Introduction to Halogen-Free PCBs
Halogen-free Printed Circuit Boards (PCBs) have gained significant popularity in recent years due to growing environmental concerns and stricter regulations regarding the use of hazardous materials in electronic products. As we move towards a more sustainable future, understanding the importance of halogen-free PCBs and their role in the electronics industry becomes crucial. In this comprehensive guide, we will explore the concept of halogen-free PCBs, their benefits, and their applications in various sectors.
What are Halogens?
Halogens are a group of chemical elements that include fluorine (F), chlorine (Cl), bromine (Br), iodine (I), and astatine (At). These elements are highly reactive and can form strong bonds with other elements, making them useful in various industrial applications. However, when halogens are used in the production of PCBs, they can pose significant risks to both human health and the environment.
The Risks Associated with Halogens in PCBs
Traditional PCBs often contain halogenated flame retardants (HFRs) to improve their fire resistance properties. While these additives enhance the safety of PCBs, they can also lead to several negative consequences:
- Toxicity: When exposed to high temperatures or fire, HFRs can release toxic fumes containing dioxins and furans, which are known carcinogens and can cause serious health issues.
- Environmental Pollution: The improper disposal of PCBs containing HFRs can lead to the release of these hazardous substances into the environment, contaminating soil, water, and air.
- Recycling Difficulties: PCBs with HFRs are more challenging to recycle, as the presence of halogens complicates the recycling process and can result in the formation of toxic byproducts.
What are Halogen-Free PCBs?
Halogen-free PCBs are printed circuit boards that do not contain any halogenated flame retardants or other halogenated materials. These PCBs are manufactured using alternative, non-toxic flame retardants that provide similar fire resistance properties without the associated risks.
Characteristics of Halogen-Free PCBs
- Absence of Halogens: Halogen-free PCBs are produced without the use of any halogenated materials, ensuring that they do not release toxic fumes when exposed to high temperatures or fire.
- Eco-Friendly: By eliminating the use of hazardous substances, halogen-free PCBs are more environmentally friendly and contribute to a greener electronics industry.
- Compliance with Regulations: Halogen-free PCBs help manufacturers comply with various international regulations and directives, such as RoHS (Restriction of Hazardous Substances) and WEEE (Waste Electrical and Electronic Equipment).
- Improved Recyclability: The absence of halogens in these PCBs makes them easier to recycle, reducing electronic waste and promoting a circular economy.
Benefits of Using Halogen-Free PCBs
- Enhanced Safety: Halogen-free PCBs minimize the risk of toxic fume release during high-temperature exposure or fire, ensuring a safer environment for both manufacturers and end-users.
- Environmental Sustainability: By reducing the use of hazardous substances, halogen-free PCBs contribute to a cleaner and more sustainable environment.
- Regulatory Compliance: Adopting halogen-free PCBs helps manufacturers meet strict environmental regulations and avoid potential penalties or legal issues.
- Improved Public Image: Companies that prioritize the use of halogen-free PCBs demonstrate their commitment to environmental responsibility, enhancing their public image and attracting environmentally conscious consumers.
Applications of Halogen-Free PCBs
Halogen-free PCBs find applications in various industries and sectors, including:
- Consumer Electronics: Smartphones, laptops, tablets, and other consumer electronic devices increasingly use halogen-free PCBs to meet environmental standards and consumer expectations.
- Automotive Industry: As vehicles incorporate more electronic components, halogen-free PCBs play a crucial role in ensuring the safety and reliability of these systems.
- Medical Devices: Halogen-free PCBs are essential in medical equipment to minimize the risk of toxic fume release and ensure patient safety.
- Industrial Equipment: In industrial settings, halogen-free PCBs are used in control systems, sensors, and other electronic components to improve safety and environmental performance.
- Aerospace and Defense: Halogen-free PCBs are employed in critical aerospace and defense applications, where reliability and safety are of utmost importance.
