What is LED PCB Assembly?
LED PCB Assembly is the process of mounting LED components onto a printed circuit board to create a functional LED lighting module. The PCB serves as the foundation for the LED components, providing both mechanical support and electrical connections. The assembly process involves several steps, including PCB design, component selection, soldering, and testing.
Benefits of LED PCB Assembly
LED PCB assembly offers numerous benefits over traditional lighting solutions. Some of the key advantages include:
-
Energy Efficiency: LEDs are highly energy-efficient, consuming significantly less power than incandescent or fluorescent bulbs. This translates to lower energy costs and reduced environmental impact.
-
Long Lifespan: LEDs have a much longer lifespan compared to traditional lighting options. They can last up to 50,000 hours or more, reducing maintenance and replacement costs.
-
Customization: LED PCB assembly allows for a high degree of customization. The PCB layout and component selection can be tailored to meet specific lighting requirements, such as color temperature, brightness, and beam angle.
-
Compact Size: LEDs are small in size, allowing for compact and lightweight PCB designs. This makes them ideal for applications where space is limited, such as in portable devices or miniature lighting fixtures.
-
Durability: LEDs are solid-state devices, making them more resistant to shock, vibration, and extreme temperatures compared to traditional bulbs. This durability ensures reliable performance in demanding environments.
LED PCB Design Considerations
Designing an LED PCB requires careful consideration of various factors to ensure optimal performance and reliability. Some key design considerations include:
Thermal Management
LEDs generate heat during operation, which can impact their performance and lifespan if not properly managed. Effective thermal management is crucial in LED PCB design. This can be achieved through the use of heat sinks, thermal vias, and appropriate PCB materials with good thermal conductivity.
Current and Voltage Regulation
LEDs are sensitive to variations in current and voltage. Overdriving an LED can lead to premature failure, while underdriving can result in reduced brightness. Proper current and voltage regulation is essential to ensure consistent and reliable LED performance. This can be achieved through the use of constant current drivers or voltage regulators.
Optical Design
The optical design of an LED PCB involves considerations such as lens selection, reflector design, and light distribution. The choice of lens and reflector materials can impact the beam angle, color uniformity, and overall light output. Proper optical design ensures that the LED lighting meets the desired illumination requirements.
Component Selection
Selecting the right LED components is crucial for the success of an LED PCB assembly. Factors to consider include the LED type (surface mount or through-hole), color temperature, brightness, forward voltage, and viewing angle. Additionally, the selection of resistors, capacitors, and other supporting components should be based on the specific circuit requirements.
LED PCB Manufacturing Process
The manufacturing process for LED PCBs involves several steps to ensure high-quality and reliable assemblies. The typical steps in LED PCB manufacturing include:
PCB Fabrication
The first step in LED PCB manufacturing is the fabrication of the printed circuit board itself. This involves creating the copper traces, solder pads, and vias on the PCB substrate according to the design specifications. The PCB fabrication process includes steps such as etching, drilling, and plating.
Solder Paste Printing
Once the PCB is fabricated, solder paste is applied to the solder pads using a stencil or screen printing process. The solder paste consists of tiny solder particles suspended in a flux medium, which helps to clean and protect the metal surfaces during soldering.
Component Placement
The LED components, along with other supporting components, are then placed onto the PCB using automated pick-and-place machines. These machines accurately position the components based on the PCB design files, ensuring precise and consistent placement.
Reflow Soldering
After component placement, the PCB undergoes a reflow soldering process. The PCB is heated in a reflow oven, causing the solder paste to melt and form electrical and mechanical connections between the components and the PCB pads. The reflow soldering process is carefully controlled to ensure proper solder joint formation and to prevent component damage.
Inspection and Testing
Once the soldering process is complete, the LED PCB assembly undergoes thorough inspection and testing. Visual inspection is performed to check for any visible defects, such as solder bridges, component misalignment, or damaged components. Electrical testing is also conducted to verify the functionality and performance of the LED PCB assembly. This may include tests for brightness, color accuracy, and power consumption.
