The PCB Manufacturing Process Overview
The PCB manufacturing process can be broken down into several key steps:
- PCB Design
- PCB Fabrication
- Inner Layer Processing
- Outer Layer Processing
- Solder Mask Application
- Silkscreen Application
- PCB Assembly
- Component Placement
- Soldering
- Inspection and Testing
- Final Inspection and Packaging
Let’s dive into each of these steps in more detail.
PCB Design
The first step in the PCB manufacturing process is design. This is where the layout and functionality of the PCB are determined. PCB designers use specialized software to create a digital representation of the board, including the placement of components, traces, and vias.
Some key considerations during the PCB design phase include:
- Component selection and placement
- Signal integrity
- Power distribution
- Thermal management
- Manufacturing constraints
Once the design is finalized, it is sent to the PCB fabrication house for manufacturing.
PCB Fabrication
PCB fabrication is the process of turning the digital design into a physical board. This is done through a series of chemical and mechanical processes.
Inner Layer Processing
The first step in PCB fabrication is inner layer processing. This is where the conductive copper layers that form the inner layers of the PCB are created.
- A thin layer of copper is laminated onto a substrate material, typically FR-4 glass epoxy.
- The copper is then coated with a photoresist material.
- The photoresist is exposed to light through a photomask, which hardens the exposed areas.
- The unexposed photoresist is then removed, leaving behind a pattern of copper traces.
- The copper is then etched away, leaving only the desired traces behind.
This process is repeated for each inner layer of the PCB.
Outer Layer Processing
Once the inner layers are complete, the outer layers are added.
- The inner layers are laminated together with prepreg, a type of insulating material.
- Copper foil is then laminated onto the top and bottom of the stack.
- The copper is then patterned and etched using a similar process to the inner layers.
- Holes are drilled through the board to create vias, which connect the different layers of the PCB.
- The holes are then plated with copper to create electrical connections between layers.
Solder Mask Application
After the outer layers are complete, a solder mask is applied to the PCB. This is a protective coating that prevents solder from bridging between traces and components during assembly.
- The solder mask is applied as a liquid or film.
- It is then exposed to light through a photomask, which hardens the exposed areas.
- The unexposed solder mask is then removed, leaving behind a protective coating over the copper traces.
Silkscreen Application
The final step in PCB fabrication is the application of the silkscreen. This is a layer of text and symbols that is printed onto the PCB to aid in assembly and troubleshooting.
- The silkscreen is applied as a ink or paste.
- It is then cured, typically through exposure to heat or UV light.
With the silkscreen applied, the PCB fabrication process is complete.
PCB Assembly
Once the PCB is fabricated, it is ready for assembly. This is where the components are attached to the board and soldered in place.
Component Placement
The first step in PCB assembly is component placement. This is typically done using automated pick-and-place machines, which can place hundreds of components per minute with high accuracy.
- The components are loaded into the machine, typically on reels or trays.
- The machine picks up each component using a vacuum nozzle and places it onto the PCB in the correct location.
- The components are then held in place with a small amount of solder paste.
Soldering
After the components are placed, the PCB is run through a reflow oven. This melts the solder paste, permanently attaching the components to the board.
- The PCB is heated to a specific temperature profile, which activates the flux in the solder paste and melts the solder.
- The solder then cools and solidifies, creating a permanent electrical and mechanical connection between the components and the PCB.
Inspection and Testing
After soldering, the PCB undergoes a series of inspections and tests to ensure that it is functioning correctly.
- Automated optical inspection (AOI) machines scan the PCB for any visible defects, such as missing components or solder bridges.
- In-circuit testing (ICT) is then used to verify the electrical functionality of the board.
- Functional testing may also be performed to ensure that the PCB performs as intended in its final application.
Any defects or issues found during inspection and testing are corrected before the PCB moves on to final assembly.
Final Inspection and Packaging
The final step in the PCB manufacturing process is inspection and packaging.
- The PCB undergoes a final visual inspection to ensure that it meets all quality standards.
- It is then packaged for shipping, typically in ESD (electrostatic discharge) safe bags or containers to prevent damage during transport.
With this, the PCB is complete and ready to be shipped to the customer.
PCB Manufacturing Equipment
The PCB manufacturing process relies on a variety of specialized equipment. Some of the key pieces of equipment used in PCB manufacturing include:
Equipment | Function |
---|---|
Laminator | Bonds the layers of the PCB together under heat and pressure. |
Exposure System | Exposes the photoresist to light to create the desired pattern. |
Etching Machine | Removes the unwanted copper from the PCB, leaving only the desired traces. |
Drill Machine | Drills the holes in the PCB for vias and through-hole components. |
Plating Machine | Plates the holes and surface of the PCB with copper, tin, or other metals. |
Pick-and-Place Machine | Automatically places components onto the PCB. |
Reflow Oven | Melts the solder paste to permanently attach the components to the PCB. |
AOI Machine | Automatically inspects the PCB for visible defects. |
ICT Machine | Performs in-circuit testing to verify the electrical functionality of the PCB. |
Each of these machines plays a critical role in the PCB manufacturing process, and the specific machines used can vary depending on the complexity and requirements of the PCB being manufactured.
