Introduction to PCB Manufacturing
Printed Circuit Board (PCB) manufacturing is a complex process that involves the creation of electronic circuits on a non-conductive substrate. PCBs are essential components in almost all electronic devices, from smartphones and computers to medical equipment and aerospace systems. The PCB manufacturing process involves several stages, including design, fabrication, assembly, and testing.
The Importance of PCB Manufacturing
PCB manufacturing is crucial for the electronics industry because it enables the creation of compact, reliable, and cost-effective electronic devices. PCBs allow for the miniaturization of electronic components, which is essential for the development of smaller and more powerful devices. Additionally, PCBs provide a stable and secure platform for electronic components, ensuring that they function correctly and reliably.
The PCB Manufacturing Process
The PCB manufacturing process consists of several stages, each of which is critical to the quality and reliability of the final product. The stages include:
-
Design: The PCB design is created using specialized software, such as Altium Designer or Eagle. The design includes the layout of the electronic components, the routing of the traces, and the placement of the vias and pads.
-
Fabrication: The PCB fabrication process involves the creation of the physical board. This process typically involves the following steps:
-
Printing the circuit pattern onto a Copper-Clad Laminate using a photoresist and exposure to UV light.
- Etching away the unwanted copper to create the circuit traces.
- Drilling holes for vias and component leads.
-
Applying a solder mask and silkscreen to protect the board and label the components.
-
Assembly: The PCB Assembly process involves the placement and soldering of electronic components onto the board. This process can be done manually or using automated equipment, such as pick-and-place machines and reflow ovens.
-
Testing: The final stage of the PCB manufacturing process is testing. This stage involves verifying that the board functions correctly and meets the required specifications. Testing can include visual inspection, automated optical inspection (AOI), X-ray inspection, and functional testing.
PCB Assembly Techniques
PCB assembly is the process of placing and soldering electronic components onto a printed circuit board. There are two main techniques used for PCB assembly: through-hole and surface mount.
Through-Hole Assembly
Through-hole assembly involves the use of components with long leads that are inserted into holes drilled in the PCB. The leads are then soldered to the pads on the opposite side of the board. Through-hole assembly is typically used for larger components, such as capacitors and resistors, and for components that require a more secure connection, such as connectors and switches.
Surface Mount Assembly
Surface mount assembly involves the use of components that are placed directly onto pads on the surface of the PCB. The components are then soldered to the pads using a reflow oven or a wave soldering machine. Surface mount assembly is typically used for smaller components, such as integrated circuits and resistors, and for high-density PCBs.
Comparison of Through-Hole and Surface Mount Assembly
Feature | Through-Hole Assembly | Surface Mount Assembly |
---|---|---|
Component Size | Larger components | Smaller components |
Connection Strength | More secure connection | Less secure connection |
PCB Density | Lower density | Higher density |
Assembly Speed | Slower | Faster |
Cost | Higher cost | Lower cost |
PCB Manufacturing Capabilities
PCB manufacturers offer a range of capabilities to meet the needs of different applications and industries. These capabilities include:
Multi-Layer PCBs
Multi-layer PCBs are boards that consist of multiple layers of copper traces separated by insulating layers. Multi-layer PCBs allow for higher density and more complex designs than single-layer boards. They are typically used in applications that require high speed, high power, or high density, such as telecommunications equipment and aerospace systems.
Flexible PCBs
Flexible PCBs are boards that are made from flexible materials, such as polyimide or polyester. Flexible PCBs can be bent or folded to fit into tight spaces or to conform to irregular shapes. They are typically used in applications that require flexibility, such as wearable devices and medical equipment.
High-Density Interconnect (HDI) PCBs
High-Density Interconnect (HDI) PCBs are boards that have a higher density of interconnects than traditional PCBs. HDI PCBs use smaller vias and pads, as well as finer pitch components, to achieve higher density. They are typically used in applications that require high performance and small form factors, such as smartphones and tablets.
Rigid-Flex PCBs
Rigid-flex PCBs are boards that combine rigid and flexible sections in a single board. The rigid sections provide stability and support for components, while the flexible sections allow for bending and folding. Rigid-flex PCBs are typically used in applications that require both flexibility and stability, such as automotive electronics and industrial control systems.
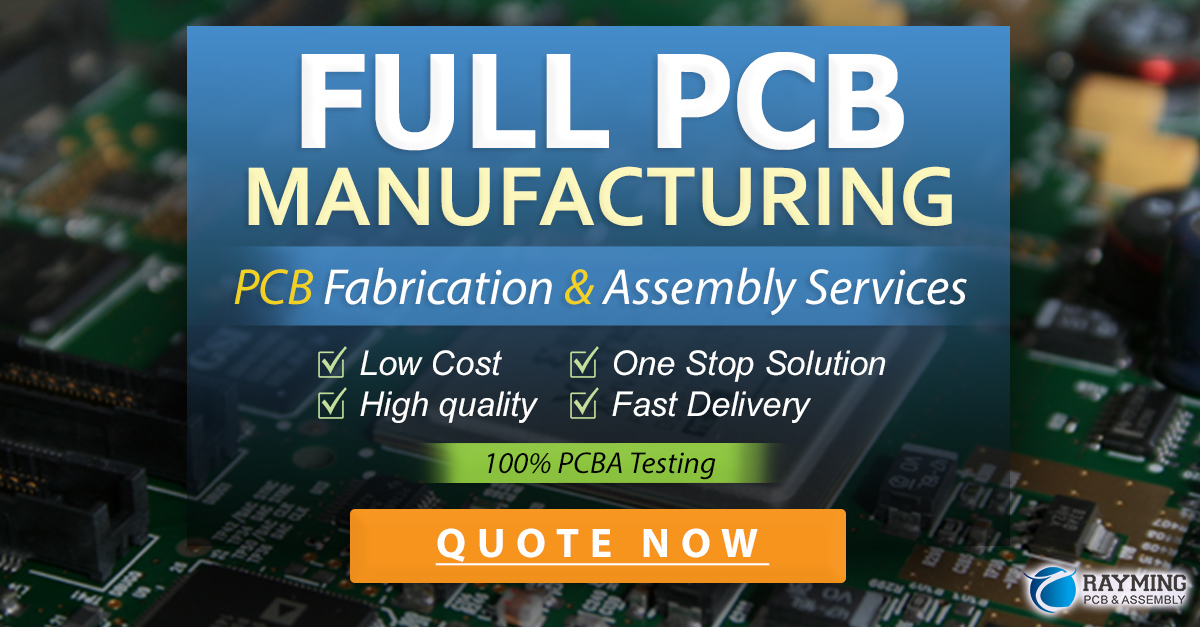
PCB Testing and Inspection
PCB testing and inspection are critical steps in the PCB manufacturing process. They ensure that the board functions correctly and meets the required specifications. There are several methods used for PCB testing and inspection, including:
Automated Optical Inspection (AOI)
Automated Optical Inspection (AOI) is a method of inspecting PCBs using cameras and image processing software. AOI systems can detect a wide range of defects, such as missing components, solder bridges, and incorrect component placement. AOI is typically used for high-volume production and can inspect boards at a rate of up to 100 per minute.
