include single and double-sided flex circuits and rigid-flex boards
- Supplies Apple, Samsung, Microsoft, Sony, Huawei and other major OEMs
5. Sumitomo Denko Printed Circuits
- Japanese flexible PCB manufacturer part of the Sumitomo Electric Group
- Founded in 1958, head office and plants located in Japan
- Specialized in small-volume, high-mix flex PCB production
- Products include single, double and multilayer FPCBs
- Main end markets are industrial equipment, automotive, and consumer devices
6. Mektec Manufacturing Corporation
- Leading US-based flex PCB manufacturer with operations focused in Asia
- Founded in 2000, headquartered in Florida, factories in Taiwan and China
- Capabilities in rigid, rigid-flex, flex, and metal-based PCBs
- Applications in medical, telecom infrastructure, industrial controls, automotive
7. Interflex
- International flexible circuit provider headquartered in Germany
- Founded in 1970, additional facilities in the USA, India and China
- Diverse industry expertise in automotive, industrial, health care and printing
- Innovative flex technologies like 3D formed flex circuits and heatable flex boards
8. BH FlexIBLE CIRCUITS Pvt Ltd
- Top flexible PCB manufacturer in India serving global customers
- Founded in 1989, state-of-the-art manufacturing facility in Mysore
- Provider of high-quality flex circuits, rigid-flex boards, and flexible heaters
- Production optimised for medium to high volume requirements
- Markets served include medical, telecom, industrial, defense, and aerospace
9. All Flex Flexible Circuits LLC
- Leading maker of flexible circuits boards, cable assemblies, and flex heaters
- Founded in 1989, headquartered in Minnesota USA
- Additional manufacturing sites in Wisconsin and Chihuahua, Mexico
- Custom flex PCB solutions for medical, military, industrial, and commercial applications
- Specializes in fast-turn prototyping and ramp-to-volume production
10. American Standard Circuits
- Full-service PCB company providing rigid, flex, and rigid-flex boards
- Founded in 1964, head office in Illinois, factory in Wisconsin USA
- Flex circuit capabilities include single, double, and multilayer
- Applications in medical, industrial controls, telecom infrastructure and aerospace
- High-volume manufacturer able to scale efficiently
How to Choose A Flexible PCB Manufacturer?
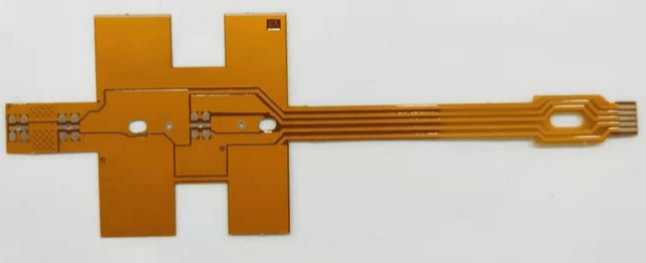
Choosing the right flexible PCB supplier depends on your specific requirements for quality, technology capabilities, industry expertise, volumes, and more. Here are some key factors to consider in your selection process:
1. Technical Capabilities
- Does the manufacturer offer expertise in the flex circuit types you need – single-sided, double-sided, multilayer, rigid-flex?
- Do they have experience producing high complexity flex boards for your industry and application?
- What PCB materials, features and production processes are supported?
- Do they have qualified processes to assure the quality and reliability of flex circuits?
2. Quality Systems
- Is the manufacturer certified to quality standards like ISO 9001, ISO 13485, IPC standards?
- Do they have a comprehensive quality management system and inspection procedures in place?
- What is their defect rate and on-time delivery performance?
- Will they share qualification, reliability test reports and other quality data with customers?
3. Industry Experience
- Does the FPCB company have demonstrated expertise and a customer base in your target industry – medical, automotive, aerospace, etc?
- Do they understand the application requirements and regulations for that industry?
- Can they produce flex boards optimized for the mechanical, electrical, and environmental demands of the end product?
4. Design Support
- Do they offer design review and feedback during the prototype stages?