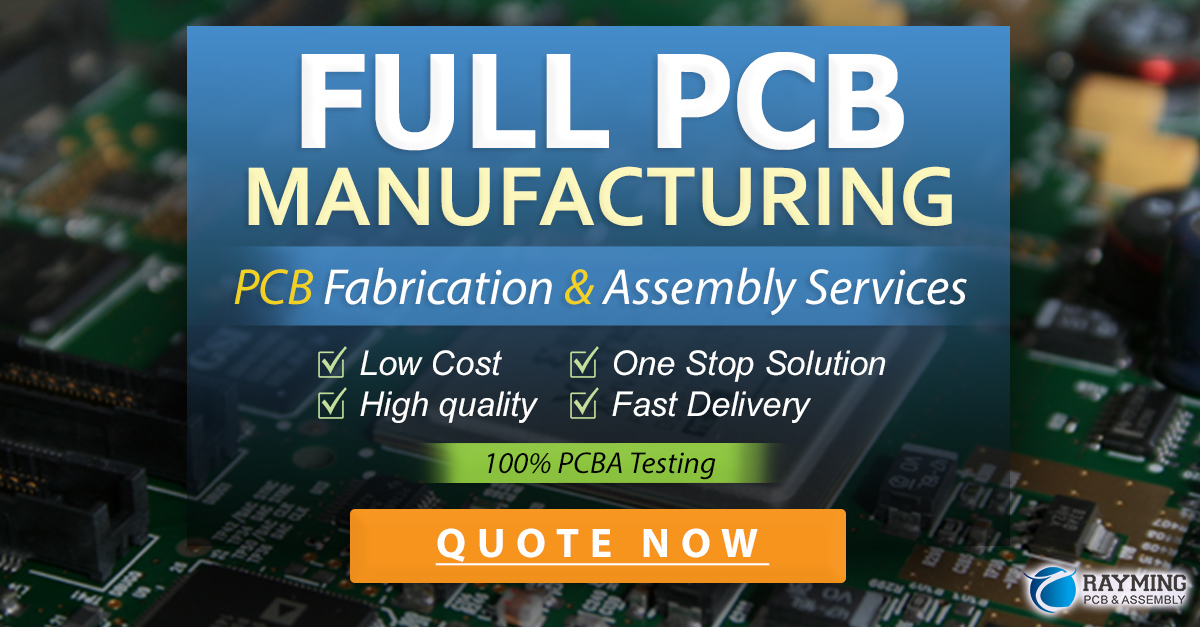
Quality Control in LED PCB Assembly
Ensuring the quality of LED PCB assemblies is critical for reliable and long-lasting LED lighting products. Several quality control measures are implemented throughout the manufacturing process, including:
Incoming Material Inspection
All incoming materials, including PCBs, LED components, and other parts, are inspected for quality and conformance to specifications. This ensures that only high-quality materials are used in the assembly process.
Process Control
The manufacturing process is closely monitored and controlled to maintain consistency and minimize defects. This includes regular equipment calibration, process parameter monitoring, and statistical process control (SPC) techniques.
Automated Optical Inspection (AOI)
AOI systems are used to automatically inspect the LED PCB assemblies for any defects or anomalies. These systems use high-resolution cameras and advanced image processing algorithms to detect issues such as solder defects, component placement errors, or missing components.
Functional Testing
Functional testing is performed to verify that the LED PCB assembly meets the specified performance requirements. This may include tests for light output, color consistency, and power consumption. Functional testing ensures that the LED lighting product will perform as intended in its intended application.
Burn-In Testing
Burn-in testing involves operating the LED PCB assembly under controlled conditions for an extended period to identify any early failures or performance degradation. This helps to screen out any potential reliability issues before the product is shipped to the customer.
Applications of LED PCB Assembly
LED PCB assembly finds applications in a wide range of industries and products. Some common applications include:
-
General Lighting: LED PCB assemblies are used in various general lighting applications, such as home lighting, office lighting, and commercial lighting. They provide energy-efficient and long-lasting lighting solutions for indoor and outdoor spaces.
-
Automotive Lighting: LED PCB assemblies are increasingly used in automotive lighting applications, including headlights, taillights, and interior lighting. They offer improved visibility, styling options, and energy efficiency compared to traditional automotive lighting.
-
Backlighting: LED PCB assemblies are commonly used for backlighting applications in displays, such as smartphones, tablets, and televisions. They provide uniform and bright illumination for the display panels.
-
Signage and Advertising: LED PCB assemblies are used in signage and advertising displays, offering vibrant colors, high brightness, and the ability to create dynamic and eye-catching visual effects.
