What is PCB Assembly?
PCB assembly is the process of attaching electronic components to a printed circuit board. The components are placed on the board according to a predetermined design and then soldered to establish electrical connections. The assembLED PCB forms the backbone of the electronic device, enabling it to perform its intended functions.
Key Components in PCB Assembly
- Printed Circuit Board (PCB)
- Surface Mount Devices (SMDs)
- Through-Hole Components
- Solder Paste
- Solder Wire
Importance of PCB Assembly
PCB assembly plays a vital role in the electronics industry. It offers several advantages over traditional point-to-point wiring, making it essential for the production of modern electronic devices.
Benefits of PCB Assembly
- Miniaturization: PCBs allow for the compact arrangement of components, enabling the creation of smaller and more portable devices.
- Reliability: Properly assembled PCBs ensure reliable electrical connections and reduce the risk of short circuits or component failures.
- Mass Production: PCB assembly techniques enable the efficient mass production of electronic devices, reducing manufacturing costs and time.
- Consistency: Automated PCB assembly processes ensure consistent quality and minimize human errors.
PCB Assembly Process
The PCB assembly process involves several steps, each of which requires precision and attention to detail. Let’s take a closer look at the key stages of PCB assembly.
Step 1: PCB Design and Fabrication
Before the assembly process begins, the PCB must be designed and fabricated. This involves creating a schematic diagram, laying out the components, and generating the necessary files for manufacturing. The PCB is then fabricated using materials such as FR-4, a glass-reinforced epoxy laminate.
Step 2: Solder Paste Application
Solder paste, a mixture of tiny solder particles and flux, is applied to the PCB’s contact pads using a stencil or screen printing technique. The solder paste holds the components in place during the reflow soldering process.
Step 3: Component Placement
Surface mount devices (SMDs) and through-hole components are placed onto the PCB according to the design specifications. This step can be performed manually or using automated pick-and-place machines for higher efficiency and accuracy.
Step 4: Reflow Soldering
The PCB with the placed components undergoes reflow soldering. It is exposed to high temperatures in a reflow oven, causing the solder paste to melt and form permanent electrical connections between the components and the PCB.
Step 5: Inspection and Testing
After the soldering process, the assembled PCB undergoes visual inspection and testing to ensure its functionality and quality. Automated optical inspection (AOI) systems and electrical testing methods are employed to detect any defects or malfunctions.
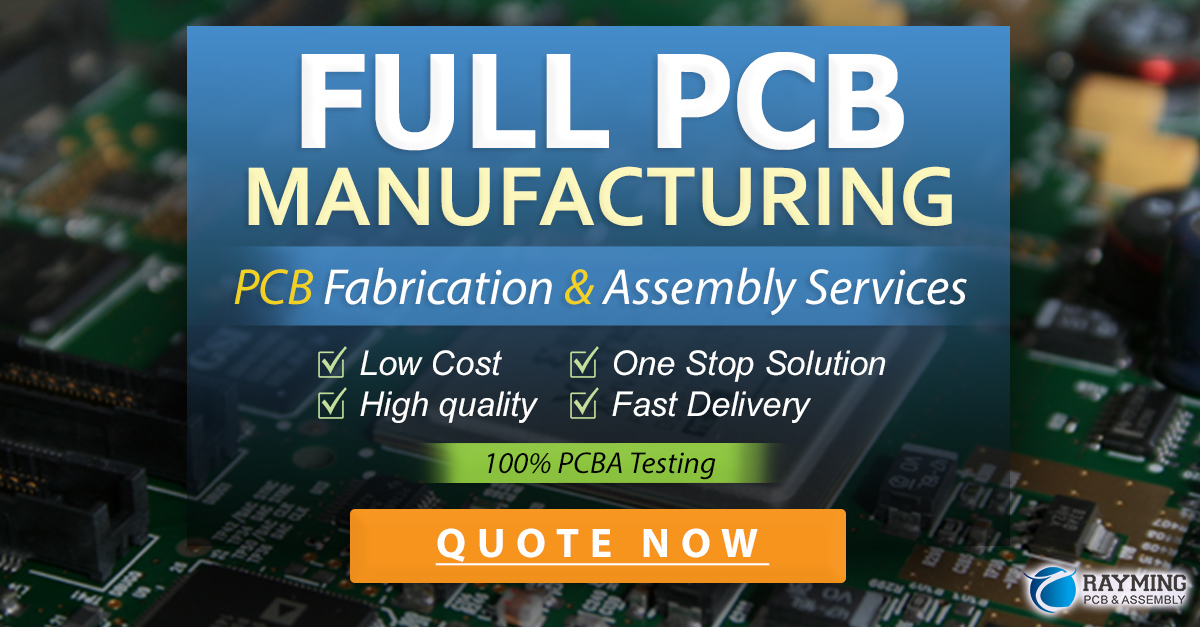
PCB Assembly Techniques
There are two primary techniques used in PCB assembly: surface mount technology (SMT) and through-hole technology (THT). Each technique has its advantages and is suitable for different types of components and applications.