X-Ray Inspection
X-ray inspection is a method of inspecting PCBs using X-rays to penetrate the board and detect defects that are not visible on the surface. X-ray inspection can detect defects such as voids in solder joints, missing or misaligned components, and broken traces. X-ray inspection is typically used for high-reliability applications, such as aerospace and medical equipment.
Functional Testing
Functional testing is a method of testing PCBs by applying power and signals to the board and verifying that it functions correctly. Functional testing can detect defects such as short circuits, open circuits, and incorrect component values. Functional testing is typically done using specialized test equipment, such as in-circuit testers and boundary scan testers.
PCB Design Considerations
PCB design is a critical step in the PCB manufacturing process. A well-designed PCB can improve the performance, reliability, and manufacturability of the final product. There are several considerations that should be taken into account when designing a PCB, including:
Component Placement
Component placement is the process of determining the location of components on the PCB. Good component placement can improve the routing of traces, reduce the length of traces, and improve the overall performance of the board. Component placement should take into account factors such as thermal management, signal integrity, and manufacturability.
Trace Routing
Trace routing is the process of determining the path of the copper traces on the PCB. Good trace routing can reduce signal reflections, crosstalk, and electromagnetic interference (EMI). Trace routing should take into account factors such as trace width, spacing, and impedance matching.
Thermal Management
Thermal management is the process of ensuring that the PCB and its components operate within their specified temperature range. Good thermal management can improve the reliability and lifespan of the board. Thermal management techniques include the use of heatsinks, thermal vias, and copper pours.
Signal Integrity
Signal integrity is the process of ensuring that signals on the PCB are transmitted accurately and reliably. Good signal integrity can reduce signal distortion, jitter, and bit errors. Signal integrity techniques include the use of impedance matching, termination, and differential signaling.
Frequently Asked Questions (FAQ)
What is the difference between a PCB and a PCBA?
A PCB (Printed Circuit Board) is the bare board without any components mounted on it. A PCBA (Printed Circuit Board Assembly) is a PCB with components mounted on it.
What are the different types of PCBs?
There are several types of PCBs, including:
- Single-Layer PCBs: PCBs with one layer of copper traces.
- Double-layer PCBs: PCBs with two layers of copper traces, one on each side of the board.
- Multi-layer PCBs: PCBs with more than two layers of copper traces, separated by insulating layers.
- Flexible PCBs: PCBs made from flexible materials that can be bent or folded.
- Rigid-flex PCBs: PCBs that combine rigid and flexible sections in a single board.
What is the difference between through-hole and surface mount assembly?
Through-hole assembly involves the use of components with long leads that are inserted into holes drilled in the PCB and soldered to pads on the opposite side of the board. Surface mount assembly involves the use of components that are placed directly onto pads on the surface of the PCB and soldered using a reflow oven or wave soldering machine.
What are some common PCB manufacturing defects?
Common PCB manufacturing defects include:
- Solder bridges: Unintended connections between two or more solder joints.
- Cold solder joints: Solder joints that have not been heated sufficiently, resulting in a weak or incomplete connection.
- Tombstoning: When a component lifts off the PCB during the soldering process, standing up on one end like a tombstone.
- Misaligned components: When components are not placed correctly on the PCB, resulting in poor connections or short circuits.
How can I ensure the quality of my PCBs?
To ensure the quality of your PCBs, you should:
- Work with a reputable PCB manufacturer that has experience in your industry and can meet your specific requirements.
- Provide clear and accurate design files, including Gerber files, drill files, and assembly drawings.
- Specify your requirements for materials, finishes, and tolerances.
- Request a prototype or sample before placing a full production order.
- Perform thorough testing and inspection of the finished boards to ensure they meet your specifications.
Conclusion
PCB manufacturing is a complex process that requires expertise in design, fabrication, assembly, and testing. By understanding the different techniques and capabilities of PCB manufacturing, designers and engineers can create high-quality, reliable, and cost-effective electronic products.
When designing a PCB, it is important to consider factors such as component placement, trace routing, thermal management, and signal integrity. By taking these factors into account, designers can improve the performance, reliability, and manufacturability of their boards.
Finally, thorough testing and inspection are critical to ensuring the quality of the finished product. By using techniques such as automated optical inspection, X-ray inspection, and functional testing, manufacturers can detect and correct defects before the boards are shipped to customers.
Leave a Reply