-
Medical Devices: LED PCB assemblies find applications in various medical devices, such as endoscopes, surgical lights, and dental lamps. They provide focused and high-quality illumination for precise medical procedures.
Frequently Asked Questions (FAQ)
-
What are the advantages of using LED PCB assemblies over traditional lighting solutions?
LED PCB assemblies offer several advantages, including energy efficiency, long lifespan, customization options, compact size, and durability. They consume less power, last longer, and are more resistant to shock and vibration compared to traditional lighting solutions. -
How do I ensure proper thermal management in my LED PCB design?
Proper thermal management in LED PCB design can be achieved through the use of heat sinks, thermal vias, and appropriate PCB materials with good thermal conductivity. It is important to consider factors such as the LED power dissipation, ambient temperature, and PCB layout to effectively dissipate heat and maintain optimal LED performance. -
What is the difference between surface mount and through-hole LED components?
Surface mount LEDs (SMD LEDs) are mounted directly onto the surface of the PCB, while through-hole LEDs have leads that are inserted into holes drilled in the PCB. SMD LEDs are smaller, more compact, and suitable for automated assembly processes. Through-hole LEDs are typically larger and are often used in applications where mechanical stability is important. -
How do I select the right LED components for my PCB assembly?
When selecting LED components for your PCB assembly, consider factors such as the desired color temperature, brightness, forward voltage, and viewing angle. Additionally, consider the PCB layout, thermal management requirements, and the specific application needs. It is recommended to consult with LED manufacturers or suppliers to choose components that meet your specific requirements. -
What quality control measures are typically implemented in LED PCB assembly?
Quality control measures in LED PCB assembly include incoming material inspection, process control, automated optical inspection (AOI), functional testing, and burn-in testing. These measures help to ensure the use of high-quality materials, minimize defects, and verify the performance and reliability of the LED PCB assembly before it is shipped to the customer.
Conclusion
LED PCB assembly is a critical process in the manufacturing of LED lighting products, providing a one-stop solution for efficient and reliable lighting solutions. By understanding the benefits, design considerations, manufacturing processes, and quality control measures involved in LED PCB assembly, manufacturers can create high-quality and customized LED lighting products for various applications.
From energy efficiency and long lifespan to customization options and durability, LED PCB assemblies offer numerous advantages over traditional lighting solutions. However, successful LED PCB assembly requires careful consideration of thermal management, current and voltage regulation, optical design, and component selection.
The manufacturing process for LED PCBs involves PCB fabrication, solder paste printing, component placement, reflow soldering, and thorough inspection and testing. Quality control measures, such as incoming material inspection, process control, AOI, functional testing, and burn-in testing, ensure the production of high-quality and reliable LED PCB assemblies.
With their versatility and performance benefits, LED PCB assemblies find applications in various industries, including general lighting, automotive lighting, backlighting, signage and advertising, and medical devices. As technology continues to advance, the adoption of LED PCB assemblies is expected to grow, driving innovation and efficiency in the lighting industry.
By partnering with experienced LED PCB assembly providers, businesses can leverage the expertise and capabilities necessary to bring their LED lighting products to market quickly and cost-effectively. With a focus on quality, reliability, and customer satisfaction, LED PCB assembly offers a comprehensive solution for creating cutting-edge LED lighting products that meet the evolving needs of consumers and industries alike.
Characteristic | LED PCB Assembly |
---|---|
Energy Efficiency | High energy efficiency, consuming less power |
Lifespan | Long lifespan, up to 50,000 hours or more |
Customization | Highly customizable, tailored to specific lighting needs |
Size | Compact and lightweight PCB designs |
Durability | Resistant to shock, vibration, and extreme temperatures |
Thermal Management | Requires effective thermal management for optimal performance |
Current and Voltage | Sensitive to variations, proper regulation is essential |
Optical Design | Lens selection, reflector design, and light distribution |
Component Selection | Careful selection based on specific circuit requirements |
Manufacturing Process | Involves PCB fabrication, soldering, and testing |
Quality Control | Strict measures to ensure high-quality and reliable assemblies |
Applications | General lighting, automotive, backlighting, signage, medical |
In conclusion, LED PCB assembly is a one-stop solution for creating efficient, reliable, and customizable LED lighting products. By understanding the intricacies of LED PCB design, manufacturing, and quality control, businesses can leverage the benefits of LED technology to develop innovative and high-performance lighting solutions for a wide range of applications.
Leave a Reply