Introduction
Custom LED PCB Assembly is a complex process that requires careful planning, attention to detail, and adherence to best practices to ensure success. Failing to properly execute any step in the assembly process can lead to costly delays, defects, and even complete failure of the final product. In this article, we will explore seven key ways to prevent the case of failing custom LED PCB assembly, helping you to optimize your manufacturing process and deliver high-quality products to your customers.
1. Choose the Right PCB Material
Importance of PCB Material Selection
Selecting the appropriate PCB material is crucial for the success of your custom LED PCB assembly. The material you choose will impact the performance, durability, and reliability of your final product. Some key factors to consider when choosing a PCB material include:
- Thermal conductivity
- Dielectric constant
- Coefficient of thermal expansion (CTE)
- Mechanical strength
- Cost
Common PCB Materials for LED Applications
There are several PCB materials commonly used in LED applications, each with its own advantages and disadvantages. Some popular options include:
- FR-4: A cost-effective, versatile material with good mechanical and electrical properties.
- Aluminum-backed PCBs: Offer excellent thermal dissipation, making them ideal for high-power LED applications.
- Metal Core PCBs (MCPCBs): Provide superior thermal management and are often used in high-brightness LED applications.
- Ceramic PCBs: Offer excellent thermal stability and are suitable for high-temperature LED applications.
Material | Thermal Conductivity (W/mK) | Dielectric Constant | CTE (ppm/°C) | Mechanical Strength | Cost |
---|---|---|---|---|---|
FR-4 | 0.3 – 0.4 | 4.5 – 5.0 | 12 – 16 | Good | Low |
Aluminum-backed PCBs | 1.0 – 2.0 | 4.5 – 5.0 | 12 – 16 | Good | Medium |
MCPCBs | 2.0 – 4.0 | 4.5 – 5.0 | 12 – 16 | Good | High |
Ceramic PCBs | 20 – 30 | 9.0 – 10.0 | 6 – 8 | Excellent | Very High |
2. Optimize PCB Design
Importance of PCB Design Optimization
Optimizing your PCB design is essential for preventing failures in custom LED PCB assembly. A well-designed PCB will not only improve the performance and reliability of your final product but also simplify the manufacturing process, reducing the risk of defects and delays. Some key aspects to consider when optimizing your PCB design include:
- Component placement
- Trace routing
- Thermal management
- Signal integrity
- Manufacturing considerations
Best Practices for PCB Design Optimization
To optimize your PCB design for custom LED PCB assembly, follow these best practices:
- Place components strategically to minimize trace lengths and improve signal integrity.
- Use appropriate trace widths and spacing to ensure proper current carrying capacity and minimize crosstalk.
- Incorporate thermal management features, such as thermal vias and heat spreaders, to dissipate heat effectively.
- Follow manufacturing guidelines for minimum trace widths, spacing, and hole sizes to ensure compatibility with your chosen assembly process.
- Conduct thorough design reviews and simulations to identify and address potential issues before manufacturing.
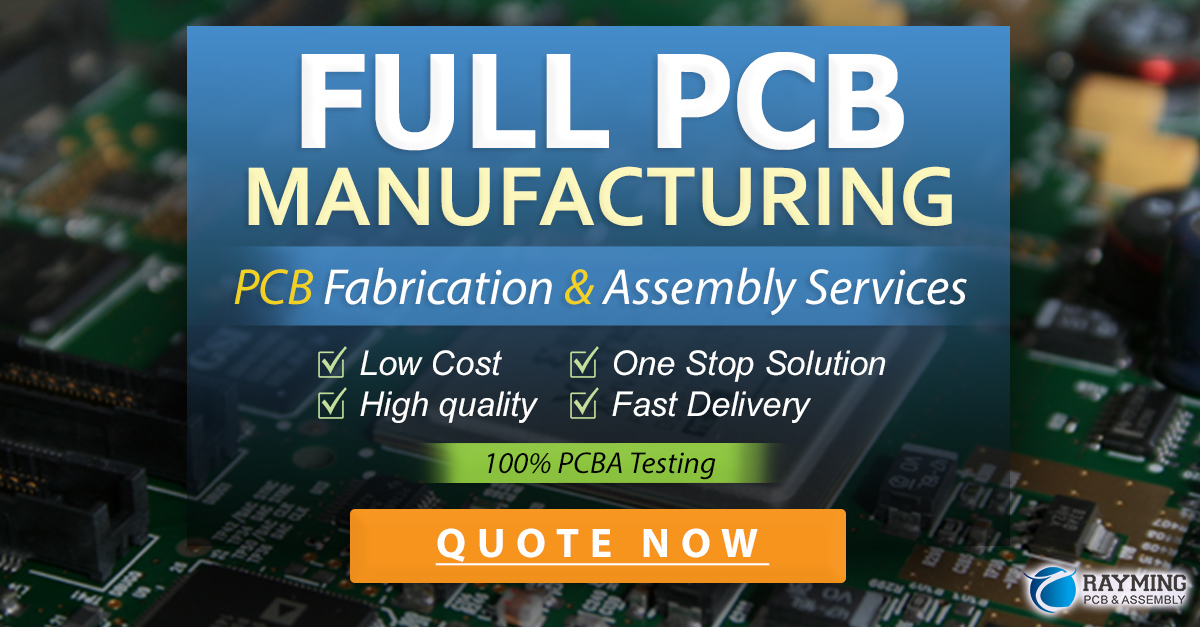
3. Select Reliable Components
Importance of Component Selection
Choosing reliable components is crucial for preventing failures in custom LED PCB assembly. Low-quality or counterfeit components can lead to premature failure, reduced performance, and even safety hazards. When selecting components for your LED PCB assembly, consider the following factors:
- Manufacturer reputation
- Component specifications
- Quality certifications
- Availability and lead times
- Cost
Identifying Reliable Component Suppliers
