Understanding PCB Layers
Before diving into the comparison between 2 layer and 4 layer PCBs, let’s first understand what PCB layers are and their significance.
What are PCB Layers?
PCB layers refer to the number of conductive copper layers within a PCB. These layers are used to route electrical signals and power between components on the board. The layers are separated by insulating material, typically FR-4, which is a glass-reinforced epoxy laminate.
Significance of PCB Layers
The number of layers in a PCB directly impacts several aspects of the board’s design and performance:
- Signal Integrity: More layers allow for better signal routing and reduced electromagnetic interference (EMI).
- Power Distribution: Additional layers can be dedicated to power and ground planes, providing stable power distribution.
- Routing Density: Increased layers offer more space for routing traces, enabling higher component density and complex designs.
- Cost: Generally, the more layers a PCB has, the higher the manufacturing cost.
2 Layer PCB
A 2 layer PCB consists of two conductive copper layers, one on the top and one on the bottom of the board. The top layer is typically used for component placement and signal routing, while the bottom layer is used for additional routing and ground planes.
Advantages of 2 Layer PCB
- Lower Cost: 2 layer PCBs are generally less expensive to manufacture compared to multi-layer boards.
- Simpler Design: With fewer layers, the design process is simpler and less time-consuming.
- Easier Fabrication: 2 layer PCBs are easier to fabricate and have shorter lead times.
- Suitable for Simple Circuits: For projects with low complexity and fewer components, 2 layer PCBs are often sufficient.
Disadvantages of 2 Layer PCB
- Limited Routing Space: With only two layers, routing can become challenging in complex designs or high-density layouts.
- Signal Integrity Challenges: 2 layer PCBs are more susceptible to crosstalk and electromagnetic interference (EMI).
- Power Distribution Limitations: Limited layers restrict the ability to create dedicated power and ground planes, which can impact power stability.
Applications of 2 Layer PCB
2 layer PCBs are commonly used in the following applications:
- Simple consumer electronics
- Low-speed digital circuits
- Prototype designs
- Cost-sensitive projects
4 Layer PCB
A 4 layer PCB consists of four conductive copper layers, with two layers on the top and two layers on the bottom of the board. The inner layers are typically used for power and ground planes, while the outer layers are used for component placement and signal routing.
Advantages of 4 Layer PCB
- Improved Signal Integrity: The additional layers allow for better signal routing and shielding, reducing crosstalk and EMI.
- Enhanced Power Distribution: Dedicated power and ground planes provide stable and low-impedance power distribution.
- Increased Routing Density: With more layers available, complex designs and high-density layouts can be accommodated.
- Better Thermal Management: The inner layers can help dissipate heat more effectively, improving thermal performance.
Disadvantages of 4 Layer PCB
- Higher Cost: 4 layer PCBs are more expensive to manufacture compared to 2 layer boards.
- Longer Lead Times: The fabrication process for 4 layer PCBs is more complex and time-consuming.
- Design Complexity: Designing a 4 layer PCB requires more expertise and effort to ensure proper signal integrity and layer stackup.
Applications of 4 Layer PCB
4 layer PCBs are commonly used in the following applications:
- High-speed digital circuits
- RF and wireless designs
- Microcontroller and FPGA-based systems
- Automotive and aerospace electronics
- Medical devices
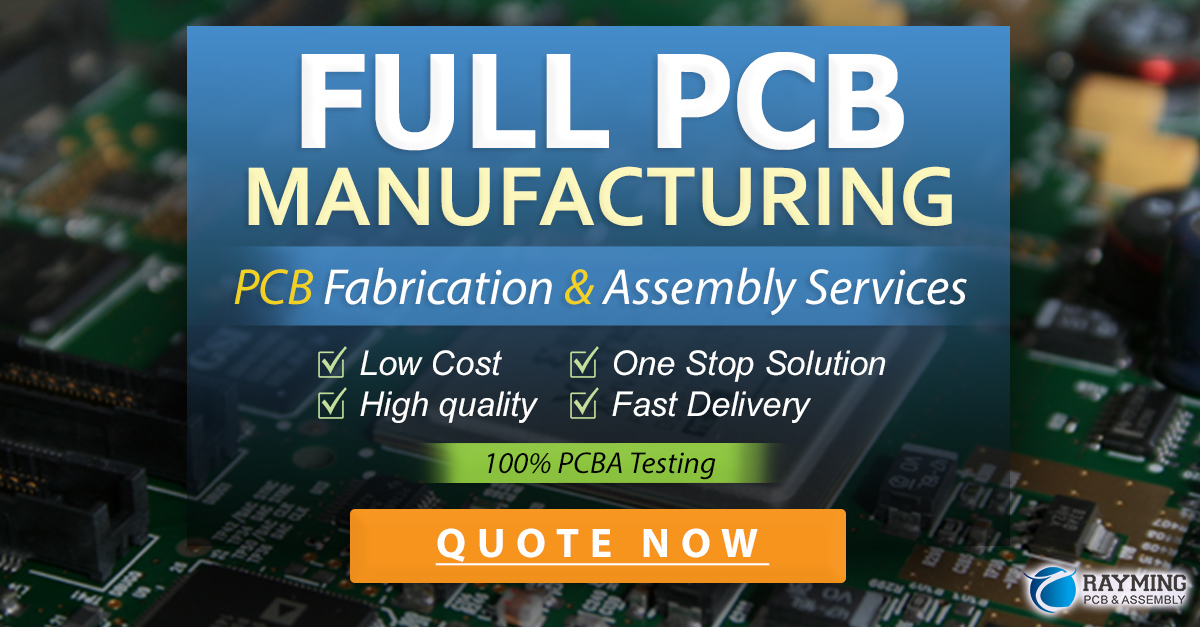
Factors to Consider When Choosing Between 2 Layer and 4 Layer PCB
When deciding between a 2 layer and 4 layer PCB, several factors should be taken into account:
Circuit Complexity
The complexity of your circuit design is a crucial factor in determining the appropriate number of layers. If your design has a high component count, dense routing requirements, or complex signal paths, a 4 layer PCB may be necessary to accommodate these needs. On the other hand, if your circuit is relatively simple with fewer components and straightforward routing, a 2 layer PCB may suffice.
