What is an LED PCB?
An LED PCB (Light Emitting Diode Printed Circuit Board) is a specialized circuit board designed to power and control LED lights. These PCBs are used in a wide range of applications, from simple indicator lights to complex LED displays and lighting systems. LED PCBs are designed to provide the necessary electrical connections, heat dissipation, and mechanical support for the LED components.
Key Components of an LED PCB
- Substrate Material
- FR-4 (Flame Retardant 4)
- Aluminum
- Ceramic
- Copper Layers
- Conductive traces
- Power and ground planes
- Solder Mask
- Insulating layer
- Protects copper traces
- Silkscreen
- Component labels and markings
- LED Components
- Surface-mounted LEDs (SMD)
- Through-hole LEDs
- Passive Components
- Resistors
- Capacitors
- Inductors
- Connectors and Headers
- Power input
- Data communication
Advantages of Using LED PCBs
Energy Efficiency
LED PCBs are highly energy-efficient compared to traditional lighting solutions. LEDs consume significantly less power while producing the same or higher levels of brightness. This energy efficiency translates into reduced operating costs and a lower environmental impact.
Long Lifespan
LEDs have a much longer lifespan compared to other lighting technologies. A well-designed LED PCB can last for tens of thousands of hours, reducing the need for frequent replacements and maintenance.
Design Flexibility
LED PCBs offer great design flexibility, allowing for the creation of custom lighting solutions tailored to specific applications. The compact size and versatility of LEDs enable the development of innovative and space-saving designs.
Durability
LED PCBs are robust and resistant to shock, vibration, and extreme temperatures. This durability makes them suitable for use in harsh environments and applications where reliability is critical.
Cost-Effectiveness
Although the initial cost of LED PCBs may be higher than traditional lighting solutions, their long lifespan, energy efficiency, and low maintenance requirements make them a cost-effective choice in the long run.
LED PCB Design Considerations
Thermal Management
Proper thermal management is crucial for the performance and longevity of LED PCBs. LEDs generate heat during operation, and excessive heat can lead to reduced light output, color shifts, and premature failure. Effective thermal management techniques include:
- Using thermally conductive substrates (e.g., aluminum, ceramic)
- Incorporating thermal vias to transfer heat away from the LEDs
- Designing adequate copper area for heat dissipation
- Using thermal interface materials (TIMs) to improve heat transfer
Current and Voltage Control
LEDs are current-driven devices, and their brightness is directly proportional to the current flowing through them. Proper current control is essential to ensure consistent light output and prevent overdriving, which can lead to premature failure. Common current control methods include:
- Series resistors
- Constant current drivers
- PWM (Pulse Width Modulation) dimming
Voltage control is also important to ensure that the LEDs operate within their specified voltage range. Overvoltage can cause damage to the LEDs, while undervoltage can result in reduced light output.
Optical Design
The optical design of an LED PCB plays a significant role in determining the light distribution, intensity, and color quality. Factors to consider in optical design include:
- LED selection (wavelength, viewing angle, intensity)
- Lens and reflector design
- Diffuser materials
- Spacing between LEDs
- Color mixing and uniformity
EMI and EMC Considerations
LED PCBs can generate electromagnetic interference (EMI) and may be susceptible to electromagnetic compatibility (EMC) issues. Proper design techniques to mitigate EMI and ensure EMC compliance include:
- Proper grounding and shielding
- Filtering and decoupling capacitors
- Minimizing current loops and trace lengths
- Following PCB layout best practices
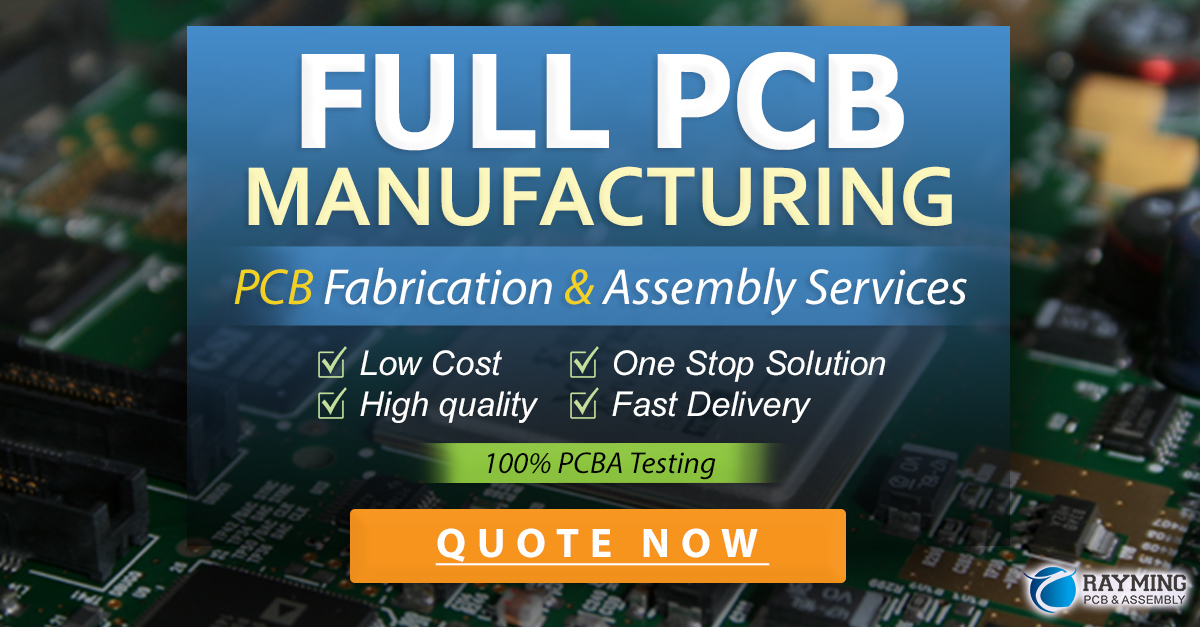
LED PCB Manufacturing Process
PCB Fabrication
- Substrate preparation
- Copper etching and plating
- Solder mask application
- Silkscreen printing
- Surface finish (e.g., HASL, ENIG, OSP)
PCB Assembly
- Solder paste application (stencil printing or jet dispensing)
- Component placement (SMT and through-hole)
- Reflow soldering
- Inspection and testing (AOI, X-ray, functional testing)
