Introduction to PCB Substrate
Printed Circuit Boards (PCBs) are the backbone of modern electronics. They provide a platform for electronic components to be mounted and connected, forming a functional circuit. One of the critical elements of a PCB is its substrate material. The substrate is the foundation upon which the copper traces, pads, and other features are built. It plays a crucial role in determining the performance, reliability, and cost of the final product. In this article, we will explore the various aspects of PCB substrate materials, their properties, and their applications.
Types of PCB Substrate Materials
There are several types of PCB substrate materials available, each with its own unique properties and advantages. The choice of substrate material depends on factors such as the intended application, environmental conditions, frequency of operation, and cost constraints. Some of the most common PCB substrate materials include:
1. FR-4
FR-4 (Flame Retardant 4) is the most widely used PCB substrate material. It is a composite material made of woven fiberglass cloth impregnated with an epoxy resin. FR-4 offers good mechanical strength, electrical insulation, and thermal stability. It is suitable for a wide range of applications, from consumer electronics to industrial control systems.
Advantages of FR-4:
- Low cost
- Good mechanical strength
- Excellent electrical insulation
- Flame retardant properties
- Wide availability
Disadvantages of FR-4:
- Limited high-frequency performance
- Higher dielectric constant compared to some other materials
- Moisture absorption can affect electrical properties
2. Rogers Materials
Rogers Corporation is a leading manufacturer of high-performance PCB substrate materials. They offer a range of products designed for demanding applications, such as high-frequency RF and microwave circuits, aerospace, and defense systems. Some popular Rogers materials include:
a. RO4000 Series
The RO4000 series is a family of high-frequency laminate materials. They offer low dielectric constant and loss tangent, making them suitable for applications up to 40 GHz. The RO4000 series includes materials like RO4003C and RO4350B.
b. RT/duroid
RT/duroid is another line of high-performance substrate materials from Rogers. They are known for their excellent electrical properties, low moisture absorption, and thermal stability. RT/duroid materials, such as 5870 and 6002, are commonly used in satellite communication, radar systems, and wireless infrastructure.
3. Polyimide
Polyimide is a high-temperature resistant polymer material used in PCB substrates. It offers excellent thermal stability, mechanical strength, and chemical resistance. Polyimide PCBs can withstand temperatures up to 260°C, making them suitable for harsh environments and high-reliability applications.
Advantages of Polyimide:
- High temperature resistance
- Excellent mechanical strength
- Good chemical resistance
- Low dielectric constant and loss tangent
Disadvantages of Polyimide:
- Higher cost compared to FR-4
- Challenging to process and fabricate
- Limited availability compared to FR-4
4. PTFE (Teflon)
PTFE (Polytetrafluoroethylene), also known as Teflon, is a fluoropolymer material with exceptional electrical properties. It has a very low dielectric constant and loss tangent, making it ideal for high-frequency applications. PTFE PCBs are commonly used in radar systems, satellite communication, and RF/microwave circuits.
Advantages of PTFE:
- Excellent high-frequency performance
- Very low dielectric constant and loss tangent
- High temperature resistance
- Low moisture absorption
Disadvantages of PTFE:
- High cost
- Difficult to process and fabricate
- Limited mechanical strength compared to other materials
Properties of PCB Substrate Materials
When selecting a PCB substrate material, several key properties need to be considered. These properties determine the performance, reliability, and suitability of the material for a given application. Let’s take a closer look at some of these properties:
1. Dielectric Constant (Dk)
The dielectric constant, also known as relative permittivity, is a measure of a material’s ability to store electrical energy in an electric field. It is the ratio of the permittivity of the material to the permittivity of vacuum. A lower dielectric constant is desirable for high-frequency applications, as it reduces signal propagation delay and minimizes signal distortion.
Material | Dielectric Constant (Dk) |
---|---|
FR-4 | 4.2 – 4.5 |
RO4003C | 3.38 |
RT/duroid 5870 | 2.33 |
Polyimide | 3.5 – 3.8 |
PTFE | 2.1 |
2. Loss Tangent (Df)
The loss tangent, also known as dissipation factor, is a measure of the energy lost in a material as heat when an electric field is applied. It represents the inefficiency of the material in transmitting electromagnetic energy. A lower loss tangent is desirable for high-frequency applications, as it minimizes signal attenuation and improves signal integrity.
Material | Loss Tangent (Df) |
---|---|
FR-4 | 0.02 |
RO4003C | 0.0027 |
RT/duroid 5870 | 0.0012 |
Polyimide | 0.002 – 0.003 |
PTFE | 0.0002 |
3. Thermal Conductivity
Thermal conductivity is a measure of a material’s ability to conduct heat. It is important for PCB substrates, as it affects the dissipation of heat generated by electronic components. A higher thermal conductivity helps in preventing hotspots and improving the overall thermal management of the PCB.
Material | Thermal Conductivity (W/mK) |
---|---|
FR-4 | 0.3 – 0.4 |
RO4003C | 0.71 |
RT/duroid 5870 | 0.22 |
Polyimide | 0.2 – 0.3 |
PTFE | 0.25 |
4. Glass Transition Temperature (Tg)
The glass transition temperature (Tg) is the temperature at which a material transitions from a rigid, glassy state to a softer, rubbery state. It is a critical property for PCB substrates, as it determines the maximum operating temperature of the PCB. A higher Tg allows the PCB to withstand higher temperatures without deformation or degradation.
