Introduction to LED PCB Assembly
Light-emitting diode (LED) printed circuit boards (PCBs) have revolutionized the lighting industry with their energy efficiency, durability, and versatility. As the demand for LED lighting solutions continues to grow, manufacturers must ensure that their LED PCB Assembly processes are optimized for quality and efficiency. This comprehensive guide will explore the intricacies of LED PCB assembly and provide insights into common defects and their analysis.
What is an LED PCB?
An LED PCB is a specialized printed circuit board designed to support and connect LED components. These boards are engineered to dissipate heat efficiently, ensure proper electrical connections, and maintain the overall stability of the LED lighting system. LED PCBs can be found in a wide range of applications, from automotive lighting to indoor and outdoor illumination.
Advantages of LED PCBs
Compared to traditional lighting solutions, LED PCBs offer several advantages:
- Energy efficiency: LEDs consume significantly less power than incandescent or fluorescent bulbs, resulting in lower energy costs.
- Longevity: With proper thermal management, LEDs can last up to 50,000 hours or more, reducing maintenance and replacement costs.
- Versatility: LED PCBs can be customized to fit various form factors and designed for specific lighting requirements.
- Environmentally friendly: LEDs contain no toxic materials and are recyclable, making them a more sustainable lighting option.
LED PCB Assembly Process
The LED PCB assembly process involves several critical steps to ensure the proper functioning and longevity of the final product. Understanding these steps is essential for identifying and preventing potential defects.
PCB Design and Fabrication
The first step in LED PCB assembly is designing and fabricating the printed circuit board. Key considerations during this stage include:
- Material selection: Choosing the appropriate PCB substrate material, such as FR-4 or Metal-Core PCBs (MCPCBs), based on thermal management and application requirements.
- Copper thickness: Determining the optimal copper thickness for efficient current flow and heat dissipation.
- Solder mask and silkscreen: Applying solder mask and silkscreen layers to protect the board and provide clear component labeling.
Once the PCB design is finalized, the board is fabricated using a combination of etching, drilling, and plating processes.
LED Component Selection
Selecting the right LED components is crucial for achieving the desired lighting performance and ensuring compatibility with the PCB design. Factors to consider include:
- Lumen output: Choosing LEDs with the appropriate lumen output for the intended application.
- Color temperature: Selecting LEDs with the desired color temperature (measured in Kelvin) to achieve the intended mood or atmosphere.
- Forward voltage and current: Ensuring that the selected LEDs have compatible forward voltage and current ratings with the PCB design and power supply.
Surface Mount Technology (SMT) Assembly
Surface mount technology (SMT) is the most common method for assembling LED PCBs. The SMT process involves the following steps:
- Solder paste application: Applying solder paste to the PCB pads using a stencil or solder paste printer.
- LED placement: Placing the LED components onto the PCB using a pick-and-place machine or manual assembly methods.
- Reflow soldering: Passing the PCB through a reflow oven, which melts the solder paste and creates a permanent electrical and mechanical connection between the LEDs and the PCB.
Through-Hole Technology (THT) Assembly
Some LED PCBs may require through-hole technology (THT) assembly, particularly for larger components or connectors. THT assembly involves the following steps:
- Component insertion: Manually inserting the LED components or connectors into the pre-drilled holes on the PCB.
- Wave soldering: Passing the PCB over a molten solder wave, which creates a connection between the component leads and the PCB pads.
Inspection and Testing
After the LED PCB assembly process is complete, the boards undergo thorough inspection and testing to ensure proper functionality and identify any potential defects. Common inspection and testing methods include:
- Visual inspection: Examining the PCB for visible defects such as solder bridges, component misalignment, or damaged components.
- Automated optical inspection (AOI): Using machine vision systems to detect surface-level defects and component placement issues.
- X-ray inspection: Employing X-ray imaging to detect hidden defects, such as voids in solder joints or component failures.
- Functional testing: Powering on the LED PCB and verifying proper light output, color consistency, and overall performance.
Common LED PCB Assembly Defects and Analysis
Despite advancements in LED PCB assembly processes, defects can still occur, leading to reduced performance or complete failure of the lighting system. Identifying and analyzing these defects is essential for implementing corrective actions and improving the overall quality of LED PCBs.