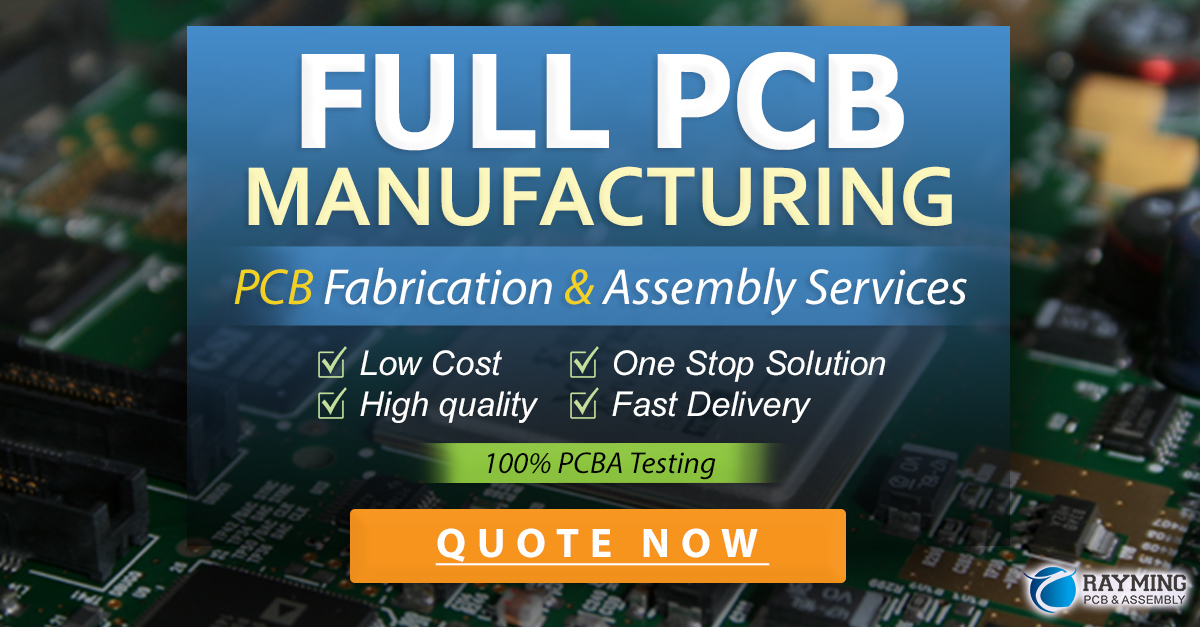
Halogen-Free PCB materials and Manufacturing Process
Common Halogen-Free PCB Materials
- Polyphenylene Oxide (PPO): PPO is a high-performance, halogen-free material that offers excellent electrical and mechanical properties, making it suitable for demanding applications.
- Polyethylene Terephthalate (PET): PET is a cost-effective, halogen-free material that provides good electrical insulation and mechanical strength.
- Polyimide (PI): PI is a high-temperature, halogen-free material that offers exceptional thermal stability and mechanical properties, making it ideal for harsh environments.
Manufacturing Process for Halogen-Free PCBs
The manufacturing process for halogen-free PCBs is similar to that of traditional PCBs, with a few key differences:
- Material Selection: Manufacturers choose halogen-free materials, such as PPO, PET, or PI, based on the specific requirements of the application.
- Lamination: The selected halogen-free material is laminated to form the PCB Substrate.
- Drilling and Plating: Holes are drilled into the substrate, and the walls of the holes are plated with copper to establish electrical connections between layers.
- Patterning: The desired circuit pattern is transferred onto the PCB using photolithography and etching processes.
- Surface Finishing: A protective surface finish, such as ENIG (Electroless Nickel Immersion Gold) or OSP (Organic Solderability Preservative), is applied to the PCB to improve solderability and protect the exposed copper.
- Quality Control: Strict quality control measures are implemented throughout the manufacturing process to ensure that the halogen-free PCBs meet the required specifications and standards.
Standards and Regulations for Halogen-Free PCBs
Several international standards and regulations govern the use of halogen-free materials in PCBs:
- RoHS (Restriction of Hazardous Substances): This European Union directive restricts the use of certain hazardous substances, including some halogens, in electrical and electronic equipment.
