What are HDI PCBs?
HDI PCBs are printed circuit boards that feature higher wiring density and smaller vias compared to traditional PCBs. They are characterized by their fine pitch traces, micro-vias, and buried/blind vias, which allow for more compact and complex designs. HDI technology enables the manufacturing of PCBs with higher component density, improved signal integrity, and reduced overall board size.
Key Features of HDI PCBs
- Fine pitch traces: HDI PCBs utilize traces with a width and spacing of 3 mils (0.075 mm) or less, allowing for denser routing and more efficient use of board space.
- Micro-vias: These are small, laser-drilled vias with diameters ranging from 50 to 150 microns (0.05 to 0.15 mm). Micro-vias enable the interconnection of multiple layers within the PCB, facilitating more complex designs.
- Buried and blind vias: Buried vias connect inner layers of the PCB without reaching the outer layers, while blind vias connect an outer layer to one or more inner layers without penetrating the entire board thickness. These vias help reduce board size and improve signal integrity.
Advantages of HDI PCBs
HDI PCBs offer several advantages over traditional PCBs, making them an attractive choice for various applications:
- Miniaturization: The higher wiring density and smaller vias in HDI PCBs allow for more compact designs, reducing the overall size and weight of electronic devices.
- Improved signal integrity: The shorter signal paths and reduced layer count in HDI PCBs minimize signal distortion and crosstalk, resulting in better signal integrity and higher-speed performance.
- Increased reliability: HDI PCBs feature smaller vias and more precise manufacturing processes, which contribute to improved reliability and reduced failure rates.
- Cost-effectiveness: Although the initial manufacturing costs of HDI PCBs may be higher than traditional PCBs, the overall cost savings from reduced board size, fewer layers, and improved performance often outweigh the initial investment.
HDI PCB Manufacturing Processes
The manufacturing of HDI PCBs involves several advanced processes and technologies:
1. Laser Drilling
Laser drilling is used to create micro-vias in HDI PCBs. There are two main types of laser drilling processes:
a. CO2 Laser Drilling: This method uses a CO2 laser to create micro-vias with diameters ranging from 50 to 150 microns. CO2 laser drilling is suitable for larger via sizes and is more cost-effective compared to UV laser drilling.
b. UV Laser Drilling: UV laser drilling employs a shorter wavelength laser to create smaller and more precise micro-vias, with diameters as small as 25 microns. This method is ideal for high-density designs and fine-pitch applications.
2. Via Filling
After laser drilling, the micro-vias are filled with conductive material to ensure reliable electrical connections between layers. There are two primary via filling methods:
a. Electroplating: This process involves depositing a thin layer of copper onto the walls of the micro-vias using an electric current. Electroplating is suitable for larger via sizes and provides a strong, reliable connection.
b. Conductive Paste Filling: In this method, a conductive paste is screen-printed or stenciled into the micro-vias. Conductive paste filling is faster and more cost-effective than electroplating, making it suitable for high-volume production.
3. Sequential Lamination
Sequential lamination is a process used to build up the layers of an HDI PCB. It involves laminating and pressing individual layers together, followed by laser drilling and via filling. This process is repeated until the desired number of layers is achieved. Sequential lamination allows for the creation of complex, multi-layer HDI PCBs with buried and blind vias.
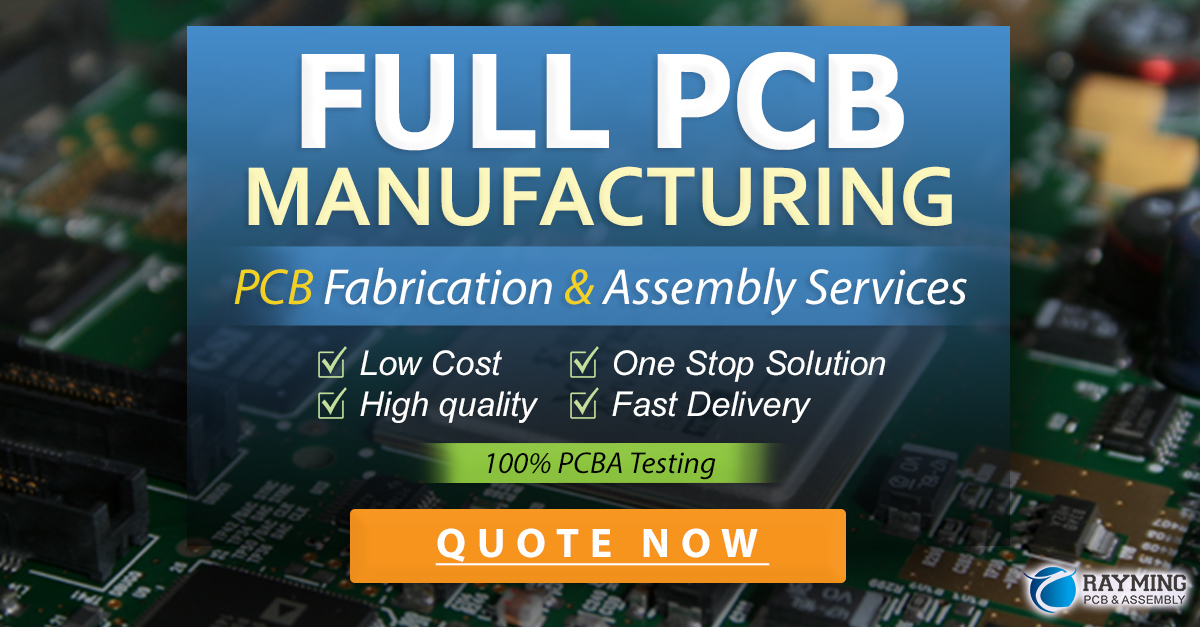
Applications of HDI PCBs
HDI PCBs find applications in various industries where miniaturization, high performance, and reliability are crucial:
- Consumer Electronics: Smartphones, tablets, wearables, and other portable devices rely on HDI PCBs to accommodate their compact designs and high-performance requirements.
