Introduction to PCB Stencils
A PCB stencil is a thin sheet of material, typically stainless steel or polyester, that is used in the process of applying solder paste to a printed circuit board (PCB) during the surface mount technology (SMT) assembly process. The stencil has openings that correspond to the pads on the PCB where components will be placed. When solder paste is applied to the stencil and then the stencil is placed on the PCB, the solder paste is deposited onto the pads through the openings in the stencil.
Benefits of Using PCB Stencils
Using a PCB stencil offers several benefits in the SMT Assembly process:
-
Precise solder paste application: PCB stencils ensure that the correct amount of solder paste is applied to each pad on the PCB, leading to more consistent and reliable solder joints.
-
Increased efficiency: Using a stencil allows for the rapid application of solder paste to multiple PCBs, reducing the time and labor required for the assembly process.
-
Improved quality: By ensuring precise solder paste application, PCB stencils contribute to higher-quality solder joints and fewer defects in the assembLED PCBs.
Types of PCB Stencils
There are two main types of PCB stencils: stainless steel and polyester.
Stainless Steel Stencils
Stainless steel stencils are the most common type used in PCB Assembly. They offer several advantages:
-
Durability: Stainless steel stencils are highly durable and can withstand repeated use without deformation or damage.
-
Precision: Stainless steel stencils can be manufactured with high precision, ensuring accurate solder paste application.
-
Compatibility: Stainless steel stencils are compatible with a wide range of solder paste types and can be used for both lead-based and lead-free solder pastes.
Stainless Steel Stencil Thicknesses
Stainless steel stencils are available in various thicknesses to accommodate different component sizes and solder paste requirements. Common thicknesses include:
Thickness (mm) | Typical Applications |
---|---|
0.100 | Very fine pitch components (0.3mm and below) |
0.127 | Fine pitch components (0.4mm to 0.5mm) |
0.150 | Standard SMD components (0.5mm and above) |
0.200 | Large components or high-volume solder paste applications |
Polyester Stencils
Polyester stencils, also known as mesh stencils, are an alternative to stainless steel stencils. They offer some unique advantages:
-
Cost-effectiveness: Polyester stencils are generally less expensive than stainless steel stencils, making them a good choice for low-volume or prototype production.
-
Flexibility: Polyester stencils are flexible, which allows them to conform to slightly uneven PCB Surfaces, ensuring better solder paste contact.
-
Ease of use: Polyester stencils are lightweight and easy to handle, making them suitable for manual solder paste application processes.
However, polyester stencils have some limitations compared to stainless steel stencils:
-
Limited durability: Polyester stencils are less durable than stainless steel stencils and may degrade over time with repeated use.
-
Lower precision: Polyester stencils cannot achieve the same level of precision as stainless steel stencils, particularly for very fine pitch components.
PCB Stencil Design Considerations
When designing a PCB stencil, several factors must be considered to ensure optimal solder paste application and assembly quality.
Aperture Size and Shape
The aperture size and shape in the PCB stencil should be designed to match the pads on the PCB. The aperture size is typically slightly larger than the pad size to allow for proper solder paste release. The aperture shape can be circular, square, or rectangular, depending on the pad shape and the specific requirements of the components being assembled.
Stencil Thickness
The thickness of the PCB stencil determines the amount of solder paste deposited on the pads. Thicker stencils deposit more solder paste, while thinner stencils deposit less. The optimal stencil thickness depends on the size and pitch of the components being assembled, as well as the desired solder joint profile.
Aperture Wall Angle
The aperture wall angle, also known as the aperture sidewall angle, refers to the angle of the walls of the openings in the stencil. A higher wall angle (closer to 90 degrees) results in better solder paste release and more precise solder paste deposition. However, higher wall angles can be more difficult to manufacture and may require special laser cutting techniques.
Fiducial Marks
Fiducial marks are reference points on the PCB stencil that are used to align the stencil with the PCB during the solder paste application process. Fiducial marks should be included in the stencil design to ensure accurate alignment and prevent solder paste misregistration.