- Will they recommend flex circuit materials and manufacturing methods best suited for your product?
- Is comprehensive PCB layout and CAD support available?
5. Prototyping and Low Volume Support
- For product development, look for manufacturers that offer rapid prototyping and low volume manufacturing
- What is the minimum order quantity and lead time they can accommodate?
- Do they have in-house engineering support for prototyping?
6. Volume Production Capabilities
- Once in full production, the manufacturer should be able to scale efficiently
- Do they have sufficient production capacity and facilities to meet your forecasted volume?
- Do they use automated assembly processes for higher volumes?
7. Cost Factors
- Flex PCB pricing depends on materials, layer count, complexity, and order quantities
- Make sure to get detailed quotes accounting for all requirements
- Ask about their process for cost optimization without compromising on quality
8. Supply Chain and Logistics
- Look at ease of doing business, communication, and geographic proximity
- What is their purchasing and inventory management system like?
- Can they integrate with your systems and processes?
- Do they have provisions to protect your intellectual property?
Finding the right flexible PCB partner requires research and due diligence across these criteria specific to your needs. But the benefits of a streamlined, high-quality supplier relationship are immense in terms of product quality, development efficiency, and reduced time-to-market.
Flexible PCB Design Considerations
Designing a flex circuit requires accounting for the mechanical, electrical, and manufacturing demands of the end application. Here are some best practices to follow:
- Minimize unsupported spans in traces between attachment points to reduce risk of cracks
- Avoid acute angles bends where traces change directions – use curved corners instead
- Provide strain relief features like slits, darts or corner cutouts in areas prone to flexing
- Use teardrop pads at junctions between plated through holes and conductors
- Select flex laminate materials to withstand expected bending cycles and environmental conditions
- Allow for slightly larger spacing and trace widths compared to rigid boards
- Consult the flex PCB manufacturer during design review to improve manufacturability
Conclusion
Flexible printed circuit boards offer unique advantages for electronics requiring lightweight and dynamic form factors. As FPCB adoption increases across industries, partnering with the right manufacturer becomes critical. This guide summarized the top flex PCB manufacturers providing high-quality, innovative solutions tailored to the needs of customers worldwide. Factors like technical expertise, quality systems, industry experience, prototyping capabilities, volume production and overall value should drive the decision when selecting your ideal flexible circuit board supplier.
FQA
What are the different types of flexible PCBs?
The main types of flexible PCBs are:
- Single-sided – Circuitry on one side only
- Double-sided – Circuitry on both sides
- Multilayer – Multiple circuit layers separated by insulating dielectric
- Rigid-flex – Combination of rigid and flexible circuits
What are some key applications of FPCBs?
Major applications of FPCBs include:
- Consumer electronics – Mobile phones, laptops, wearable devices
- Automotive – Sensors, circuits in steering systems, engine controls
- Medical – Imaging equipment, surgical devices, implants
- Industrial – Robotics joints and arms, controls, monitors
- Military/Aerospace – Guidance systems, communications, avionics
What are the major raw materials used in flex PCBs?
Common flexible PCB substrate materials are:
- Polyimide – Kapton®, Apical®, Upilex®
- Polyester – Melinex®, Teslin®
- Liquid Crystal Polymer (LCP)
- Fluoropolymer Films
Copper foils, adhesives, coverlays, and stiffeners are other components.
Why choose a flex PCB over a rigid PCB?
Advantages of FPCBs include:
- Thin, lightweight, and can flex or conform to shapes
- Can withstand vibration, impacts, and flexing stresses
- Simplified assembly by integrating flexible connections
- Used where space is limited and 3D form factors are required
- Often improve reliability versus connectors between rigid PCBs
How can I reduce costs for my flex PCB project?
Tips for cost reduction:
- Standardize designs across product variants
- Build panel designs to manufacture multiple units in parallel
- Select standard flex materials and adhesive systems
- Reduce layer count where possible
- Consult with manufacturer early regarding design and material choices
- Optimize shipping and logistics
- Negotiate price for high-volume production
Leave a Reply