Quality Control and Testing
- Visual inspection
- Electrical testing (continuity, resistance, voltage)
- Functional testing (light output, color, uniformity)
- Environmental testing (temperature, humidity, vibration)
- Burn-in testing
Applications of LED PCBs
General Lighting
- Indoor lighting (residential, commercial, industrial)
- Outdoor lighting (street lights, landscape lighting)
- Automotive lighting (headlights, taillights, interior lighting)
Displays and Signage
- Digital signage and billboards
- Scoreboard displays
- Traffic signals and signage
Medical and Scientific Instrumentation
- Medical imaging and diagnostic devices
- Microscopy and spectroscopy
- Phototherapy and light therapy devices
Entertainment and Arts
- Stage and theater lighting
- Architectural lighting and illumination
- Media facades and interactive installations
Future Trends in LED PCB Technology
Miniaturization and Integration
The trend towards miniaturization and integration of LED PCBs continues, with the development of smaller, more compact designs that incorporate additional functionalities, such as sensors, wireless communication, and power management.
Smart Lighting and IoT
The integration of LED PCBs with the Internet of Things (IoT) enables the development of smart lighting systems that can be remotely controlled, monitored, and optimized for energy efficiency and user comfort.
Flexible and Stretchable PCBs
The development of flexible and stretchable LED PCBs opens up new possibilities for wearable electronics, conformable lighting, and innovative product designs.
Sustainable and Eco-Friendly Materials
There is a growing focus on the use of sustainable and eco-friendly materials in LED PCB manufacturing, such as biodegradable substrates, lead-free solders, and recyclable components.
Frequently Asked Questions (FAQ)
1. What is the difference between an LED and an LED PCB?
An LED is a single light-emitting diode component, while an LED PCB is a printed circuit board that incorporates multiple LEDs along with the necessary electrical components and connections to power and control them.
2. Can LED PCBs be dimmed?
Yes, LED PCBs can be dimmed using various methods, such as PWM (Pulse Width Modulation), analog dimming, or using dedicated LED dimming drivers.
3. How do I choose the right LED PCB for my application?
When choosing an LED PCB, consider factors such as the required light output, color temperature, power consumption, operating environment, and design constraints. Consult with an experienced LED PCB manufacturer or lighting designer to select the most suitable solution for your specific application.
4. What is the expected lifespan of an LED PCB?
The lifespan of an LED PCB depends on various factors, such as the quality of the components, thermal management, and operating conditions. A well-designed LED PCB can last for 50,000 hours or more, which is significantly longer than traditional lighting solutions.
5. Are LED PCBs more expensive than traditional lighting solutions?
Initially, LED PCBs may have a higher upfront cost compared to traditional lighting solutions. However, their long lifespan, energy efficiency, and low maintenance requirements often make them a more cost-effective choice in the long run.
Characteristic | LED PCB | Traditional Lighting (e.g., Incandescent, Fluorescent) |
---|---|---|
Energy Efficiency | High | Low to moderate |
Lifespan | Long (50,000+ hours) | Short to moderate (1,000-20,000 hours) |
Upfront Cost | Higher | Lower |
Operating Cost | Lower | Higher |
Design Flexibility | High | Limited |
Environmental Impact | Low | Moderate to high |
Color Quality | Excellent | Moderate to good |
Dimming Capability | Excellent | Moderate |
Heat Generation | Low | High |
In conclusion, LED PCBs offer numerous advantages over traditional lighting solutions, including energy efficiency, long lifespan, design flexibility, and durability. By understanding the key components, design considerations, and manufacturing processes involved in LED PCB development, engineers and designers can create innovative and high-performance lighting solutions for a wide range of applications. As the technology continues to evolve, with advancements in miniaturization, smart lighting, and sustainable materials, LED PCBs are poised to play an increasingly important role in shaping the future of lighting and electronics.
Leave a Reply