Surface Mount Technology (SMT)
SMT involves placing components directly onto the surface of the PCB. SMDs have small leads or terminations that are soldered to the PCB’s contact pads. SMT offers several benefits:
- Smaller component sizes
- Higher component density
- Faster assembly process
- Improved performance at high frequencies
Through-Hole Technology (THT)
THT involves inserting component leads through holes drilled in the PCB and soldering them on the opposite side. Through-hole components are generally larger and more robust compared to SMDs. THT is used for:
- Components that require greater mechanical strength
- High-power applications
- Certain types of connectors and sockets
Quality Control in PCB Assembly
Ensuring the quality of assembled PCBs is crucial for the reliability and performance of electronic devices. Several quality control measures are implemented throughout the assembly process.
Visual Inspection
Visual inspection is the first line of defense against defects. Operators or automated optical inspection (AOI) systems examine the assembled PCBs for issues such as:
- Misaligned or missing components
- Solder bridges or short circuits
- Insufficient or excessive solder
- Damaged components
Electrical Testing
Electrical testing verifies the functionality and performance of the assembled PCB. Various testing methods are employed, including:
- In-circuit testing (ICT): Checks the connectivity and values of individual components.
- Functional testing: Verifies the overall functionality of the PCB under real-world conditions.
- Boundary scan testing: Tests the interconnections between integrated circuits (ICs) on the PCB.
Environmental Testing
Environmental testing ensures that the assembled PCBs can withstand the intended operating conditions. Tests may include:
- Temperature cycling: Exposes the PCB to extreme temperature variations.
- Humidity testing: Verifies the PCB’s resistance to moisture.
- Vibration and shock testing: Checks the PCB’s durability under mechanical stress.
Common PCB Assembly Challenges
PCB assembly can present various challenges that manufacturers must address to ensure a successful outcome. Some common challenges include:
Component Availability
The availability of electronic components can impact the PCB assembly process. Component shortages, obsolescence, or long lead times can cause delays and require alternative sourcing strategies.
Miniaturization
As electronic devices become smaller and more compact, PCB assembly must adapt to handle miniaturized components and tighter tolerances. This requires advanced equipment, skilled operators, and precise process control.
Electrostatic Discharge (ESD) Protection
Electronic components are sensitive to electrostatic discharge, which can cause damage or failure. Implementing ESD Protection measures, such as grounded workstations and ESD-safe packaging, is essential during PCB assembly.
Thermal Management
High-power electronic devices generate significant heat, which must be dissipated effectively to prevent component damage and ensure reliable operation. Thermal management techniques, such as heatsinks and thermal interface materials, are incorporated into PCB assembly.
Future Trends in PCB Assembly
The PCB assembly industry is constantly evolving to keep pace with advancements in electronics technology. Some notable trends shaping the future of PCB assembly include:
Automation and Robotics
Automated assembly lines and robotic systems are becoming increasingly prevalent in PCB assembly. These technologies enhance efficiency, accuracy, and repeatability while reducing labor costs and human errors.
3D Printing
3D printing technology is finding applications in PCB assembly, particularly for rapid prototyping and low-volume production. Conductive inks and advanced materials enable the printing of functional PCBs and components.
Flexible and Stretchable Electronics
Flexible and stretchable PCBs are gaining traction in wearable devices, medical applications, and IoT solutions. These PCBs can conform to curved surfaces and withstand bending and stretching, opening up new possibilities for electronic device design.
Sustainable and Eco-Friendly Practices
There is a growing emphasis on sustainable and eco-friendly practices in PCB assembly. This includes the use of lead-free solder, recyclable materials, and energy-efficient processes to minimize environmental impact.
Frequently Asked Questions (FAQ)
- What is the difference between SMT and THT in PCB assembly?
-
SMT (Surface Mount Technology) involves placing components directly onto the surface of the PCB, while THT (Through-Hole Technology) involves inserting component leads through holes in the PCB and soldering them on the opposite side.
-
How long does the PCB assembly process typically take?
-
The duration of the PCB assembly process depends on factors such as the complexity of the design, the number of components, and the assembly techniques used. Simple PCBs can be assembled in a matter of hours, while complex boards may take several days.
-
What are some common defects that can occur during PCB assembly?
-
Common defects in PCB assembly include component misalignment, solder bridges, insufficient or excessive solder, Cold Solder Joints, and damaged components. These defects can be detected through visual inspection and testing.
-
Can PCB assembly be outsourced to third-party manufacturers?
-
Yes, many companies outsource their PCB assembly requirements to specialized contract manufacturers. Outsourcing allows companies to leverage the expertise, equipment, and scale of these manufacturers, reducing costs and time-to-market.
-
What certifications are important for PCB assembly providers?
- Important certifications for PCB assembly providers include ISO 9001 (quality management), ISO 14001 (environmental management), IATF 16949 (automotive quality management), and IPC Standards (industry-specific guidelines for PCB design and manufacturing).
Conclusion
PCB assembly is a critical process in the production of electronic devices. It involves the placement and soldering of components onto a printed circuit board, forming the foundation for the device’s functionality. The assembly process encompasses various steps, including PCB design, solder paste application, component placement, reflow soldering, and inspection.
Quality control measures, such as visual inspection, electrical testing, and environmental testing, ensure the reliability and performance of assembled PCBs. Manufacturers must also navigate challenges like component availability, miniaturization, ESD protection, and thermal management.
As technology advances, PCB assembly continues to evolve, with trends like automation, 3D printing, flexible electronics, and sustainable practices shaping the future of the industry. By understanding the intricacies of PCB assembly and staying updated with the latest developments, manufacturers can deliver high-quality, reliable electronic devices that meet the ever-growing demands of the market.
Leave a Reply