Understanding Rigid-Flex PCB Technology
Before diving into the best practices, it’s essential to understand what rigid-flex PCB technology is and how it differs from traditional rigid or flexible PCBs.
What is a Rigid-Flex PCB?
A rigid-flex PCB is a printed circuit board that combines both rigid and flexible substrates in a single design. The rigid portions of the board provide structural support and allow for the mounting of components, while the flexible portions enable the board to bend or fold, allowing for more compact and versatile designs.
Advantages of Rigid-Flex PCBs
Rigid-flex PCBs offer several advantages over traditional PCBs:
- Reduced size and weight: By eliminating the need for connectors and cables, rigid-flex PCBs can significantly reduce the overall size and weight of electronic devices.
- Improved reliability: With fewer interconnects and a more streamlined design, rigid-flex PCBs are less prone to failures caused by vibrations, shocks, and other environmental factors.
- Enhanced flexibility: The flexible portions of the board allow for more creative and space-saving designs, enabling the creation of unique form factors.
- Cost-effective: Although the initial design and fabrication costs may be higher, rigid-flex PCBs can lead to cost savings in the long run by reducing assembly time and improving reliability.
Material Selection for Rigid-Flex PCBs
Choosing the right materials is crucial for the success of your rigid-flex PCB design. The materials used should be able to withstand the stresses of bending and flexing while maintaining their electrical and mechanical properties.
Flexible Substrates
The most common flexible substrates used in rigid-flex PCBs are:
- Polyimide (PI): Known for its excellent thermal stability and mechanical strength, polyimide is the most widely used flexible substrate material.
- Polyester (PET): PET is a cost-effective alternative to polyimide, suitable for less demanding applications.
- Flexible metal-clad laminates: These materials combine a thin layer of metal (usually copper) with a flexible substrate, providing better shielding and thermal management.
Adhesives
Adhesives play a critical role in bonding the rigid and flexible portions of the board. The most common adhesives used in rigid-flex PCBs are:
- Acrylic: Acrylic adhesives offer good flexibility and adhesion, making them suitable for most applications.
- Epoxy: Epoxy adhesives provide excellent strength and durability but are less flexible than acrylic adhesives.
- Pressure-sensitive adhesives (PSAs): PSAs are easy to apply and provide good adhesion, but they may not be suitable for high-temperature applications.
Rigid-Flex PCB Layout Considerations
Designing the layout of a rigid-flex PCB requires careful planning to ensure the board’s reliability and functionality.
Bend Radius
One of the most critical aspects of rigid-flex PCB layout is determining the appropriate bend radius. The bend radius is the minimum radius at which the flexible portion of the board can be bent without causing damage. The bend radius depends on several factors, including the thickness of the flexible substrate, the number of copper layers, and the type of adhesive used.
Flexible Substrate Thickness (mm) | Minimum Bend Radius (mm) |
---|---|
0.05 | 1.0 |
0.075 | 1.5 |
0.1 | 2.0 |
0.125 | 2.5 |
Copper Placement
When designing the copper traces on a rigid-flex PCB, it’s essential to consider the placement of the copper in relation to the bend areas. Copper traces should be routed perpendicular to the bend line whenever possible to minimize stress on the traces during flexing. Additionally, it’s recommended to use teardrop-shaped pads at the junction of the trace and pad to reduce the risk of pad lifting or trace cracking.
Stiffener Placement
Stiffeners are used to provide additional support to the flexible portions of the board, preventing excessive bending and improving the overall reliability of the design. Stiffeners should be placed in areas where the board is likely to experience the most stress, such as at connector interfaces or where the board transitions from rigid to flexible.
Component Placement
When placing components on a rigid-flex PCB, it’s important to consider the location of the components in relation to the bend areas. Components should be placed on the rigid portions of the board whenever possible to avoid subjecting them to the stresses of flexing. If components must be placed on the flexible portions, it’s essential to use components specifically designed for flexible applications and to provide adequate strain relief.
