What is Impedance Control and Why is it Important?
Impedance control is the practice of designing and manufacturing printed circuit boards (PCBs) and interconnects to have a specific characteristic impedance. This is crucial for maintaining signal integrity, especially in high-speed digital systems where impedance mismatches can lead to reflections, crosstalk, and other issues that degrade signal quality.
Proper impedance control helps ensure that signals propagate through the system with minimal distortion, maintaining the desired signal shape and timing. This is particularly important for high-frequency signals, where even small impedance mismatches can cause significant problems.
How to Calculate Characteristic Impedance
Characteristic impedance (Z0) is determined by the physical properties of the transmission line, such as the conductor width, thickness, and spacing, as well as the dielectric constant of the insulating material. The characteristic impedance of a transmission line can be calculated using the following equation:
Z0 = sqrt((R + jωL) / (G + jωC))
Where:
– R = series resistance per unit length
– L = series inductance per unit length
– G = shunt conductance per unit length
– C = shunt capacitance per unit length
– ω = angular frequency (2πf)
For most PCB applications, the characteristic impedance is typically designed to be 50Ω or 100Ω, depending on the system requirements.
10 Ways to Avoid Signal Integrity Problems
1. Design for Proper Characteristic Impedance
When designing PCBs, it’s essential to choose the appropriate trace width, thickness, and spacing to achieve the desired characteristic impedance. This can be done using impedance calculators or simulation tools that take into account the PCB stackup and material properties.
2. Use Controlled Impedance Materials
Select PCB materials with well-controlled dielectric constants and low loss tangents to maintain consistent impedance and minimize signal attenuation. Some common controlled impedance materials include FR-4, Rogers, and Isola.
3. Maintain Consistent Trace Geometry
Keep trace width and spacing consistent throughout the signal path to avoid impedance discontinuities. If changes in trace geometry are necessary, use gradual transitions (tapers) to minimize reflections.
4. Terminate Transmission Lines Properly
Use appropriate termination techniques, such as series termination, parallel termination, or differential termination, to match the impedance of the source and load to the characteristic impedance of the transmission line. This helps minimize reflections and ringing.
5. Minimize Stub Lengths
Keep stub lengths as short as possible to reduce the impact of impedance mismatches caused by unterminated branches. If long stubs are unavoidable, consider using techniques like series termination or stub resonance compensation.
6. Use Differential Signaling for High-Speed Interfaces
Differential signaling, such as LVDS or CML, is less sensitive to impedance variations and offers better noise immunity compared to single-ended signaling. When using differential pairs, ensure that the traces are closely coupled and have equal length to maintain a balanced impedance.
7. Implement Proper Power Distribution Network (PDN) Design
A well-designed PDN with low impedance and adequate decoupling helps maintain signal integrity by providing a stable reference plane for signal return currents. Use appropriate decoupling capacitors, placed close to the ICs, to minimize power supply noise and ripple.
8. Simulate and Verify Signal Integrity
Use signal integrity simulation tools to analyze the performance of your design before manufacturing. These tools can help identify potential issues, such as reflections, crosstalk, or excessive losses, allowing you to make necessary adjustments to the design.
9. Perform Impedance Testing and Validation
After manufacturing, perform impedance testing to verify that the actual impedance of the PCB matches the designed value. Time-domain reflectometry (TDR) is a common technique used to measure the impedance profile along a transmission line and identify any discontinuities.
10. Follow Industry Standards and Guidelines
Adhere to industry standards and guidelines, such as IPC-2141 (Controlled Impedance Circuit Boards and High-Speed Design), to ensure that your design meets the necessary requirements for impedance control and signal integrity.
