Introduction to Electrostatic Copper-Spraying in PCB Manufacturing
Electrostatic copper-spraying is a cutting-edge technology that has revolutionized the manufacturing process of thick-copper printed circuit boards (PCBs). This innovative method has gained popularity in recent years due to its ability to produce high-quality, reliable, and cost-effective PCBs with enhanced electrical and thermal properties. In this article, we will delve into the intricacies of electrostatic copper-spraying technology, its advantages over traditional methods, and its applications in various industries.
What is Electrostatic Copper-Spraying?
Electrostatic copper-spraying is a process that involves the deposition of copper onto a substrate using an electrostatic charge. The copper particles are atomized and charged with a high voltage, which causes them to be attracted to the grounded substrate. This results in a uniform and adherent copper layer on the surface of the PCB.
Advantages of Electrostatic Copper-Spraying
- Uniform copper distribution
- Enhanced adhesion
- Increased electrical conductivity
- Improved thermal dissipation
- Cost-effective process
The Electrostatic Copper-Spraying Process
Substrate Preparation
Before the electrostatic copper-spraying process can begin, the substrate must be properly prepared. This involves cleaning the surface to remove any contaminants, followed by the application of a conductive seed layer. The seed layer serves as a foundation for the subsequent copper deposition and ensures adequate adhesion.
Copper Atomization and Charging
The copper used in the electrostatic spraying process is typically in the form of a fine powder. This powder is fed into an atomizer, where it is transformed into a mist of tiny copper particles. These particles are then charged with a high voltage, typically ranging from 30 to 100 kV, using a charging electrode.
Deposition and Consolidation
The charged copper particles are attracted to the grounded substrate, forming a uniform layer on the surface. The thickness of the deposited copper layer can be precisely controlled by adjusting the spraying parameters, such as the powder feed rate, the charging voltage, and the distance between the atomizer and the substrate.
After deposition, the copper layer undergoes a consolidation process to improve its density and adhesion. This is typically achieved through sintering, which involves heating the PCB to a temperature below the melting point of copper, allowing the particles to bond together and form a cohesive layer.
Advantages of Electrostatic Copper-Spraying in PCB Manufacturing
Uniform Copper Distribution
One of the primary advantages of electrostatic copper-spraying is its ability to produce a uniform copper distribution across the entire surface of the PCB. This is achieved through the precise control of the spraying parameters and the electrostatic attraction between the charged copper particles and the grounded substrate. The uniform copper distribution ensures consistent electrical and thermal properties throughout the PCB, reducing the risk of hotspots and improving overall reliability.
Enhanced Adhesion
Electrostatic copper-spraying results in excellent adhesion between the copper layer and the substrate. The high-velocity impact of the charged copper particles on the surface creates a mechanical interlocking effect, which contributes to the strong bond between the two materials. Additionally, the use of a conductive seed layer further enhances the adhesion by providing a suitable surface for the copper particles to bond with.
Increased Electrical Conductivity
The uniform and dense copper layer produced by electrostatic spraying exhibits higher electrical conductivity compared to traditional methods, such as electroplating. This is due to the absence of voids and the tight packing of the copper particles, which allows for efficient electron flow. The increased electrical conductivity is particularly beneficial in applications that require high current-carrying capacity, such as power electronics and automotive systems.
Improved Thermal Dissipation
Thick-Copper PCBs manufactured using electrostatic copper-spraying technology have excellent thermal dissipation properties. The uniform and adherent copper layer provides an effective heat transfer path, allowing for the efficient removal of heat generated by electronic components. This is crucial in applications that generate significant amounts of heat, such as high-power LEDs, power converters, and motor drives. The improved thermal dissipation helps to prevent overheating and enhances the overall reliability and lifespan of the electronic devices.
Cost-Effective Process
Electrostatic copper-spraying is a cost-effective alternative to traditional PCB manufacturing methods, particularly for thick-copper applications. The process requires minimal setup time and can be easily automated, reducing labor costs and increasing production efficiency. Additionally, the high material utilization rate associated with electrostatic spraying minimizes waste, further contributing to cost savings.
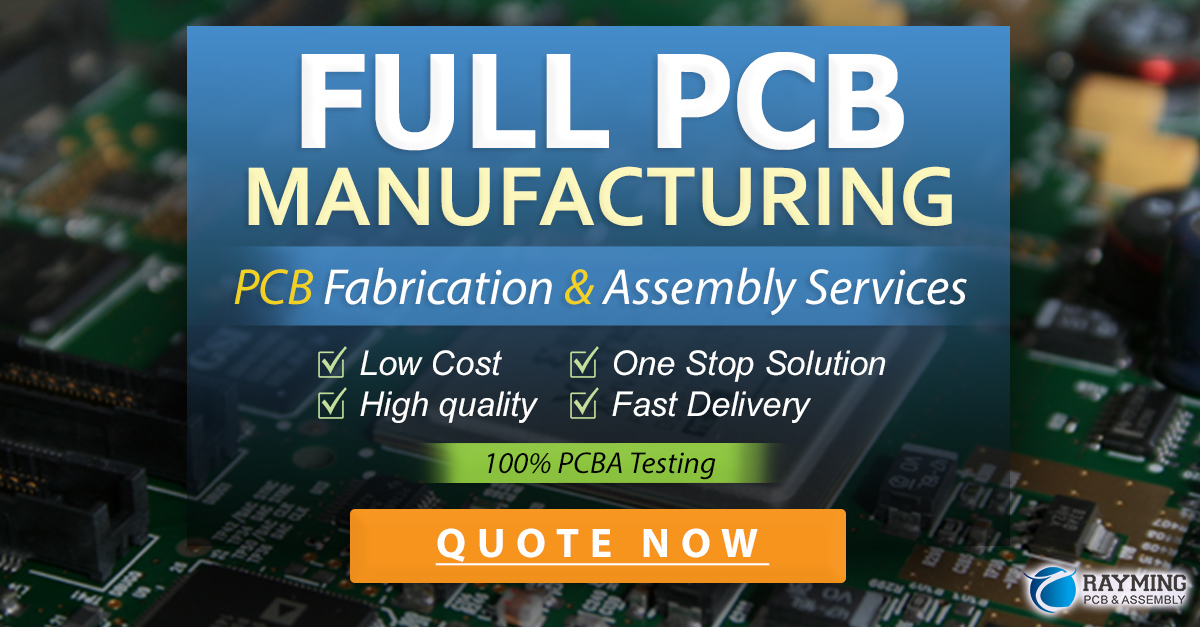
Applications of Electrostatic Copper-Spraying in Various Industries
Automotive Electronics
The automotive industry has increasingly adopted electrostatic copper-spraying technology for the production of high-power electronic components, such as engine control units, power inverters, and battery management systems. The enhanced electrical and thermal properties of thick-copper PCBs manufactured using this technology ensure reliable performance in the demanding automotive environment, where factors such as vibration, temperature extremes, and electrical noise pose significant challenges.