Signal Integrity Requirements
Consider the signal integrity requirements of your design. If your circuit involves high-speed signals, sensitive analog circuits, or is susceptible to electromagnetic interference (EMI), a 4 layer PCB is often the better choice. The additional layers in a 4 layer PCB allow for dedicated power and ground planes, which provide better shielding and reduce noise coupling. The inner layers can also be used for controlled impedance routing, enhancing signal integrity.
Power Distribution Needs
Evaluate the power distribution requirements of your circuit. If your design has multiple power domains or requires stable and low-impedance power delivery, a 4 layer PCB is advantageous. The dedicated power and ground planes in a 4 layer PCB offer better power distribution and reduce voltage drops across the board. This is especially important for circuits with high current demands or sensitive analog components.
Board Size and Layer Count Constraints
Consider the physical size constraints of your PCB. If your design requires a compact form factor, a 2 layer PCB may be more suitable as it allows for thinner Board Thickness. However, if the board size is not a primary concern and you have the flexibility to accommodate a thicker board, a 4 layer PCB can provide more routing space and better signal integrity.
Cost and Budget Considerations
Cost is always a significant factor in any design decision. 2 layer PCBs are generally less expensive to manufacture compared to 4 layer PCBs. The additional layers in a 4 layer PCB require more materials, processing steps, and time, resulting in higher fabrication costs. If your project has a tight budget or is cost-sensitive, a 2 layer PCB may be the more economical choice. However, it’s essential to balance cost with the other factors discussed above to ensure the overall functionality and reliability of your design.
Manufacturing Capabilities and Lead Times
Consider the manufacturing capabilities of your chosen PCB fabricator and the lead times associated with different layer counts. Some manufacturers may have quicker turnaround times for 2 layer PCBs compared to 4 layer PCBs. Additionally, ensure that your fabricator has the necessary capabilities and expertise to handle the complexity of your design, especially if you opt for a 4 layer PCB with specific requirements such as controlled impedance or tight tolerances.
Future Scalability and Upgradability
Think about the future scalability and upgradability of your design. If you anticipate the need for future enhancements, additional features, or increased functionality, a 4 layer PCB may provide more flexibility. The extra layers can accommodate future additions or modifications without requiring a complete redesign. On the other hand, if your design is unlikely to change significantly over time, a 2 layer PCB may be sufficient.
PCB Layer Stackup Considerations
When deciding between a 2 layer and 4 layer PCB, it’s important to consider the layer stackup and its impact on the overall performance of your design.
2 Layer PCB stackup
A typical 2 layer PCB stackup consists of the following layers:
- Top Layer (Signal and Component Placement)
- Dielectric Material (FR-4)
- Bottom Layer (Signal and Ground Plane)
In a 2 layer stackup, the top layer is primarily used for component placement and signal routing, while the bottom layer serves as a ground plane and provides additional routing space. The dielectric material separates the two conductive layers.
4 Layer PCB Stackup
A common 4 layer PCB stackup consists of the following layers:
- Top Layer (Signal and Component Placement)
- Dielectric Material (FR-4)
- Inner Layer 1 (Ground Plane)
- Dielectric Material (FR-4)
- Inner Layer 2 (Power Plane)
- Dielectric Material (FR-4)
- Bottom Layer (Signal and Component Placement)
In a 4 layer stackup, the top and bottom layers are used for component placement and signal routing, while the inner layers are dedicated to power and ground planes. The power plane provides a low-impedance path for power distribution, while the ground plane serves as a reference for signals and helps reduce EMI.
