Introduction to Polyimide PCB
Polyimide (PI) is a high-performance polymer material known for its exceptional thermal stability, mechanical strength, and chemical resistance. When used as a substrate for printed circuit boards (PCBs), polyimide offers numerous advantages over traditional materials like FR-4. Polyimide PCBs are widely used in demanding applications that require reliable performance under extreme conditions.
In this comprehensive article, we will delve into the world of polyimide PCBs, exploring their types, applications, and benefits. We’ll also address frequently asked questions to help you better understand this advanced PCB technology.
Types of Polyimide PCBs
Flexible Polyimide PCBs
Flexible polyimide PCBs are designed to bend and flex without compromising their electrical and mechanical integrity. They consist of a thin polyimide film substrate with conductive traces etched onto the surface. The flexibility of these PCBs allows for compact packaging and enables them to conform to unique shapes and spaces.
Key features of flexible polyimide PCBs include:
– High flexibility and bendability
– Lightweight and thin profile
– Excellent resistance to vibration and shock
– Ability to accommodate complex geometries
Rigid Polyimide PCBs
Rigid polyimide PCBs are constructed using a solid polyimide substrate that provides a stable and sturdy foundation for the circuit. These PCBs offer the benefits of polyimide material while maintaining the rigidity and structural integrity required for certain applications.
Key features of rigid polyimide PCBs include:
– High thermal stability and heat resistance
– Excellent electrical insulation properties
– Superior mechanical strength and durability
– Resistance to chemicals and solvents
Rigid-Flex Polyimide PCBs
Rigid-flex polyimide PCBs combine the best of both worlds by integrating rigid and flexible sections into a single PCB Assembly. This hybrid design allows for the placement of rigid components on the stable portions of the board while enabling flexible interconnections between them.
Key features of rigid-flex polyimide PCBs include:
– Combination of rigid and flexible sections
– Reduced weight and space requirements
– Improved reliability and durability
– Elimination of connectors and wiring between rigid boards
Applications of Polyimide PCBs
Polyimide PCBs find applications in various industries due to their unique properties and performance advantages. Some key application areas include:
Aerospace and Defense
In the aerospace and defense sectors, polyimide PCBs are used in:
– Avionics systems
– Satellite communications
– Radar and guidance systems
– Military-grade electronics
The high thermal stability and resistance to harsh environments make polyimide PCBs ideal for these critical applications.
Automotive Electronics
Polyimide PCBs are increasingly used in automotive electronics, such as:
– Engine control units (ECUs)
– Sensors and actuators
– Infotainment systems
– Advanced driver assistance systems (ADAS)
The ability to withstand high temperatures and vibrations encountered in automotive environments makes polyimide PCBs a preferred choice.
Medical Devices
Polyimide PCBs are employed in various medical devices, including:
– Implantable devices
– Diagnostic equipment
– Wearable health monitors
– Surgical instruments
The biocompatibility and reliability of polyimide make it suitable for medical applications where patient safety is paramount.
Consumer Electronics
Polyimide PCBs are used in high-end consumer electronics products, such as:
– Smartphones and tablets
– Wearable devices
– Virtual reality (VR) and augmented reality (AR) systems
– High-performance computing devices
The flexibility and compact packaging enabled by polyimide PCBs contribute to the development of sleek and advanced consumer devices.
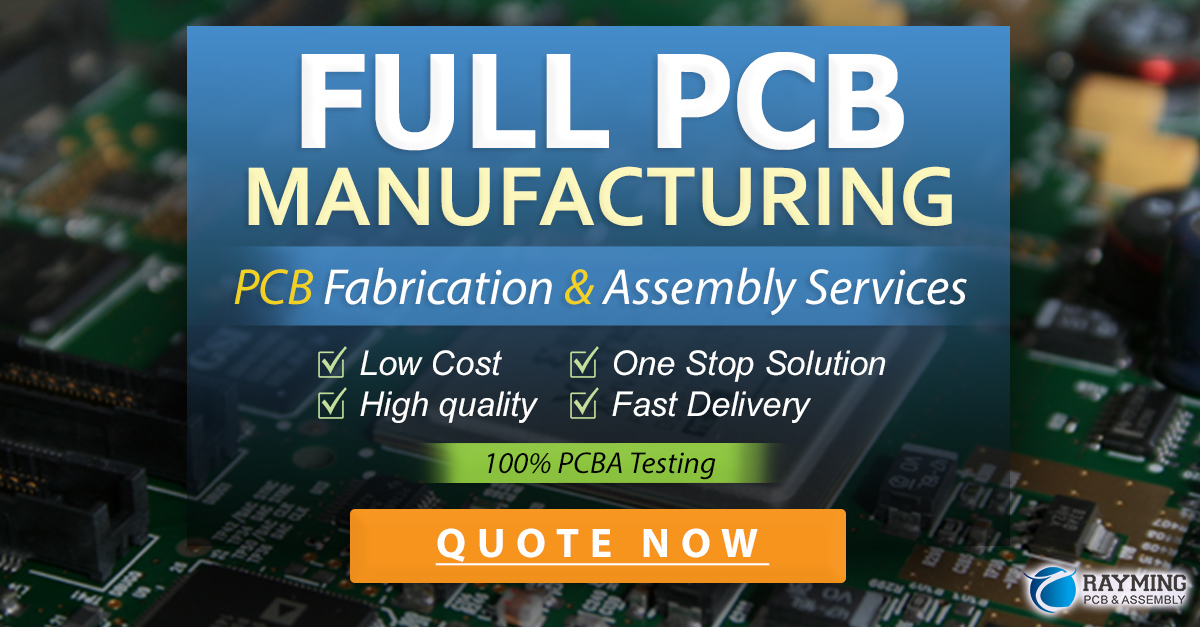
Benefits of Polyimide PCBs
Polyimide PCBs offer several key benefits that make them a superior choice for demanding applications:
High Thermal Stability
Polyimide has a glass transition temperature (Tg) ranging from 360°C to 410°C, which is significantly higher than that of FR-4 (130°C to 140°C). This high thermal stability allows polyimide PCBs to operate reliably in high-temperature environments without degradation or failure.