Power Electronics
Power electronic devices, such as switched-mode power supplies, motor drives, and renewable energy systems, rely on thick-copper PCBs to handle high currents and dissipate heat effectively. Electrostatic copper-spraying enables the production of PCBs with the required copper thickness and thermal management capabilities, ensuring efficient and reliable operation of these devices.
LED Lighting
High-power LED lighting applications require PCBs with excellent thermal dissipation properties to prevent overheating and ensure long-term reliability. Electrostatic copper-spraying technology is well-suited for the production of LED PCBs, as it allows for the creation of thick-copper layers with uniform heat distribution. This helps to maintain optimal LED performance and prolongs the lifespan of the lighting system.
Aerospace and Defense
The aerospace and defense industries have stringent requirements for PCB performance and reliability. Electrostatic copper-spraying technology is used to manufacture PCBs for various aerospace and defense applications, such as radar systems, satellite communications, and avionics. The high electrical conductivity and thermal dissipation properties of thick-copper PCBs produced using this technology ensure reliable operation in harsh environments and critical situations.
Future Trends and Developments
As the demand for high-performance electronic devices continues to grow, the adoption of electrostatic copper-spraying technology in PCB manufacturing is expected to increase. Ongoing research and development efforts are focused on further optimizing the process parameters to achieve even better copper distribution, adhesion, and electrical and thermal properties.
One area of interest is the development of advanced copper alloys and composites that can be used in the electrostatic spraying process. These materials could offer enhanced mechanical, electrical, and thermal properties, enabling the production of PCBs with improved performance and reliability.
Another trend is the integration of electrostatic copper-spraying with other advanced manufacturing technologies, such as 3D printing and laser structuring. This could enable the creation of complex, multi-functional PCBs with embedded components, sensors, and interconnects, paving the way for the next generation of electronic devices.
Frequently Asked Questions (FAQ)
-
Q: What is the typical copper thickness achieved with electrostatic copper-spraying?
A: Electrostatic copper-spraying can produce copper layers with thicknesses ranging from 50 to 500 microns, depending on the specific application requirements. -
Q: Can electrostatic copper-spraying be used for Multilayer PCBs?
A: Yes, electrostatic copper-spraying can be used to create multilayer PCBs by repeating the deposition process on each layer and using insulating materials between the layers. -
Q: Is electrostatic copper-spraying suitable for high-volume production?
A: Yes, electrostatic copper-spraying is a highly scalable process that can be automated for high-volume production, making it suitable for industrial-scale PCB manufacturing. -
Q: What is the environmental impact of electrostatic copper-spraying compared to traditional methods?
A: Electrostatic copper-spraying is considered a more environmentally friendly process compared to traditional methods, as it generates less waste and requires fewer chemicals. However, proper safety precautions must be taken to prevent the inhalation of copper particles during the spraying process. -
Q: Can electrostatic copper-spraying be used for Flexible PCBs?
A: Yes, electrostatic copper-spraying can be applied to flexible substrates, such as polyimide or PET, to create flexible PCBs with thick-copper layers. However, the process parameters may need to be adjusted to account for the different material properties.
Conclusion
Electrostatic copper-spraying technology has emerged as a game-changer in the manufacturing of thick-copper PCBs. Its ability to produce uniform, adherent, and highly conductive copper layers has made it an attractive option for various industries, including automotive, power electronics, LED lighting, and aerospace and defense. The advantages of this technology, such as improved electrical and thermal properties, cost-effectiveness, and scalability, have driven its adoption and continued development.
As the electronics industry evolves and the demand for high-performance PCBs grows, electrostatic copper-spraying is poised to play an increasingly important role in enabling the next generation of electronic devices. With ongoing research and advancements in materials and process integration, this technology holds immense potential for shaping the future of PCB manufacturing and powering innovation across various sectors.
Property | Electrostatic Copper-Spraying | Traditional Methods (e.g., Electroplating) |
---|---|---|
Copper distribution | Uniform | Potential for non-uniformity |
Adhesion | Enhanced | Adequate |
Electrical conductivity | High | Moderate |
Thermal dissipation | Excellent | Good |
Process cost | Cost-effective | Higher setup and material costs |
Environmental impact | Lower | Higher chemical usage and waste |
Scalability | High | Moderate |
Leave a Reply