To ensure that you are sourcing reliable components for your custom LED PCB assembly, follow these tips:
- Choose reputable manufacturers with a proven track record of producing high-quality components.
- Verify that the components meet the required specifications for your application, such as voltage, current, and temperature ratings.
- Look for components with relevant quality certifications, such as ISO 9001, IATF 16949, or UL.
- Consider the availability and lead times of components to avoid supply chain disruptions.
- Compare costs from multiple suppliers to ensure you are getting the best value without compromising on quality.
4. Implement Robust Quality Control
Importance of Quality Control in LED PCB Assembly
Implementing robust quality control measures is essential for preventing failures in custom LED PCB assembly. Effective quality control helps to identify and address defects early in the manufacturing process, reducing the risk of costly rework or product recalls. Some key aspects of quality control in LED PCB assembly include:
- Incoming inspection
- In-process inspection
- Final inspection
- Testing and validation
- Continuous improvement
Best Practices for Quality Control in LED PCB Assembly
To implement robust quality control in your custom LED PCB assembly process, follow these best practices:
- Establish clear quality standards and acceptance criteria for incoming components and materials.
- Implement in-process inspection points to identify and correct defects as early as possible.
- Conduct thorough final inspections to ensure that finished products meet all specified requirements.
- Perform rigorous testing and validation to verify the performance, reliability, and safety of your LED PCB assemblies.
- Foster a culture of continuous improvement by regularly reviewing quality data and implementing corrective actions as needed.
5. Collaborate with Experienced Assembly Partners
Benefits of Partnering with Experienced Assembly Providers
Collaborating with experienced assembly partners can significantly reduce the risk of failures in custom LED PCB assembly. Experienced assembly providers offer several benefits, including:
- Expertise in LED PCB assembly processes and best practices
- Access to advanced manufacturing equipment and technologies
- Robust quality control systems and procedures
- Ability to scale production to meet changing demand
- Support for design optimization and manufacturability improvements
Selecting the Right Assembly Partner
To select the right assembly partner for your custom LED PCB assembly needs, consider the following factors:
- Experience and expertise in LED PCB assembly
- Quality certifications and standards compliance
- Manufacturing capabilities and capacity
- Communication and collaboration processes
- Cost and lead time competitiveness
By partnering with an experienced and reliable assembly provider, you can leverage their expertise and resources to optimize your LED PCB assembly process and prevent costly failures.
6. Conduct Thorough Testing and Validation
Importance of Testing and Validation
Conducting thorough testing and validation is essential for preventing failures in custom LED PCB assembly. Testing and validation help to ensure that your LED PCB assemblies meet all specified performance, reliability, and safety requirements. Some key types of testing and validation for LED PCB assemblies include:
- Functional testing
- Environmental testing
- Accelerated life testing
- Compliance testing
- Failure analysis
Best Practices for Testing and Validation
To conduct effective testing and validation for your custom LED PCB assemblies, follow these best practices:
- Develop a comprehensive test plan that covers all relevant performance, reliability, and safety aspects.