- Automotive Electronics: Advanced driver assistance systems (ADAS), infotainment systems, and other automotive electronics use HDI PCBs for their reliability and ability to withstand harsh environments.
- Medical Devices: Implantable devices, diagnostic equipment, and other medical electronics benefit from the miniaturization and reliability offered by HDI PCBs.
- Aerospace and Defense: Satellite systems, avionics, and military equipment employ HDI PCBs for their high-density routing capabilities and robust performance in extreme conditions.
- Industrial Automation: Factory automation systems, process control equipment, and other industrial electronics use HDI PCBs for their compact size and improved signal integrity.
HDI PCB Design Considerations
Designing HDI PCBs requires careful consideration of various factors to ensure optimal performance and manufacturability:
- Via Placement: Proper placement of micro-vias is crucial to avoid signal integrity issues and manufacturing challenges. Designers should adhere to the manufacturer’s design rules and guidelines for via size, spacing, and placement.
- Layer Stack-up: The layer stack-up of an HDI PCB should be carefully planned to minimize signal distortion and crosstalk. Proper use of power and ground planes, as well as the arrangement of signal layers, can significantly impact the board’s performance.
- Impedance Control: Maintaining consistent impedance throughout the HDI PCB is essential for high-speed signal integrity. Designers should work closely with the manufacturer to ensure that the PCB’s impedance requirements are met.
- Thermal Management: HDI PCBs with high component density may generate significant heat, which can affect the board’s performance and reliability. Proper thermal management techniques, such as the use of thermal vias and heat sinks, should be incorporated into the design.
RAYPCB’s HDI PCB Manufacturing Capabilities
RAYPCB is a leading provider of high-quality HDI PCBs, offering state-of-the-art manufacturing facilities and expert engineering support. Some of RAYPCB’s key HDI PCB manufacturing capabilities include:
- Advanced laser drilling: RAYPCB utilizes both CO2 and UV laser drilling technologies to create precise micro-vias, ensuring high-quality interconnections between layers.
- Skilled via filling: With expertise in electroplating and conductive paste filling, RAYPCB can fill micro-vias with conductive material to create reliable electrical connections.
- Multilayer HDI PCBs: RAYPCB can manufacture complex, multi-layer HDI PCBs using sequential lamination processes, accommodating designs with up to 20 layers or more.
- Strict quality control: RAYPCB follows rigorous quality control procedures throughout the manufacturing process, ensuring that every HDI PCB meets the highest standards of performance and reliability.
- Rapid prototyping and mass production: With quick-turn prototyping services and large-scale production capabilities, RAYPCB can support projects of any size and complexity.
Frequently Asked Questions (FAQ)
- What is the minimum via size achievable in HDI PCBs?
-
The minimum via size in HDI PCBs depends on the laser drilling technology used. CO2 laser drilling can create micro-vias with diameters as small as 50 microns, while UV laser drilling can achieve diameters as small as 25 microns.
-
How many layers can an HDI PCB have?
-
HDI PCBs can have a varying number of layers, depending on the complexity of the design and the manufacturing capabilities of the PCB provider. RAYPCB can manufacture HDI PCBs with up to 20 layers or more using sequential lamination processes.
-
Are HDI PCBs more expensive than traditional PCBs?
-
The initial manufacturing costs of HDI PCBs may be higher than traditional PCBs due to the advanced processes and technologies involved. However, the overall cost savings from reduced board size, fewer layers, and improved performance often justify the investment in HDI technology.
-
What are the main applications of HDI PCBs?
-
HDI PCBs find applications in various industries where miniaturization, high performance, and reliability are essential. These include consumer electronics, automotive electronics, medical devices, aerospace and defense, and industrial automation.
-
How can I ensure my HDI PCB design is manufacturable?
- To ensure your HDI PCB design is manufacturable, work closely with your PCB manufacturer and adhere to their design rules and guidelines. Consider factors such as via placement, layer stack-up, impedance control, and thermal management during the design process. RAYPCB’s engineering team can provide expert guidance and support to help optimize your HDI PCB design for manufacturability.
Conclusion
HDI PCBs have revolutionized the electronics industry by enabling the development of more compact, high-performance devices. With their fine pitch traces, micro-vias, and buried/blind vias, HDI PCBs offer numerous advantages over traditional PCBs, including miniaturization, improved signal integrity, increased reliability, and cost-effectiveness.
RAYPCB, a leading HDI PCB Manufacturer, employs advanced manufacturing processes and technologies to produce high-quality HDI PCBs that meet the stringent requirements of various industries. By understanding the fundamentals of HDI PCBs, their advantages, manufacturing processes, and applications, designers and engineers can leverage the benefits of this technology to create innovative and reliable electronic devices.
When designing HDI PCBs, it is crucial to consider factors such as via placement, layer stack-up, impedance control, and thermal management to ensure optimal performance and manufacturability. Working closely with a reputable PCB manufacturer like RAYPCB can help streamline the design and manufacturing process, resulting in high-quality HDI PCBs that meet the specific needs of your application.
As the demand for smaller, faster, and more reliable electronic devices continues to grow, the adoption of HDI PCB technology is expected to increase across various industries. By partnering with RAYPCB for your HDI PCB needs, you can leverage their expertise and state-of-the-art manufacturing capabilities to bring your innovative ideas to life and stay ahead of the competition in today’s rapidly evolving electronics landscape.
Leave a Reply