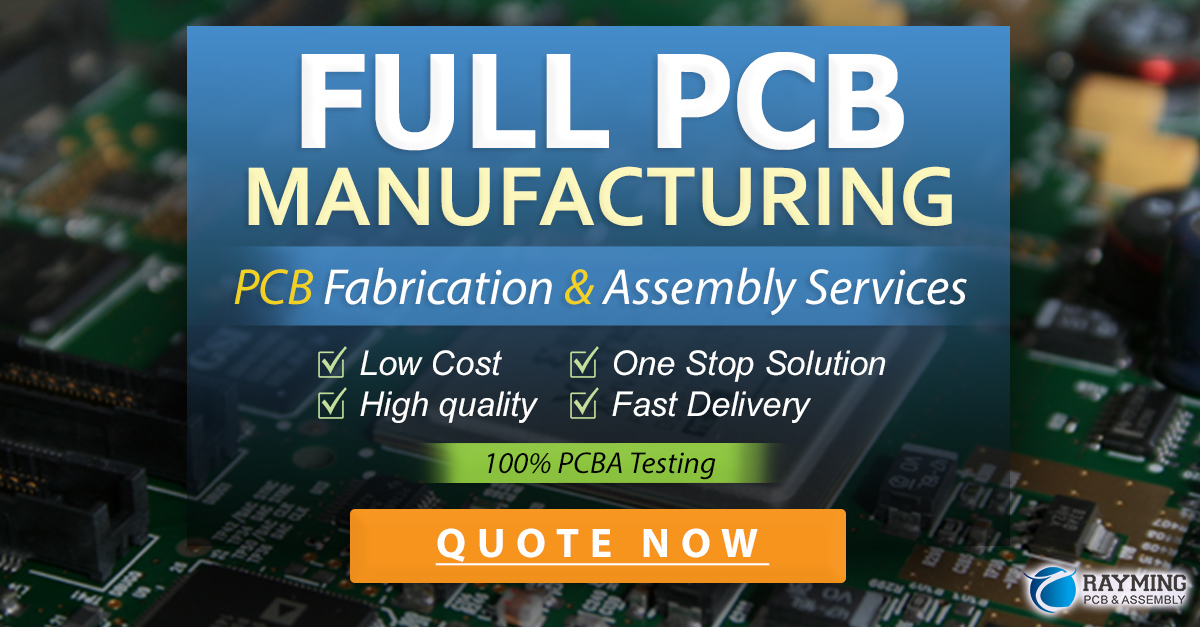
Manufacturing Considerations for Rigid-Flex PCBs
Manufacturing rigid-flex PCBs requires specialized equipment and processes, which can impact the design choices and overall cost of the project.
Layer Stack-Up
The layer stack-up of a rigid-flex PCB is more complex than that of a traditional rigid PCB. The stack-up must account for the different materials used in the rigid and flexible portions of the board and the placement of the adhesives and stiffeners. It’s essential to work closely with your PCB manufacturer to ensure the layer stack-up is optimized for your specific application.
Via Placement
Vias are used to connect different layers of the PCB, but they can also introduce stress points in the flexible portions of the board. To minimize the risk of via failure, it’s recommended to use microvias or buried vias in the flexible areas whenever possible. Additionally, vias should be placed in a staggered pattern to distribute the stress more evenly.
Cover Layer Openings
Cover layers are used to protect the copper traces and provide electrical insulation. In rigid-flex PCBs, cover layer openings are used to expose the flexible portions of the board. The size and shape of these openings should be carefully designed to ensure adequate clearance for bending and to avoid exposing any copper traces.
FAQ
-
Q: What is the minimum bend radius for a 0.1mm thick flexible substrate?
A: The minimum bend radius for a 0.1mm thick flexible substrate is typically 2.0mm. -
Q: Can components be placed on the flexible portions of a rigid-flex PCB?
A: While it’s preferable to place components on the rigid portions of the board, components can be placed on the flexible portions if they are specifically designed for flexible applications and adequate strain relief is provided. -
Q: What type of adhesive is best suited for high-temperature applications?
A: Epoxy adhesives are generally better suited for high-temperature applications compared to acrylic or pressure-sensitive adhesives. -
Q: How can I reduce the risk of via failure in the flexible portions of the board?
A: To reduce the risk of via failure in the flexible portions, use microvias or buried vias whenever possible and place vias in a staggered pattern to distribute stress more evenly. -
Q: Is it more expensive to manufacture rigid-flex PCBs compared to traditional rigid PCBs?
A: Yes, the initial design and fabrication costs for rigid-flex PCBs are usually higher than those for traditional rigid PCBs due to the specialized materials and manufacturing processes required. However, the long-term cost savings from reduced assembly time and improved reliability can often justify the higher upfront costs.
Conclusion
Designing a rigid-flex PCB requires careful consideration of materials, layout, and manufacturing processes. By following the best practices outlined in this article, you can create a reliable and cost-effective rigid-flex PCB that meets the unique requirements of your application. Remember to work closely with your PCB manufacturer throughout the design process to ensure the best possible outcome for your project.
Leave a Reply