PCB Manufacturing Materials
In addition to the equipment, PCB manufacturing also relies on a variety of specialized materials. Some of the key materials used in PCB manufacturing include:
Material | Function |
---|---|
Copper Clad Laminate (CCL) | The base material for the PCB, typically made of FR-4 glass epoxy with a layer of copper on one or both sides. |
Prepreg | A pre-impregnated glass fiber material used to bond the layers of the PCB together. |
Solder Mask | A protective coating applied to the PCB to prevent solder from bridging between traces and components. |
Silkscreen Ink | An ink used to print text and symbols onto the PCB for assembly and troubleshooting. |
Solder Paste | A mixture of tiny solder balls and flux used to attach components to the PCB during assembly. |
The quality and characteristics of these materials can have a significant impact on the final quality and reliability of the PCB.
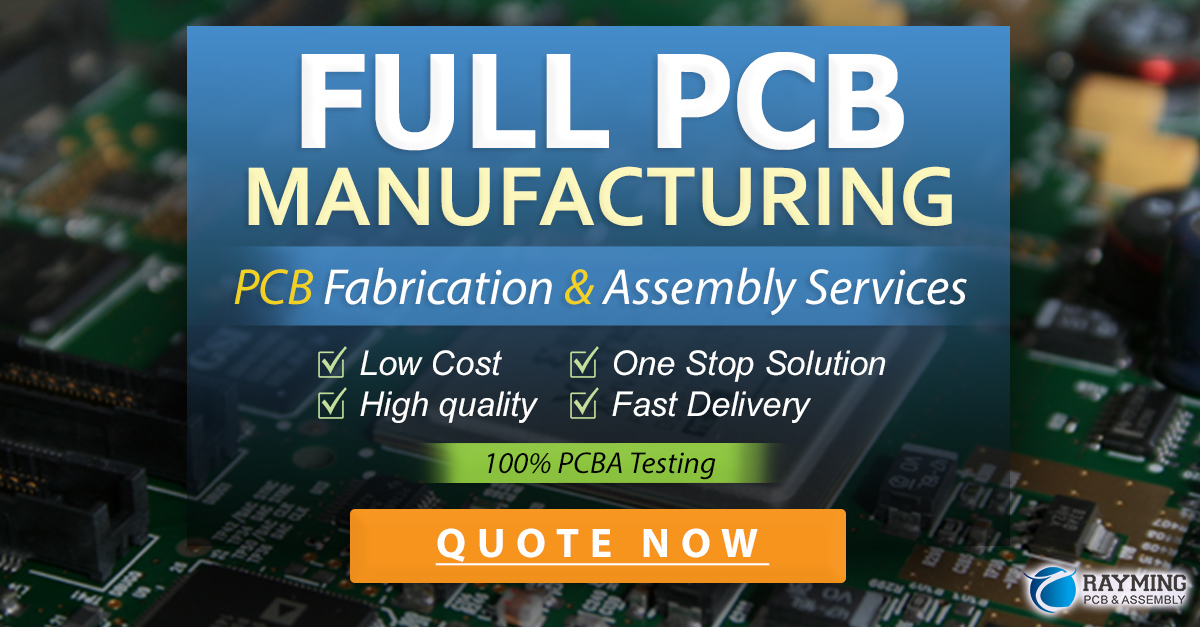
PCB Manufacturing Standards
PCB manufacturing is governed by a variety of industry standards that ensure consistency and reliability across different manufacturers. Some of the key standards in PCB manufacturing include:
- IPC-A-600: Acceptability of Printed Boards
- IPC-6011: Generic Performance Specification for Printed Boards
- IPC-6012: Qualification and Performance Specification for Rigid Printed Boards
- IPC-A-610: Acceptability of Electronic Assemblies
These standards define the criteria for acceptable PCBs and assemblies, including aspects such as hole size, trace width, solder mask coverage, and component placement.
Frequently Asked Questions (FAQ)
-
Q: How long does it take to manufacture a PCB?
A: The time it takes to manufacture a PCB can vary depending on the complexity of the board and the quantity being produced. Simple, low-volume PCBs can be manufactured in a few days, while complex, high-volume PCBs can take several weeks. -
Q: What is the minimum trace width and spacing for a PCB?
A: The minimum trace width and spacing depends on the capabilities of the PCB manufacturer and the requirements of the design. Typical minimum trace widths range from 3 to 6 mils (0.003 to 0.006 inches), while minimum spacing ranges from 3 to 8 mils. -
Q: What is the difference between through-hole and surface-mount components?
A: Through-hole components have leads that are inserted into holes drilled in the PCB and soldered in place. Surface-mount components are attached directly to the surface of the PCB using solder paste. Surface-mount components are smaller and allow for higher component density, but through-hole components are still used for certain applications. -
Q: Can PCBs be manufactured with different colors?
A: Yes, PCBs can be manufactured with different solder mask and silkscreen colors. Green is the most common solder mask color, but other colors such as red, blue, yellow, and black are also available. White is the most common silkscreen color, but other colors can be used as well. -
Q: What is the typical turnaround time for PCB Prototypes?
A: The turnaround time for PCB Prototypes can vary depending on the manufacturer and the complexity of the design. Many PCB manufacturers offer expedited prototype services, with turnaround times as short as 24 hours for simple designs. More complex designs may take several days or longer.
Conclusion
PCB manufacturing is a complex process that involves a variety of specialized equipment, materials, and processes. From design to final assembly, each step in the process plays a critical role in ensuring the quality and reliability of the final product.
By understanding the PCB manufacturing process, designers and engineers can make informed decisions about their designs and work more effectively with their manufacturing partners. And for anyone who uses electronic devices, understanding how PCBs are made can provide a deeper appreciation for the complexity and ingenuity that goes into the technology we rely on every day.
Leave a Reply