What is Copper Clad?
Copper clad, also known as copper-clad laminate (CCL) or printed circuit board (PCB) laminate, is a composite material that consists of a non-conductive substrate bonded with a thin layer of copper on one or both sides. The copper layer serves as a conductive surface for electrical connections, while the substrate provides mechanical support and insulation.
The most common substrates used in copper clad include:
- FR-4: A glass-reinforced epoxy laminate, widely used in PCB manufacturing due to its excellent mechanical and electrical properties.
- CEM-1/CEM-3: Composite epoxy materials that offer a cost-effective alternative to FR-4 for less demanding applications.
- Polyimide: A high-performance substrate that can withstand extreme temperatures and harsh environments.
- PTFE: A low-loss, high-frequency substrate often used in RF and microwave applications.
The thickness of the copper layer can vary depending on the intended application, ranging from 0.5 oz/ft² (17 μm) to 4 oz/ft² (140 μm) or more.
Properties of Copper Clad
Copper clad possesses a unique combination of properties that make it an ideal choice for various applications:
- Conductivity: The copper layer provides excellent electrical conductivity, allowing for efficient current flow and signal transmission.
- Thermal stability: Many copper clad substrates, such as FR-4 and polyimide, offer good thermal stability, ensuring reliable performance in high-temperature environments.
- Mechanical strength: The substrate materials used in copper clad provide mechanical support and durability, making it suitable for applications that require structural integrity.
- Insulation: The non-conductive substrate acts as an insulator, preventing short circuits and unintended electrical connections.
- Manufacturability: Copper clad is compatible with various manufacturing processes, including etching, drilling, and plating, making it easy to fabricate complex electronic circuits and components.
Manufacturing Process
The manufacturing process of copper clad involves several steps to ensure a high-quality, reliable product:
- Substrate preparation: The chosen substrate material is cut to the desired size and shape, and any necessary surface treatments are applied.
- Copper foil preparation: The copper foil is cleaned and treated to promote adhesion to the substrate.
- Lamination: The copper foil is bonded to the substrate using heat and pressure, typically in a lamination press.
- Cooling and inspection: The laminated copper clad is cooled and inspected for any defects or irregularities.
- Cutting and packaging: The copper clad is cut to the required dimensions and packaged for distribution.
Some manufacturers may also offer additional services, such as pre-etching, pre-drilling, or the application of protective coatings, depending on the customer’s requirements.
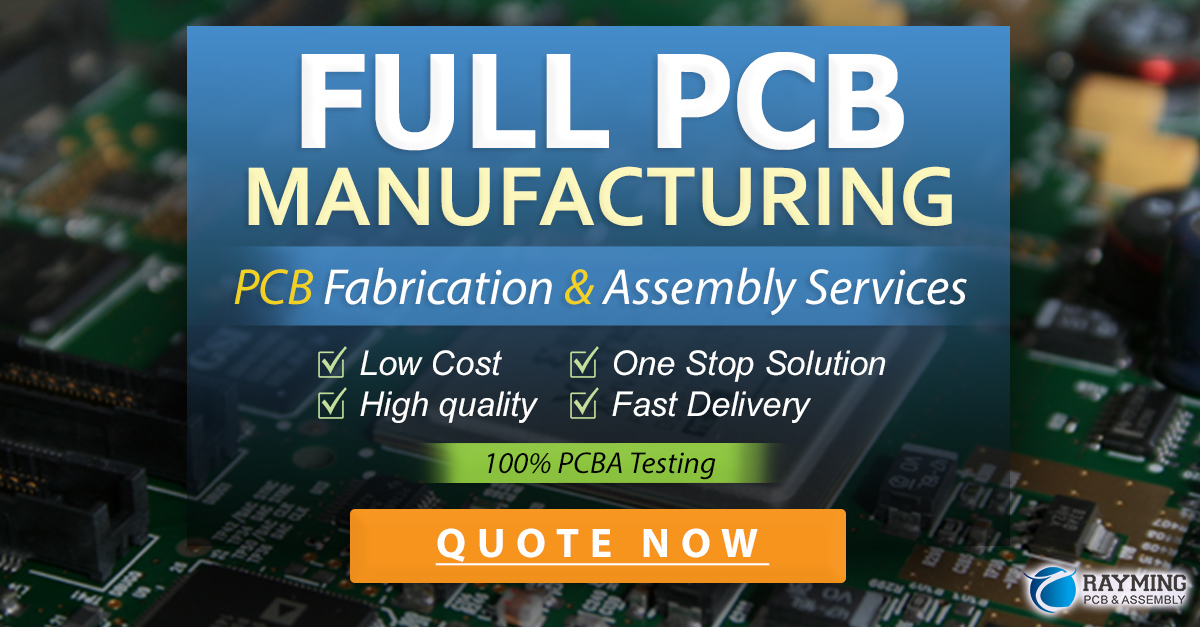
Types of Copper Clad
Copper clad is available in various types, each with its own unique characteristics and applications:
- Single-sided copper clad: This type has a copper layer on one side of the substrate and is often used for simple, low-density electronic circuits.
- Double-sided copper clad: With copper layers on both sides of the substrate, double-sided copper clad allows for more complex circuit designs and higher component density.
- Multi-layer copper clad: This type consists of multiple layers of copper and substrate, enabling the creation of highly complex, high-density electronic circuits.
- Flexible copper clad: Using flexible substrates like polyimide, flexible copper clad is suitable for applications that require bendable or conformable circuits.