Solder Joint Defects
Solder joint defects are among the most common issues encountered in LED PCB assembly. These defects can compromise the electrical and mechanical integrity of the connection between the LED component and the PCB. Common solder joint defects include:
- Solder bridges: Unintended connections between two or more solder pads, caused by excess solder or improper solder mask application.
- Cold solder joints: Weak, dull-looking solder joints resulting from insufficient heat or contamination during the soldering process.
- Solder voids: Gaps or pockets within the solder joint, which can increase electrical resistance and lead to premature failure.
- Tombstoning: When an LED component stands up on one end due to uneven heating or surface tension during the reflow soldering process.
Solder joint defects can be analyzed using visual inspection, X-ray imaging, or cross-sectional analysis. Corrective actions may include adjusting solder paste volume, optimizing reflow oven temperature profiles, or improving PCB design to minimize the risk of defects.
LED Component Defects
LED component defects can occur due to manufacturing issues, improper handling, or incompatibility with the PCB design. Common LED component defects include:
- LED chip failures: When the LED chip itself fails due to manufacturing defects or excessive electrical stress.
- Phosphor degradation: Gradual deterioration of the phosphor coating, resulting in color shift or reduced light output over time.
- Lens or encapsulant damage: Physical damage to the LED lens or encapsulant, which can affect light distribution and protection from environmental factors.
LED component defects can be analyzed using visual inspection, light output measurements, and color consistency testing. Corrective actions may involve improving LED component quality control, optimizing PCB design for better thermal management, or implementing more robust handling and assembly processes.
PCB Substrate Defects
PCB substrate defects can impact the overall performance and reliability of the LED lighting system. Common PCB substrate defects include:
- Delamination: Separation of the PCB Layers due to poor bonding or excessive thermal stress.
- Warping or bending: Distortion of the PCB due to uneven thermal expansion or improper handling during assembly.
- Copper trace defects: Issues with the copper traces, such as thinning, cracking, or oxidation, which can increase electrical resistance or cause open circuits.
PCB substrate defects can be analyzed using visual inspection, cross-sectional analysis, or thermal imaging. Corrective actions may include selecting higher-quality PCB materials, optimizing the PCB design for better thermal management, or improving handling and storage procedures.
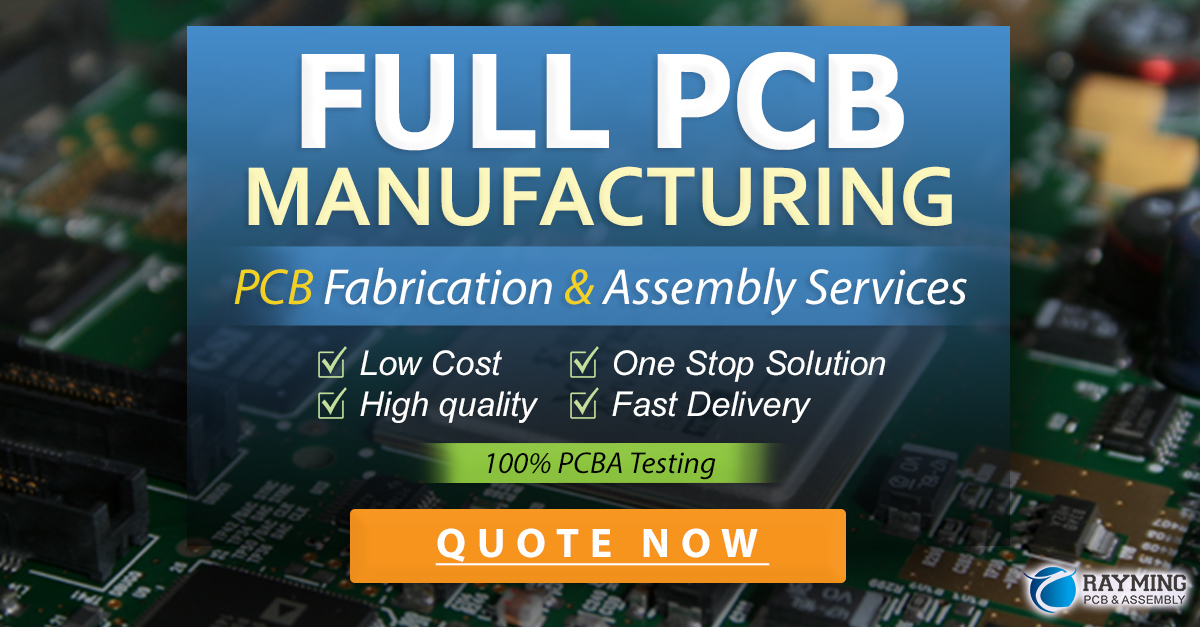
Table: Summary of LED PCB Assembly Defects and Analysis Techniques
Defect Category | Common Defects | Analysis Techniques | Corrective Actions |
---|---|---|---|
Solder Joint Defects | – Solder bridges – Cold solder joints – Solder voids – Tombstoning |
– Visual inspection – X-ray imaging – Cross-sectional analysis |
– Adjust solder paste volume – Optimize reflow oven temperature profiles – Improve PCB design |
LED Component Defects | – LED chip failures – Phosphor degradation – Lens or encapsulant damage |
– Visual inspection – Light output measurements – Color consistency testing |
– Improve LED component quality control – Optimize PCB design for better thermal management – Implement more robust handling and assembly processes |
PCB Substrate Defects | – Delamination – Warping or bending – Copper trace defects |
– Visual inspection – Cross-sectional analysis – Thermal imaging |
– Select higher-quality PCB materials – Optimize PCB design for better thermal management – Improve handling and storage procedures |
Best Practices for Minimizing LED PCB Assembly Defects