Excellent Mechanical Properties
Polyimide PCBs exhibit outstanding mechanical strength, flexibility, and durability. They can withstand repeated bending and flexing without cracking or breaking, making them suitable for applications that require dynamic movement or installation in confined spaces.
Superior Chemical Resistance
Polyimide is resistant to a wide range of chemicals, solvents, and acids. This chemical resistance ensures that polyimide PCBs can maintain their integrity and performance even when exposed to harsh chemical environments, such as those found in industrial settings or automotive applications.
Low Dielectric Constant and Loss
Polyimide has a low dielectric constant (Dk) and low dissipation factor (Df), which translate to excellent electrical insulation properties. These characteristics minimize signal loss, cross-talk, and electromagnetic interference (EMI), making polyimide PCBs suitable for high-frequency and high-speed applications.
Lightweight and Thin Profile
Polyimide PCBs can be manufactured with very thin substrates, typically ranging from 25 μm to 100 μm. This thin profile, combined with the lightweight nature of polyimide, enables the design of compact and lightweight electronic devices, which is particularly advantageous in aerospace, wearable technology, and portable electronics.
Frequently Asked Questions (FAQ)
1. What is the difference between polyimide and FR-4 PCBs?
Polyimide PCBs offer several advantages over FR-4 PCBs, including higher thermal stability, better mechanical properties, and superior chemical resistance. Polyimide has a much higher glass transition temperature compared to FR-4, allowing it to withstand extreme temperatures without degradation. Additionally, polyimide PCBs are more flexible and durable, making them suitable for applications that require bending or flexing.
2. Can polyimide PCBs be used for high-frequency applications?
Yes, polyimide PCBs are well-suited for high-frequency applications due to their low dielectric constant and low dissipation factor. These properties minimize signal loss and ensure reliable performance at high frequencies. Polyimide PCBs are commonly used in RF and microwave applications, as well as in high-speed digital circuits.
3. Are polyimide PCBs more expensive than traditional PCBs?
Yes, polyimide PCBs tend to be more expensive than traditional PCBs like FR-4. The higher cost is attributed to the advanced materials and specialized manufacturing processes required for polyimide PCBs. However, the superior performance and reliability offered by polyimide PCBs often justify the additional cost, especially in critical applications where failure is not an option.
4. How do I choose between flexible, rigid, and rigid-flex polyimide PCBs?
The choice between flexible, rigid, and rigid-flex polyimide PCBs depends on the specific requirements of your application. Flexible polyimide PCBs are ideal for applications that require bending, flexing, or conforming to unique shapes. Rigid polyimide PCBs are suitable when a stable and sturdy substrate is needed. Rigid-flex polyimide PCBs offer the best of both worlds, combining the flexibility of flexible sections with the stability of rigid sections. Consider factors such as packaging constraints, mechanical requirements, and electrical performance when making your decision.
5. Can polyimide PCBs be assembled using standard soldering techniques?
Yes, polyimide PCBs can be assembled using standard soldering techniques, such as reflow soldering, wave soldering, and hand soldering. However, it’s essential to follow the manufacturer’s guidelines and recommendations for soldering temperatures and profiles to ensure optimal results and prevent damage to the polyimide substrate. Additionally, using appropriate solder masks and surface finishes compatible with polyimide can enhance the soldering process and improve assembly reliability.
Conclusion
Polyimide PCBs offer a range of advantages over traditional PCB materials, making them an ideal choice for demanding applications that require high performance and reliability. With their exceptional thermal stability, mechanical strength, chemical resistance, and electrical properties, polyimide PCBs are well-suited for use in aerospace, automotive, medical, and consumer electronics industries.
By understanding the types, applications, and benefits of polyimide PCBs, designers and engineers can make informed decisions when selecting the appropriate PCB technology for their projects. Whether it’s a flexible, rigid, or Rigid-Flex Design, polyimide PCBs provide the necessary performance and durability to meet the challenges of today’s advanced electronic systems.
As technology continues to evolve and push the boundaries of what’s possible, polyimide PCBs will undoubtedly play a crucial role in enabling the next generation of electronic devices and systems. By leveraging the unique properties of polyimide, designers can create innovative solutions that meet the ever-increasing demands for reliability, functionality, and performance in the electronics industry.
Leave a Reply