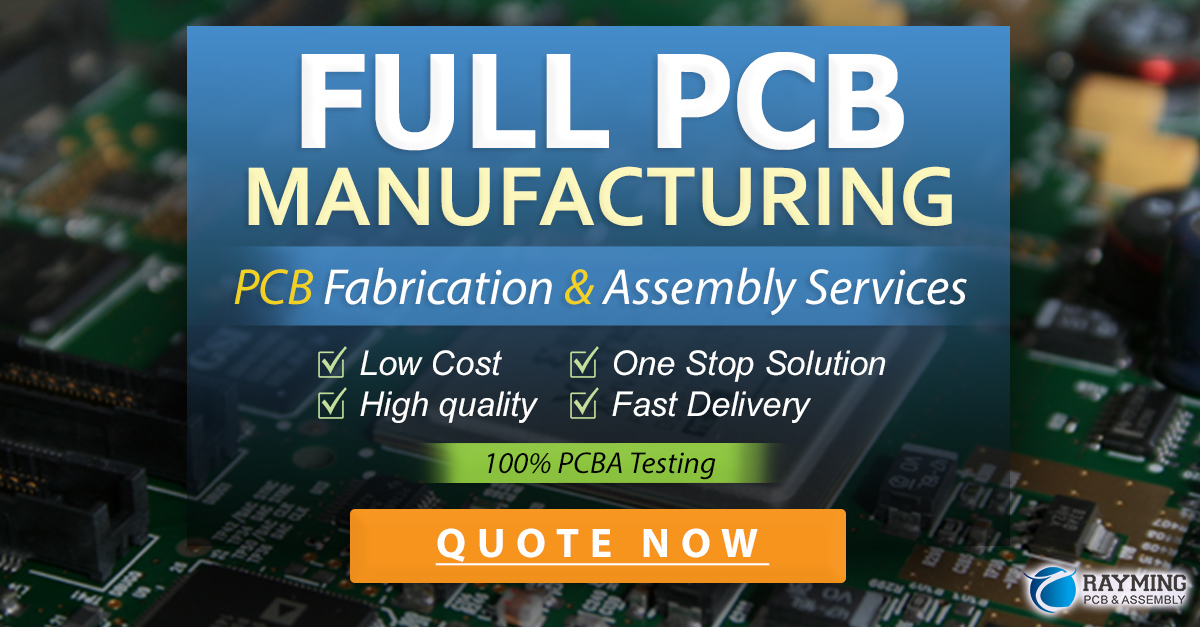
PCB Stencil Manufacturing Processes
PCB stencils can be manufactured using several different processes, each with its own advantages and limitations.
Laser Cutting
Laser cutting is the most common method for manufacturing PCB stencils. A high-powered laser is used to cut the apertures in the stencil material. Laser cutting offers several advantages:
-
High precision: Laser cutting can produce apertures with very high precision and accuracy, making it suitable for fine pitch components.
-
Rapid production: Laser cutting is a fast process, allowing for quick turnaround times and high-volume production.
-
Versatility: Laser cutting can be used to create apertures with various sizes, shapes, and wall angles.
Chemical Etching
Chemical etching is another method for manufacturing PCB stencils. In this process, the stencil material is coated with a photoresist, which is then exposed to UV light through a photomask. The unexposed areas of the photoresist are then removed, and the stencil material is etched using chemicals to create the apertures.
Chemical etching offers some advantages over laser cutting:
-
Lower cost: Chemical etching is generally less expensive than laser cutting, particularly for high-volume production.
-
Smooth aperture walls: Chemical etching produces smooth aperture walls, which can improve solder paste release and reduce the risk of solder paste clogging.
However, chemical etching also has some limitations:
-
Lower precision: Chemical etching cannot achieve the same level of precision as laser cutting, particularly for very fine pitch components.