- Use appropriate test equipment and methods to simulate real-world operating conditions.
- Establish clear pass/fail criteria and acceptance thresholds for each test.
- Document all test results and analyze data to identify potential issues or areas for improvement.
- Conduct failure analysis on any defective units to determine root causes and implement corrective actions.
By investing in thorough testing and validation, you can proactively identify and address potential failure modes, ensuring the quality and reliability of your custom LED PCB assemblies.
7. Foster Continuous Improvement
Importance of Continuous Improvement in LED PCB Assembly
Fostering a culture of continuous improvement is crucial for preventing failures in custom LED PCB assembly over the long term. Continuous improvement involves regularly reviewing your assembly processes, identifying areas for optimization, and implementing changes to enhance quality, efficiency, and reliability. Some key benefits of continuous improvement in LED PCB assembly include:
- Reduced defect rates and rework costs
- Improved product performance and reliability
- Increased manufacturing efficiency and throughput
- Enhanced customer satisfaction and loyalty
- Ability to adapt to changing market demands and technologies
Best Practices for Continuous Improvement in LED PCB Assembly
To foster continuous improvement in your custom LED PCB assembly process, follow these best practices:
- Establish clear metrics and key performance indicators (KPIs) to track assembly process performance.
- Regularly review process data and identify areas for improvement using tools such as root cause analysis and Pareto charts.
- Engage employees at all levels in identifying and implementing improvement ideas, using techniques such as kaizen events and suggestion systems.
- Collaborate with suppliers and customers to gather feedback and insights on product performance and quality.
- Invest in training and development to keep employees up-to-date with the latest assembly technologies and best practices.
By embracing a culture of continuous improvement, you can proactively prevent failures in your custom LED PCB assembly process and ensure long-term success in a competitive market.
Frequently Asked Questions (FAQ)
- What are the most common causes of failure in custom LED PCB assembly?
Some of the most common causes of failure in custom LED PCB assembly include: - Poor component selection and quality
- Inadequate PCB design and layout
- Insufficient thermal management
- Improper handling and assembly processes
-
Lack of testing and validation
-
How can I ensure that I am selecting reliable components for my LED PCB assembly?
To ensure that you are selecting reliable components, follow these tips: - Choose reputable manufacturers with a proven track record
- Verify that components meet required specifications
- Look for relevant quality certifications
- Consider availability and lead times
-
Compare costs from multiple suppliers
-
What are the benefits of partnering with an experienced assembly provider for custom LED PCB assembly?
Partnering with an experienced assembly provider offers several benefits, including: - Expertise in LED PCB assembly processes and best practices
- Access to advanced manufacturing equipment and technologies
- Robust quality control systems and procedures
- Ability to scale production to meet changing demand
-
Support for design optimization and manufacturability improvements
-
How can I implement effective quality control in my custom LED PCB assembly process?
To implement effective quality control, follow these best practices: - Establish clear quality standards and acceptance criteria
- Implement in-process inspection points
- Conduct thorough final inspections
- Perform rigorous testing and validation
-
Foster a culture of continuous improvement
-
What role does continuous improvement play in preventing failures in custom LED PCB assembly?
Continuous improvement plays a crucial role in preventing failures by: - Reducing defect rates and rework costs
- Improving product performance and reliability
- Increasing manufacturing efficiency and throughput
- Enhancing customer satisfaction and loyalty
- Enabling adaptation to changing market demands and technologies
Conclusion
Preventing failures in custom LED PCB assembly requires a comprehensive approach that encompasses PCB design, component selection, quality control, testing, and continuous improvement. By following the seven key strategies outlined in this article, you can optimize your assembly process, ensure the reliability and performance of your LED PCB assemblies, and ultimately, deliver high-quality products to your customers.
Remember to choose the right PCB material, optimize your PCB design, select reliable components, implement robust quality control, collaborate with experienced assembly partners, conduct thorough testing and validation, and foster a culture of continuous improvement. By adopting these best practices, you can minimize the risk of costly failures and position your business for long-term success in the competitive LED PCB assembly market.
Leave a Reply