Material | Glass Transition Temperature (Tg) |
---|---|
FR-4 | 130°C – 140°C |
RO4003C | >280°C |
RT/duroid 5870 | >260°C |
Polyimide | >260°C |
PTFE | 327°C |
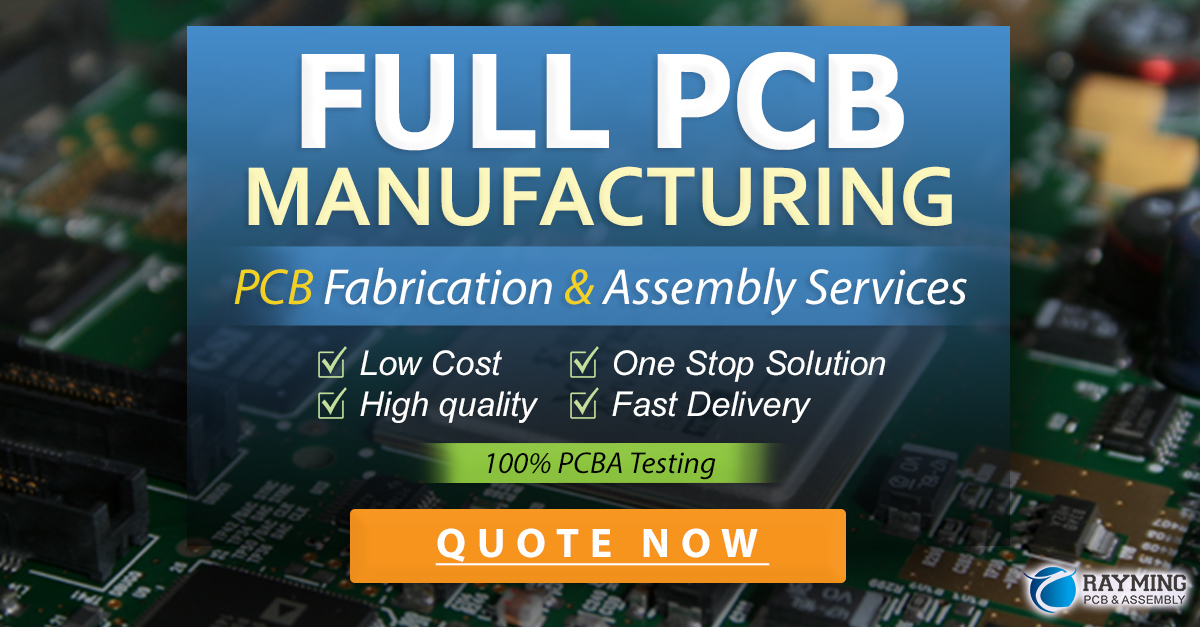
Applications of PCB Substrate Materials
The choice of PCB substrate material depends on the specific requirements of the application. Different materials are suited for different environments, frequencies, and performance levels. Here are some common applications and the substrate materials typically used:
1. Consumer Electronics
Consumer electronics, such as smartphones, laptops, and home appliances, primarily use FR-4 as the PCB substrate material. FR-4 offers a good balance of cost, mechanical strength, and electrical properties for these applications.
2. High-Frequency RF and Microwave
High-frequency applications, such as radar systems, satellite communication, and wireless infrastructure, require PCB substrate materials with low dielectric constant and loss tangent. Rogers materials (RO4000 series, RT/duroid) and PTFE are commonly used for these applications due to their excellent high-frequency performance.
3. Aerospace and Defense
Aerospace and defense applications demand high reliability and the ability to operate in harsh environments. Polyimide and PTFE are often used in these applications due to their high temperature resistance, mechanical strength, and chemical resistance.
4. Automotive Electronics
Automotive electronics require PCB substrate materials that can withstand high temperatures and vibrations. FR-4 is commonly used for general automotive applications, while polyimide is used for high-temperature environments, such as engine control units and exhaust systems.
Frequently Asked Questions (FAQ)
-
What is the most commonly used PCB substrate material?
FR-4 is the most widely used PCB substrate material due to its low cost, good mechanical strength, and excellent electrical insulation properties. -
Which PCB substrate materials are suitable for high-frequency applications?
Rogers materials (RO4000 series, RT/duroid) and PTFE are commonly used for high-frequency applications due to their low dielectric constant and loss tangent. -
What is the advantage of using polyimide as a PCB substrate material?
Polyimide offers high temperature resistance, excellent mechanical strength, and good chemical resistance, making it suitable for harsh environments and high-reliability applications. -
How does the dielectric constant affect the performance of a PCB substrate material?
A lower dielectric constant is desirable for high-frequency applications, as it reduces signal propagation delay and minimizes signal distortion. -
What is the glass transition temperature (Tg) of a PCB substrate material?
The glass transition temperature (Tg) is the temperature at which a material transitions from a rigid, glassy state to a softer, rubbery state. It determines the maximum operating temperature of the PCB.
Conclusion
PCB substrate materials play a crucial role in determining the performance, reliability, and cost of electronic circuits. Understanding the properties and characteristics of different substrate materials is essential for selecting the right material for a given application. FR-4 is the most commonly used substrate material, offering a good balance of cost and performance for general-purpose applications. High-frequency applications require materials with low dielectric constant and loss tangent, such as Rogers materials and PTFE. Polyimide is a popular choice for high-temperature and harsh environments.
When choosing a PCB substrate material, designers must consider factors such as the intended application, operating frequency, environmental conditions, and cost constraints. By carefully evaluating these factors and selecting the appropriate substrate material, designers can ensure optimal performance and reliability of their electronic products.
As technology continues to advance, new PCB substrate materials are being developed to meet the ever-increasing demands of modern electronics. These materials aim to provide better electrical properties, thermal stability, and mechanical strength, enabling the development of more advanced and efficient electronic systems.
[Word count: 1736 words]
Leave a Reply