-
Longer production times: Chemical etching is a slower process than laser cutting, resulting in longer turnaround times.
Electroforming
Electroforming is a less common method for manufacturing PCB stencils. In this process, a photoresist is applied to a conductive substrate, exposed to UV light through a photomask, and then developed. The exposed areas of the substrate are then electroplated with a metal, typically nickel, to build up the stencil thickness. Finally, the photoresist and substrate are removed, leaving the electroformed stencil.
Electroforming offers some unique advantages:
-
High precision: Electroforming can produce stencils with very high precision and accuracy, making it suitable for ultra-fine pitch components.
-
Smooth aperture walls: Electroformed stencils have very smooth aperture walls, which can improve solder paste release and reduce the risk of solder paste clogging.
However, electroforming also has some limitations:
-
High cost: Electroforming is a more expensive process than laser cutting or chemical etching, making it less suitable for high-volume production.
-
Limited material options: Electroforming is typically limited to nickel stencils, which may not be suitable for all applications.
Maintaining and Cleaning PCB Stencils
Proper maintenance and cleaning of PCB stencils are essential to ensure consistent solder paste application and high-quality assembly results.
Stencil Cleaning Methods
There are several methods for cleaning PCB stencils, depending on the type of solder paste and the degree of contamination.
-
Manual cleaning: For light contamination, manual cleaning with isopropyl alcohol (IPA) and a lint-free wipe can be effective. The stencil should be wiped in a single direction to avoid spreading contamination.
-
Ultrasonic cleaning: For more stubborn contamination, ultrasonic cleaning can be used. The stencil is placed in an ultrasonic cleaner filled with a cleaning solution, and high-frequency sound waves are used to agitate the solution and remove contamination.
-
Automated cleaning: For high-volume production, automated stencil cleaning systems can be used. These systems typically use a combination of spraying, brushing, and drying to clean the stencil quickly and effectively.
Stencil Storage
When not in use, PCB stencils should be stored properly to prevent damage and contamination. Stencils should be stored in a clean, dry environment, away from direct sunlight and extreme temperatures. Stainless steel stencils should be stored flat to prevent warping, while polyester stencils can be rolled for storage.
FAQ
-
What is the difference between a PCB stencil and a solder paste mask?
A PCB stencil is a separate sheet of material with apertures that correspond to the pads on the PCB, used to apply solder paste. A solder paste mask, on the other hand, is a layer applied directly to the PCB that defines the areas where solder paste should be applied. -
Can PCB stencils be reused?
Yes, PCB stencils can be reused multiple times, provided they are properly cleaned and maintained between uses. Stainless steel stencils are more durable and can withstand more reuse than polyester stencils. -
How do I choose the right stencil thickness for my PCB?
The optimal stencil thickness depends on several factors, including the size and pitch of the components being assembled, the desired solder joint profile, and the type of solder paste being used. Generally, thicker stencils are used for larger components and higher-volume solder paste applications, while thinner stencils are used for finer pitch components. -
Can PCB stencils be used for both lead-based and lead-free solder pastes?
Yes, PCB stencils can be used with both lead-based and lead-free solder pastes. However, lead-free solder pastes may require different stencil thicknesses and aperture designs to achieve optimal results. -
How often should PCB stencils be cleaned?
PCB stencils should be cleaned regularly to prevent solder paste buildup and contamination. The frequency of cleaning depends on the volume of production and the type of solder paste being used. As a general rule, stencils should be cleaned at least once per shift or every 1000 prints, whichever comes first.
Conclusion
PCB stencils play a critical role in the SMT assembly process, ensuring precise and consistent solder paste application for high-quality PCB assembly. By understanding the types of PCB stencils, their design considerations, manufacturing processes, and maintenance requirements, engineers and technicians can optimize the stencil design and production process for their specific applications. With proper use and care, PCB stencils can help to improve assembly quality, reduce defects, and increase production efficiency in a wide range of electronics manufacturing applications.
Leave a Reply