To minimize the occurrence of defects in LED PCB assembly, manufacturers should adhere to the following best practices:
- Robust PCB design: Ensure that the PCB design is optimized for thermal management, electrical performance, and manufacturability. This includes selecting appropriate materials, copper thicknesses, and component placement.
- Quality component selection: Source high-quality LED components from reputable suppliers and ensure that they are compatible with the PCB design and application requirements.
- Process control and optimization: Implement strict process controls and continuously monitor and optimize assembly processes, such as solder paste application, reflow soldering, and inspection.
- Training and skill development: Invest in training and skill development for assembly operators and quality control personnel to ensure consistent and accurate assembly practices.
- Continuous improvement: Regularly analyze defect data and implement corrective actions to address the root causes of defects and drive continuous improvement in LED PCB assembly quality.
Frequently Asked Questions (FAQ)
- What is the difference between SMT and THT LED PCB assembly?
-
SMT (Surface Mount Technology) assembly involves placing LED components directly onto the surface of the PCB and using reflow soldering to create electrical and mechanical connections. THT (Through-Hole Technology) assembly requires inserting LED components or connectors through pre-drilled holes in the PCB and using wave soldering to create connections.
-
How can I improve the thermal management of my LED PCB?
-
To improve thermal management, consider using metal-core PCBs (MCPCBs) or incorporating thermal vias to dissipate heat more efficiently. Additionally, ensure proper component placement and use thermal interface materials (TIMs) to enhance heat transfer between the LED components and the PCB substrate.
-
What are the most common causes of solder joint defects in LED PCB assembly?
-
Common causes of solder joint defects include improper solder paste application, incorrect reflow oven temperature profiles, PCB design issues (such as inadequate pad size or spacing), and contamination during the soldering process.
-
How can I detect hidden defects in LED PCBs, such as solder voids or component failures?
-
X-ray inspection is a powerful tool for detecting hidden defects in LED PCBs. X-ray imaging can reveal solder voids, component failures, and other issues that may not be visible through visual inspection alone.
-
What steps can I take to minimize LED component defects in my assembly process?
- To minimize LED component defects, source components from reputable suppliers with strong quality control processes. Ensure that the components are compatible with your PCB design and assembly process, and implement robust handling and storage procedures to prevent physical damage. Additionally, consider conducting incoming quality inspections to identify any defective components before they enter the assembly process.
Conclusion
LED PCB assembly is a complex process that requires careful attention to design, component selection, and manufacturing processes to ensure the production of high-quality, reliable LED lighting systems. By understanding the common defects that can occur during assembly and employing appropriate analysis techniques and corrective actions, manufacturers can minimize the occurrence of defects and improve the overall quality of their LED PCBs.
Implementing best practices, such as robust PCB design, quality component selection, process control and optimization, training and skill development, and continuous improvement, can further enhance the efficiency and effectiveness of LED PCB assembly operations. As the demand for LED lighting solutions continues to grow, mastering the art and science of LED PCB assembly will be critical for manufacturers seeking to remain competitive in this dynamic industry.
Leave a Reply