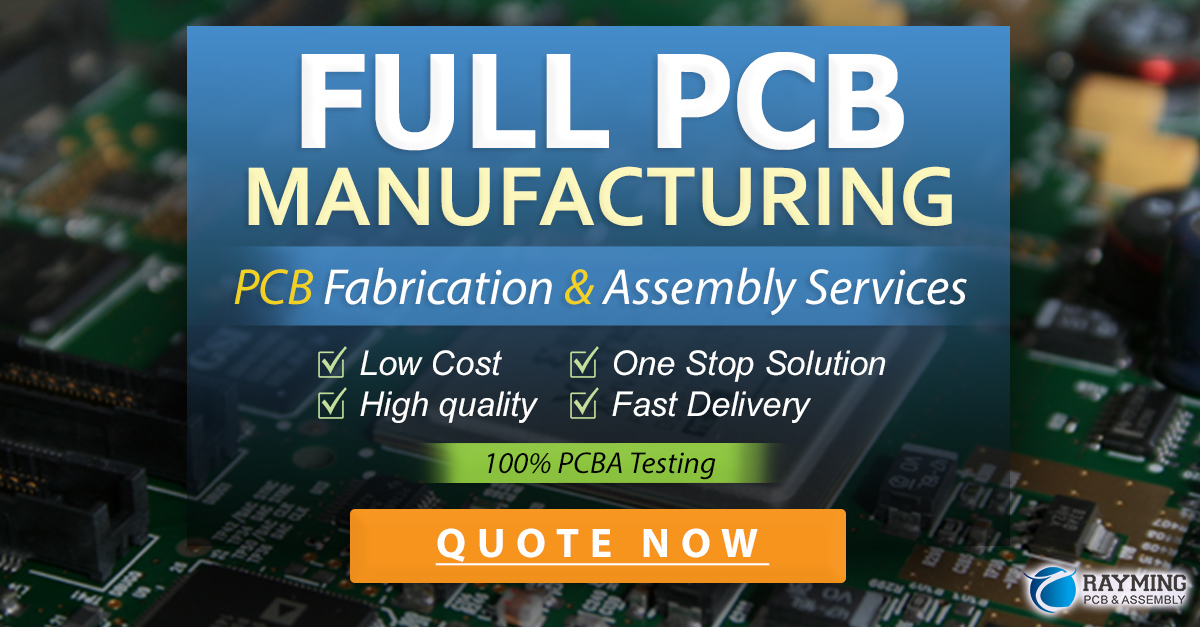
FAQs
1. What is the difference between characteristic impedance and controlled impedance?
Characteristic impedance is the inherent impedance of a transmission line, determined by its physical properties, such as conductor geometry and dielectric material. Controlled impedance, on the other hand, refers to the process of designing and manufacturing PCBs to have a specific characteristic impedance within a certain tolerance.
2. How does impedance mismatch affect signal integrity?
Impedance mismatch occurs when the characteristic impedance of a transmission line does not match the impedance of the source or load. This mismatch causes a portion of the signal to be reflected back towards the source, leading to signal distortion, ringing, and reduced noise margin. In severe cases, impedance mismatch can cause false triggering, data errors, or even damage to the connected devices.
3. What are some common impedance values used in PCB design?
The most common characteristic impedance values used in PCB design are 50Ω and 100Ω. The choice between these values depends on factors such as the application, signaling standard, and PCB stackup. For example, many high-speed digital interfaces, such as USB, HDMI, and Ethernet, use 100Ω differential impedance, while 50Ω is often used for single-ended signals like UART or SPI.
4. How does the PCB stackup affect impedance control?
The PCB stackup, which defines the arrangement of conductive and insulating layers, has a significant impact on impedance control. The thickness and dielectric constant of the insulating layers, as well as the presence of reference planes, influence the characteristic impedance of the traces. When designing for impedance control, it’s crucial to work closely with your PCB manufacturer to ensure that the stackup is optimized for your specific requirements.
5. What are some best practices for routing high-speed signals on a PCB?
When routing high-speed signals, it’s important to follow these best practices:
- Keep trace lengths as short as possible to minimize signal attenuation and delay.
- Route signals over a continuous reference plane (ground or power) to provide a low-impedance return path.
- Avoid routing high-speed signals near board edges or gaps in the reference plane, as this can cause impedance discontinuities.
- Use appropriate via design and placement to minimize impedance mismatches and signal reflections.
- Follow recommended trace width and spacing guidelines for the desired impedance and PCB stackup.
By understanding the principles of impedance control and following these best practices, designers can effectively mitigate signal integrity issues and ensure reliable performance in high-speed digital systems.
Leave a Reply