- High-frequency copper clad: Designed for RF and microwave applications, high-frequency copper clad uses low-loss substrates like PTFE to ensure optimal signal integrity.
Applications of Copper Clad
Copper clad finds applications across a wide range of industries, including:
- Electronics: Copper clad is the primary material used in the manufacture of printed circuit boards (PCBs), which are essential components in nearly all electronic devices.
- Telecommunications: High-frequency copper clad is used in the production of antennas, filters, and other RF components for wireless communication systems.
- Automotive: Copper clad is used in the fabrication of automotive electronics, such as engine control units, infotainment systems, and sensors.
- Aerospace: The high-reliability and thermal stability of copper clad make it suitable for use in aerospace applications, including avionics and satellite systems.
- Medical devices: Copper clad is used in the production of medical electronics, such as implantable devices, diagnostic equipment, and monitoring systems.
- Industrial automation: Copper clad is employed in the manufacturing of industrial control systems, sensors, and power electronics.
Advantages of Using Copper Clad
Copper clad offers several advantages over other materials in electronic and manufacturing applications:
- Excellent electrical properties: The copper layer provides superior conductivity and low resistance, ensuring efficient current flow and signal transmission.
- Thermal management: Many copper clad substrates have good thermal conductivity, allowing for effective heat dissipation in high-power electronic applications.
- Mechanical stability: The substrate materials used in copper clad offer mechanical strength and durability, ensuring the longevity and reliability of the final product.
- Design flexibility: Copper clad is compatible with various manufacturing processes, allowing for the creation of intricate, high-density electronic circuits.
- Cost-effectiveness: Compared to other conductive materials, such as gold or silver, copper clad provides a cost-effective solution for many applications.
Choosing the Right Copper Clad
When selecting copper clad for your application, consider the following factors:
- Substrate material: Choose a substrate that meets your requirements for mechanical strength, thermal stability, and dielectric properties.
- Copper thickness: The thickness of the copper layer should be appropriate for your current carrying and signal integrity needs.
- Surface finish: Consider the surface finish of the copper layer, such as bare copper, tin-plated, or gold-plated, based on your soldering and assembly requirements.
- Manufacturing process: Ensure that the copper clad is compatible with your intended manufacturing processes, such as etching, drilling, or plating.
- Cost: Select a copper clad that balances performance and cost-effectiveness for your specific application.
Copper Clad Thickness and Weight
The thickness and weight of the copper layer in copper clad are typically expressed in ounces per square foot (oz/ft²). The most common copper weights used in PCB manufacturing are:
Copper Weight (oz/ft²) | Thickness (μm) | Thickness (mils) |
---|---|---|
0.5 | 17 | 0.7 |
1 | 35 | 1.4 |
2 | 70 | 2.8 |
3 | 105 | 4.2 |
4 | 140 | 5.6 |
Thicker copper layers can carry more current and provide better thermal management, but they also increase the cost and weight of the final product. The choice of copper thickness depends on the specific requirements of the application.
Handling and Storage of Copper Clad
To ensure the quality and longevity of copper clad, proper handling and storage practices should be followed:
- Store copper clad in a clean, dry, and temperature-controlled environment, ideally between 10°C and 30°C (50°F and 86°F) with a relative humidity of 50% or less.
- Avoid exposing copper clad to direct sunlight, moisture, or corrosive substances, as these can degrade the material’s properties.
- Handle copper clad with clean, lint-free gloves to prevent contamination and minimize the risk of damage to the copper surface.
- When cutting or machining copper clad, use sharp, well-maintained tools to minimize burrs and ensure clean, accurate cuts.
- Store copper clad sheets horizontally, with a protective layer between each sheet to prevent scratches or damage to the copper surface.
Frequently Asked Questions (FAQ)
- What is the difference between copper clad and printed circuit boards (PCBs)?
-
Copper clad is the raw material used to manufacture PCBs. It consists of a non-conductive substrate bonded with a layer of copper. PCBs are fabricated by etching away unwanted copper from the copper clad to create the desired circuit pattern.
-
Can copper clad be used for high-frequency applications?
-
Yes, specific types of copper clad, such as those with PTFE or other low-loss substrates, are designed for high-frequency applications like RF and microwave circuits.
-
How do I choose the right copper thickness for my application?
-
The choice of copper thickness depends on factors such as current carrying requirements, signal integrity, thermal management, and cost. Consult with a PCB manufacturer or refer to industry standards and guidelines to determine the appropriate copper thickness for your specific application.
-
Is copper clad environmentally friendly?
-
Copper clad itself is not considered environmentally harmful, as copper is a recyclable material. However, the manufacturing process of copper clad and PCBs can involve chemicals and processes that may have an environmental impact. Responsible manufacturers follow strict environmental regulations and implement best practices to minimize any negative effects.
-
Can copper clad be used for flexible electronics?
- Yes, flexible copper clad is available, which uses flexible substrates like polyimide. This type of copper clad is suitable for applications that require bendable or conformable circuits, such as wearable electronics or flexible displays.
Conclusion
Copper clad is a versatile and essential material in the world of electronics and manufacturing. Its unique combination of conductivity, insulation, and mechanical properties makes it an ideal choice for a wide range of applications, from simple electronic circuits to complex, high-density PCBs.
By understanding the properties, types, manufacturing processes, and applications of copper clad, designers and engineers can make informed decisions when selecting materials for their projects. As technology continues to advance, the demand for high-quality copper clad will only continue to grow, driving innovation and shaping the future of electronics.
Leave a Reply