Stackup Considerations for Signal Integrity
The layer stackup plays a crucial role in maintaining signal integrity. Here are some considerations:
-
Controlled Impedance: In a 4 layer PCB, the inner layers can be used for controlled impedance routing. By carefully designing the trace width, thickness, and spacing in relation to the dielectric material, you can achieve the desired characteristic impedance for your signals. This is particularly important for high-speed designs to minimize reflections and ensure proper signal termination.
-
Crosstalk Reduction: By strategically placing signal traces on different layers and using proper spacing and shielding techniques, you can minimize crosstalk between signals. In a 4 layer PCB, the ground and power planes act as shields, reducing the coupling between signals on different layers.
-
Power Plane Placement: In a 4 layer PCB, the power plane should be placed close to the ground plane to minimize the loop area and reduce inductance. This helps provide a low-impedance path for power distribution and minimizes voltage drops across the board.
FAQs
1. What is the cost difference between a 2 layer and 4 layer PCB?
The cost difference between a 2 layer and 4 layer PCB can vary depending on factors such as the PCB Size, quantity, and manufacturer. On average, a 4 layer PCB can cost 20-50% more than a comparable 2 layer PCB. However, the exact cost difference should be determined by requesting quotes from PCB fabricators based on your specific design requirements.
2. Can I use a 2 layer PCB for high-speed designs?
While it is possible to use a 2 layer PCB for high-speed designs, it may not be the optimal choice. High-speed signals are more susceptible to signal integrity issues such as crosstalk, EMI, and impedance mismatches. A 4 layer PCB offers better signal routing options, shielding, and controlled impedance, making it more suitable for high-speed designs. However, if the high-speed signals are localized and proper design techniques are employed, a 2 layer PCB may still be viable.
3. How does the layer count affect the thickness of the PCB?
The layer count directly affects the thickness of the PCB. Each additional layer requires an additional dielectric material and copper foil, increasing the overall thickness of the board. A typical 2 layer PCB has a thickness of around 1.6mm, while a 4 layer PCB can have a thickness of approximately 2.4mm or more. The exact thickness will depend on the specific dielectric material and copper weights used in the PCB stackup.
4. Can I mix signal and power/ground layers in a 4 layer PCB?
In a 4 layer PCB, it is common to dedicate the inner layers to power and ground planes, while the outer layers are used for signal routing and component placement. Mixing signal and power/ground layers is generally not recommended as it can lead to signal integrity issues and increased noise coupling. However, in certain cases, such as when using split power planes or creating local power/ground areas, mixed layers may be used with careful design considerations.
5. How do I determine the appropriate layer count for my design?
To determine the appropriate layer count for your design, consider the following factors:
- Circuit complexity and component count
- Signal integrity requirements
- Power distribution needs
- Board size constraints
- Cost and budget limitations
- Manufacturing capabilities and lead times
- Future scalability and upgradability
Evaluate each factor in the context of your specific design requirements and constraints. If your design has high complexity, strict signal integrity requirements, or demanding power distribution needs, a 4 layer PCB is often the preferred choice. For simpler designs with fewer constraints, a 2 layer PCB may be sufficient.
Layer Selection Table
Here is a quick reference table to help you compare 2 layer and 4 layer PCBs:
Factor | 2 Layer PCB | 4 Layer PCB |
---|---|---|
Cost | Lower | Higher |
Design Complexity | Simpler | More complex |
Signal Integrity | Limited | Improved |
Power Distribution | Limited | Enhanced |
Routing Density | Lower | Higher |
Manufacturing Time | Shorter | Longer |
Suitable Applications | Simple circuits, prototypes | High-speed designs, complex circuits |
Conclusion
Choosing between a 2 layer and 4 layer PCB depends on various factors such as circuit complexity, signal integrity requirements, power distribution needs, board size constraints, cost considerations, and manufacturing capabilities. 2 layer PCBs are generally more cost-effective and suitable for simpler designs, while 4 layer PCBs offer improved signal integrity, better power distribution, and higher routing density, making them ideal for complex and high-speed designs.
To make an informed decision, carefully evaluate your design requirements, budget, and manufacturing constraints. Consider the current needs of your project as well as any future scalability or upgradability requirements. By understanding the advantages and disadvantages of each option and considering the factors discussed in this article, you can select the appropriate layer count for your PCB design.
Remember, the choice between a 2 layer and 4 layer PCB is not always straightforward, and there may be cases where a mix of both or even higher layer counts is necessary. Consult with experienced PCB designers and manufacturers to get their insights and recommendations based on your specific project requirements.
Ultimately, the goal is to strike a balance between performance, reliability, and cost-effectiveness while ensuring that your PCB meets the functional and quality standards required for your application.
Leave a Reply