- WEEE (Waste Electrical and Electronic Equipment): This EU directive aims to reduce electronic waste and promote the recycling and proper disposal of electrical and electronic equipment.
- IEC 61249-2-21: This international standard specifies the requirements for halogen-free materials used in the manufacture of PCBs and other electronic components.
- JEDEC JS709: This standard, developed by the Joint Electron Device Engineering Council (JEDEC), provides guidelines for the use of halogen-free materials in electronic products.
By adhering to these standards and regulations, manufacturers can ensure that their halogen-free PCBs are compliant and environmentally friendly.
Challenges and Future Prospects
Challenges in Adopting Halogen-Free PCBs
- Cost: Halogen-free materials may be more expensive than traditional PCB materials, which can increase the overall cost of production.
- Performance: Some halogen-free materials may not offer the same level of performance as their halogenated counterparts, particularly in terms of fire resistance and thermal stability.
- Supply Chain: Ensuring a consistent and reliable supply of halogen-free materials can be challenging, as not all suppliers may offer these options.
Future Prospects for Halogen-Free PCBs
Despite the challenges, the future of halogen-free PCBs looks promising:
- Increasing Demand: As environmental awareness grows and regulations become stricter, the demand for halogen-free PCBs is expected to increase significantly in the coming years.
- Technological Advancements: Ongoing research and development efforts are focused on improving the performance and cost-effectiveness of halogen-free materials, making them more attractive to manufacturers.
- Industry Collaboration: Collaboration among material suppliers, PCB manufacturers, and end-users is crucial in driving the adoption of halogen-free PCBs and promoting a more sustainable electronics industry.
Frequently Asked Questions (FAQ)
- Q: Are halogen-free PCBs more expensive than traditional PCBs?
A: Yes, halogen-free PCBs may be slightly more expensive due to the higher cost of halogen-free materials. However, the price difference is expected to decrease as demand grows and production scales up. - Q: Can halogen-free PCBs be used in all applications?
A: Halogen-free PCBs can be used in most applications, but their suitability may depend on specific performance requirements. Some high-performance applications may still require the use of halogenated materials. - Q: How can I ensure that the PCBs I purchase are halogen-free?
A: When purchasing PCBs, look for certifications and compliance with relevant standards, such as RoHS and IEC 61249-2-21. You can also request documentation from the manufacturer to verify the use of halogen-free materials. - Q: Do halogen-free PCBs have a shorter lifespan than traditional PCBs?
A: The lifespan of halogen-free PCBs is comparable to that of traditional PCBs, provided they are manufactured using high-quality materials and processes. Proper design and handling can also help extend the lifespan of halogen-free PCBs. - Q: Can halogen-free PCBs be recycled?
A: Yes, halogen-free PCBs are generally easier to recycle than PCBs containing halogenated materials. The absence of halogens simplifies the recycling process and reduces the risk of generating toxic byproducts.
Conclusion
Halogen-free PCBs represent a significant step forward in the pursuit of a more sustainable and environmentally friendly electronics industry. By eliminating the use of hazardous halogenated materials, these PCBs offer numerous benefits, including enhanced safety, reduced environmental impact, and improved recyclability. As regulations become stricter and consumer demand for eco-friendly products grows, the adoption of halogen-free PCBs is expected to accelerate in the coming years.
However, the transition to halogen-free PCBs is not without challenges. Manufacturers must carefully navigate the trade-offs between cost, performance, and environmental impact while ensuring compliance with relevant standards and regulations. Ongoing research and development efforts, as well as collaboration among industry stakeholders, will be crucial in overcoming these challenges and driving the widespread adoption of halogen-free PCBs.
As we look ahead to 2024 and beyond, it is clear that halogen-free PCBs will play an increasingly important role in shaping the future of the electronics industry. By embracing this technology and prioritizing environmental sustainability, manufacturers can not only contribute to a greener future but also position themselves for long-term success in a rapidly evolving market.
Leave a Reply